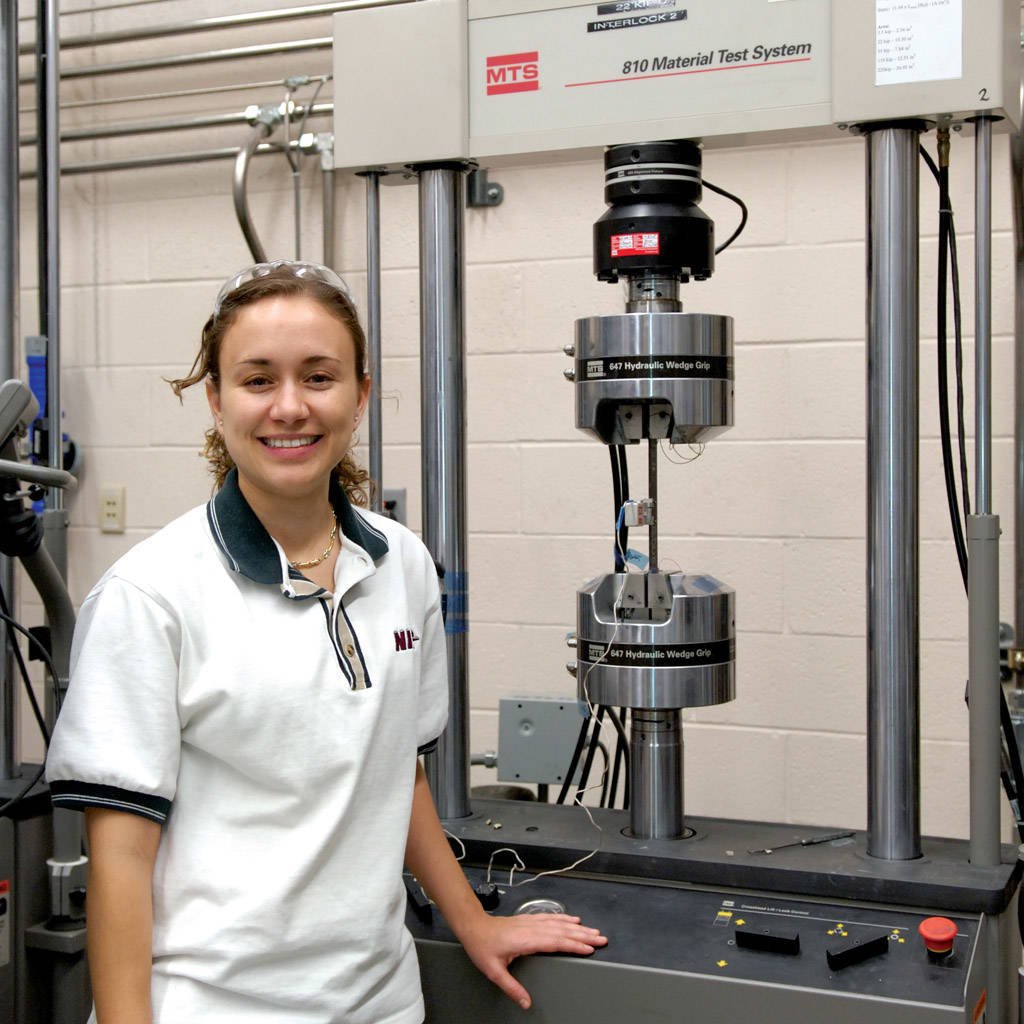
CUSTOMER CHALLENGE
Since 1985, Wichita State University’s National Institute for Aviation Research (NIAR) has met the industry’s need for research, design, testing and certification by providing competitive and innovative solutions that meet high technological standards. Located in Wichita, Kan., NIAR brings together university, government and industry to advance technologies for aviation and related industries. NIAR’s 120,000 square foot facility is home to 15 labs, which conduct research in aerodynamics, aging aircraft, crash dynamics, composites and advanced materials, advanced joining, structural components, virtual reality, computational mechanics, among other areas.
The Fatigue and Fracture Lab opened its doors in 2003. The lab supports various research programs for numerous organizations, including material suppliers, aircraft manufacturers, the Federal Aviation Administration (FAA) and the U.S. Air Force. Mechanical testing of various materials is conducted to generate design allowables, fatigue and damage tolerance properties of materials under constant amplitude or spectrum loading. This information is typically used during the screening phase of a material or to populate the pyramid necessary to the building block approach adopted by all manufacturers to certify a product.
Since its inception, the Fatigue and Fracture Lab has relied upon MTS Systems to provide testing equipment that fulfills its evolving requirements.
“Our testing needs are in constant evolution, as each research and development program we undertake often has its own unique requirements,” said Lamia Salah, manager of NIAR’s Fatigue and Fracture Lab. “MTS has been a dependable partner from the very beginning, always going the extra mile to ensure we receive the equipment and support required.”
For example, customers increasingly request NIAR’s lab to conduct fatigue testing for larger loads. As a result, the lab recently purchased a 55 KIP load frame from MTS; however, the grips to accompany the frame were not immediately available and NIAR was under a tight deadline to complete tests that required this product. Through its extensive network of customers, MTS was able to provide NIAR with access to these grips on a temporary basis until the lab received its own order.
MTS SOLUTION
The Fatigue and Fracture Lab uses a wide range of MTS equipment, software and accessories to support its testing requirements, including servohydraulic load frames; FlexTest GT Digital Servocontrollers and TestStar 21 controllers; TestWorks and MultiPurpose TestWare (MPT) software; hydraulic power supplies; transducers; extensometers; displacement gauges; and strain and displacement measuring devices.
While conducting bending tests, displacement gages are used to monitor maximum deformation at the center of the specimen. During fatigue tests, MTS extensometers are used to monitor the compliance of the material as it is subjected to fatigue loading. The MTS software is used to build elaborate testing programs that can be used to trigger different commands depending on the test specimen response.
CUSTOMER BENEFIT
To help it reap the full benefits of MTS systems, the Fatigue and Fracture Lab works with the company’s consulting team to learn how to best optimize specific features and functionality.
Ultimately, the entire MTS solution enables NIAR to improve testing productivity by reducing the amount of time spent writing test programs, setting up tests and acquiring test data. For instance, the lab can use built-in functions of MTS software to quickly and nearly automatically create test programs and acquire data.
And, because the system is extremely user-friendly, lab employees can be trained to set up specific test methods and use MTS hardware and software in as little as two months.
“We’ve been using MTS for as long as I’ve been working for NIAR, which predates the creation of the Fatigue and Fracture Lab,” Salah commented. “We continue to be pleased with the high-quality products MTS provides and plan to continue acquiring more of their equipment to fulfill our expanding needs.”