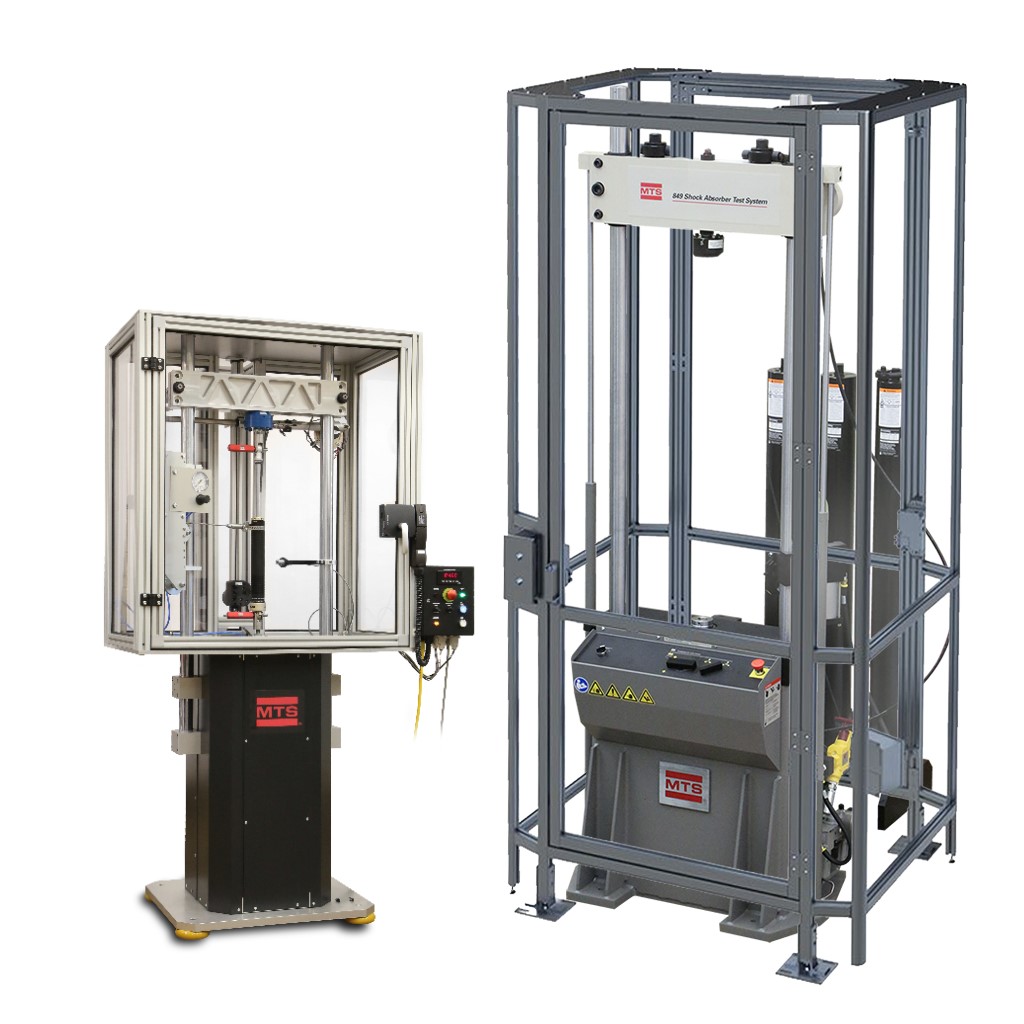
Q: What are the high-level guiding principles when selecting between electric and hydraulic test systems?
Bieganek: The choice of which technology to deploy is very situational and depends on numerous factors, such as system functional and performance requirements, available budget, existing infrastructure, etc. It’s complex. The best approach is to start by considering the type of testing environment (production facility/factory; R&D laboratory; proving ground/race track) and go from there. MTS’ portfolios of damper test and tire-coupled road simulation solutions feature a complementary mix of electric and hydraulic systems. It’s our job to apply our experience and expertise to help customers find a system that meets both their current and anticipated future needs.
Q: Let’s start with damper testing in a production environment. What are the primary applications?
Bieganek: Typically, customers need to perform in-line characterization tests to make sure the damper has been assembled properly and is performing as expected. In other words, it’s quality control. They are typically checking the damping force, gas pressure and oil levels. The test may be fully integrated with the production line to test every damper. Or it may be a quality audit, where the customer pulls a few samples every hour and tests them off the line.
Q: What performance attributes are needed from a damper test system in a production environment?
Simpson: Speed is critical. The test system can’t hold up the production line or cause bottlenecks. It may need to be integrated with the line to improve productivity or enabled for automation through the facility’s existing robotics. In any case, the system has to be easy to use so operators can run the test efficiently and quickly determine whether a damper sample has passed. The system typically needs to offer a force capacity between 2,000 and 6,000 pounds.
Q: What test solutions does MTS offer for a damper production line?
Simpson: Line Electromagnetic Actuator, or LEMA, Production Line Damper Testers are ideal for production environments. They are right-sized in terms of force capacity, and their easy-to-use and responsiveness are ideal for maintaining high rates of throughput. Additionally, they feature an open architecture for full or partial integration with the line.
Q: What factors do customers need to consider for damper production testing?
Bieganek: Facility impact is a key consideration when purchasing test systems. All manufacturing plants have electrical infrastructure in place making a LEMA test system ideal for production quality testing. Versatility comes into play too. The LEMA systems are fully programmable, making production line change-over quick and easy. Then there are practical factors, such as ease of use. With these systems, an indicator light shows pass/fail status and the digital interface enables either robotic or human specimen disposition on test completion. Operating efficiency is another important factor. With electric actuation power is consumed on-demand, so it’s more efficient and less expensive than hydraulic actuation in this case. Finally, LEMA systems have low maintenance needs, resulting in high up-time and efficient operation.
Q: How do the applications change for damper testing in the laboratory environment?
Bieganek: There are two primary applications: single-specimen characterization and multi-specimen durability testing. Characterization applies a displacement or velocity into the damper and measures the force response out. Engineers run gas tests to remove gas from the analysis portion of the force-velocity curve. Seal tests help them understand stick/slip characteristics. Noise, vibration and harshness tests characterize swish and chuckle noise attributes. There are also environmental tests to see how dampers respond to changes in temperature or humidity. All of this is intended to improve product design. Durability testing is necessary to determine expected product life under real-world conditions and involves the application of sinusoidal, block, cyclic, random or road profile inputs. To optimize test productivity, durability tests are run typically with multiple specimens, requiring a test system with higher force capacity than a characterization system.
Q: What solutions does MTS offer for damper testing in a laboratory environment?
Simpson: MTS has a broad range of options for lab-based damper testing. Electric Scotch Yoke Dyno, or SYD series systems (often referred to as Crank Dynos), are a good choice for budget-sensitive labs that require only sinusoidal inputs. Electromagnetic Actuator, or EMA series 2K, 4K and 6K systems provide force capacities from 9 to 53 kN, and more complex, programmable inputs. Both of these electric systems feature quiet operation, easy maintenance and cost-efficient operation. Then there is a full complement of hydraulic systems, including the MTS 849, 850 and 852 Damper Test Systems, which are versatile enough to handle road load data. They come with higher force capacities, from 15 to 150 kN, and are easily expandable to deliver higher forces if the lab’s needs change.
Q: How can labs make the right choice for their specific damper test situation?
Bieganek: There are several factors to think about, and it’s not always clear cut. Whether or not the lab already has hydraulic infrastructure in place is very important. If it is already present, a hydraulic system will be more affordable than if the lab has to add that infrastructure. If the lab is dedicated to single-specimen characterization, EMA systems present an appropriate solution. However, if the intent is to perform characterization and durability testing with the same system — or retain the option for durability testing in the future — a hydraulic system is more appropriate. The same thought applies to force capacity: will requirements stay the same or increase over time? The lab may also have larger priorities that affect the decision, such as the total capital investment, a benchmark for energy efficiency, a commitment to environmental friendliness, or a high emphasis on ease of use. MTS has worked with hundreds of labs and we can help find a test system that aligns with all of the lab’s needs.
Q: What about the proving ground or race track? What damper testing applications are important here?
Simpson: Whether it is an OEM at the proving ground or a race team at the track, the application is virtually always single-specimen characterization. Occasionally there is a need to do a seal or gas test, but for the most part, our customers want to look at a damper’s force-velocity curve, tune it accordingly, and then test it in a vehicle. Specifically, test engineers are looking to identify speeds of interest and the track impacts, run a sinusoidal test based on road input data and analyze the damper curve at a specific velocity. OEMs are measuring vehicle dynamic attributes, while race teams are getting feedback from the driver. Either way, time pressure can be intense, so test speed and efficiency are very important. So is test consistency, from the practice laps to qualifying to race day.
Q: What do damper test systems need to deliver in a track environment?
Bieganek: Test system portability and size are critical in a track environment. These tests are typically run in vans or semi-trailers where space is at a premium. The test systems have to offer the right level of programmability and performance; and they need to be affordable, given the diverse range of customers and levels of investment in the racing community. For the garage racer or hobbyist, an SYD series (Crank Dyno) system is perfect. The EMA systems are small, portable and lightweight, yet they have the advanced capabilities professional racing teams require. They do not require hydraulic infrastructure and they are easy to maintain.
Q: Let’s talk about tire-coupled road simulation. What applications are performed in production environments?
Bieganek: Buzz, squeak and rattle, or BSR, testing is the primary road simulation application for a production environment. As with damper testing, it can be fully integrated into the production line to test every vehicle. Or it can be done offline as a quality audit with a few sample vehicles per hour. Test systems for BSR need to provide adequate force capacity per vehicle size, as well as low noise (60dB or less) so as not to interfere with the test.
Q: What solutions does MTS offer for BSR testing in a production environment?
Bieganek: There are a range of test systems available, including the Model 320 ePost Tire-Coupled Road Simulators, which feature electric actuation. The 4K configuration can handle small to large cars and the 6K configuration is appropriate for large cars up to light trucks and SUVs. These systems provide quieter operation. Like the LEMA systems, they are electric and so are more amenable to existing production environment infrastructure. They deliver highly efficient performance with unique environmental advantages. In addition, they have a design-optimized user interface for thorough, efficient BSR investigations such that a test operator can run the test from within the vehicle. For production environments with existing hydraulic power and distribution infrastructure, the hydraulic Model 320 First Road System is also an option.
Q: Are road simulation applications different in a test laboratory environment?
Simpson: Yes, the test lab is interested in BSR investigations, as well as more detailed noise, vibration and harshness, or NVH. These are essentially BSR tests done in an environmental chamber while simulating rain/humidity, temperature or solar exposure to account for specimen aging. Some labs have anechoic chambers to create an even quieter test environment. In addition, labs are also commonly tasked with performing durability testing to determine life attributes for both subsystems and full vehicles.
Q: What requirements do road simulators need to meet in laboratory environment?
Bieganek: Much of it has to do with the size of the vehicle being tested, whether it’s a small car or a piece of farm equipment. The force capacity, velocity and acceleration all need to be aligned with the vehicle. For BSR, low noise is very important. Simulator flexibility is also important to accommodate multiple types of vehicles and integrate seamlessly with various environmental chambers.
Q: What electric solutions does MTS offer for tire-coupled road simulation in a lab setting?
Simpson: The Model 320 ePost systems feature electric actuation and can accommodate vehicles from motorcycles and ATVs up to large cars and light trucks. Specifically designed for BSR testing, they offer low facility impact and a low capital investment. Like other electric systems, they make operation, maintenance and training very easy. And they can accommodate environmental testing.
Q: What hydraulic solutions does MTS offer for tire-coupled road simulation in a lab setting?
Bieganek: Multipurpose hydraulic Model 320 simulators are designed for durability testing but they can be tuned for BSR testing. These systems offer proven performance for higher force applications as well as higher velocity and acceleration. They can accommodate large vehicles, including heavy trucks and construction and agricultural equipment. Again, it depends on what infrastructure the lab has in place and whether they want the option to add durability testing in the future.
Contact MTS today and explore how our diverse offering of electric and hydraulic damper test and road simulation solutions can meet your specific production, laboratory or proving ground/track requirements.
Bieganek: The choice of which technology to deploy is very situational and depends on numerous factors, such as system functional and performance requirements, available budget, existing infrastructure, etc. It’s complex. The best approach is to start by considering the type of testing environment (production facility/factory; R&D laboratory; proving ground/race track) and go from there. MTS’ portfolios of damper test and tire-coupled road simulation solutions feature a complementary mix of electric and hydraulic systems. It’s our job to apply our experience and expertise to help customers find a system that meets both their current and anticipated future needs.
Q: Let’s start with damper testing in a production environment. What are the primary applications?
Bieganek: Typically, customers need to perform in-line characterization tests to make sure the damper has been assembled properly and is performing as expected. In other words, it’s quality control. They are typically checking the damping force, gas pressure and oil levels. The test may be fully integrated with the production line to test every damper. Or it may be a quality audit, where the customer pulls a few samples every hour and tests them off the line.
Q: What performance attributes are needed from a damper test system in a production environment?
Simpson: Speed is critical. The test system can’t hold up the production line or cause bottlenecks. It may need to be integrated with the line to improve productivity or enabled for automation through the facility’s existing robotics. In any case, the system has to be easy to use so operators can run the test efficiently and quickly determine whether a damper sample has passed. The system typically needs to offer a force capacity between 2,000 and 6,000 pounds.
Q: What test solutions does MTS offer for a damper production line?
Simpson: Line Electromagnetic Actuator, or LEMA, Production Line Damper Testers are ideal for production environments. They are right-sized in terms of force capacity, and their easy-to-use and responsiveness are ideal for maintaining high rates of throughput. Additionally, they feature an open architecture for full or partial integration with the line.
Q: What factors do customers need to consider for damper production testing?
Bieganek: Facility impact is a key consideration when purchasing test systems. All manufacturing plants have electrical infrastructure in place making a LEMA test system ideal for production quality testing. Versatility comes into play too. The LEMA systems are fully programmable, making production line change-over quick and easy. Then there are practical factors, such as ease of use. With these systems, an indicator light shows pass/fail status and the digital interface enables either robotic or human specimen disposition on test completion. Operating efficiency is another important factor. With electric actuation power is consumed on-demand, so it’s more efficient and less expensive than hydraulic actuation in this case. Finally, LEMA systems have low maintenance needs, resulting in high up-time and efficient operation.
Q: How do the applications change for damper testing in the laboratory environment?
Bieganek: There are two primary applications: single-specimen characterization and multi-specimen durability testing. Characterization applies a displacement or velocity into the damper and measures the force response out. Engineers run gas tests to remove gas from the analysis portion of the force-velocity curve. Seal tests help them understand stick/slip characteristics. Noise, vibration and harshness tests characterize swish and chuckle noise attributes. There are also environmental tests to see how dampers respond to changes in temperature or humidity. All of this is intended to improve product design. Durability testing is necessary to determine expected product life under real-world conditions and involves the application of sinusoidal, block, cyclic, random or road profile inputs. To optimize test productivity, durability tests are run typically with multiple specimens, requiring a test system with higher force capacity than a characterization system.
Q: What solutions does MTS offer for damper testing in a laboratory environment?
Simpson: MTS has a broad range of options for lab-based damper testing. Electric Scotch Yoke Dyno, or SYD series systems (often referred to as Crank Dynos), are a good choice for budget-sensitive labs that require only sinusoidal inputs. Electromagnetic Actuator, or EMA series 2K, 4K and 6K systems provide force capacities from 9 to 53 kN, and more complex, programmable inputs. Both of these electric systems feature quiet operation, easy maintenance and cost-efficient operation. Then there is a full complement of hydraulic systems, including the MTS 849, 850 and 852 Damper Test Systems, which are versatile enough to handle road load data. They come with higher force capacities, from 15 to 150 kN, and are easily expandable to deliver higher forces if the lab’s needs change.
Q: How can labs make the right choice for their specific damper test situation?
Bieganek: There are several factors to think about, and it’s not always clear cut. Whether or not the lab already has hydraulic infrastructure in place is very important. If it is already present, a hydraulic system will be more affordable than if the lab has to add that infrastructure. If the lab is dedicated to single-specimen characterization, EMA systems present an appropriate solution. However, if the intent is to perform characterization and durability testing with the same system — or retain the option for durability testing in the future — a hydraulic system is more appropriate. The same thought applies to force capacity: will requirements stay the same or increase over time? The lab may also have larger priorities that affect the decision, such as the total capital investment, a benchmark for energy efficiency, a commitment to environmental friendliness, or a high emphasis on ease of use. MTS has worked with hundreds of labs and we can help find a test system that aligns with all of the lab’s needs.
Q: What about the proving ground or race track? What damper testing applications are important here?
Simpson: Whether it is an OEM at the proving ground or a race team at the track, the application is virtually always single-specimen characterization. Occasionally there is a need to do a seal or gas test, but for the most part, our customers want to look at a damper’s force-velocity curve, tune it accordingly, and then test it in a vehicle. Specifically, test engineers are looking to identify speeds of interest and the track impacts, run a sinusoidal test based on road input data and analyze the damper curve at a specific velocity. OEMs are measuring vehicle dynamic attributes, while race teams are getting feedback from the driver. Either way, time pressure can be intense, so test speed and efficiency are very important. So is test consistency, from the practice laps to qualifying to race day.
Q: What do damper test systems need to deliver in a track environment?
Bieganek: Test system portability and size are critical in a track environment. These tests are typically run in vans or semi-trailers where space is at a premium. The test systems have to offer the right level of programmability and performance; and they need to be affordable, given the diverse range of customers and levels of investment in the racing community. For the garage racer or hobbyist, an SYD series (Crank Dyno) system is perfect. The EMA systems are small, portable and lightweight, yet they have the advanced capabilities professional racing teams require. They do not require hydraulic infrastructure and they are easy to maintain.
Q: Let’s talk about tire-coupled road simulation. What applications are performed in production environments?
Bieganek: Buzz, squeak and rattle, or BSR, testing is the primary road simulation application for a production environment. As with damper testing, it can be fully integrated into the production line to test every vehicle. Or it can be done offline as a quality audit with a few sample vehicles per hour. Test systems for BSR need to provide adequate force capacity per vehicle size, as well as low noise (60dB or less) so as not to interfere with the test.
Q: What solutions does MTS offer for BSR testing in a production environment?
Bieganek: There are a range of test systems available, including the Model 320 ePost Tire-Coupled Road Simulators, which feature electric actuation. The 4K configuration can handle small to large cars and the 6K configuration is appropriate for large cars up to light trucks and SUVs. These systems provide quieter operation. Like the LEMA systems, they are electric and so are more amenable to existing production environment infrastructure. They deliver highly efficient performance with unique environmental advantages. In addition, they have a design-optimized user interface for thorough, efficient BSR investigations such that a test operator can run the test from within the vehicle. For production environments with existing hydraulic power and distribution infrastructure, the hydraulic Model 320 First Road System is also an option.
Q: Are road simulation applications different in a test laboratory environment?
Simpson: Yes, the test lab is interested in BSR investigations, as well as more detailed noise, vibration and harshness, or NVH. These are essentially BSR tests done in an environmental chamber while simulating rain/humidity, temperature or solar exposure to account for specimen aging. Some labs have anechoic chambers to create an even quieter test environment. In addition, labs are also commonly tasked with performing durability testing to determine life attributes for both subsystems and full vehicles.
Q: What requirements do road simulators need to meet in laboratory environment?
Bieganek: Much of it has to do with the size of the vehicle being tested, whether it’s a small car or a piece of farm equipment. The force capacity, velocity and acceleration all need to be aligned with the vehicle. For BSR, low noise is very important. Simulator flexibility is also important to accommodate multiple types of vehicles and integrate seamlessly with various environmental chambers.
Q: What electric solutions does MTS offer for tire-coupled road simulation in a lab setting?
Simpson: The Model 320 ePost systems feature electric actuation and can accommodate vehicles from motorcycles and ATVs up to large cars and light trucks. Specifically designed for BSR testing, they offer low facility impact and a low capital investment. Like other electric systems, they make operation, maintenance and training very easy. And they can accommodate environmental testing.
Q: What hydraulic solutions does MTS offer for tire-coupled road simulation in a lab setting?
Bieganek: Multipurpose hydraulic Model 320 simulators are designed for durability testing but they can be tuned for BSR testing. These systems offer proven performance for higher force applications as well as higher velocity and acceleration. They can accommodate large vehicles, including heavy trucks and construction and agricultural equipment. Again, it depends on what infrastructure the lab has in place and whether they want the option to add durability testing in the future.
Contact MTS today and explore how our diverse offering of electric and hydraulic damper test and road simulation solutions can meet your specific production, laboratory or proving ground/track requirements.