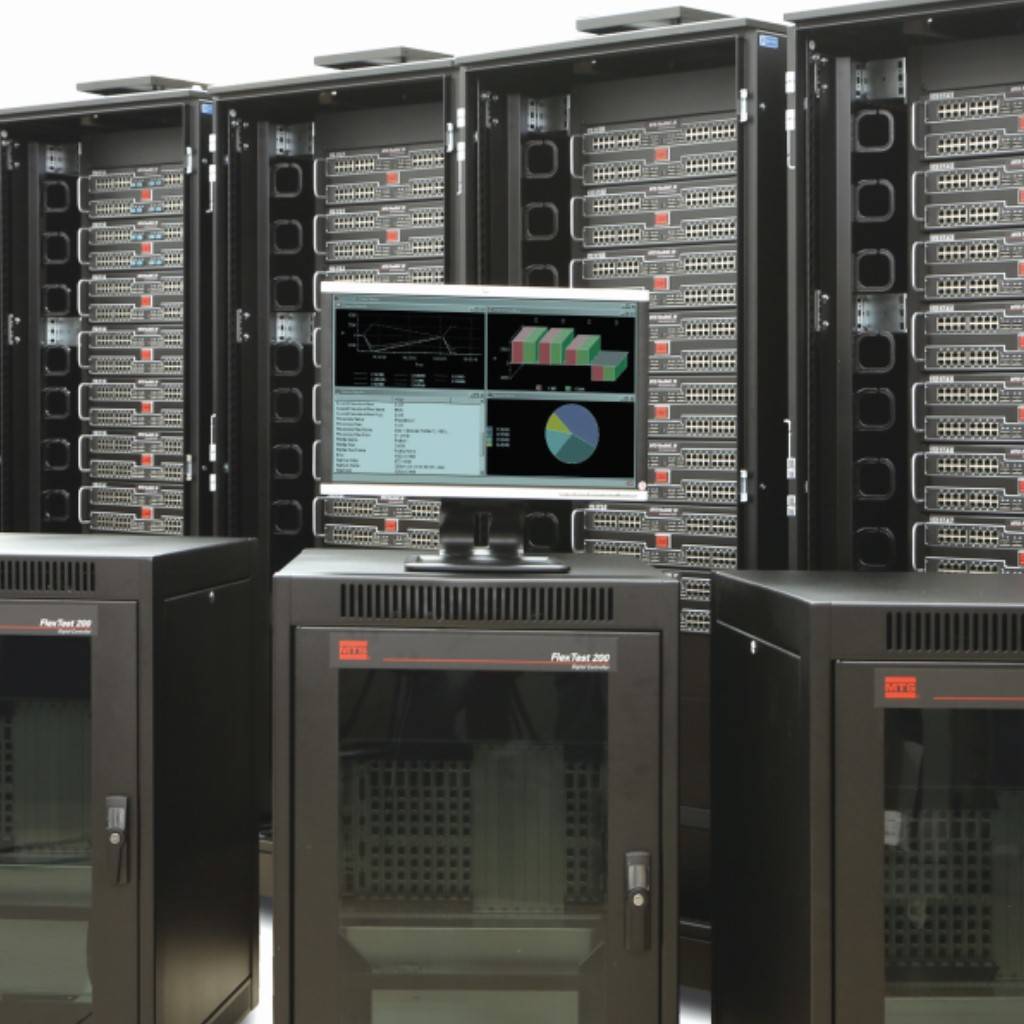
Q: How has data acquisition changed over the past decade?
A: We've seen continued advancement in the number of channels as structural test teams try to get as many gages as possible on the specimen to better understand load paths and correlate them with models. There has been tremendous acceleration in this area over the past few years. Today, test teams are placing as many as 10,000 gages on a full-frame aircraft, and this number is only going to rise. At the same time, pressure to bring new aircraft to market faster drives the need to accelerate test schedules. But it takes more time to configure more gages, so it’s important for test teams to understand the value those extra gages bring, and the process needs to be completed as efficiently as possible.
Q: What are some of the ways test labs can optimize test efficiency?
A: A couple ideas come to mind. You need test software that is designed to speed the setup process. And you need maximum flexibility with respect to how the data acquisition channels are distributed across tests. With some systems, as soon as you dedicate one channel of the DAC box to a specific test, you sacrifice the whole box. For labs running multiple tests with fewer channels apiece, that is not ideal. If you can split up the channels, you don’t have to manage a separate box for every test, which is very efficient. This is why MTS FlexDAC 20 systems are designed to distribute channels in any proportion across as many as eight test stations at the same time. MTS offers the only DAC system that can do this.
Q: Do labs need to replace existing DAC systems to benefit from this flexibility?
A: No, that would not be very cost-effective. The MTS FlexDAC 20 systems can work alongside DAC units from other providers on the same test and the lab can manage all of them with MTS AeroPro software. This integration allows you to add channel count with MTS DAC systems while protecting the lab’s investment in current systems. For even more flexibility, labs can mix and match the two types of FlexDAC chassis, the A32 and B24, in any combination, depending on the lab’s needs. Within AeroPro, it’s very easy to distinguish the various platforms. Data from non-MTS DAC systems is combined, while data acquired via FlexDAC offers the industry’s only hardware-based clock synchronization with FlexTest controllers.
Q: Why is hardware-based clock synchronization important?
A: It’s critical to know what load level produces a given strain value. If there is any skew between the controller and the data acquisition system, it introduces troubling questions about what load was actually applied to produce the strain. We avoid this with a hard sync between the FlexDAC 20 systems and FlexTest controllers through AeroPro software. Specifically, FlexDAC 20 units employ the same internal clock as FlexTest controllers, so you get a scan of the data at exactly the same clock tick. It generates truly synchronized control and data acquisition streams. Without it, you have to port data after the fact from two separate software applications and stitch it together—but it’s not perfect. Our approach has zero skew between the load and data acquisition.
Q: Are there other advantages to integrating DAC with controllers and software?
A: The real benefit is that you can manage everything with one software application, as opposed to using separate tools to run the controller and the data acquisition, which, again, involves some level of back-end data integration. This is why FlexDAC 20 systems are designed from day one to be fully compatible with AeroPro. On a practical basis, this means test engineers can display plots, charts and readings as well as view limits for all data acquisition channels with one application, regardless of the DAC manufacturer. You can perform shunt calibration, shunt validation and many other operations on hundreds of thousands of channels simultaneously. Setup wizards speed everything along, so operators spend less time on setup and more time on the test. You can even prepare sensors and hardware assignments offline and import them into AeroPro. And you only have one user interface, which helps address increasing test complexity.
Q: Are there other ways labs can increase efficiency?
A: Automatic calibration is an important part of this. MTS has created an automated calibration method that takes about ten minutes to verify and document that every FlexDAC 20 chassis is performing to our specifications. It involves more than 1,200 separate electrical measurements and calculations. You can even calibrate without disrupting the test setup. There is no need to remove cables from boxes, which saves time and lowers the risk of errors. Of course, strain gage data is what gets delivered to the regulatory agencies, so it’s critical to be able to verify the performance of the DAC system's conditioners.
A: We've seen continued advancement in the number of channels as structural test teams try to get as many gages as possible on the specimen to better understand load paths and correlate them with models. There has been tremendous acceleration in this area over the past few years. Today, test teams are placing as many as 10,000 gages on a full-frame aircraft, and this number is only going to rise. At the same time, pressure to bring new aircraft to market faster drives the need to accelerate test schedules. But it takes more time to configure more gages, so it’s important for test teams to understand the value those extra gages bring, and the process needs to be completed as efficiently as possible.
Q: What are some of the ways test labs can optimize test efficiency?
A: A couple ideas come to mind. You need test software that is designed to speed the setup process. And you need maximum flexibility with respect to how the data acquisition channels are distributed across tests. With some systems, as soon as you dedicate one channel of the DAC box to a specific test, you sacrifice the whole box. For labs running multiple tests with fewer channels apiece, that is not ideal. If you can split up the channels, you don’t have to manage a separate box for every test, which is very efficient. This is why MTS FlexDAC 20 systems are designed to distribute channels in any proportion across as many as eight test stations at the same time. MTS offers the only DAC system that can do this.
Q: Do labs need to replace existing DAC systems to benefit from this flexibility?
A: No, that would not be very cost-effective. The MTS FlexDAC 20 systems can work alongside DAC units from other providers on the same test and the lab can manage all of them with MTS AeroPro software. This integration allows you to add channel count with MTS DAC systems while protecting the lab’s investment in current systems. For even more flexibility, labs can mix and match the two types of FlexDAC chassis, the A32 and B24, in any combination, depending on the lab’s needs. Within AeroPro, it’s very easy to distinguish the various platforms. Data from non-MTS DAC systems is combined, while data acquired via FlexDAC offers the industry’s only hardware-based clock synchronization with FlexTest controllers.
Q: Why is hardware-based clock synchronization important?
A: It’s critical to know what load level produces a given strain value. If there is any skew between the controller and the data acquisition system, it introduces troubling questions about what load was actually applied to produce the strain. We avoid this with a hard sync between the FlexDAC 20 systems and FlexTest controllers through AeroPro software. Specifically, FlexDAC 20 units employ the same internal clock as FlexTest controllers, so you get a scan of the data at exactly the same clock tick. It generates truly synchronized control and data acquisition streams. Without it, you have to port data after the fact from two separate software applications and stitch it together—but it’s not perfect. Our approach has zero skew between the load and data acquisition.
Q: Are there other advantages to integrating DAC with controllers and software?
A: The real benefit is that you can manage everything with one software application, as opposed to using separate tools to run the controller and the data acquisition, which, again, involves some level of back-end data integration. This is why FlexDAC 20 systems are designed from day one to be fully compatible with AeroPro. On a practical basis, this means test engineers can display plots, charts and readings as well as view limits for all data acquisition channels with one application, regardless of the DAC manufacturer. You can perform shunt calibration, shunt validation and many other operations on hundreds of thousands of channels simultaneously. Setup wizards speed everything along, so operators spend less time on setup and more time on the test. You can even prepare sensors and hardware assignments offline and import them into AeroPro. And you only have one user interface, which helps address increasing test complexity.
Q: Are there other ways labs can increase efficiency?
A: Automatic calibration is an important part of this. MTS has created an automated calibration method that takes about ten minutes to verify and document that every FlexDAC 20 chassis is performing to our specifications. It involves more than 1,200 separate electrical measurements and calculations. You can even calibrate without disrupting the test setup. There is no need to remove cables from boxes, which saves time and lowers the risk of errors. Of course, strain gage data is what gets delivered to the regulatory agencies, so it’s critical to be able to verify the performance of the DAC system's conditioners.