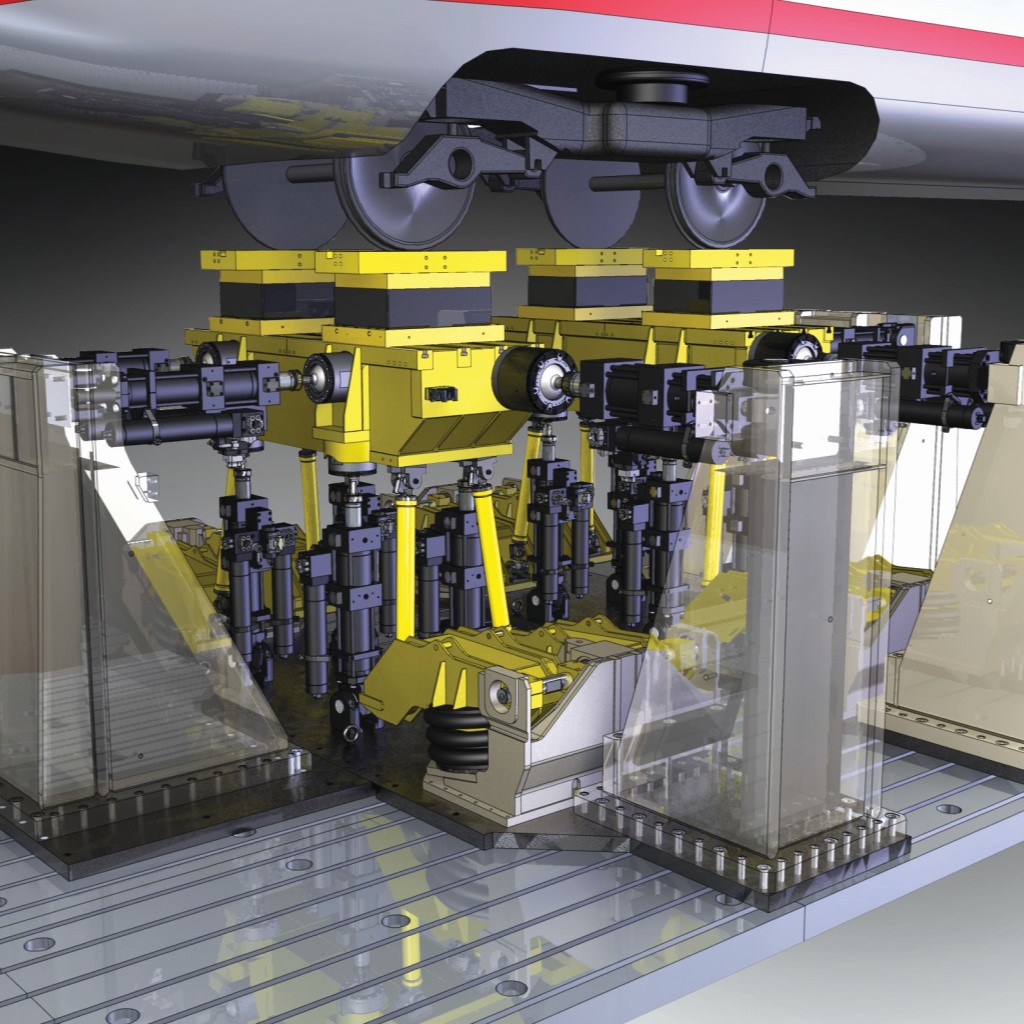
O crescimento global das viagens de trem está aumentando a demanda por novos vagões de passageiros, o que é uma notícia bem-vinda para os fabricantes em todo o mundo. Ao mesmo tempo, esses novos carros devem atender a expectativas mais elevadas. Os modernos vagões de passageiros precisam viajar a velocidades mais altas, proporcionar uma viagem confortável, maximizar a eficiência energética e, é claro, atingir a conformidade total com as regulamentações.
Abordar essas necessidades simultaneamente apresenta um conjunto difícil de desafios de projeto. A eficiência depende da remoção do peso, mas isto não pode afetar a estabilidade. A estabilidade se torna mais difícil em altas velocidades, e os vagões mais rápidos do mundo anda, agora a até 350 quilômetros por hora. O conforto de viagem também é mais difícil de alcançar em altas velocidades.
Como estes fatores estão relacionados, os fabricantes devem ser capazes de otimizar novos projetos a fim de gerenciar as compensações de forma eficaz. Por exemplo, um bogie mais rígido pode proporcionar maior estabilidade, mas menos conforto ao viajante. A rigidez das barras rolantes pode ser mudada para proporcionar melhor manuseio ou uma experiência mais confortável para os passageiros, mas não as duas coisas ao mesmo tempo.
As equipes de desenvolvimento de produtos estão sob intensa pressão de tempo devido à alta demanda do mercado, e os projetistas devem trabalhar rapidamente. É aqui que os testes mecânicos se tornam muito úteis.
DESAFIOS NO LABORATÓRIO
No laboratório de testes, os projetistas de componentes podem examinar muitas iterações de um novo projeto relativamente rápido de uma maneira altamente controlada e repetível. Os resultados dos testes revelam coeficientes e outros fatores que podem ser introduzidos novamente em modelos virtuais de componentes e subsistemas para torná-los mais precisos. Isto ajuda a acelerar o processo de análise e aperfeiçoamento de novos projetos.
O laboratório oferece seus próprios desafios. A lista de testes relevantes é longa, e cada um deles normalmente requer um tipo diferente de sistema de teste com uma configuração única. Adquirir os sistemas necessários para otimizar novos projetos de bogie pode ser caro. A configuração e execução dos testes pode se tornar ineficiente quando múltiplos sistemas estão em uso.
O maior desafio de todos é a necessidade de testar todo o mecanismo, não apenas um único componente. Isto pode parecer contra intuitivo, mas os engenheiros de projeto avançados compreendem que testar peças individualmente não fornece a mesma precisão ou insight que testar um bogie completo.
Embora os testes discretos de componentes sejam mais fáceis de gerenciar e possam ser realizados rapidamente, eles não oferecem a mesma precisão que os testes de todos os componentes de um sistema. As interações de componentes produzem comportamentos inesperados devido ao atrito e movimentos fora do eixo. Estas interações não podem ser replicadas pela avaliação de cada componente separadamente. Há muito tempo os engenheiros suspeitam que este era o caso, mas só na última década é que isso se tornou óbvio. Os modelos virtuais se tornaram mais sofisticados, mas os engenheiros não conseguiram prever com precisão o desempenho do sistema sobre o trilho, com base nas características individuais dos componentes.
Recentemente, foi colocado em serviço um sistema inovador de teste de vagões que pode ser usado para medir a cinemática e a conformidade de um mecanismo completo de bogie. O sistema, fornecido pela MTS Systems Corp., também pode ser usado para fornecer caracterização, durabilidade básica e testes de vibração, tudo em um único sistema.
TESTES DE SUSPENSÃO PRIMÁRIA E SECUNDÁRIA
Atualmente instalado em um fabricante de vagões de passageiros de alta velocidade na Ásia, o novo sistema de medição de bogies fornece o tamanho e a força necessários para carregar um bogie completo, bem como um vagão completo. O sistema de teste incorpora instrumentos consideráveis projetados para medições extremamente precisas desses complexos mecanismos.
A complexidade vem das muitas maneiras pelas quais os dados de teste podem ser distorcidos. Para garantir resultados precisos, os sistemas de teste devem ser capazes de evitar (ou compensar) todos os fenômenos a seguir: deslocamento de fase causado por chicote ou amortecimento; distorção do sinal e ruído causados por ressonâncias do sistema e dos corpos de prova; e erros de medição de força decorrentes de cross-talk, compensação de temperatura dos transdutores, expansão térmica e contração dos dispositivos e corpos de prova, erros de calibração, deslizamento, deriva ou danos aos transdutores, suportes, cabos ou condicionadores. Em muitos casos, vários sinais são combinados para calcular o resultado desejado, compondo o erro total.
Alguns dos testes mais importantes que o sistema realiza são os da suspensão primária, que inclui todos os componentes entre o bogie e o eixo (mola, mola helicoidal, barra de torção, calha de borracha, etc). Enquanto a suspensão primária afeta a direção, o manuseio e até certo grau o conforto do viajante, os engenheiros precisam entender o conjunto completo de rodas e o sistema de suspensão em grandes detalhes para otimizar novos designs. A rigidez da suspensão primária está na mesma faixa que a rigidez da estrutura do bogie, e a interação entre os dois determina a resposta geral de manuseio do bogie. Por este motivo, o novo sistema de teste é projetado exclusivamente para medir as contribuições individuais dos componentes ou a característica de montagem completa como um sistema integrado.
O teste de rigidez da suspensão primária envolve a fixação da suspensão secundária, montagem de transformadores diferenciais lineares variáveis (LVDTs) na carcaça do rolamento do eixo e pontos de resposta do bogie, e aplicação de força programada ou deslocamento em cada um dos graus de liberdade desejados (DOF). Para alcançar um resultado útil, os engenheiros precisam garantir a precisão e a resolução das células de carga e dos LVDTs, manter uma temperatura constante no laboratório e fazer medições em diferentes taxas para avaliar as características de amortecimento. É importante medir a rigidez do bogie em cada direção, não apenas na vertical, porque a estabilidade é uma função dos deslocamentos multiaxiais combinados, não apenas na vertical. Durante as curvas, por exemplo, as deformações do bogie (deformações no eixo de guinada) e a rigidez da deformação é crítica para uma direção estável.
Esta mesma configuração pode ser usada para realizar um teste de amortecimento da suspensão primária e avaliar o amortecimento em relação à rigidez da mola. Os dados de teste de suspensão primária são muito úteis para alimentar os modelos virtuais do bogie tanto para a geração de modelos quanto para a validação.
Outro conjunto importante de testes são os realizados na suspensão secundária, que está localizada entre a parte superior do bogie e a parte inferior do vagão. Para estes testes a suspensão primária é fixa e a suspensão secundária, normalmente um par de bolsas de ar, é montada em células de carga multiaxial. Uma fixação simulada de vagão é limitada em 3DOF e controlada no 3DOF restante para apresentar a suspensão secundária com as mesmas cargas e deformações que ela vê em serviço. Isto permite avaliar a rigidez e as características de amortecimento. Devido à forma canelada do "chapéu" do air bag, prever a rigidez lateral e do rolo é particularmente desafiador. O material elastomérico deforma de forma imprevisível, e esses movimentos afetam muito o conforto da viagem.
TESTES DE DESEMPENHO ADICIONAIS
Outro tipo de teste que este sistema pode realizar é a medição do torque de resistência da direção, na qual o bogie é girado sob o vagão simulado e sua rigidez é medida. Para realizar este teste, cargas ou deslocamentos laterais iguais e opostos são aplicados a cada eixo. As forças de tensão/compressão e longitudinais são ajustadas a zero e os atuadores verticais são comandados para manter a força desejada ou movimento plano fixo nas rodas.
Além disso, o sistema de teste pode ser configurado para testar o coeficiente de suspensão para pista reta ou curva. Neste teste, o corpo de prova é um vagão completo (ou simulado) com giroscópios medidores de ângulo nas mesas, bogies e carroceria do carro. O teste envolve levantar as rodas de um lado do bogie até uma super-elevação desejada e medir o ângulo do bogie e do carro em relação ao ângulo da mesa. Estas relações podem ser difíceis de prever devido aos muitos elementos da suspensão completa. Os fabricantes podem usar um teste semelhante para compreender o coeficiente de capotagem, que é vital para garantir o conforto e a segurança do passeio.
Carros ferroviários completos também podem ser avaliados. Se os engenheiros quiserem entender a resposta dinâmica para testes de coeficiente, o sistema pode ser comandado com amplo ruído em forma de banda ou formas específicas de onda, como uma onda sinusoidal. A resposta da carroceria do vagão é medida e sua frequência natural pode ser estimada a partir dos dados resultantes usando um software de teste.
Outros testes que o sistema pode realizar incluem localização do centro de gravidade, momento de teste de inércia e reprodução em tempo real de dados operacionais em trilhos.
Embora seja verdade que um sistema de testes de desempenho multiuso representa um investimento de capital significativo para o laboratório, ele proporciona um retorno de investimento igualmente significativo através de sua capacidade de acelerar o cronograma de testes, reduzir custos e melhorar a precisão dos dados dos testes e da caracterização dos corpos de prova. Em última análise, estas capacidades permitirão aos fabricantes de vagões e bogies melhorar a precisão dos modelos, alcançar inovação mais rapidamente, fabricar veículos de maior qualidade e construir uma vantagem competitiva duradoura.
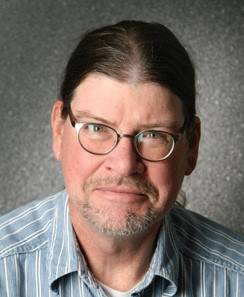