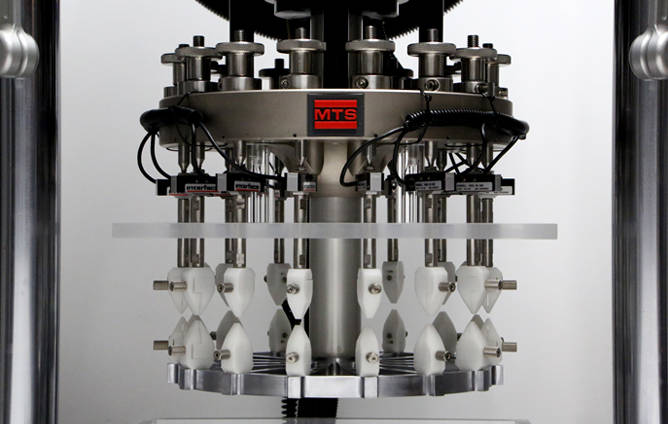
INTRODUCTION
A multi-sample test system has been created with advanced control techniques, which allow the user to individually monitor the fracture of nitinol single apex samples cut from an endovascular device. The system can reliably detect a reduction in load of less than one gram at test frequency indicating impending failure on each station and increases the rate of data acquisition on the specified station where the load falloff precursors are detected. The software used allows the operator to record peak-valley load data as needed for long term fatigue but also has the ability to capture a user defined number of cycles of that load cell only when a load drop-off occurs without the burden of recording the data from all of the load cells in the test. Only the test site of interest is magnified and detailed. Following a fracture, the system allows the user to decide if the test should continue, pause in order to remove the damaged specimen, or terminate, without damaging any of the other samples.
EXPERIMENTAL RESULTS
The advanced control techniques used for the multi-sample test system were verified by cycling nitinol single apex samples cut from an endovascular device until failure. The load measurement system is compensated and sufficiently sensitive to detect the load fall off on a single sample prior to fracture. Eight specimens were installed in the system and were individually adjusted to have zero preload applied. The system cycled the specimens at 3 mm displacement for 40 Hz until a specimen fracture was detected. The software procedure initiated data acquisition upon detecting that the peak and valley load readings had fallen into the predetermined region, as shown by the red dashed line in Fig 1 below. The fracture detection program began with a higher data acquisition rate once the load readings decreased by 90%, as shown by the blue dashed line in Fig.1.
Figure 1: Break Detection of NiTi Specimen
After the fracture was detected, the program controlled the system to stop within 0.1 s without causing further damage to any of the remaining specimens, as shown in Fig. 2 below. This procedure can be modified to pause the test for specimen inspection or removal instead of ending the test for all specimens. When a pause function is used, the lifecycle testing can continue for the remaining, non-damaged specimens without losing cycle count or data.
Figure 2: System Controlled Stop after Fracture Detection
DISCUSSION
The multi-sample test system detects and monitors individual nitinol specimen damage during lifecycle testing using the procedure described in the figure below. Peak or valley load reductions of less than 1 gram can be reliably measured at frequency. The software may then stop the system for examination, or continue and remove the failed loading site from the data stream. It is our observation that this capability is unique.
Figure 3: System Response Discussion
CONCLUSIONS
The advanced control techniques used on the multi-sample test system provide the ability to individually monitor and record fractures of nitinol apices. The pause and stop test functions are controlled with advanced techniques which ensure no further damage will be done to any of the installed samples. These software capabilities also allow for high reliability in the event of power loss or unforeseen interference. Additional operator specified data acquisition methods and analysis are available within the control system to meet specific test needs. The ability to individually detect the load falloff of nitinol apices allows for advanced insight in device fractures during testing.