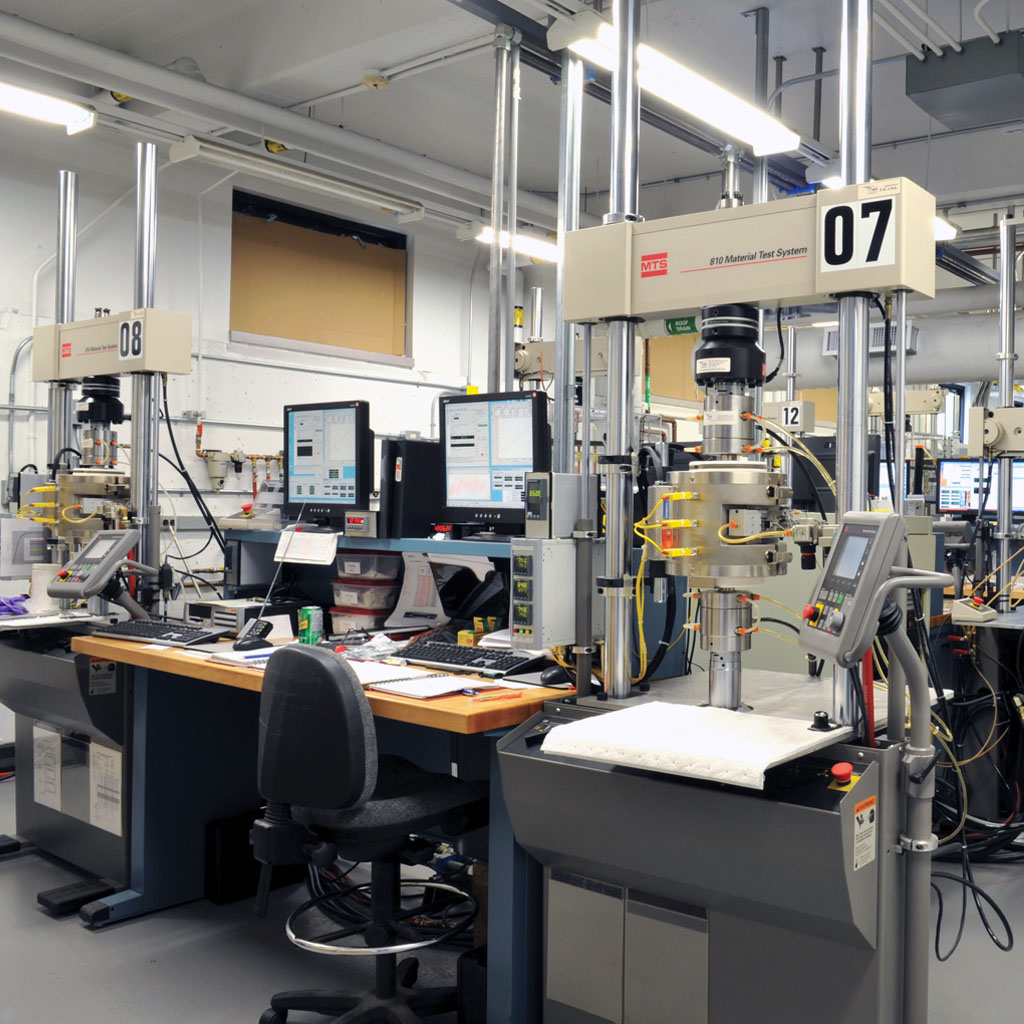
CUSTOMER CHALLENGE
The development of high-temperature materials—those that can perform at extreme temperatures for extended periods—is setting the stage for the next generation of jet engines and gas turbines that will redefine expectations for fuel-efficiency. Some of the most advanced research in this field happens in the Structures and Materials Performance Laboratory, part of the National Research Council of Canada’s Institute for Aerospace Research located in Ottawa, Ontario.
Here, the Materials and Component Technologies Group, a team of 15 research scientists, specializes in designing, developing and testing new gas turbine materials, including high-temperature alloys and ceramic matrix composites. The group pursues in-house research and also collaborates with commercial engine manufacturers such as Pratt & Whitney, Rolls-Royce and General Electric, and material vendors such as ATI Allvac and Carpenter Technologies. To determine exactly how new materials will perform—and how long they will last—when exposed to increasingly high temperatures they must pursue a wide array of precision mechanical testing.
“We do anything from tensile, creep and fracture toughness testing to more specialized tests, such as fretting fatigue, thermomechanical fatigue, fatigue crack growth and creep crack growth rate,” said Dr. Kearsey, manager of the group’s High-Temperature Fatigue and Fracture Mechanics Facility. “We are developing the materials, testing them and then developing standard test methods for characterizing these materials, which includes figuring out the geometry of the specimen as well as duplicating the service environment of the engine in the lab.”
Right now, Dr. Kearsey’s biggest challenge is simple: heat. In previous decades, temperatures for testing stainless steel, titanium and aluminum alloys were relatively moderate. Testing today’s most advanced materials requires temperatures as much as 25 percent hotter.
“The temperatures are so high that testing the materials becomes a more complex problem,” he said. “How do you measure materials at 1000°C when the standard practice relies on equipment rated for 800°C? How do you add proper instrumentation to measure crack growth rate? It’s not impossible, but it is very complicated. We have to make absolutely sure that the temperatures and loads are 100 percent traceable, because our results are being used to make critical engine components.”
MTS SOLUTION
The Materials and Component Technologies Group deploys 18 different MTS solutions for high-temperature testing, a lineup that includes everything from legacy MTS 810 load frames to state-of-the-art MTS Landmark® Servohydraulic Test Systems.
“The reason we only use MTS load frames is stability,” Dr. Kearsey said. “When we have four or five frames running side by side, the lab is shaking. The MTS frames are so stable; there is no twisting or torsion that might misalign the specimen.”
Rounding out the facility’s test equipment are two MTS hydraulic power units, FlexTest® digital controls and Multipurpose TestWare® software. The lab also employs a full complement of MTS test accessories, including grips and fixtures, extensometers and strain gages, furnaces and induction heating units—all of which must be easy to combine and integrate into the often complex configurations required for specific high temperature tests.
“The hardware needs to work properly at different test temperatures and conditions,” Dr. Kearsey said. “We like that we can take an MTS furnace and stick it on any load frame. Interchangeability is important, especially for repeatability. When we have to do 100 tests on a similar geometry, we don’t want to spend time redoing the calibration for every single one.”
CUSTOMER BENEFITS
For Dr. Kearsey, nothing is more important than the reliability of the test hardware and software. Reliability is essential for the accuracy of the results, the productivity of the lab and the satisfaction of external clients.
“We buy MTS equipment because it almost never fails,” he said. “It doesn’t have to be replaced. It’s reliable and it’s traceable. As a research lab, traceability is a key requirement. If we do an alignment on a system, we have to be sure that is exactly what happens on the next test. It doesn’t matter if we’re testing an advanced single-crystal alloy or evaluating 50-year-old alloys for life prediction modeling. With MTS test systems, we can generate the data required to make confident decisions.”
The reliability of extensometers is particularly critical in high-temperature materials testing, especially at frequencies up to 10 Hz or with stiffer materials where measured reflections are smaller. Dr. Kearsey also cites the reliability of the software as a significant factor.
“When you’re doing thermomechanical fatigue testing, for example, the tests can last three months,” he said. “It’s very expensive for our clients. You never want to tell them the software crashed during the test and their results are invalid. MTS software is critical in this regard because it doesn’t give us that headache. It’s very reliable and many of the modules are preprogrammed for low-cycle fatigue, thermomechanical fatigue and other types of tests.”
Even now, as Dr. Kearsey works to overcome the challenges associated with testing at 1000°C, he expects the upper bound to rise. In fact, he is working with MTS to design test systems that can perform at these much hotter temperatures.
“As the newer alloys are replaced with ceramic matrix composites, we will need to run tests up to 1300°C or 1400°C,” he said. “We are already discussing how to make this happen with MTS. What size furnace will we need? What will the hot zone be? What extensometry will we need? MTS always seems to come to us at the right time. That kind of support is why we keep going back to MTS.”