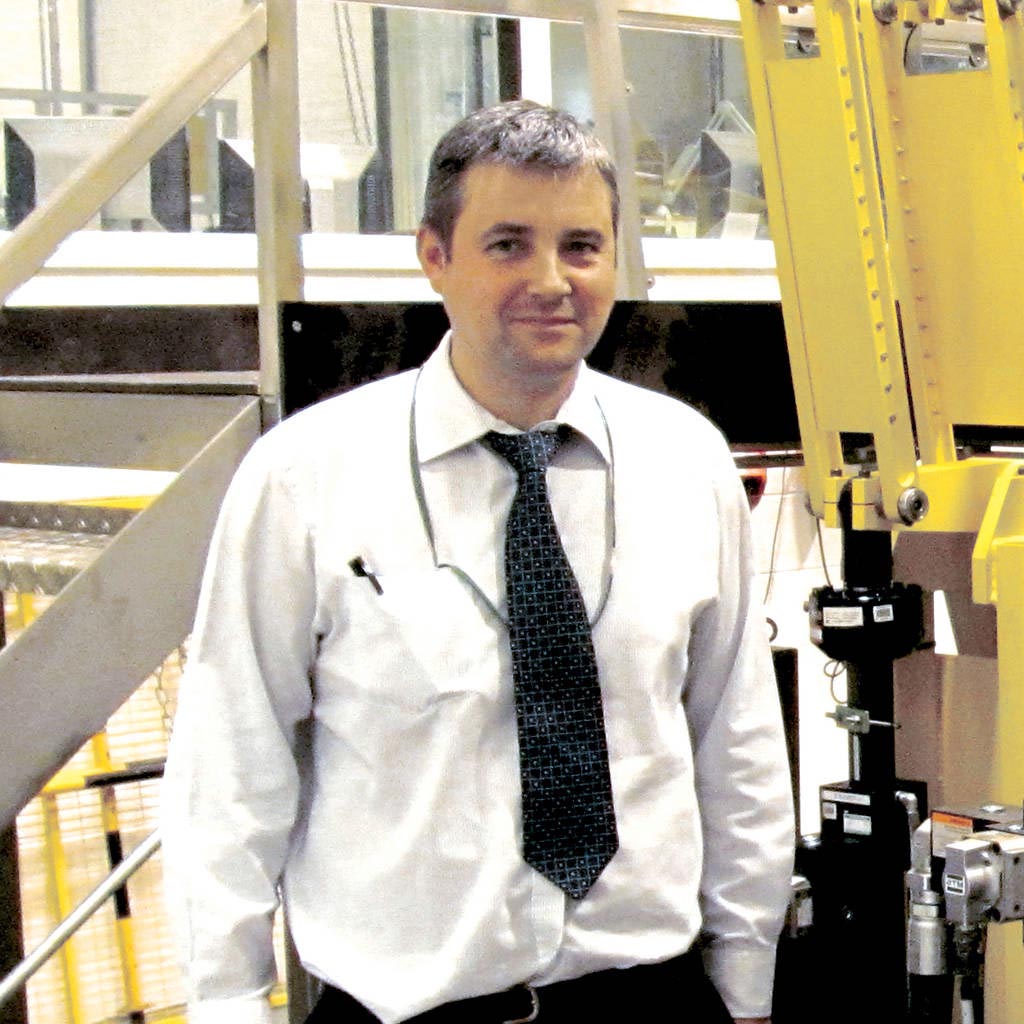
CUSTOMER CHALLENGE
Jaguar Land Rover (JLR) offers a diverse portfolio of vehicles, manufacturing some of the world’s best-known luxury cars and 4x4s. To support the ongoing development of this portfolio, structural test engineers at two sites in the UK are kept busy performing batteries of durability tests on numerous components, subsystems and vehicle prototypes. Among those leading this effort is Ian Payne, group leader for product analysis and verification. Payne’s team is responsible for the test rigs used to assess the strength and endurance of all JLR products from the component level up to full vehicle simulation.
“We design, manufacture and operate equipment ranging from single-axis rigs right through to state-of-the-art full vehicle road simulators in all of our laboratories,” Payne said. “We’re the foundation of vehicle durability verification. The data we gather supports product development across the entire business.”
One of the biggest challenges Payne faces is the constant pressure to produce better results more quickly, accelerating speed to market for new products. As a result, Payne and his team seek every opportunity to improve the accuracy and efficiency of testing. One way they are approaching the problem is through test integration – combining multiple discrete tests into a single, data-rich simulation.
“The top priority for us is to optimize test time,” Payne said. “The downside is we’re getting more complex tests. It is very difficult to simulate all the active systems on our vehicles – such as variable damping, active roll and active differentials – and incorporate all that complexity in a real-time test.”
MTS SOLUTION
Today, JLR is solving this challenge with a pair of MAST (Multi-axial Simulation Table) systems from MTS. Payne’s team uses the MAST systems to verify the structural endurance of complete engine mounting systems, including the power train and drive train, with body inputs, structural engine mount loads and real-time torque delivered through Torque Inputs Fixtures (TIFs).
“We run real-time simulations to establish structural endurance through the correlated predicted life of the vehicle,” Payne said. “With MAST systems from MTS, we can look at the entire engine mounting system at one time. It enables us to look at vehicle packaging as well, including underbonnet packaging and wiring harnesses. It’s a great tool for us.”
Available in both orthogonal and hexapod configurations, MTS MAST systems are engineered to accurately replicate the vibration phenomena of real-world service environments in controlled laboratory settings. The orthogonal systems employed by Payne’s team feature square, resonance-free 2 x 3 meter tables and are capable of providing six degree-of-freedom (6DOF) simulations – three vertical actuators apply vertical, pitch and roll motions, while three horizontal actuators apply lateral, yaw, and longitudinal motions.
“We’re putting direct control loading onto the power train, typically longitudinal and lateral, and occasionally vertical, to ensure the correct mean loads on the engine mounts during testing,” Payne said. “It’s a rather big table. It enables us to package a full 4x4 front power train system with the V8 engine. We run the table at frequencies up to 30 Hz, and the drive torque up to 20 Hz.”
CUSTOMER BENEFITS
According to Payne, MTS MAST systems are essential to combining many formerly separate tests into one. Specifically, the MAST system’s sturdy design and high payload allows Payne’s team to maximize specimen mass, while precision 6DOF motion control provides all the testing capabilities needed for a full spectrum of prototype verification.
“We’re trying to roll as many tests as we can into a single physical prototype,” Payne said. “It’s more complex, but we’re actually saving a great deal of time during development. The test is also more robust because the system interactions are all working together, which is a lot more realistic.”
Increased realism means a single MAST test can shed light on many of the real-world failures JLR teams expect to see once prototypes make it to the test track. Understanding and addressing these failures prior to the proving ground improves efficiency and shortens time to market.
“With a 6DOF test, we get great insight into the full vehicle’s structural endurance,” Payne said. “The MAST system is fantastic for this work. With respect to combining tests and creating more complex full vehicle simulations, our focus is going to stay on the MAST system and 6DOF testing for the time being.”
Test systems, of course, are only one part of the complete solution. MTS also provides industry-leading test software and expert service and support, which Payne’s team has come to rely on.
“We get great support from MTS,” Payne said. “We have strong relationships with everyone on the MTS team, and we have great respect for the expertise the field service engineers bring. Their technical knowledge is most esteemed and will be very valuable as we continue to move forward.”