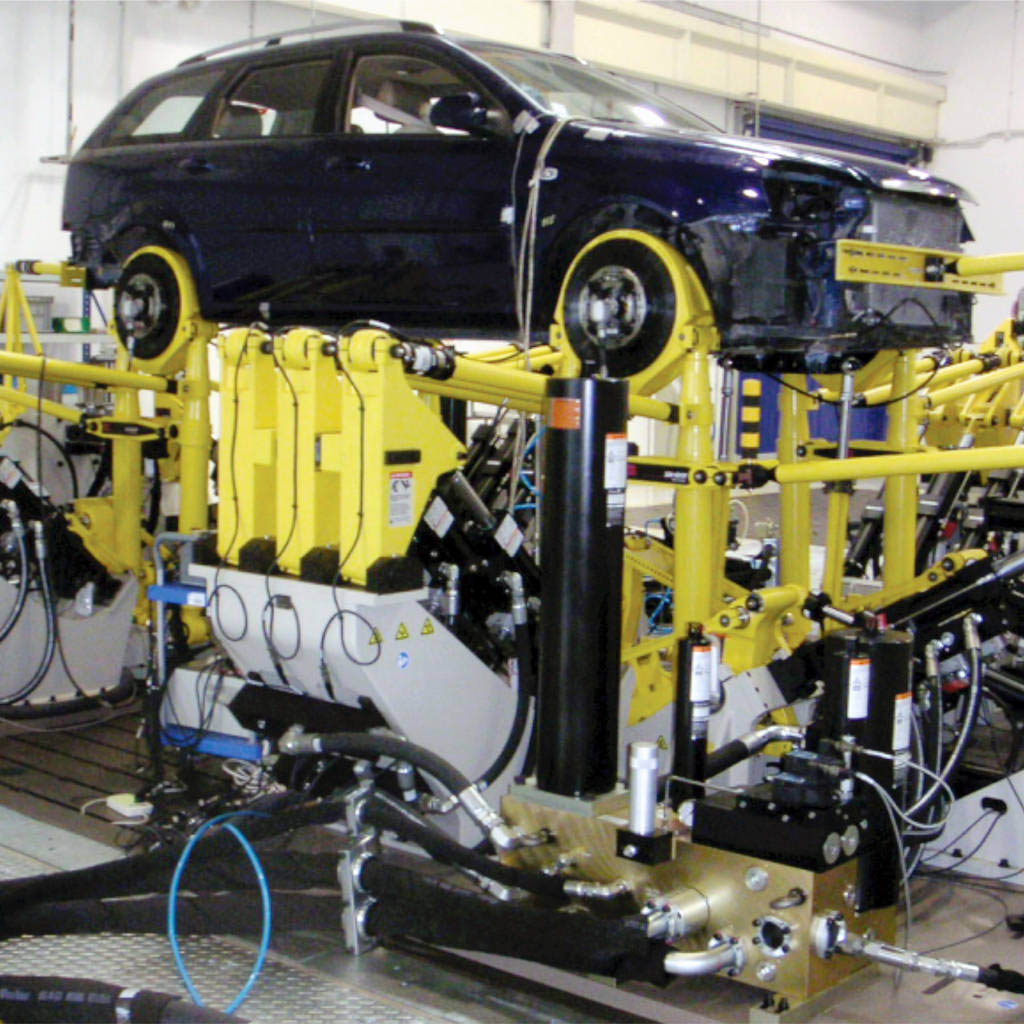
CUSTOMER CHALLENGE
The Pan Asia Automobile Technology Center (PAATC) is a dedicated automotive test lab for the SAIC Group, a leading Chinese automaker and a member of the Global 500. Before 1997, the PAATC performed mechanical testing for a relatively small line of products. However, with the establishment of Shanghai GM — a joint venture that combined the strengths of the SAIC Group and General Motors — the PAATC needed to perform tests related to the entire product range of Shanghai GM.
The Shanghai GM product line has expanded dramatically in recent years. Due to the rapid development of the domestic automobile industry in China in the late 1990s, Shanghai GM needed to make a huge change in its product development strategy. Instead of relying on a single vehicle platform, the company needed to develop multiple vehicle platforms simultaneously at three locations.
As a result, the PAATC became responsible for supporting the development of both global and local vehicle lines. This change brought PAATC a considerable amount of new testing work. Time-consuming, labor-intensive road durability testing could no longer satisfy Shanghai GM’s product development requirements. So, it was replaced by fast, effective and economical indoor development and verification testing. In the months that followed, indoor real-time simulation of road durability testing was gradually and widely applied in the PAATC as a proven and reliable testing alternative.
As the technical center of a large-scale automobile manufacturer, the PAATC faced unique challenges as it made this transition. To thoroughly verify new products, it was necessary to verify the same components in multiple cycles under different testing conditions — as well as perform related tests at the component level, system level and vehicle level. This required the addition of many new types of test systems in the PAATC’s labs. Essentially, the PAATC needed as many types of testing equipment as possible, with multiple setups for each type to enable simultaneous operation.
MTS SOLUTION
To meet new requirements for full-vehicle testing, PAATC added three sets of vehicle road stimulation test beds from MTS, including a 4-poster tire-coupled road simulator, a 16-poster spindle-coupled road simulator, and a 24-poster spindle-coupled road simulator. To verify power trains and engine mounts it added a multiaxial simulation table (MAST) system from MTS. To help reproduce a larger volume of tests indoors, as well as verify improvement schemes after road testing on the proving ground, the PAATC also acquired up to 40 linear and rotary actuators for individual component and subsystem testing.
Supporting all of this equipment are four complete setups of RPC® Pro software and four setups of Component RPC Pro (cRPC Pro) software from MTS. Together, these applications allow test engineers to control five FlexTest® digital controllers.
In the R&D center, which focuses exclusively on chassis development, suspension assembly testing comprises more than one third of the total testing volume. Here, the flexibility of the MTS systems comes into play. For example, it is common for test teams to separate the vehicle-level spindle-coupled 4DOF and 6DOF test beds into front and rear suspension test beds for real-time, multiaxial durability tests.
CUSTOMER BENEFITS
Both the data collection lab and the structure lab in the PAATC have adopted test solutions from MTS, including the integrated six-component wheel force transducer with fully integrated RPC Pro and cRPC Pro software for data processing and management. These solutions are also supported by FlexTest digital controls. According to engineers at the PAATC, the solutions deliver great convenience for testing at the vehicle, system and component level, effectively improving both operating efficiency and testing quality.
With the completion of its new large structure lab four years ago, the PAATC added many testing functions to its list of capabilities. It installed several sets of vehicle road simulation test beds, a simulation test platform (MAST), a small 3DOF vibration table composed of various actuator cylinders, a suspension test bed, a steering gear test bed and more. This wide array of equipment has also enabled the PAATC to develop a very well-trained staff of testing technicians.
With the combination of all these MTS test solutions and well-trained test professionals, the PAATC can easily satisfy the testing and verification needs for developing new vehicle models, making major modifications to several models, and making minor modifications of other models for Shanghai GM. Because the workload is so great, the improvement in testing efficiency brought by MTS solutions is very significant, reducing testing costs and improving the quality of the final products.
“In the increasingly competitive automobile market, the development of high-quality products requires fast and effective testing,” said Zhang Guiming, former manager of the PAATC structure lab. “Testing technology from MTS provides us with a guarantee for quality, time and cost with respect to the continuous development of new products.”