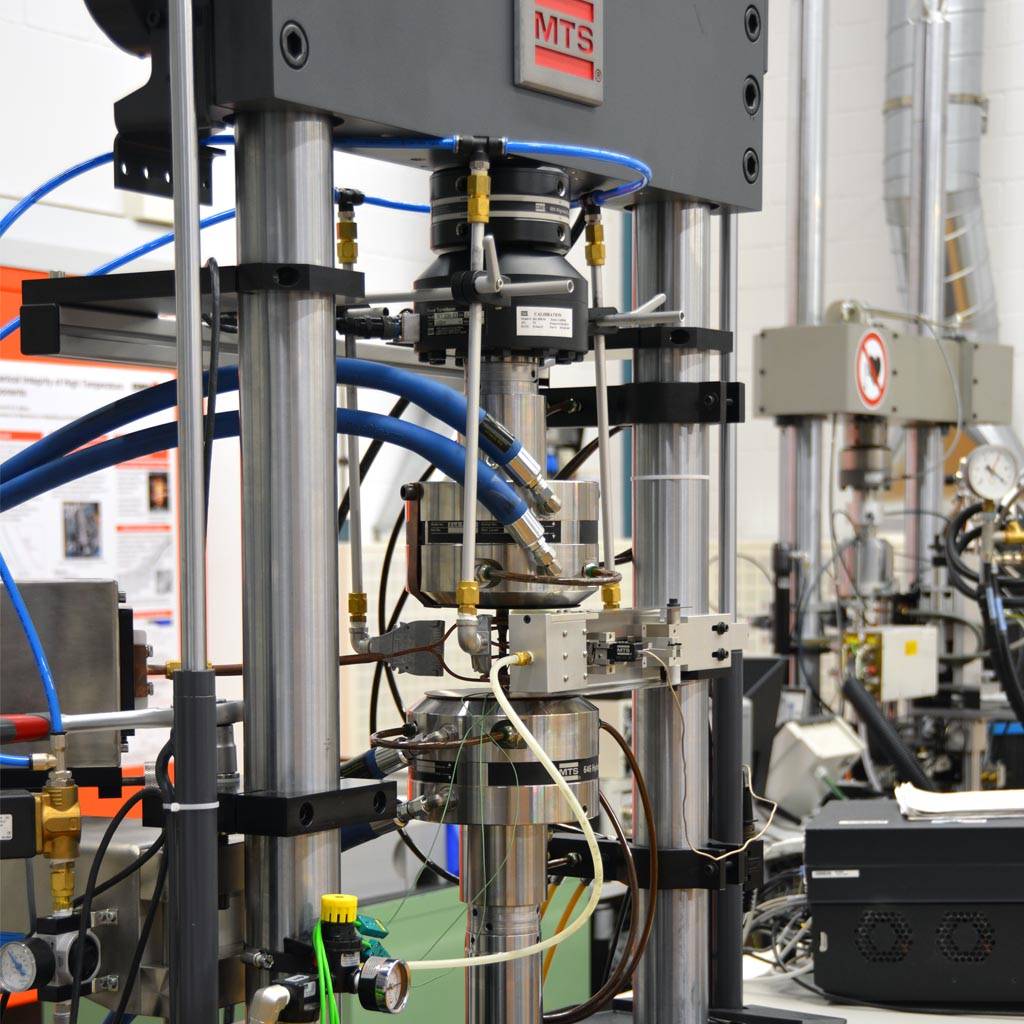
DESAFIO DO CLIENTE
As turbinas a gás e a vapor de hoje solucionam problemas que não existiam algumas décadas atrás. A eficácia superior requer maiores temperaturas operacionais e materiais resistentes à oxidação e à fluência em tais condições. Os ciclos de trabalho mais flexíveis implicam que os materiais devem ainda ser resistentes a danos por fadiga termomecânica. Sem dúvida, é preciso fazer todas as melhorias sem comprometer os custos operacionais ou a confiabilidade.
Portanto, as filosofias de engenharia estão em transformação. Assim, metodologias convencionais de projeção de vida útil já não são sempre a melhor opção para estimar com precisão a vida útil de componentes de turbinas. É preciso novas metodologias, que, todavia, devem ser testadas e verificadas antes de receberem a confiança dos fabricantes e dos usuários.
Um laboratório pioneiro em avanços neste campo é o Empa, um instituto federal de pesquisa da Suíça, situado em Dübendorf, próximo a Zurique. Conduzindo de forma inovadora os testes de fadiga mecânica (TMF), os pesquisadores do Empa são capazes de simular condições operacionais de turbinas próximas à realidade, com alta fidelidade, e verificar a eficácia de novas metodologias de projeção.
Pesquisadores usam tecnologias de TMF para estimar com precisão a vida útil de turbinas.
“Tradicionalmente, os testes de TMF vêm sendo usados para a caracterização de materiais”, afirma o Dr. Stuart Holdsworth, chefe do Grupo de Integridade em Alta Temperatura do Empa. “Também estamos usando os resultados desses testes para fundamentar conceitos avançados de modelagem de deformação e danos em materiais e, sobretudo, para comparar a eficácia de novos procedimentos de avaliação em alta temperatura na projeção da vida útil de componentes.”
Os componentes de novas turbinas são projetados para esquentar o máximo possível (isto é, para operar do modo mais eficaz), mas não tanto a ponto de os materiais excederem os limites de suas propriedades. Com vista a evitar falhas em altas temperaturas, é preciso ter em conta os processos de danificação em função do tempo, como fluência e oxidação, bem como seus efeitos de interação sobre o acúmulo de dano de fadiga.
Estudos simples de fluência e fluência-fadiga focam-se em como os materiais reagem sob controle, com alta carga estável e em alta temperatura. Entretanto, isso não reflete corretamente a operação real da turbina, na qual as cargas e as temperaturas variam.
“Com a crescente tendência para a operação de dois turnos na década de 1990, e a subsequente adoção de unidades de ciclos combinados, passou a haver maior necessidade de operação mais flexível e de turbinas que pudessem ser ligadas e desligadas mais vezes pelos operadores”, afirma Holdsworth. “Hoje, os requisitos são ainda mais rigorosos.”
De igual modo, os ciclos de trabalho dos motores a jato estão em transformação. Motores de aeronaves para voos regionais e de curta distância experimentam tempos menores entre a decolagem e a aterrissagem. Em razão das asas mais curtas e das fuselagens menores de tais aeronaves, os motores encontram condições de tensão vibratória muito diferentes das dos motores em aeronaves maiores, para voos de longa distância.
Diante de ciclos de trabalho sempre diferentes, é difícil para os fabricantes de turbinas estimarem com confiança a duração de cada componente das turbinas. Conhecer o “elo mais fraco” permite que os fabricantes otimizem novos projetos em termos de confiabilidade e estabeleçam cronogramas de manutenção eficazes, com foco em possíveis pontos de vulnerabilidade.
É por isso que Holdsworth e sua equipe elaboraram um método inovador de avaliação de componentes de turbinas em alta temperatura, que envolve análises não lineares de elementos finitos e análises de danificação de fluência-fadiga, bem como métodos eficazes de comparar e verificar as projeções.
A técnica de análise segue um processo iterativo, começando por uma avaliação de fadiga de fluência em componentes específicos da turbina. Emprega-se então uma análise avançada e não linear de elementos finitos para determinar os estados de tensão e deformação e os locais críticos nos componentes durante a operação. Com base nessas informações, a equipe pode fazer projeções sobre a vida útil dos componentes.
A fim de determinar a precisão de tais projeções, a equipe de Holdsworth desenvolveu uma metodologia de teste de TMF que pode reproduzir o ciclo de operação com os mesmos estados térmicos e de tensão e deformação mecânica identificados na análise inicial do componente. O processo é então repetido, e os resultados são usados para aprimorar o procedimento de análise até se verificar que ele fornece uma projeção precisa da vida útil.
SOLUÇÃO DA MTS
Para realizar seus testes, o laboratório do Empa usa dois sistemas de teste servo-hidráulicos da MTS, capazes de executar testes complexos de TMF. As capacidades desses sistemas, seus acessórios, seu controlador digital e suas arquiteturas de software correspondem a dois aspectos exclusivos de como o Empa realiza testes de TMF.
O primeiro é a capacidade de reproduzir os estados de tensão e deformação em locais críticos do componente submetido a condições operacionais reais. Para tanto, o teste deve alternar de controle mecânico de deformação para controle de carga no mesmo ciclo, o que requer flexibilidade sem precedentes. Técnicas avançadas de compensação fornecem o controle preciso de servoválvulas necessário para alternar entre os modos de controle. Além disso, o software MTS TestSuite™ permite que os operadores criem formas de onda altamente personalizadas, incorporando uma sequência apropriada de variações e estabilizações. O software permite ainda que eles criem um ciclo único, de vários segmentos, com dois modos de controle distintos.
O software MTS TestSuite permite que os projetistas do teste criem formas de onda personalizadas.
O segundo é a capacidade de sobrepor vibrações de alta frequência a condições cíclicas de tensão e deformação de frequência relativamente baixa para simular, por exemplo, as cargas de flexão de gás em aerofólios da turbina sobrepostas a cargas centrífugas cíclicas. A variação da pressão de gás no aerofólio deve-se à interação cíclica entre as lâminas móveis e estacionárias, enquanto a carga centrífuga cíclica é consequência das condições operacionais da turbina. Novamente, a arquitetura de controle da solução de teste da MTS fornece a velocidade de processamento e a flexibilidade de programação necessárias para adicionar tais vibrações ao teste de TMF e, assim, criar simulações altamente realistas.
BENEFÍCIOS PARA O CLIENTE
Os beneficiários finais dos exclusivos testes de TMF do Empa são os fabricantes de componentes e estruturas para turbinas a gás e a vapor, bem como os operadores de aeronaves e de fábricas que os instalam. Como o Empa agora pode fazer e verificar projeções de vida útil mais precisas, condizentes com a forma como as turbinas de fato serão operadas, os fabricantes podem desenvolver e otimizar novos projetos com confiança. De igual modo, os usuários finais têm mais garantia de que as turbinas satisfarão suas exigências de desempenho, confiabilidade, eficácia e segurança.