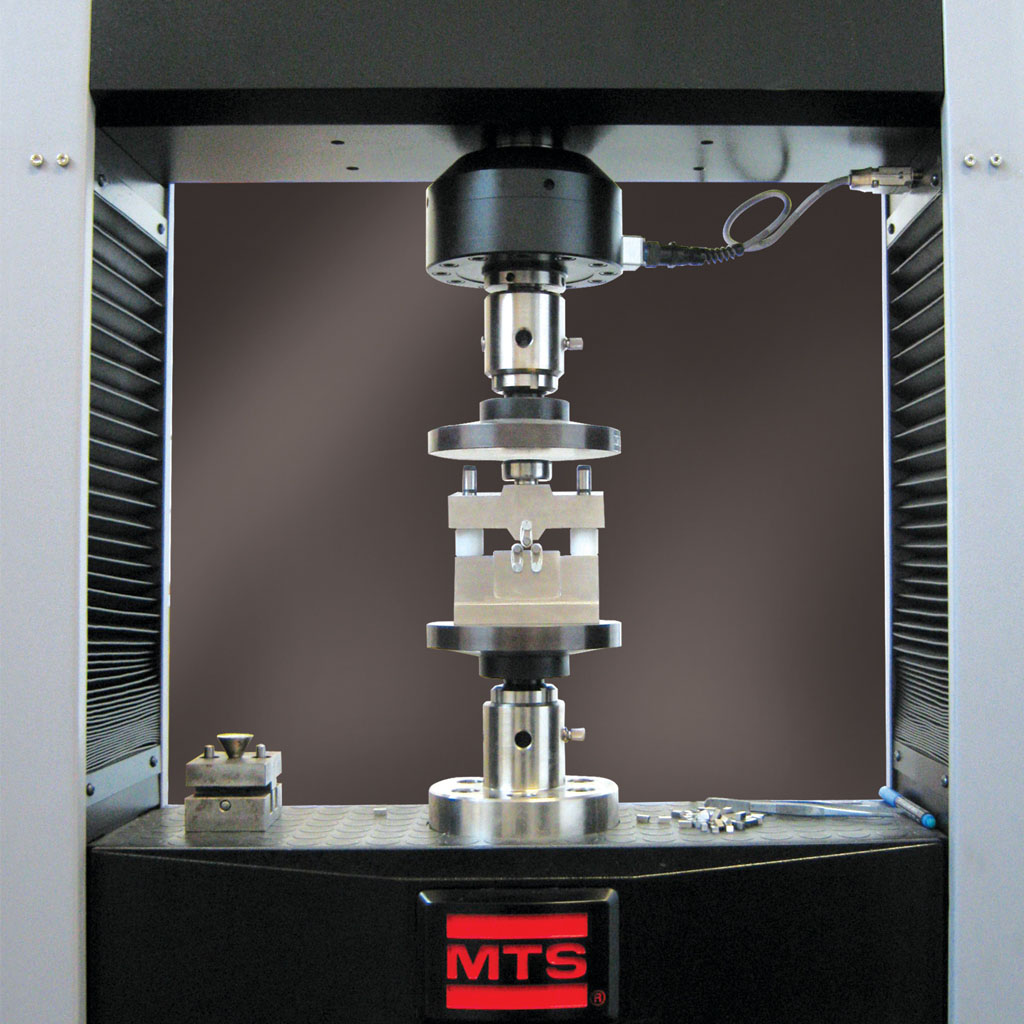
CUSTOMER CHALLENGE
Orthopaedic device developers face intense competition, which means speed to market is critical. Developers are constantly searching for new ways to accelerate the product development process and gain insight into new materials and designs sooner, with greater confidence.
K4Sint is a small company making a big impact in this field of study. The private research and development company, which is located just outside Trento, Italy, specializes in applying powder metallurgy techniques to produce new materials for implantable orthopaedic devices that would otherwise be impossible to obtain.
“Our clients are manufacturers of high-performance orthopaedic devices,” said Dr. Mario Zadra, one of the founders of K4Sint and an expert in both material science and powder metallurgy. “They typically need to improve device performance but also want to keep costs as low as possible. We produce new parts using different combinations of materials to find the best solution.”
Just like the developers that K4Sint serves, Dr. Zadra’s team is under constant pressure to create new parts very quickly. To do this, K4Sint uses a patented sequence of mechanical alloying and spark plasma sintering. Sintering, a method of creating objects from powdered materials, helps K4Sint researchers form new compositions much faster than with direct alloying. When each new alloy is ready, the next step is performing mechanical tests with equal efficiency.
MTS SOLUTION
From femoral heads and acetabular cups to condyles and metallic sponges, all of the parts in implantable orthopaedic devices must deliver the performance developers expect. Manufacturers of high-end devices are particularly interested in new alloys that may provide ideal strength and reliability yet offer new ways to reduce material and production costs.
“In terms of alloys, there are only a few elements that can be used, including titanium and zirconium,” Dr. Zadra said. “We mix them to obtain a composition that exhibits the right mechanical properties, the most important of which is hardness. We produce 20-millimeter discs, which we cut to obtain smaller samples that we test with a three-point bend fixture in our MTS test system. We can quickly obtain test data, fine-tune the material, redo the three-point bend test and know when the composition is right.”
In the K4Sint lab, Dr. Zadra’s team relies on an MTS Criterion® Series 40 Electromechanical Universal Test System along with MTS TestSuite™ TW software, MTS wedge grips and compression plates, and a unique three-point bending tool that was custom-designed by the K4Sint team. The MTS Criterion system gives the lab the ability to characterize the hardness of new alloys as well as evaluate their yield strength, ultimate tensile strength and ductility.
CUSTOMER BENEFITS
With the MTS Criterion system in its lab, K4Sint can maintain a rigorously efficient test program, performing 10 to 15 three-point bend tests every week in addition to weekly tensile testing of materials that have proven they merit further evaluation.
“Before we acquired the MTS test system, we had to do all of our testing at the University of Trento,” said Dr. Zadra. “Now our testing is much faster and more convenient. And speed of test is directly related to the success of our business.”
Dr. Zadra also appreciates the performance of the MTS Criterion system, which has been running in the K4Sint lab for a little more than a year. The system is built to operate reliably and is specifically designed for easy maintenance.
“The reason why we chose MTS initially is that we required a system that could keep pace with our testing objectives by leveraging test versatility and maximizing uptime,” Dr. Zadra said. “With the MTS brand, we obtained both. We have a very good relationship with MTS.”