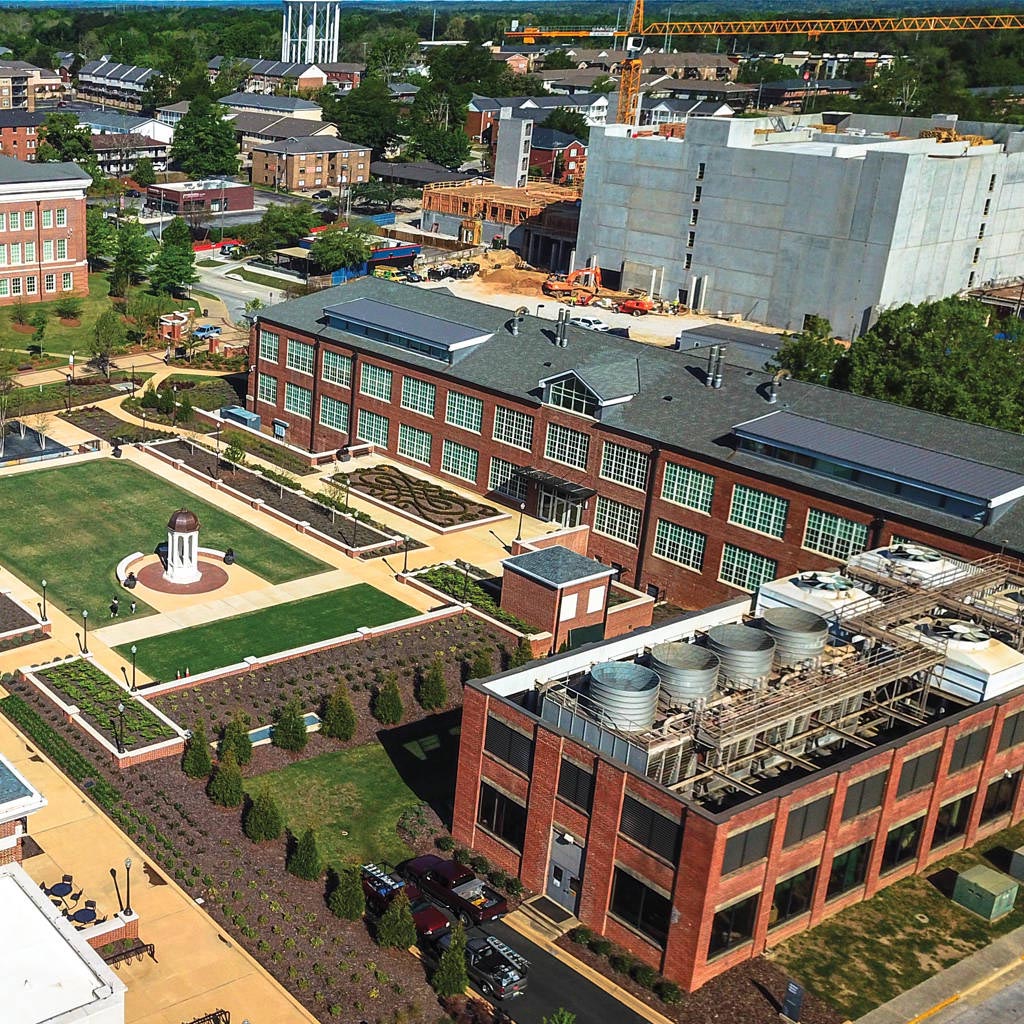
Fatigue is still the cause for the majority of mechanical failures in many structural applications, and a typical fatigue failure has at least 3 stages: crack initiation, crack propagation, and final fracture. It is well established that surface defects (e.g. surface roughness), volumetric defects (e.g. pores, lack of fusion), and microstructure are influential factors on fatigue performance of metallic materials. It is also worth noting that cracks often nucleate from/near the surface due to several reasons such as easier inelastic deformation, higher stresses/strains from external loads, and stress concentration effects.
The booming interest in the layer-wise manufacturing processes, also called additive manufacturing (AM), has attracted many industries to consider adopting these technologies. Although the AM processes seem straightforward (layer-by-layer manufacturing), there are many physical and metallurgical complexities associated with the repetitious melting/rapid solidification during fabrication. The intricate thermal history (i.e. thermal gradient, cooling rates, etc.) experienced by the part during fabrication influences the microstructure, crystallographic texture, residual stresses, surface roughness, and formation of volumetric defects (e.g. gas entrapped pores and lack of fusions), which consequently affect the mechanical properties, specifically under cyclic loading [1, 2]. In this regard, there are several studies that investigated the effect of volumetric defects, surface roughness, and microstructure on fatigue behavior of additively manufactured (AM) metallic materials [3].
Most studies have reported an inferior fatigue resistance for AM metallic materials, even in their machined surface condition, as compared to their wrought counterparts due to the detrimental effects of volumetric defects inherent to the AM processes [4]. In this regard, much effort has been made to reduce the size and number of these defects by adjusting the process parameters. However, even by using the most optimized manufacturing process parameters, there still will be some process-induced defects, such as gas entrapped pores in the AM parts, which can exacerbate their fatigue performance. Post-manufacture surface and thermal processes are often essential to enhance the fatigue performance of AM materials. For instance, it can be seen in Figure 1 that removing the surface roughness by machining can improve the fatigue performance of laser beam powder bed fused (LB-PBF) 17-4 PH SS significantly [1]. Similar effects of surface roughness on fatigue behavior have been reported for other material systems as well [5].
Figure 1
Stress-life fatigue comparison of LB-PBF 17-4 PH SS undergone CA-H900 heat treatment condition with as-built and machined surface conditions [1].
Post-manufacture thermal processes (e.g. hot isostatic pressing (HIP) or heat treatment) may influence the fatigue performance of AM metallic materials associated with changes in the microstructure (e.g. pore size and distribution, grain size and morphology, precipitation behavior, etc.) [2,4]. For instance, post-manufacture heat treatment processes including the solution heat treatment process (known as condition A (CA) for 17-4 PH SS) enhance the fatigue resistance of LB-PBF 17-4 PH SS (Figure 2). This is attributed to the more homogenized and finer microstructure obtained after the CA step as compared to the microstructure produced after heat treatment procedures without this step [1].
Figure 2
Stress-life fatigue data of LB-PBF 17-4 PH SS, in as-built surface condition, undergone various heat treatment procedures [1]. Note that hollow markers show the heat treatment procedures without CA step, while filled markers present heat treatment conditions including CA step.
Interestingly, additively manufactured metallic materials mostly exhibit similar fatigue crack growth behavior (FCG) with that of the wrought counterpart in Paris regime (i.e. the stable crack growth region). Figure 3 is an example showing that LB-PBF 17-4 PH SS has identical FCG behavior as compared to the wrought material [6]. However, the LB-PBF 17-4 PH SS shows a higher FCG rate (i.e. lower FCG resistance) in the unstable FCG region (i.e. high ÄK region) as compared to the wrought material. This may be due to the differences in the microstructure as well as the presence of volumetric defects in LB-PBF 17-4 PH SS resulting in lower cyclic fracture toughness than that of the wrought material. Such defects can also increase the FCG rate of LB-PBF 17-4 PH SS in the near-threshold region.
Figure 3
Fatigue crack growth (FCG) behavior of LBPBF 17-4 PH SS undergone CA-H900 heat treatment compared with that of the wrought counterpart with the same heat treatment condition [6].
References
1. Nezhadfar PD, Shrestha R, Phan N, Shamsaei N. Int J Fatigue. 2019;124:188-204.
2. Pegues J.W., Shao S., Shamsaei N., Sanaei N., Fatemi A., Warner D.H., Li P., Phan N., Int J Fatigue, 2020: 132, p.105358.
3. Fatemi A, Molaei R, Simsiriwong J, Sanaei N, Pegues J, Torries B, Phan N, Shamsaei N., Fatigue & Fracture of Eng. Mater. & Struc. 2019: 991-1009.
4. Molaei R., Fatemi A., Sanaei N., Pegues J., Shamsaei N., Shao S., Li P., Warner D.H., Phan N., Int J Fatigue, 2020: 132, p.105363.
5. Pegues J., Roach M., Williamson R. S., Shamsaei N. Int J Fatigue, 116, 2018: 543-552.
6. Nezhadfar PD, Burford E, Anderson-wedge K, Zhang B, Daniewicz SR, Shamsaei N., Int J Fatigue. 2019.
The National Center for Additive Manufacturing Excellence (NCAME) at Auburn University was formed in 2017 through a collaboration with the NASA Marshall Space Flight Center.