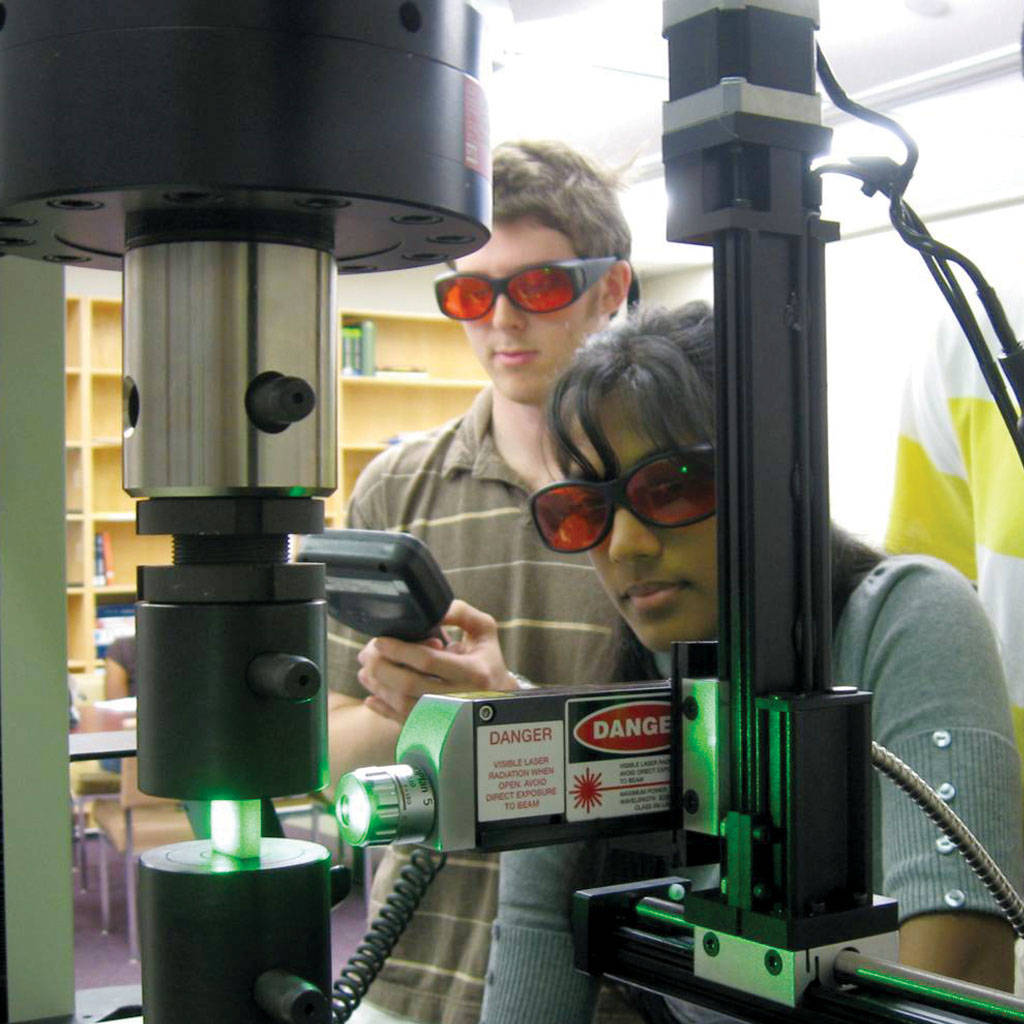
CUSTOMER CHALLENGE
Jet engine turbines must operate flawlessly within extreme-temperature environments, over many years of service and millions of miles in the air. Thermal barrier coatings are one of the technologies that make this possible. These thin layers of ceramic material conduct very little heat, enabling turbine blades to withstand very high temperatures — and allowing jet engines to operate more efficiently.
Advanced research into thermal barrier coatings is currently underway at the University of Central Florida in Orlando. The school is a partner university of the Florida Center for Advanced Aero-Propulsion (FCAAP), a state-funded research organization formed to develop a highly skilled workforce and design new technologies for the aerospace industry. At UCF, researchers in the Department of Mechanical, Materials and Aerospace Engineering are studying the evolution of strain in oxides of thermal barrier coatings, gaining insight that will help improve turbine performance.
Seetha Raghavan, Ph.D., leads a team of students dedicated to analyzing the behavior of the oxide layer of thermal barrier coatings under specific thermal and mechanical loads. The team uses both spectroscopy and high-energy x-rays for acquiring in situ measurements of specimens under thermal and mechanical loads. This approach allows Dr. Raghavan’s team to observe exactly how high-strength ceramics fail in real-time.
In the past, the observation of spectral signals with strain was limited to a microprobe-based test setup. However, this approach, – with its inherent space constraints – presents demanding equipment integration challenges. Attempts to develop specialized loading equipment that would fit into the microprobe space have so far yielded systems with compromised maximum load ranges, control and accuracy.
To overcome this challenge, Dr. Raghavan decided to employ a Renishaw Raman spectrometer with a fiber-optic probe and couple this with an MTS system, allowing precision Raman/photo-luminescence data acquisition with in situ loading via remote non-contacting laser. However, this created additional challenges. The data from the spectrometer and the loading system had to interact, and both data streams needed to be stress-mapped in real-time during compression or tension.
An additional challenge proved to be the nature of the high compressive strains within the oxides of the thermal barrier coatings themselves. Calibration of the spectral peaks with strain in compression testing required the application of large loads on relatively small cross-sectional specimens of polycrystalline alumina. As the compression strength of these specimens is over an order of magnitude higher than the tensile strength, generating high-quality data and avoiding premature failure would require highly-uniform and precise application of compression loads.
“We needed precise, highly reliable loading with superior control, in a complex setup with several other instruments,” Dr. Raghavan said.
MTS SOLUTION
To fulfill these needs, Dr. Raghavan chose an MTS Insight 50 System, featuring a twin-column, 50 kN tabletop design. This system provides high-resolution control during continuous loads as well as load holding while automatic stress maps are generated- both critical for determining the strain behavior of the oxides within thermal barrier coatings using spectroscopy.
“We selected the MTS Insight 50 system because it gives us the ability to stress-test high-strength ceramics with in situ spectroscopy,” Dr. Raghavan said. “Plus, we get the added benefit of working with MTS technicians who understand how to integrate these complex setups.”
The electromechanical MTS Insight load frame is driven by best-in-class TestWorks® software, which is vital for meeting the UCF team’s needs. The software must interface seamlessly with proprietary spectrometer software, as well as ensure that spectral signals are recorded at the exact same time as loads are applied, in order for spectral load plots to be accurate.
“MTS technicians were particularly helpful getting the TestWorks software to match data collection times, and modifying the software to hold the strains,” Dr. Raghavan said. “They were genuinely interested in getting this novel combination of instrumentation to perform to our exact specifications.”
Even though the instrumentation and methods in the laboratory are highly sophisticated, it is important that the controls are intuitive and easy to use.
“Senior design students from our department took on the challenge of developing hardware and software integration modules for this novel instrumentation. The entire MTS solution was really helpful when the senior design team was integrating the instrumentation, because they did not have to spend too much time figuring out the TestWorks software,” Dr. Raghavan said. “It’s really flexible, and the interface is simple for the students to operate. It will also be very useful for our laboratory classes.”
CUSTOMER BENEFITS
Dr. Raghavan believes the research the department is conducting on thermal barrier coatings will lead to more effective structural and materials characterization tools for the entire aerospace industry.
“This is very exciting, up-and-coming technology,” she said. “These testing capabilities give us a highly sophisticated method of noninvasive measurement, which will move us forward significantly in terms of in situ mechanical characterization. This method shows strong potential for real-time assessment of high-strength ceramics as well as carbon additive composites in the field. It will deliver high-impact results for aerospace and for the broader field of materials science.”
The key is calibrating the spectral peaks with highly accurate and consistently applied loads, all of which can easily be achieved using TestWorks software and the MTS Insight 50 system.
“It is essential for our laboratory to conduct reliable, highly accurate loading and consistently deliver high-quality, high-resolution load measurements. That’s why we chose to work with MTS,” Dr. Raghavan said.
In addition to the precision hardware, the proactive approach of MTS technicians enabled the lab to create an effective testing solution quickly and easily.
“The MTS technicians were excited about our project,” Dr. Raghavan said. “They were really proactive in helping us understand what we needed for this very unique testing application. We talked extensively about integration before we purchased any MTS products, and MTS even spoke directly with the spectroscopy system manufacturer about software compatibility. They made every effort to help us achieve our goals. Together, we are successfully pushing the boundaries of what’s possible in noninvasive materials characterization.”