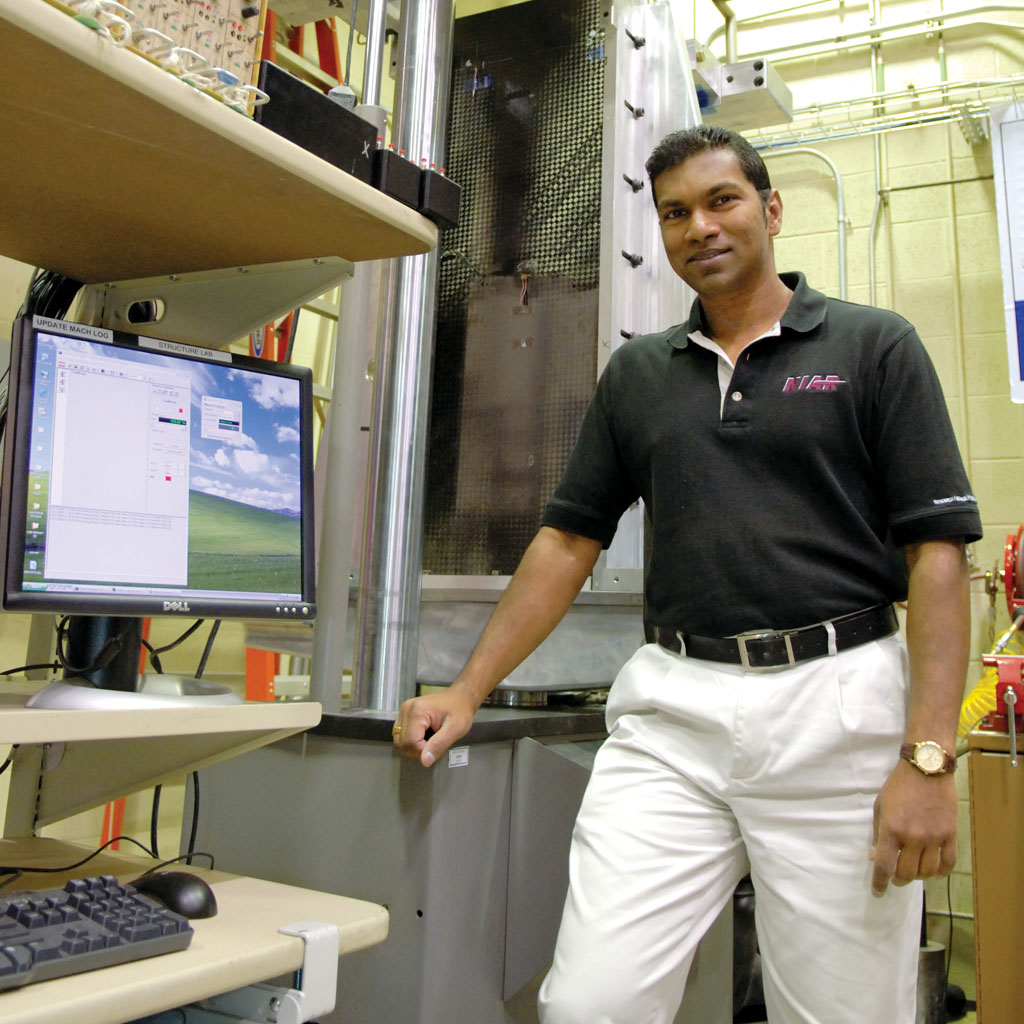
CUSTOMER CHALLENGE
Since 1985, Wichita State University’s National Institute for Aviation Research (NIAR) has met the industry’s need for research, design, testing and certification by providing competitive and innovative solutions that meet high technological standards. Located in Wichita, Kan., NIAR brings together university, government and industry to advance technologies for aviation and related industries. NIAR’s 120,000 square foot facility is home to 15 labs, with research in advanced joining, aerodynamics, aging aircraft, crash dynamics, composites and advanced materials, structural components, virtual reality, computational mechanics, and many more.
NIAR’s Structures Laboratory provides research and testing capabilities for test articles ranging from material samples to large-scale aircraft structures. The research conducted by the Structures Lab allows commercial, general aviation and military organizations to better understand how to reduce manufacturing costs while increasing operational efficiency. Research projects related to damage tolerance, effects of defects and element testing for design and certification of aircraft and unmanned aerial vehicles make NIAR’s Structures Lab one of the busiest – and most sought after – facilities of its kind.
The lab supports the testing needs of the Federal Aviation Administration’s (FAA) Center of Excellence for Composites and Advanced Materials (CECAM) and the NASA National Center for Advanced Materials Performance (NCAMP), both headquartered at NIAR. Through these organizations, NIAR is developing cost-effective methods for qualifying composite material by sharing central material qualification databases. In the future, using these shared databases, a manufacturer will be able to select an approved composite material system from which to fabricate parts and perform a smaller subset of testing, compared to the materials testing already completed by NCAMP, for a specific application.
“For materials to be accepted into our shared databases, the raw materials must be manufactured in accordance with material specifications, which impose strict control over key physical, chemical and mechanical properties,” said Waruna Seneviratne, manager of the Structures Lab. “We’re able to accomplish this research and meet our testing objectives, in large part, because of our use of advanced materials testing equipment from MTS Systems.”
MTS SOLUTION
The Structures Lab is equipped with a wide variety of standard and custom MTS test fixtures and extensometers, including a laser extensometer and KGR-type extensometers for adhesive testing. The lab also utilizes MTS environmental cham bers, allowing it to perform static and spectrum fatigue tests in temperatures ranging from –200°F to 2,500°F, as well as in humidity- controlled and salt-fog environments. MTS test solutions are equipped with advanced FlexTest software, industry-leading control technology and multi-channel data acquisition capabilities, giving the lab the flexibility to perform virtually any materials testing research needed.
CUSTOMER BENEFIT
In coordination with the FAA and NCAMP, the lab completed several significant research and testing programs during the past year utilizing its sophisticated MTS solutions. Much of the research was conducted to speed development of advanced aircraft structures, such as the Boeing 787 and Airbus A380, and will help drive aircraft vehicle development during the next decade as new, emerging technologies are applied to design and placed into production throughout the aircraft industry.
Using MTS equipment, the lab performs adhesive characterization and element testing of fatigued and damaged bonded joints. The lab identifies characteristic responses of bonded structures to real-world manufacturing and repair defects. Research includes the effects of manufacturing defects, lightning strikes and low-velocity impacts on the residual strength of bonded joints. This work will help establish guidelines for adhesive and process controls for bonded structures.
The team also investigates the intricacy associated with the use of unconventional advanced composite materials in aircraft structures through finite element analysis and subcomponent testing. From their findings, the lab developed a simplified methodology for mechanical property calculation of non-orthogonal braided composite for tapered structures using an existing material database.
“We’re very familiar with MTS equipment, as NIAR uses the company’s technology extensively through its many labs to conduct advanced research,” Seneviratne said. “We’ve yet to find something that MTS’ software and equipment can’t do.”