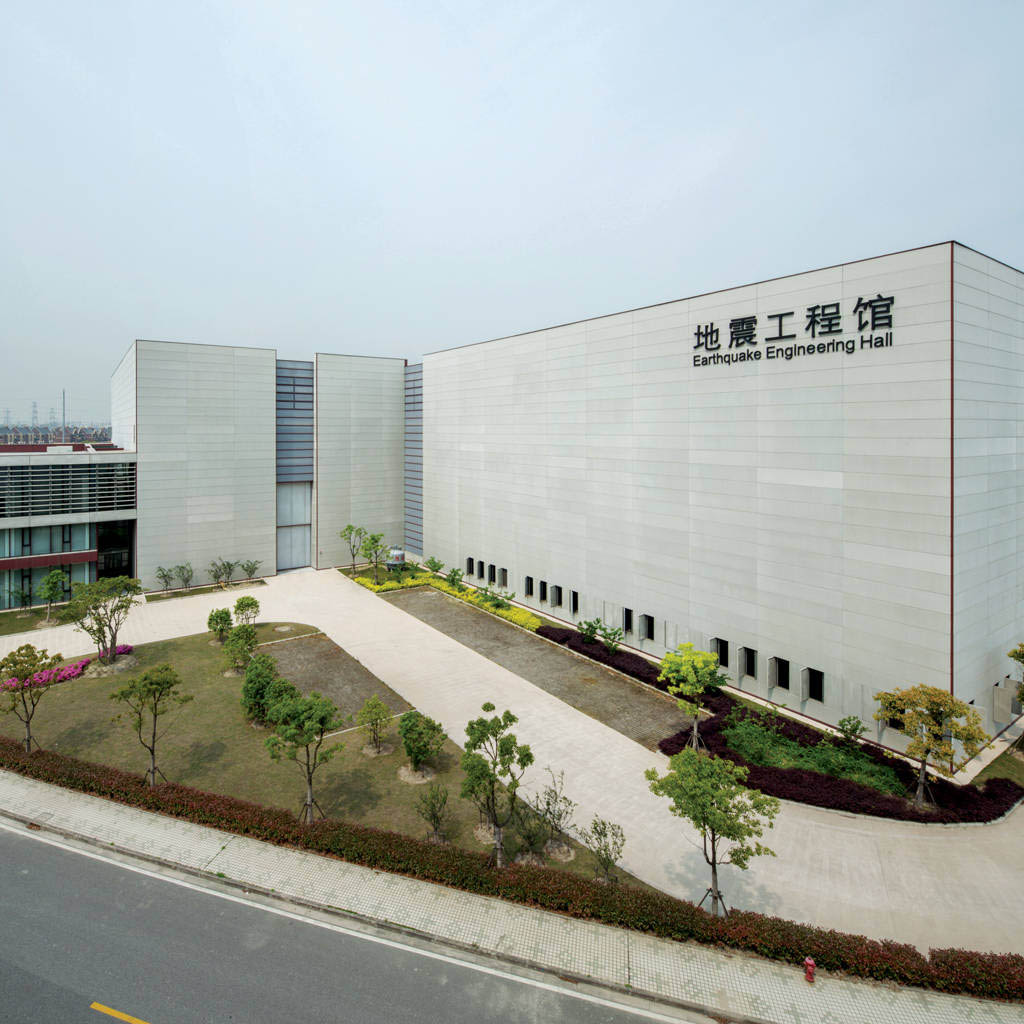
CUSTOMER CHALLENGE
Global population growth poses special challenges for civil engineers. Bigger cities require taller buildings, larger mass transit systems and longer bridges, all of which must be designed to withstand earthquakes and other disasters. Tongji, one of the oldest and most prestigious universities in China, is leading the way in this field, using new testing methods to help engineers improve their designs.
The College of Civil Engineering at Tongji University is home to both the Department of Bridge Engineering and the State Key Laboratory of Disaster Reduction in Civil Engineering. Here, Dr. Chengyu Yang is a key professor in the research division for seismic design of bridges, conducting tests that help reduce the effects of devastating earthquakes on bridges, buildings, tunnels and many other structures.
“One of our biggest challenges is performing shaking table testing for models of long-span bridges,” Dr. Yang said. “If you only have one table, even one that is six-by-six meters, the model of the bridge must be relatively small, down to 1:100 or 1:200 scale.”
The problem is that the smaller the model, the less useful the results. Smaller models simply do not react in the same manner as real bridge structures, making it more difficult to extrapolate test data to the full-scale structure. And if the structure in question is Jiangsu’s Taizhou Bridge, which spans 62 kilometers, the problem becomes especially daunting to solve.
MTS SOLUTION
To complete seismic testing for large-scale models, including a replica of the Taizhou Bridge, Dr. Yang’s team worked with MTS to commission a one-of-a-kind shaking table solution that can be arranged in multiple configurations and supports models weighing up to 200 tons. Housed in Tongji’s Multi-Functional Shaking Tables (MFST) Lab, the solution incorporates four tables within the largest multi-table seismic test facility in the world.
Shaking tables use hydraulic actuators to replicate the forces and motions experienced by structures during an earthquake or other seismic event. Tongji’s MFST Lab features two 70-ton shake tables and two 30-ton shake tables that can be arranged in multiple configurations anywhere within two adjacent trenches. A 70-meter-long trench can accommodate all four tables, and a 30-meter-long trench can hold two tables. All four tables can be positioned and anchored in two-meter increments, allowing the lab to accommodate longer and larger test specimens, including those that span both trenches
Most important, the motion of all four tables can be synchronized to replicate seismic waves as if they were one very large platform, or the tables can be operated independently. Using a high-speed, real-time, shared memory application, the solution allows all tables to “see” data from all other tables. All of the data is integrated into a master controller that interprets the commands and feedback to keep everything in synch. This gives the lab more extensive control over the entire testing environment.
“No other lab in the world has shaking table technology that can be used this way, at this scale,” Dr. Yang said. “We couldn’t have located the MFST Lab in downtown Shanghai near the rest of Tongji due to its size. We had to build it on a new campus. The lab building is 100 meters long and 88 meters wide.”
While the solution leverages the traditional shaking table technology MTS has developed over the past 30 years, it is customized to meet the specifications of Dr. Yang’s team. MTS and Tongji engineers worked together to develop a solution with an unprecedented combination of size, capacity and flexibility.
CUSTOMER BENEFITS
When the Tongji MFST Lab conducted seismic testing on the scale model of the Taizhou Bridge, the size and configurability of the shaking table solution provided distinct advantages.
“Now we can use a 1:40 scale model that is 65 meters long instead of three meters long,” Dr. Yang said. “We can design our model and configure the tables to fit the test instead of the other way around. It’s very convenient for our researchers. They can get the data they want most, instead of settling for the next best thing.”
By testing larger models, Dr. Yang’s team creates a test environment that is much closer to real-world conditions, which helps researchers better predict actual system responses. More realistic testing helps verify virtual models and make them more accurate, which improves the design of large structures. The solution from MTS also creates opportunities for the MFST Lab to pursue new kinds of testing.
“We just finished testing for a tunnel connecting Mainland China, Hong Kong and Macau,” Dr. Yang said. “Before, we would put a model of one tunnel section in a four-by-four-meter box of soil. Now we can do the same test with a 40-meter-long box. This lets us evaluate segment connections using non-uniform excitation, which is critical because seismic waves hit different parts of large structures differently. This is unique research.”
The solution is just one more example of a 30-year relationship between Tongji and MTS, one that becomes stronger with each project.
“All the people at MTS are hard-working and professional, from sales to the engineers and technicians,” Dr. Yang said. “This summer, I had a question about a test so I sent an e-mail on Sunday afternoon, which would have been the middle of the night on Saturday in the U.S. I was not expecting to hear back right away. The next morning, I had responses from several different people at MTS, both in the U.S. and in China. That’s just one example of how responsive they are to our needs.”