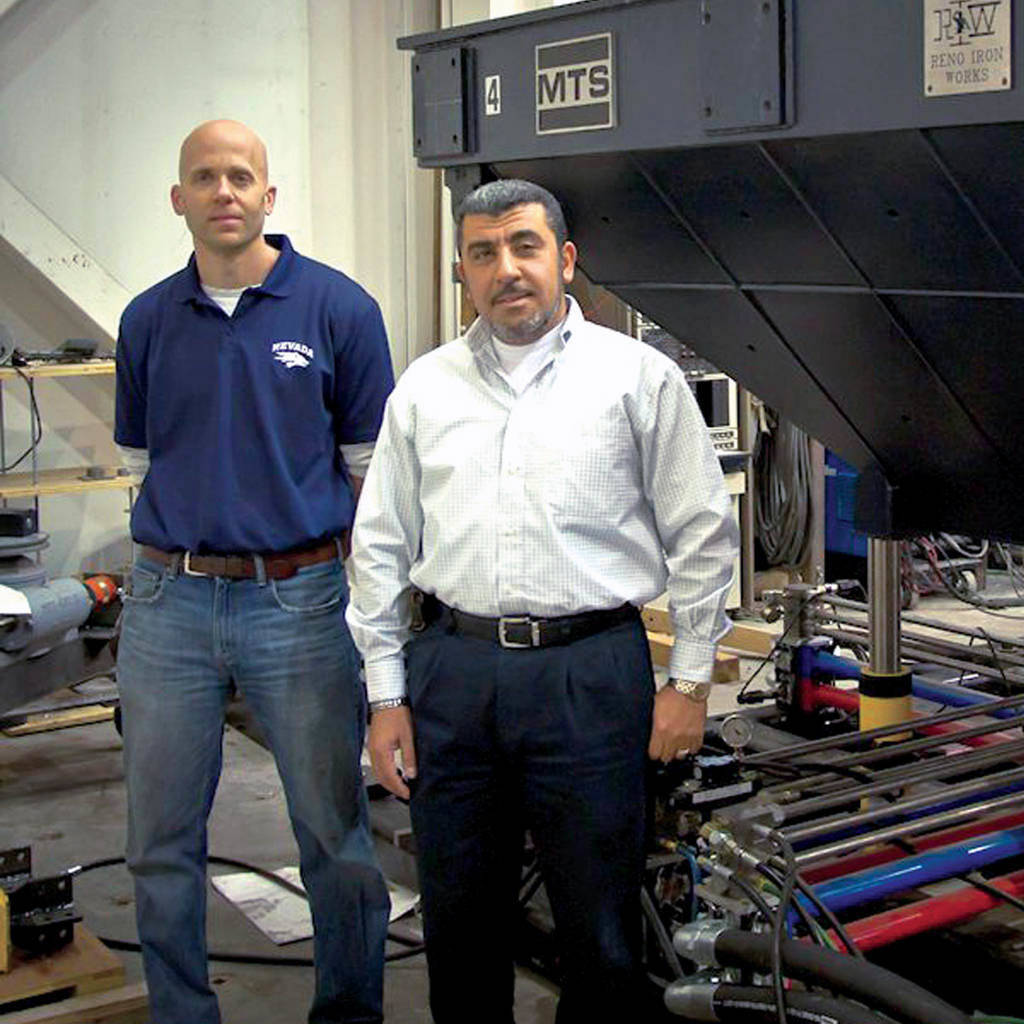
CUSTOMER CHALLENGE
Historically, civil engineers have had limited insight into how horizontally curved bridges respond to earthquakes. As part of a larger project funded by the Federal Highway Administration (FHWA) to study the seismic resilience of highway systems, the University of Nevada, Reno NEES Equipment Site (UNR-NEES) was utilized to thoroughly characterize the behavior of curved bridge segments under seismic conditions. The goal of the research was to establish guidelines for designing curved bridges that better withstand major earthquakes.
Due to their irregular shape, curved bridges have unique requirements for large-scale seismic simulations. Traditional uniaxial test systems installed in trenches below the strong floor do not offer positioning flexibility to accommodate these test specimens. At the time FHWA funded a research project at UNR-NEES, no large-scale structural seismic simulations had ever been performed on curved bridges in the test lab.
UNR-NEES set out to investigate seismic impact using a 2/5-scale model of a three-span curved bridge, measuring 44.1 meters (145 feet) long with a 24.4-meter (80-foot) radius at the model’s centerline.
“This was the biggest bridge test we had ever attempted, involving high payloads and a large and uniquely shaped specimen,” said Patrick Laplace, Ph.D., Large Scale Structures Laboratory Manager at UNR-NEES. “So for us, the major challenge was finding a way to accurately simulate a seismic event on a curved bridge at this scale and with the forces involved. We only get one of these scale models to work on, so we knew everything had to be right the first time.”
Laplace also knew why the FHWA selected UNR-NEES for the curved bridge study: because of the facility’s one-of-a-kind test setup with unprecedented flexibility to accommodate large and uniquely shaped specimens. “We got the project because we were the only test facility capable of generating the required forces and motions virtually anywhere across our lab floor,” he said.
MTS SOLUTION
Over a period of 20 years, UNR-NEES has worked closely with MTS to integrate multiple shake table systems for large-scale, high-force seismic testing, primarily on bridges and bridge components.
The facility currently includes three biaxial shake tables, along with a fourth, 6DOF shake table added in 2009. Each table measures approximately 4.25 meters (14 feet) square, has a 445 kN (50-ton) payload, and sits atop a 780-square-meter (8,400-square-foot) strong floor in a high-bay laboratory with two overhead cranes. MTS also custom-designed a hydrostatic bearing for the shake tables that prevents uplift, roll, pitch, and yaw without requiring a trench, making it possible to install these systems directly on the strong floor.
The shake tables can be operated independently, in phase or differentially with the other tables, and can be positioned to address the unique space requirements of a test specimen. All four tables were used for the curved bridge seismic simulations, including the 6DOF table set in biaxial mode.
“That is exactly what UNR wanted: multiple shake tables that can be moved across the floor and operate individually or in tandem,” Laplace said. “To my knowledge, we were the first lab to use large shake tables in an array like this.”
This arrayed, portable configuration allowed UNR-NEES to test the curved-bridge scale model in numerous unprecedented ways. Six different tests were performed to examine various components under earthquake conditions. Tests included column design with and without conventional columns; abutment design with and without backfill; seismic isolation with and without response modification; and live load, with and without trucks positioned on the superstructure surface.
“Our ability to study differential motion fills a longstanding void for curved bridge seismic testing,” Laplace said. “For example, we can now simulate an earthquake wave hitting one pier before the next, or with one pier on soil and the other on rock. Such realism cannot be achieved with a single table, no matter how big it is.”
CUSTOMER BENEFITS
UNR-NEES seismic testing for the FHWA was completed in March 2012 after nine months of continuous experimental activities, equipping the U.S. government with a wealth of test data on curved span bridge behavior under earthquake conditions. At the time of this writing, FHWA was well on its way to establishing industry design guidelines, benefiting civil engineers and citizens around the world.
UNR-NEES is currently undergoing a major expansion that includes construction of a second, larger test facility located next door to the existing facility. The 3,658-square-meter (12,000-square-foot) expansion will house all four shake tables, opening the existing facility for other large-scale floor tests. MTS is again providing the new lab’s hydraulics engineering, shake table relocation and current system upgrades.
According to Sherif Elfass, Ph.D., Research Assistant Professor and NEES Site Operations Manager, UNR-NEES researchers are constantly pushing the boundaries of what’s possible. He attributes the facility’s partnership with MTS as a major contributor to this confidence to explore uncharted territory.
“Our attitude is to say, ‘Yes we can do it,’ knowing that we will collaborate with MTS to figure out a way together,” Elfass said. “Having this backup of MTS expertise is key, especially as we expand. We consider MTS to be a pillar of our success, and our future is tied to this ongoing relationship.”
Laplace agrees. “Once MTS hands over the keys, that’s definitely not the end to the story,” he said. “There’s always a lot of interaction going on involving upgrades, maintenance and technical questions. MTS has a lot of extremely knowledgeable people, in a lot of different areas. You just can’t find such broad and applicable knowledge anywhere else."