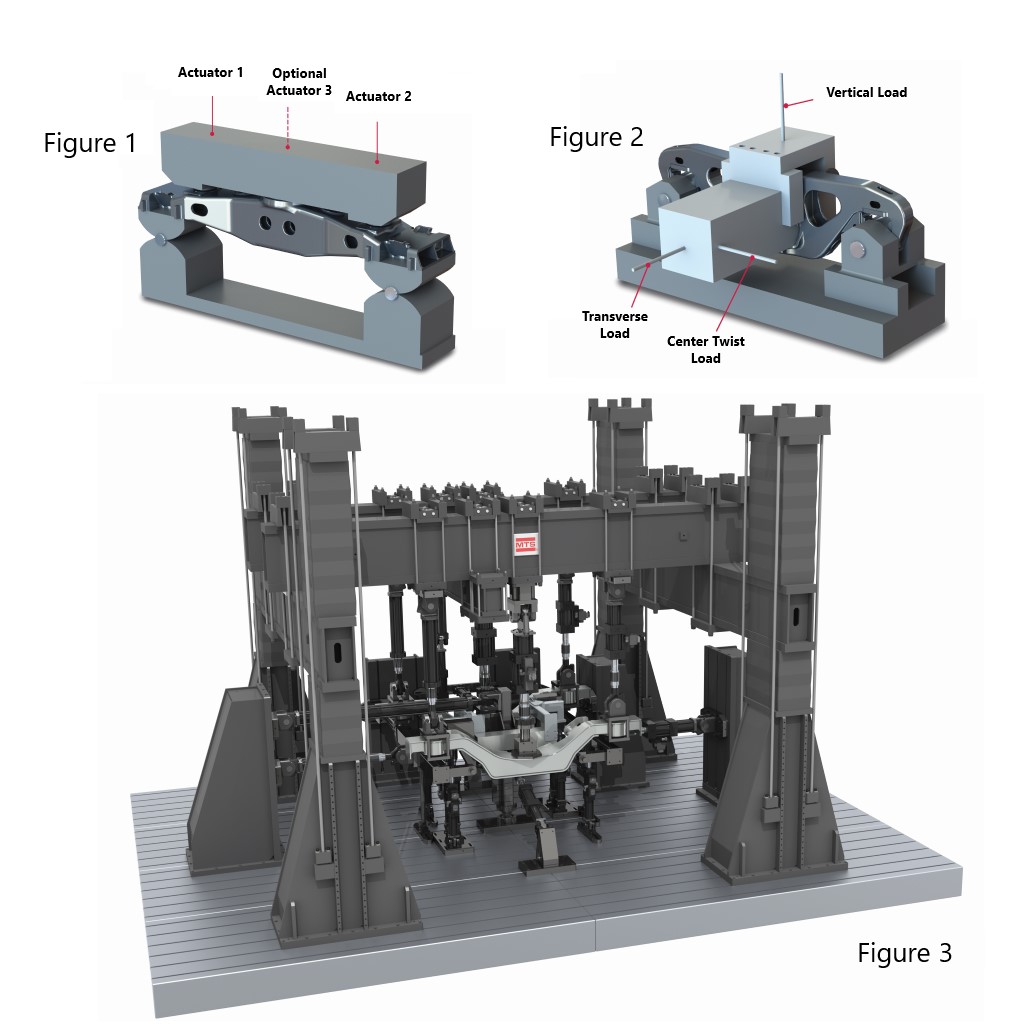
Ao considerar todos os componentes e subconjuntos que compõem um sistema de material circulante e seu ambiente circundante, ele ajuda a traçar uma linha imaginária ao longo da parte superior do trilho. Esta linha divide o sistema em dois grandes grupos. O primeiro grupo, localizado acima da linha, é o "material circulante", representado por uma estrutura de bogie (ou uma combinação de duas laterais e um suporte) juntamente com a suspensão primária e secundária e o vagão ferroviário. O segundo grupo, localizado abaixo da linha, é "o caminho", representado pelos trilhos, fixadores, dormentes, lastro e outros componentes. A interface entre os dois grupos é o eixo com um conjunto de rodas.
Enquanto muitos dos elementos mais simples deste sistema podem ser tratados através de testes básicos de componentes, a avaliação de um componente ou subconjunto dentro do material circulante requer a consideração de três fatores igualmente importantes: fadiga, desempenho e conforto.
Embora a vida de fadiga possa não ser o que o passageiro aprecia (ou mesmo pensa) durante a viagem, ela representa uma parte muito importante no projeto e no serviço do material rodante. Ao longo do século passado, a indústria ferroviária passou a compreender e reconhecer a importância dos testes de fadiga no projeto e fabricação de componentes ferroviários. A fim de garantir uma vida de fadiga consistente e segurança dos passageiros, muitas normas de certificação foram desenvolvidas.
CUMPRIMENTO DAS NORMAS DE CERTIFICAÇÃO
Os fabricantes de componentes e subsistemas ferroviários devem testar componentes e subsistemas para atender às normas de certificação apropriadas, incluindo normas internacionais como a M-202-97 para os parafusos, a M-203-05 para as estruturas laterais e a UIC 615 para os bogies. Estas normas ajudam a definir os testes utilizados para estabelecer a vida útil e a durabilidade dos novos componentes, e são essenciais para garantir o funcionamento seguro e de longo prazo das linhas ferroviárias de passageiros, de carga e veículos leves (VLTs).
Os testes de certificação de bogies, parafusos e estruturas laterais exigem que os fabricantes realizem testes de segurança e confiabilidade em estruturas e componentes de bogies em configurações específicas. As cargas estáticas e dinâmicas são aplicadas a fim de avaliar o desempenho, a força e a resistência. Os resultados dos testes incluem o rendimento e os níveis finais de carga de falha, bem como dados sobre a vida útil em fadiga.
São necessárias três cargas para testar corretamente os parafusos: carga de rocha, ressalto central e ressalto de borda (ver Figura 1). Essas cargas representam as forças a que o parafuso está sujeito em seu ambiente real de serviço. Para a estrutura lateral, também são necessárias três cargas: torção vertical, transversal e central (ver Figura 2). Todos esses vetores de força separados são importantes para apresentar as cargas adequadas e a distribuição de tensão ao corpo de prova e ajudam a garantir uma vida de fadiga adequada.
Para testar os parafusos e as armações laterais, uma estrutura de carga de piso com a classificação adequada é ideal e é relativamente simples de fixar. Os testes de fadiga da estrutura do bogie, no entanto, são mais sofisticados e complexos. Os testes de certificação do bogie são definidos por padrões internacionais e locais, e exigem um número maior de canais e uma fixação muito mais complicada. As configurações de carga para o teste são baseadas na configuração do bogie. O número de eixos por bogie, o número de bogies por vagão, e o peso combinado do bogie e do vagão são alguns dos parâmetros que determinam as cargas necessárias para o teste. Os testes de certificação exigem um sistema de carregamento multicanal e de alta força e normalmente executam milhões de ciclos. Durante um teste, são coletados e analisados sinais de tensão e outros sinais para ajudar os projetistas a entender a dinâmica de carga do ambiente de serviço, identificar áreas de alto estresse e melhorar os projetos de acordo. Ao comparar as respostas de tensão com modelos de análise de elementos finitos (FEA), os engenheiros podem validar os modelos, o que melhora os projetos futuros.
TESTE AVANÇADO DE FADIGA
As normas de certificação são rigorosas e envolvem milhões de ciclos de carga, mas se concentram exclusivamente no conjunto mínimo de cargas (verticais, transversais e empenos) necessário para verificar a vida útil de fadiga e o fator de segurança adequados. Essas cargas são significativamente maiores do que as esperadas durante a operação normal. Os históricos de carga são propositalmente conservadores para garantir uma taxa de falha o mais próxima possível de zero em todas as combinações possíveis de uso. Esta abordagem provou ser adequada para bogies de carga comuns e tem sido adotada (de alguma forma ou outra) em todo o mundo.
No moderno material circulante de passageiros, entretanto, os bogies, as suspensões e a interface do carro são muito mais complexos do que com o frete. Os bogies de passageiros de alta velocidade são soldagens complexas. Itens como amortecedores, elos de suspensão e componentes auxiliares (compressores, pinças de freio) todos apresentam cargas adicionais para o bogie. Essas cargas são frequentemente compostas de vetores e locais de carga muito diferentes daqueles descritos pela norma de certificação. Os locais, magnitudes, vetores e fases dessas cargas são importantes a serem considerados para engenheiros de teste interessados em replicar o ambiente real de operação do bogie da forma mais realista possível.
A complexidade rapidamente se torna um problema nestas circunstâncias. Enquanto os testes de certificação normalmente usam menos de 10 canais (na maioria dos casos, menos de seis), os testes de desenvolvimento mais avançados podem precisar de mais de 20 (e em alguns casos mais de 30) canais de controle. A combinação de cargas adicionais com as cargas prescritas pelas normas de certificação representa um grande desafio em termos de fixação.
Abordar esta complexidade é essencial. Durante os últimos 10 a 15 anos, a demanda cresceu consideravelmente entre os usuários finais por material circulante que proporciona maior confiabilidade, melhor desempenho e maior conforto. Para atender a essas necessidades, os fabricantes estão desenvolvendo materiais e métodos de fabricação que não estavam disponíveis quando as normas de certificação foram estabelecidas pela primeira vez. Novos materiais - e especialmente novos métodos de redução de peso - utilizados no projeto e fabricação de praticamente todos os componentes do sistema ferroviário criaram uma necessidade de novos procedimentos de testes de desenvolvimento que estão fora do escopo dos testes tradicionais de certificação.
Para estas aplicações estruturais maiores, são necessárias estruturas de portal de duas ou quatro colunas com configurações personalizadas de atuadores (ver Figura 3). Como muitas das forças em um bogie são altas, os atuadores usados para replicar essas cargas são grandes. A aplicação direta de atuadores em pontos de carga pode exigir vários atuadores para ocupar o mesmo espaço físico simultaneamente. Este é um problema que requer uma experiência substancial em mecanismos de fixação e cinemática para ser resolvido. Combinações de atuadores, alavancas, escoras (colunas de suporte de carga) e rolamentos são utilizadas para aplicar os vetores de carga nos locais corretos. Os sensores de carga podem ser instalados em atuadores, escoras de carga e/ou dispositivos de reação. Os rolamentos giratórios em ambas as extremidades das escoras e atuadores eliminam as cargas laterais e de flexão. Em alguns casos, o corpo de prova pode ser invertido para permitir melhor acesso aos pontos de carregamento.
O engate cruzado - quando a ação de um atuador afeta outro - apresenta sérios problemas de controle que devem ser superados. O controlador digital e o software devem trabalhar em conjunto para coordenar a amplitude e o faseamento dos canais afetados para remover o risco de interferência e garantir uma carga precisa. Normalmente, técnicas avançadas de controle estão envolvidas. Todo o sistema, incluindo o corpo de prova, a estrutura e o subsistema de atuadores, pode conter algumas não linearidades naturais. A contabilização dessas não linearidades pode exigir a modificação dos sinais de acionamento para alcançar o histórico de carga desejado no corpo de prova.
Os ajustes são normalmente feitos com software avançado de processamento de sinais, como o MTS Remote Parameter Control (RPC®), que se baseia na matriz da função de resposta de frequência (FRF) de todo o sistema. O software mede o comando do controlador e o compara com a amplitude e fase das respostas dos corpos de prova em toda a faixa de frequência desejada. É gerada uma matriz de acoplamento cruzado que inclui todos os acoplamentos cruzados e outras diferenças lineares entre comando e resposta. Este FRF é então invertido e multiplicado pela resposta desejada. O resultado é um arquivo de acionamento do atuador que compensa os acoplamentos cruzados e questões relacionadas. As contribuições não lineares são corrigidas calculando o erro, criando um arquivo de correção correspondente, e depois aplicando a correção ao arquivo de unidade anterior. Este processo iterativo é repetido até que a precisão desejada seja alcançada. A aplicação de tais técnicas de compensação de controle permite que o teste seja executado com precisão a uma frequência muito maior, o que reduz o tempo de teste e aumenta a qualidade do teste.
Enquanto isso ocorre, os engenheiros devem ser capazes de coletar e gerenciar grandes quantidades de dados. O sistema de teste pode precisar acomodar, por exemplo, até 250 strain gage e canais de deslocamento para encontrar possíveis vulnerabilidades no projeto. Alguns desses dados precisam ser coletados em tempo real para uso no sistema de controle, enquanto que quantidades ainda maiores de dados precisam ser coletadas para análise e comparação offline com modelos de engenharia auxiliada por computador (CAE).
Superar todos esses desafios é difícil, mas vale a pena o investimento. Os resultados permitem aos fabricantes de componentes otimizar projetos, diferenciar novas ofertas de produtos e proporcionar a confiança que os clientes precisam na qualidade e confiabilidade dos novos componentes.
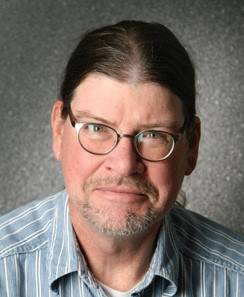