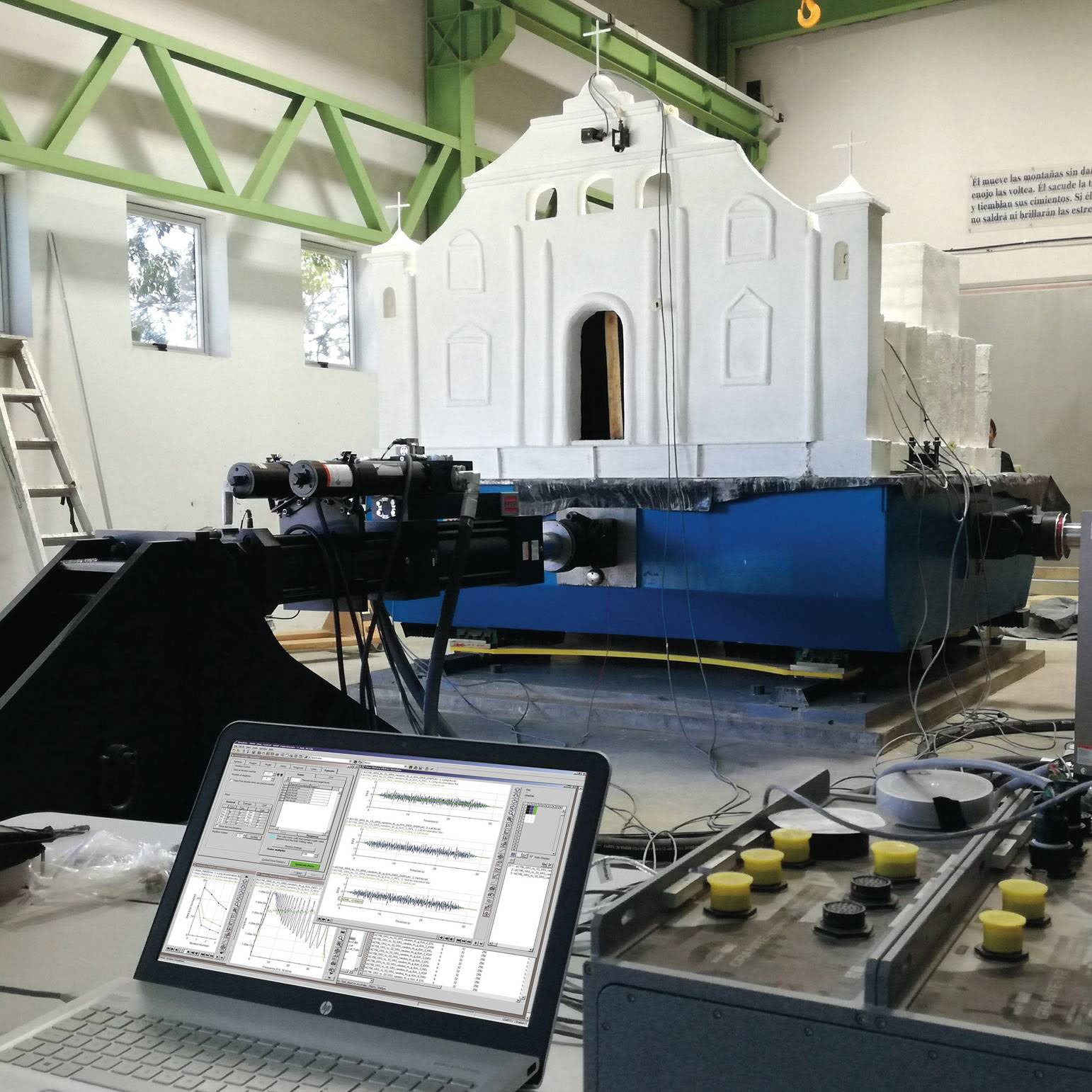
Q: What are some of the major challenges that seismic test labs face today?
Peter Gunness: Scientists first started measuring earthquake acceleration records in the mid-twentieth century, populating today’s databases with thousands of ground motion recordings. The strongest ground motion earthquakes that cause the most damage and deaths have unique attributes, so each major earthquake teaches us something new. This places demands on test systems for simulating all the possible seismic scenarios to validate earthquake readiness. Since many major earthquakes exert forces in a unique manner, they often prompt changes in structural building codes, qualification test standards and seismic testing equipment requirements.
Everyone wants to test specimens as close to full scale as possible, because this provides the most accurate and pure simulations of real-world specimen behavior. However, because structural seismic tests involve buildings, bridge segments and other extremely large and heavy test articles, the power and space requirements for testing at near actual size become cost-prohibitive. Labs have to work with a scale model of reality, which introduces inaccuracies that must be accounted for during testing.
Most earthquakes have very low-frequency, large-displacement content, but when scale model specimens are tested, the time axis compression increases the frequency content and reduces displacement. This presents design and servo-control challenges, because the system needs to perform over a relatively large frequency range and specimens are assembled directly atop the vibration table. The added mass of the specimen affects both table tuning and response.
Additionally, any forces applied to the shake table for tuning purposes can damage the specimen and fundamentally change its behavior. To protect the specimen and test fidelity, tuning has to be done at reduced amplitude. And during testing, the resonances and changing dynamics of the test specimen must be accounted for by the control system, in such a way that minimizes errors and ensures that the time history play-out is accurately achieved.
Q: How is MTS helping these test labs address these challenges?
Gunness: One primary way is through our flagship seismic qualification and simulation software, STEX Pro. This software incorporates our best-in-class Remote Parameter Control technology, known as “RPC®,” to allow precise and repeatable seismic qualification tests and simulations on civil structures and substructures, as well as non-structural equipment.
This software combines advanced seismic simulation tools with a suite of applications for precisely controlling complex multi-channel mechanical test systems. An iterative process is employed to accurately reproduce accelerations, velocities and displacements from recorded time histories and profiles that our customers define.
STEX Pro software is the ideal tool for any multidimensional seismic test application. It is versatile enough to simulate almost any seismic event on specimens of any scale and on any portion of the specimen, for configurations involving one or multiple degrees of freedom and one or several shake tables.
For qualification testing such as the Bellcore, AC156 and IEE693 specifications, STEX Pro software offers a menu of Shock Response Spectrum (SRS) tools. Test labs can generate shock response spectra from acceleration time history inputs, or an Inverse SRS function can convert SRS data into random time history outputs, which can be used as a desired response for simulation.
Q: Why is STEX Pro software important to seismic simulation?
Gunness: For seismic testing, the software allows actual earthquake force and motion data to be captured in the real world and precisely replicated to specimens in the test lab using one or more shake tables. This provides test engineers with insight into how civil and non-civil structures will perform under highly realistic seismic conditions.
Q: What measures does the software employ to uphold tuning and simulation accuracy?
Gunness: Seismic laboratory tests start with a model of the system, which is called the Frequency Response Function, or FRF. To minimize specimen damage, this FRF is measured at a very low amplitude level. However, sometimes low amplitude can result in modeling errors.
STEX Pro software includes sophisticated tools used to assess the quality of the FRF, using coherence and signal-to-noise tests while providing guidance for the usable simulation control band. The FRF is inverted and used in combination with the desired data to iteratively generate target level drive files. During each iteration step, Turbo Adaptive Inverse can be employed to improve the inverse FRF. This enhances simulation accuracy for non-linear systems.
Q: How does STEX Pro software differ from other control and command compensation techniques?
Gunness: MTS seismic control systems use a variety of advanced, real-time control techniques to optimize system performance. Those include fixed control techniques such as three-variable control, force balancing and cross-coupling compensation, as well as command compensation techniques including harmonic cancellation, amplitude phase control and adaptive inverse control.
These and other techniques are integrated into the seismic control system toolbox. They are used to overcome the seismic system control challenges previously described, along with improving overall system fidelity. STEX Pro software doesn’t replace the control functions, but is instead layered on top of the controls. Like the command compensators, the software helps to improve system fidelity and accuracy, but it does far more in a single, integrated package. It replaces command compensators resident in the controls, and also works much better on systems with large amounts of cross-coupling and/or multi-table scenarios.
Q. How will seismic test labs benefit from partnering with MTS?
Gunness: A partnership with us is about more than best-in-class software, controls and test equipment alone. Test labs that work with MTS have access to decades of hands-on experience and proven best practices. Since STEX Pro software is based on RPC technology, we offer a deep bench of local support and test methodology know-how around the world. This expertise gets directly applied toward helping our customers optimize the accuracy and efficiency of their testing program to meet both their current and long-term needs.
We are also fortunate to be working closely with some of the world’s most forward-thinking seismic test engineers, many of whom are leveraging multi-table configurations powered by STEX Pro software. The direct input from these customers is vital in our ongoing pursuit to add useful new features and functionality to future releases.
It is this unique combination of technology and domain expertise that allows our customers to convert more data into information and more information into knowledge, ultimately benefiting them in the form of more earthquake-resistant civil and non-civil structures.
Peter Gunness: Scientists first started measuring earthquake acceleration records in the mid-twentieth century, populating today’s databases with thousands of ground motion recordings. The strongest ground motion earthquakes that cause the most damage and deaths have unique attributes, so each major earthquake teaches us something new. This places demands on test systems for simulating all the possible seismic scenarios to validate earthquake readiness. Since many major earthquakes exert forces in a unique manner, they often prompt changes in structural building codes, qualification test standards and seismic testing equipment requirements.
Everyone wants to test specimens as close to full scale as possible, because this provides the most accurate and pure simulations of real-world specimen behavior. However, because structural seismic tests involve buildings, bridge segments and other extremely large and heavy test articles, the power and space requirements for testing at near actual size become cost-prohibitive. Labs have to work with a scale model of reality, which introduces inaccuracies that must be accounted for during testing.
Most earthquakes have very low-frequency, large-displacement content, but when scale model specimens are tested, the time axis compression increases the frequency content and reduces displacement. This presents design and servo-control challenges, because the system needs to perform over a relatively large frequency range and specimens are assembled directly atop the vibration table. The added mass of the specimen affects both table tuning and response.
Additionally, any forces applied to the shake table for tuning purposes can damage the specimen and fundamentally change its behavior. To protect the specimen and test fidelity, tuning has to be done at reduced amplitude. And during testing, the resonances and changing dynamics of the test specimen must be accounted for by the control system, in such a way that minimizes errors and ensures that the time history play-out is accurately achieved.
Q: How is MTS helping these test labs address these challenges?
Gunness: One primary way is through our flagship seismic qualification and simulation software, STEX Pro. This software incorporates our best-in-class Remote Parameter Control technology, known as “RPC®,” to allow precise and repeatable seismic qualification tests and simulations on civil structures and substructures, as well as non-structural equipment.
This software combines advanced seismic simulation tools with a suite of applications for precisely controlling complex multi-channel mechanical test systems. An iterative process is employed to accurately reproduce accelerations, velocities and displacements from recorded time histories and profiles that our customers define.
STEX Pro software is the ideal tool for any multidimensional seismic test application. It is versatile enough to simulate almost any seismic event on specimens of any scale and on any portion of the specimen, for configurations involving one or multiple degrees of freedom and one or several shake tables.
For qualification testing such as the Bellcore, AC156 and IEE693 specifications, STEX Pro software offers a menu of Shock Response Spectrum (SRS) tools. Test labs can generate shock response spectra from acceleration time history inputs, or an Inverse SRS function can convert SRS data into random time history outputs, which can be used as a desired response for simulation.
Q: Why is STEX Pro software important to seismic simulation?
Gunness: For seismic testing, the software allows actual earthquake force and motion data to be captured in the real world and precisely replicated to specimens in the test lab using one or more shake tables. This provides test engineers with insight into how civil and non-civil structures will perform under highly realistic seismic conditions.
Q: What measures does the software employ to uphold tuning and simulation accuracy?
Gunness: Seismic laboratory tests start with a model of the system, which is called the Frequency Response Function, or FRF. To minimize specimen damage, this FRF is measured at a very low amplitude level. However, sometimes low amplitude can result in modeling errors.
STEX Pro software includes sophisticated tools used to assess the quality of the FRF, using coherence and signal-to-noise tests while providing guidance for the usable simulation control band. The FRF is inverted and used in combination with the desired data to iteratively generate target level drive files. During each iteration step, Turbo Adaptive Inverse can be employed to improve the inverse FRF. This enhances simulation accuracy for non-linear systems.
Q: How does STEX Pro software differ from other control and command compensation techniques?
Gunness: MTS seismic control systems use a variety of advanced, real-time control techniques to optimize system performance. Those include fixed control techniques such as three-variable control, force balancing and cross-coupling compensation, as well as command compensation techniques including harmonic cancellation, amplitude phase control and adaptive inverse control.
These and other techniques are integrated into the seismic control system toolbox. They are used to overcome the seismic system control challenges previously described, along with improving overall system fidelity. STEX Pro software doesn’t replace the control functions, but is instead layered on top of the controls. Like the command compensators, the software helps to improve system fidelity and accuracy, but it does far more in a single, integrated package. It replaces command compensators resident in the controls, and also works much better on systems with large amounts of cross-coupling and/or multi-table scenarios.
Q. How will seismic test labs benefit from partnering with MTS?
Gunness: A partnership with us is about more than best-in-class software, controls and test equipment alone. Test labs that work with MTS have access to decades of hands-on experience and proven best practices. Since STEX Pro software is based on RPC technology, we offer a deep bench of local support and test methodology know-how around the world. This expertise gets directly applied toward helping our customers optimize the accuracy and efficiency of their testing program to meet both their current and long-term needs.
We are also fortunate to be working closely with some of the world’s most forward-thinking seismic test engineers, many of whom are leveraging multi-table configurations powered by STEX Pro software. The direct input from these customers is vital in our ongoing pursuit to add useful new features and functionality to future releases.
It is this unique combination of technology and domain expertise that allows our customers to convert more data into information and more information into knowledge, ultimately benefiting them in the form of more earthquake-resistant civil and non-civil structures.
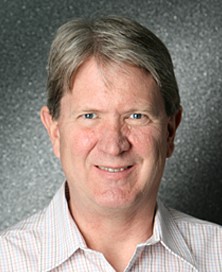