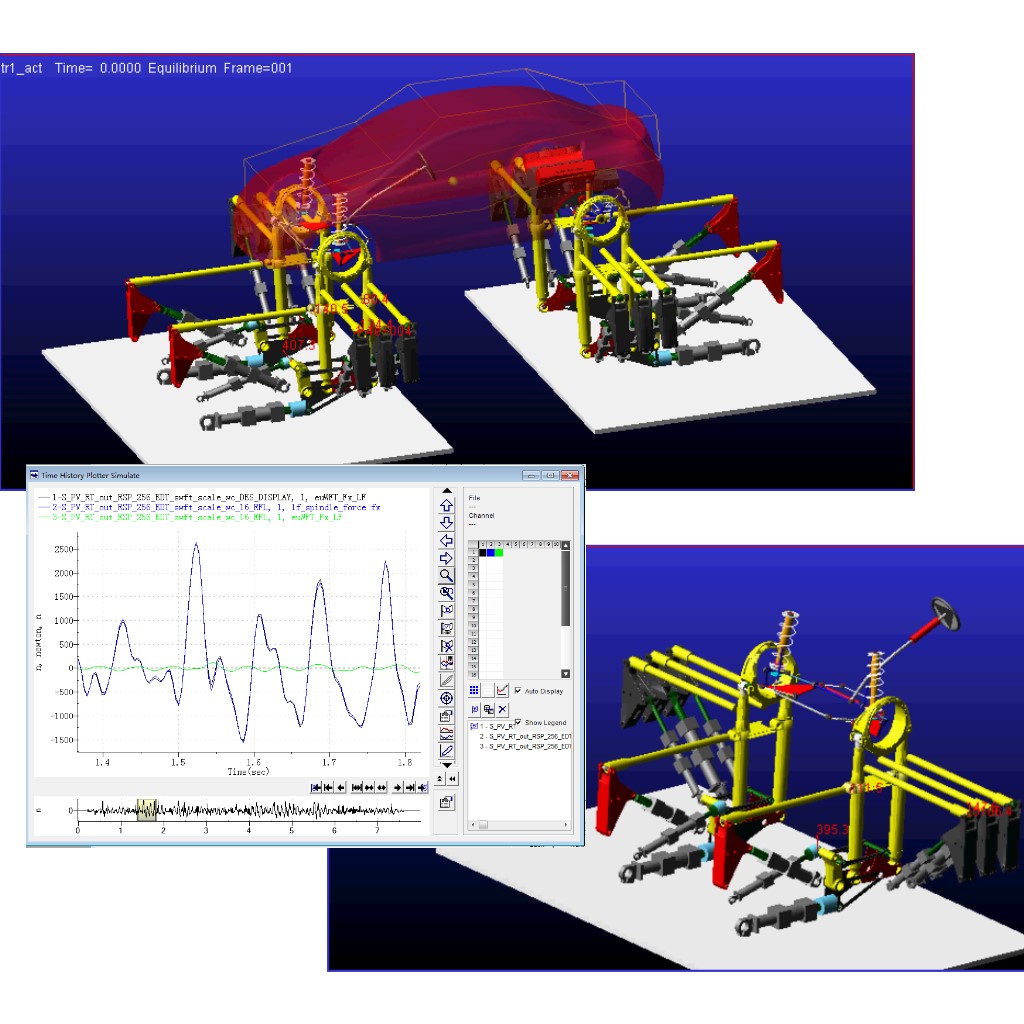
Sob uma pressão implacável para encurtar os ciclos de desenvolvimento e reduzir os custos, os fabricantes de automóveis estão explorando cada vez mais as formas de utilizar ferramentas de análise para realizar avaliações virtuais significativas de projetos de veículos logo no início do projeto, bem antes da disponibilidade de protótipos físicos. A capacidade de obter cargas previstas - ou calculadas com precisão - desta forma aumenta a eficácia dos testes físicos dos componentes, permite a identificação precoce e a eliminação de falhas de projeto, reduz a necessidade de retrabalho e a dependência de protótipos, e agiliza a validação do projeto.
Uma variedade de abordagens de simulação foi criada para obter cargas calculadas com precisão no início do processo de desenvolvimento do veículo. Um método, o Campo de Provas Virtual, envolve "dirigir" um modelo de veículo sobre uma estrada digitalizada. Embora, haja a vantagem de confiar inteiramente em modelos virtuais, esta abordagem produz cargas imprecisas que são difíceis de validar através de testes físicos. Um método semianalítico, por outro lado, utiliza cargas de fuso adquiridas de um veículo existente para excitar o modelo do veículo. Isto proporciona melhores resultados que o campo de provas virtual, mas estabelece condições de limite não inteiramente apropriadas para o modelo do veículo, portanto, as cargas calculadas ainda são incorretas e difíceis de validar. Um terceiro método, o Teste Virtual, supera estes problemas integrando um modelo de um sistema de teste físico real na simulação para excitar o modelo do veículo.
Teste virtual é a simulação de um teste físico, utilizando ferramentas de análise de elementos finitos, ferramentas de análise dinâmica multicorpo e técnicas de iteração RPC para derivar cargas precisas, movimentos e informações sobre danos de um sistema de veículo nos estágios iniciais do processo de desenvolvimento. São inúmeras as vantagens desta abordagem Primeiro, porque é mais fácil modelar as restrições de um sistema de teste físico do que provar superfícies de solo ou pneus, o teste virtual estabelece condições de contorno muito mais eficazes do que os outros métodos. Em segundo lugar, os testes virtuais usam um arsenal de ferramentas e técnicas de testes físicos comprovados e bem estabelecidos, que têm demonstrado utilidade no domínio da análise. E, terceiro, a incorporação de um sistema de teste físico modelado simplifica muito a validação dos resultados através de testes físicos subsequentes e oferece a oportunidade de melhorar as configurações de testes físicos e os projetos de equipamentos. Abrangendo as disciplinas de testes analíticos e físicos, os testes virtuais requerem conhecimentos avançados tanto de ferramentas CAE quanto de testes físicos, o desenvolvimento de um processo para vincular o software RPC Pro e modelos de análise e, de preferência, algum grau de exposição e experiência em testes virtuais.
Durante anos, a MTS tem se concentrado em aperfeiçoar a abordagem de testes virtuais, conduzindo uma variedade de projetos de demonstração com os principais clientes como Hyundai Motor Company (HMC) e Thermo King para avaliar várias metodologias. Estes projetos incluíram testes virtuais de veículos e subsistemas completos, todos produzindo uma correlação satisfatória com os dados de carga rodoviária medida (RLD) ou testes físicos reais. A metodologia básica obtida a partir dessas experiências compreende os seguintes passos: 1) Conectar modelos de bancos de ensaio com modelos de amostras; 2) Acoplar os modelos com RPC Pro; 3) Reproduzir os dados de carga da estrada no equipamento de teste virtual; 4) Extrair cargas calculadas; 5) Criar o teste do componente físico/subsistema.
Um recente projeto de demonstração com o Instituto Automotivo Estatal da China (SAIC) fornece um excelente exemplo desta metodologia, na prática:
- Conectar modelos de plataforma de teste com modelos de corpo de prova
No início do projeto, a MTS construiu uma coleção de modelos de plataformas de testes nos formatos de cosimulação ADAMS, Simulink e ADAMS-Simulink. As plataformas de teste MTS que foram modeladas incluíam uma variedade de Simuladores de Rodovias acoplados a fusos Modelo 329, um Sistema de Mesa de Simulação Multi-axial (MAST) Modelo 353.20 e um sistema de teste de componentes TestLine. Também foram modelados componentes de plataforma de teste selecionados, incluindo um controlador digital FlexTest, atuadores MTS e servoválvulas, e um atuador que converte o deslocamento, aceleração e força do atuador em deslocamento, aceleração e força DOF. Devido às restrições de tempo do projeto e à velocidade relativamente lenta de simulação dos modelos mais complexos de cosimulação, o modelo ADAMS/Car 329 foi acoplado ao veículo completo SAIC, modelos de suspensão dianteira e suspensão traseira e finalmente utilizado para a maior parte dos testes virtuais.
- Acople os modelos com o RPC Pro
Um servidor de teste virtual foi desenvolvido para conectar o software RPC Pro e o modelo ADAMS/Car 329. Durante os testes, o RPC Pro emprega este servidor virtual para enviar arquivos de unidade para o modelo ADAMS, iniciar a simulação do ADAMS e copiar o arquivo de resposta da pasta ADAMS para o diretório de trabalho do RPC Pro. Além disso, uma ferramenta de interface Matlab já existente no RPC Pro foi usada para acoplar o RPC Pro com os modelos de co-simulação.
- Reproduza dados de carga da estrada na plataforma de teste virtual
A técnica de iteração RPC foi então utilizada para reproduzir os dados de carga (força do fuso) coletados do campo de prova para uma variedade de eventos e manobras selecionadas. Curiosamente, as iterações iniciais do RPC nas sondas virtuais 329 não mostraram convergência, sugerindo falhas no modelo do veículo SAIC. A análise subsequente do modelo revelou, de fato, deficiências, que foram corrigidas em curto prazo. Com o modelo melhorado, as iterações RPC finalmente convergiram, mostrando excelente correlação entre sinais desejados e obtidos e erros RMS baixos em todos os canais, tanto para simulações virtuais de veículos completos como parciais.
- Extrair cargas calculadas
Na convergência da iteração RPC, as cargas calculadas para qualquer componente mecânico ou subsistema poderiam então ser prontamente obtidas do modelo do veículo como funções do tempo.
- Criação de testes físicos
Então, foram utilizados históricos de tempo de carga extraídos do modelo do veículo para definir testes de componentes físicos subsequentes. Uma vez determinado se uma peça está sujeita à carga de um ou vários eixos, o arsenal de métodos e ferramentas de teste RPC Pro pode ser usado para definir testes de componentes significativamente acelerados. Para componentes sob carga de eixo único, pode ser usado o método de ciclo de bloco (Block Cycle) ou o método de densidade de espectro de potência (Power Spectrum Density - PSD). Para componentes sujeitos a carregamento de múltiplos eixos, pode ser utilizado o método de Fatiamento de Vale de Pico (Peak Valley Slicing). Para situações onde a frequência de carregamento de um componente precisa ser preservada, o método de Reprodução do Histórico de Tempo é o mais apropriado; para estes tipos de testes, o RPC Pro apresenta a Edição Sensível à Fadiga que tem a possibilidade de acelerar os testes de durabilidade por um fator de 2 a 10. Uma vez determinados os sinais de carga para cada componente, o mesmo sistema de teste físico no qual as plataforma de teste virtuais foram baseados pode ser usado para conduzir o teste do componente. Além disso, uma variedade de técnicas de compensação no RPC Pro, tais como Compensação de Pico, Compensação Inversa Adaptativa e iteração de RPC, pode ser usada para garantir que as condições de carga desejadas sejam atingidas com precisão durante os testes físicos.
A exploração contínua da MTS de testes virtuais demonstra que ele é um meio eficaz para prever com precisão as cargas de componentes antes do desenvolvimento de peças físicas ou protótipos. Uma vez obtidas estas cargas calculadas, as mesmas ferramentas e técnicas RPC Pro usadas para obtê-las podem então ser usadas para criar e conduzir os testes físicos necessários para validar sua precisão, e a precisão do modelo do veículo. Os possíveis impactos dos testes virtuais efetivos no desenvolvimento do veículo são consideráveis. A disponibilidade de cargas previstas precisas e os testes físicos posteriores minimizarão o retrabalho de componentes e subsistemas, reduzirá a necessidade de múltiplos protótipos e acelerará a validação do projeto. Além disso, o papel dos testes físicos irá evoluir: embora os testes continuem a ser necessários para obter a validação final do projeto de um veículo, ele será cada vez mais adaptado para validar a precisão do modelo do veículo. E, por fim, os testes virtuais estimularão a integração de disciplinas e culturas de análise e de testes físicos, levando ao advento de novas eficiências através do compartilhamento de ferramentas, processos e experiências.
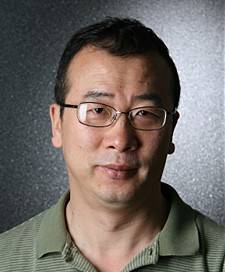