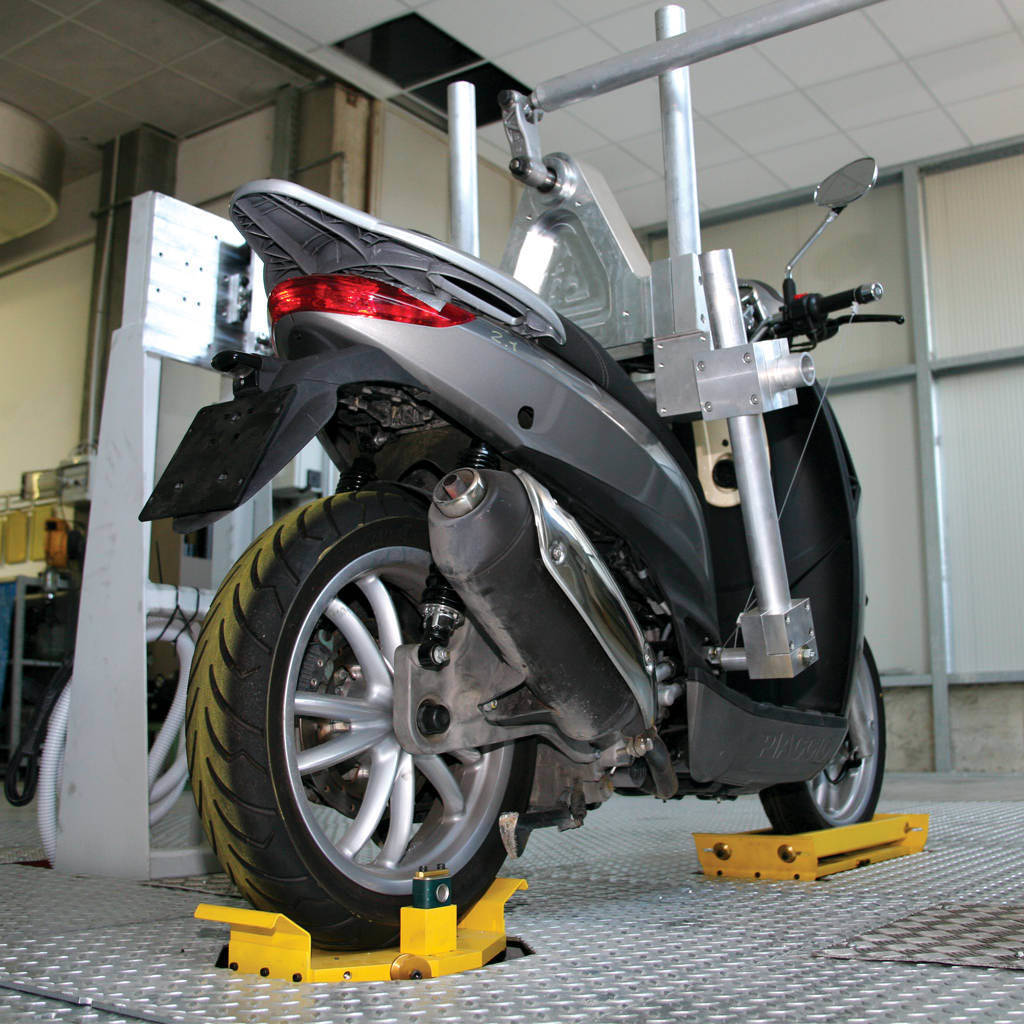
CUSTOMER CHALLENGE
Two-wheeled vehicles have become the preferred mode of transportation in many parts of the world. This is especially true in the crowded cities of Europe, Asia and Latin America that were not designed for automobiles and have serious traffic problems.
As one of the world’s leading manufacturers of scooters, mopeds and motorcycles – including the popular Vespa® brand – Pontedera, Italy-based Piaggio Group produces more than 600,000 vehicles annually. Seven brands are supported by five research and development centers and 6,700 employees in 50 countries.
Despite its strong brand equity and product leadership in the markets it serves, Piaggio faces intense competition from other manufacturers seeking to meet the rising demand for these nimble, fuel-efficient vehicles. Consequently, the company must find new ways to increase innovation while reducing development costs, in order to get feature-rich new products to market with greater frequency and at attractive price points.
“The first and most obvious place we looked to improve efficiency was the proving ground,” said Stefano Borghesi, who heads the Mechanical Laboratory in Pontedera for Piaggio. “Track testing is expensive and essentially non-repeatable, and you end up with limited amounts of information that you can actually apply toward your prototype designs.
“However, the biggest disadvantage of track testing is how long it takes from start to finish,” Borghesi added. “The typical track test requires drivers to log thousands of miles in a variety of operating conditions, which takes months to complete. In today’s competitive landscape, we no longer have the luxury to spend that much time validating a design.”
MTS SOLUTION
In November 2008, Piaggio worked closely with MTS to integrate the MTS Model 320 2-Post Test System into its Mechanical Laboratory facility in Pontedera. The system is affixed to a proprietary “seismic mass” insulating device installed below floor level, designed to prevent hydraulic actuation forces from dissipating outward across the lab and away from the test specimen.
The system ran its first official test in April 2009. Piaggio was one of the world’s first scooter manufacturers to make such advanced simulation technology part of its product development process.
This two-axis, tire-coupled simulator leverages MTS RPC® Software to precisely and repeatably replicate road-induced forces across the entire vehicle prototype, producing loads and moments that closely resemble those on the proving ground, including tests on uneven road surfaces. Since these are also the conditions that the typical rider will encounter during everyday use, test professionals have a clearer idea as to how vehicles will ultimately perform after years of real-world use.
Previously, Piaggio used simulation systems for component testing only, requiring the company to rely heavily on track testing for evaluating full-vehicle durability and performance.
“We are now evaluating the full range of vehicle types and sizes both in the test laboratory and on the test track, which is providing us with new levels of insight at earlier stages of development,” Borghesi said. “Equally important, this testing can be completed in a fraction of the time that would be required on a test track, resulting in new development cost savings for Piaggio.”
CUSTOMER BENEFITS
According to Borghesi, the MTS Model 320 2-Post Test System has helped Piaggio achieve new competitive advantage, by allowing his company to bring better product designs to market in less time and at a lower cost.
“With our new laboratory simulation capability, we have improved the performance of our vehicles while meeting customer demand for lower emissions and higher fuel-efficiency,” Borghesi said. “We have also improved vehicle fatigue life by subjecting our prototypes to the most demanding operating conditions in this controlled laboratory environment, and have made significant advances in terms of ride and comfort.”
In addition, Piaggio test engineers routinely use the test system to verify model results, providing the team with greater confidence in the validity of its calculations and the integrity of its test data.
“MTS has proven to us that it offers the best total value of any test solutions provider,” Borghesi said. “From high-quality products to an expert team of field service engineers, MTS was instrumental in helping us successfully simulate the most critical and revealing road events in our laboratory. We look forward to continuing to work with MTS well into the future.”