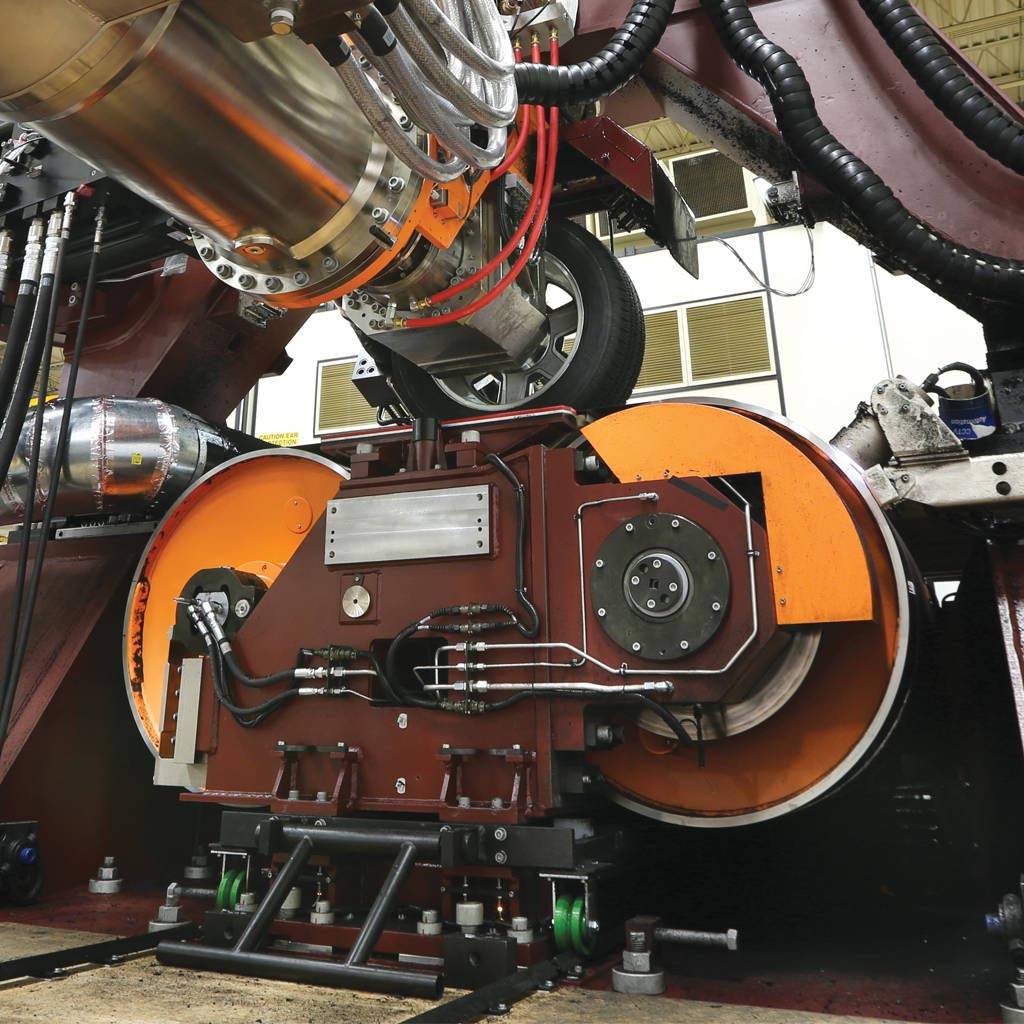
CUSTOMER CHALLENGE
The National Tire Research Center (NTRC) in Alton, Virginia, offers a full spectrum of tire testing capabilities designed to support the research and development efforts of vehicle and tire manufacturers around the world. According to the facility’s operations director, Jonathan Darab, the NTRC offers test equipment and in-house expertise manufacturers simply can’t find anywhere else. As such, he expects the facility to have a tremendous impact on the future of tire testing and virtual vehicle development.
“The closest thing to compare it to is when we went from bias to radial,” Darab said. “It was just a huge leap, in terms of the technology used to produce the tires and the performance of the tires themselves. That’s how I see our capabilities.”
To reach this level, the NTRC had to find test equipment that did not yet exist. Specifically, the facility needed a system that could replicate a wider variety of operating conditions and driving events, including the double lane change in which a driver swerves to avoid a crash and then overcorrects in the opposite direction. This maneuver, which is a frequent cause of rollovers, is what must be replicated to pass the Federal Motor Vehicle Safety Standard (FMVSS) No. 126 test. This standard requires all cars and trucks weighing less than 10,000 pounds to have an electronic stability control system by 2013.
“Right now, there is not a tire testing system that can accurately replicate the 126 maneuver in the lab,” Darab said. “To make sure new designs pass the test, vehicle OEMs and tire manufacturers must extrapolate data based on other similar events. So, instead of having 95 percent confidence a new model will pass, they are more like 80 percent confident.”
MTS SOLUTION
The 126 maneuver creates a serious issue for OEMs, who must tune vehicles to avoid certain frequency levels as well as augment virtual development efforts with additional, resource-intensive physical tests. OEMs do not have a choice, however, because any vehicle that fails the FMVSS 126 test in production incurs significant financial penalties and hurts the brand’s public image. This is exactly why the NTRC set out to find a tire testing system that could perform the 126 maneuver – among others.
This led the NTRC to work with MTS. For more than 30 years, MTS Flat-Trac® Tire Test Systems have led the industry in flat surface force and moment measurement. This legacy made MTS the natural choice. After collaborating on system requirements with the NTRC, MTS developed the Flat-Trac LTRe, a tire testing system that offers exclusive capabilities and supports advanced virtual development.
“The specifications of the machine were chosen to replicate all the driving maneuvers that a passenger car or light truck tire will see in the real world, including the 126 maneuver,” Darab said. “That’s why we insisted on 90°/s slip and 38°/s camber angles, among other things. We wanted to make sure that 95 percent of OEM products could be tested on this machine.”
The biggest differentiator of the Flat-Trac LTRe is its electric permanent magnet motor, or spindle torque drive. This motor delivers the high power density and ultra-high performance bandwidth required to apply driving and braking torque at full roadway speeds, under physical loads up to 30,000 N in all three force directions. Other key features include a specialized water bearing that keeps the roadway belt flat throughout the entire speed and load range of the system, and a second electric motor that runs the roadway up to 200 mph (320 kph) for replicating cornering maneuvers common in motorsports.
CUSTOMER BENEFITS
With all of these capabilities, the Flat-Trac LTRe enables vehicle OEMs and tire manufacturers to test a wider range of tire designs up to and beyond their physical limits.
“We’re creating a whole new genre of testing,” said Frank Della Pia, Executive Director for the NTRC. “There will not be a peer facility for the NTRC. When you add up all the capabilities the NTRC has to offer, it’s going to be a transformational leap in tire technology.”
What is important to manufacturers is that the Flat-Trac LTRe facilitates tire testing in conditions not previously attainable in a controlled laboratory environment. OEMs will not only be able to test tires in new ways, but also evaluate tire interactions with other components and subsystems using hybrid simulation, or hardware-in-the-loop testing. In this context, the LTRe system runs in tandem with a full-vehicle computer model. When the virtual vehicle executes a maneuver, the LTRe system replicates it on a real tire. The response of the tire is then fed back into the model to improve the simulation’s accuracy.
“When OEM test teams come to the NTRC, they will be able to test a single tire instead of instrumenting an entire vehicle,” Darab said. “They will be able to run thousands of simulations in two days, instead of spending those same two days running a single test with a potential error rate of 20 percent.”
So far, implementation of the LTRe system has gone well. Della Pia attributes this to how well the two teams worked together as the LTRe was being developed.
“Working with MTS, I definitely had the feeling we were all on the same team,” Della Pia said. “We were all trying to execute the science and do it right. It’s been a great experience.”