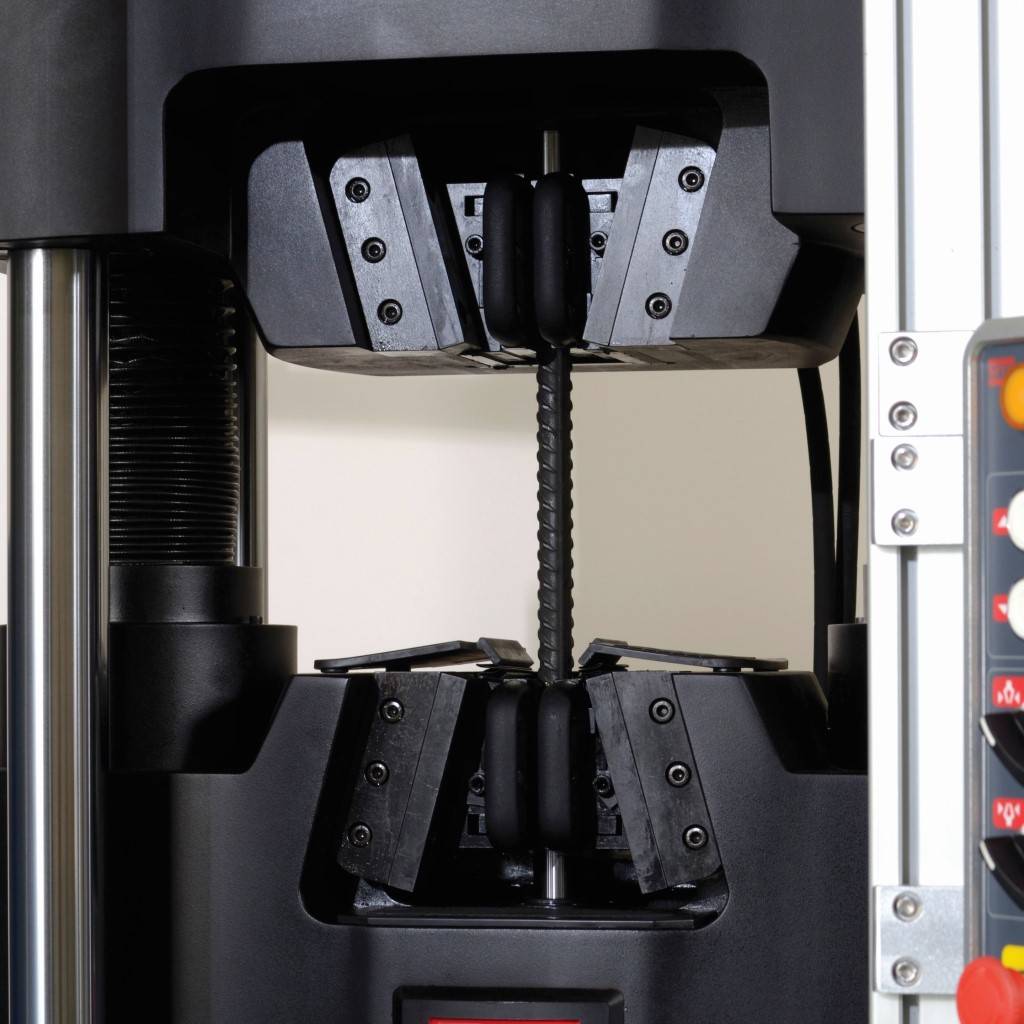
Q: What trends in civil engineering or construction are driving innovation in building materials?
Rick Bearden: Enhancing the earthquake resistance of civil structures - buildings and bridges - in seismic zones is an ongoing global focus; civil engineers and designers are continually searching for ways to improve structural safety and protect human life, so the drive for innovation is constant. One noteworthy trend is research into the use of ultra-high-strength rebar (reinforcing bar) in RC (Reinforced Concrete) structures. Specifically, researchers are exploring how to enhance the inelastic behavior of reinforced concrete structures to prevent them from failing catastrophically in seismic events; for that, their findings suggest dramatically increasing rebar strength. A great example of this is from Japan, where they currently have rebar capable of withstanding yield stresses up to 1,275 MPa (megapascals), which is just astronomical compared to the 275 – 520 MPa range of conventional rebar.
Q: Explain how reinforced concrete (RC) members can serve to enhance a structure’s earthquake-resistance.
Bearden: Rebar gives a reinforced concrete beam or column its ductility - or ability to deform under tensile stress. By nature, concrete performs well when loaded in compression, but it is brittle and cannot handle tension caused by bending or buckling. Reinforcing with steel rebar adds elastic properties, allowing an RC member to handle some bending load, returning to its original state when the load is removed. Required elastic properties of RC members are well-defined in current building and civil engineering codes around the world. In an earthquake event, however, a structure is subject to enormous lateral forces that can drive it into an inelastic condition, where elongation or yielding prevents it from returning to its original stress state. This is when structural failure occurs. Ultra-high strength rebar serves to enhance a structure’s performance in the inelastic range, enabling it to avoid complete failure even when badly damaged.
Q: Describe the ongoing research into increasing the strength of rebar and the ductility of RC members.
Bearden: Reinforced concrete design is a well-established engineering discipline, but the focus on new, ultra-high-strength rebar is prompting renewed research into the fundamentals, such as the chemical formulation of the high-strength alloys, rebar manufacturing processes, and how the rebar is deployed within RC members. Mechanical testing plays a critical role in all facets of this research: the materials that comprise the rebar and the mechanical splices that join rebar lengths together must be characterized; assembled rebar/mechanical splice components must be tested for strength and fatigue; and the RC members themselves must be tested to understand how rebar strength, concrete strength and placement of the rebar within the RC member can enhance earthquake resistance. As you would expect, this research is focused in seismically active areas, including Japan, Russia, Ukraine, the United States, Korea, India and China. However, universities around the world, not just those in seismic activity zones, are also contributing fundamental research in this area; a good example is the University of Minnesota, which is part of the NEES (Network for Earthquake Engineering Simulation) consortium.
Q: How does the development of high yield strength rebar impact mechanical testing requirements?
Bearden: Obviously, if the yield strengths are increasing then the tension forces will increase, so mechanical testing requires much higher force load frames for testing rebar and splicing materials and assembled components. To underscore this, in the last couple years we’ve seen inquiries for 1 million pound - even 2 million pound - load frames for testing rebar. This is new, until now demand for rebar tests systems has always been in the range of a half million pounds or less. And of course, the accessories that come with the test system – grips, fixtures, sensors – are also affected by higher force requirements. The use of structural test rigs for the assembled RC beams will evolve, too, as the renewed research into inelastic behavior will change testing objectives and focus. Another impact is that researchers are investigating not only static, tension-only behavior, but they want to conduct dynamic, through-zero tension-compression fatigue tests, as well.
Q: What mechanical testing solutions can MTS offer to meet such high-force requirements?
Bearden: To meet higher force materials and components testing requirements – rebar, mechanical splicing and rebar/splicing assemblies – we offer a complete selection of turnkey load frame solutions that include controls, application software, grips, fixtures and accessories, and hydraulic power and distribution, For dynamic tension-tension or tension-compression cycling, we have a complete family of fatigue-rated, four-column servohydraulic load frames with an extremely broad range of force capacities, spanning 1.0 to 30.0 MN.
To test full-scale structures - beams or columns with high-strength rebar integrated – we provide turnkey systems, comprising fatigue-rated civil test actuators, high-force swivels, large portal frames or reaction structures, controls, application software, accessories, and hydraulic power and distribution, if necessary. Typically, these systems are used to conduct three- or four-point bend tests and are more than capable of driving high-strength RC test articles to failure.
Q: Looking to the future, will any new technology be required to meet these needs?
Bearden: We need to make sure the MTS portfolio continues to include what the customers require. There are opportunities for further innovation in our hydraulic wedge grip technology. The forces required for testing high-strength rebar are pushing the envelope for our popular side-loading grips, which enable relatively quick and easy specimen installation. However, that design doesn’t scale up easily when you reach the million-pound range because the stresses in the grip housing get extremely high. Our closed-housing 641 style grips are a viable alternative for testing in this range, but don’t offer the same ease of installation. So, we’re investigating possible refinements to our side-loading wedge grips. In addition, we’re also exploring the potential advantages of different types of measurement technologies, such as optical or laser extensometry. That said, the current MTS offering is very sound for testing high-strength rebar and RC structures. Our targeted turnkey solutions, the depth and breadth of our experience in this application area, and our ability to provide researchers what they need to meet their exact requirements remains unmatched.