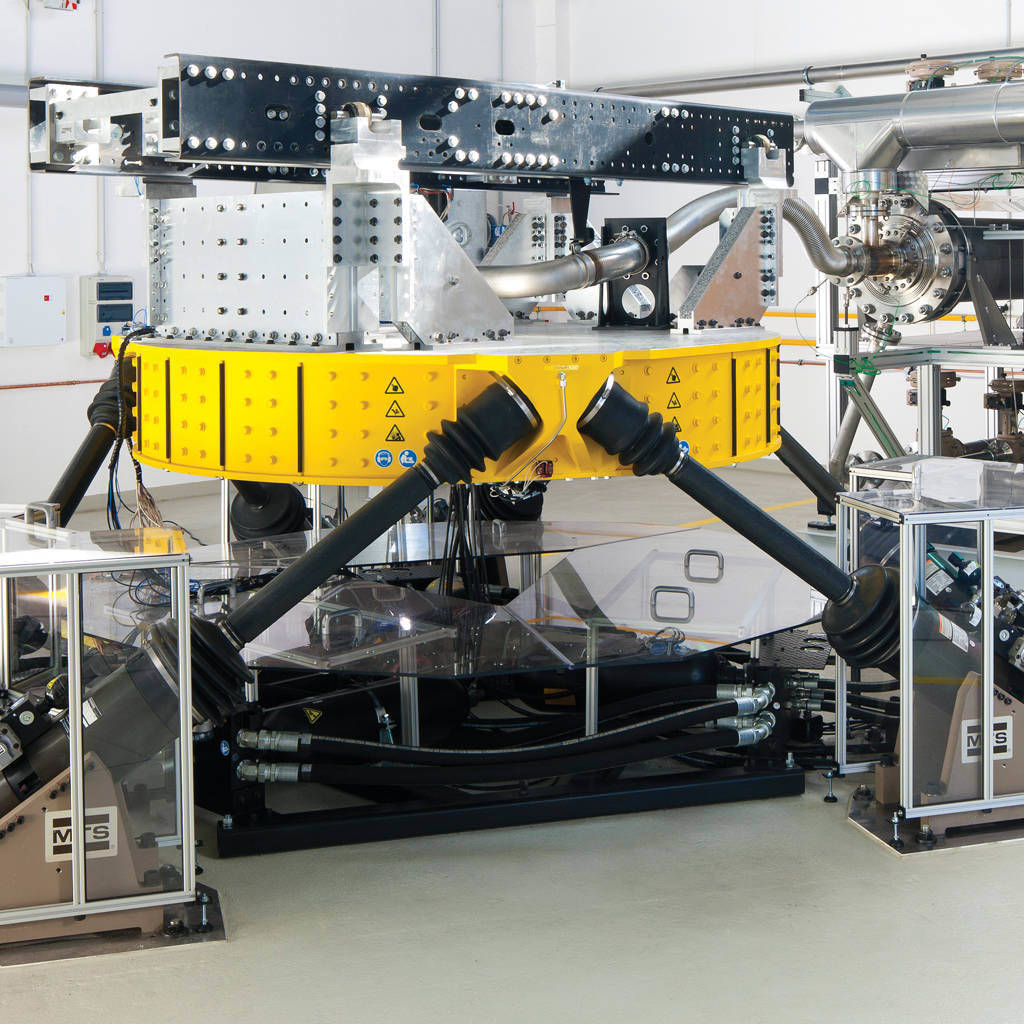
CUSTOMER CHALLENGE
Founded in 1993, IMA Materialforschung und Anwendungstechnik GmbH (IMA) is an engineering services provider and contract test lab that offers a wide range of services for the aerospace, automotive, rail and wind energy industries. Located in Dresden, Germany, IMA focuses primarily on the characterization, verification and certification of materials and structural components.
Because IMA is involved in so many industries its testing work load is dynamic and varied, reflecting its customers’ needs to respond to evolving market requirements. The pressure to bring new products to market rapidly is intense across all of the industries IMA serves, so fast response time is a basic expectation. Of course, IMA’s customers also demand accurate, high-quality results that will help them accelerate and optimize the product development process.
“Our main task is solving the customer’s problem,” said Timo Grahnert, head of sales for IMA. “We have to develop, configure and operate unique test setups every day. Each setup is used to test material behavior undergoing different loading. Our test systems have to be highly flexible, and results have to be reliable.”
This challenge is particularly difficult in automotive testing, where the loading schemes for durability testing can become quite complex.
“We have to simulate operational loads through a broad range of signal frequencies,” Grahnert said. “No matter what, our customers expect very fast reaction time. As a result, we require highly flexible test systems with modular configurations that can easily adapt to new test arrangements.”
MTS SOLUTION
One of the tools IMA deploys to meet the challenge of constantly evolving test configurations is a MAST (Multiaxial Simulation Table) system from MTS. This system, a Model 353 with a hexapod design, forms the foundation of a custom test rig developed by MTS and IMA engineers to perform service life verification of automotive components subjected to mechanical vibration in six degrees of freedom (6DOF). The custom test rig also features a multi-flow natural gas burner for thermal loading, which allows test engineers to select a precise mix of natural gas, combustion air and mixed air for a wide range of temperatures and flow rates.
“We have to be very flexible,” Grahnert said. “That’s very important, and that’s why we are using MTS systems.”
Taking advantage of the MAST system’s high-frequency vibration capabilities, IMA performs complex durability tests on next-generation exhaust systems and other vehicle body components, as well as additional tests that evaluate how components respond to internal and external thermal shocks. Tests run the gamut from single-channel to multi-channel, with each one requiring a carefully controlled execution of temperatures, accelerations and forces.
“We are often testing brand new components from the customer, which means there is no precedent to follow,” Grahnert said. “We are also combining vibration with thermal loads. Some of the exhaust system tests can run up to two weeks. We need accuracy of simulation, and the results must be reproducible. MTS helps us achieve all of these goals.”
CUSTOMER BENEFITS
For IMA, the most important advantage of the MTS MAST system is its ability to be quickly configured for a wide variety of test setups. Specifically, the system’s 6DOF capabilities enable IMA to achieve accurate simulations of difficult-to-characterize service environments through the inclusion of key high-frequency content and the excitation of critical nonlinear response effects.
The system incorporates a MTS FlexTest® digital controller, which provides high-speed closed-loop control, function generation, transducer conditioning and data acquisition for a full range of testing needs. In addition, test engineers at IMA rely on MTS Component RPC® Pro software to analyze results in real-time, including time history, time out, calculated channels and FFT (Fast Fourier Transform) adjustment. Both the controllers and the software offer the flexibility to provide control and analysis for all the unique test configurations IMA must accommodate.
The expertise of the local MTS support team also plays a critical role. “MTS is very good at what they do,” Grahnert said. “They are very engaged, dedicated and fast. Every time we need help, we get a quick response.”
Right now, MTS and IMA are working together to expand the application of the MAST system to other components that must withstand both vibration and heat in their normal operating environments, including components of vehicle heating systems and radiators.
“MTS test systems are state-of-the-art equipment,” Grahnert said. “And the cRPC Pro software is the industry standard for automotive testing. With this solution in our test lab, IMA is well positioned to simulate an even larger range of complex loading situations.”