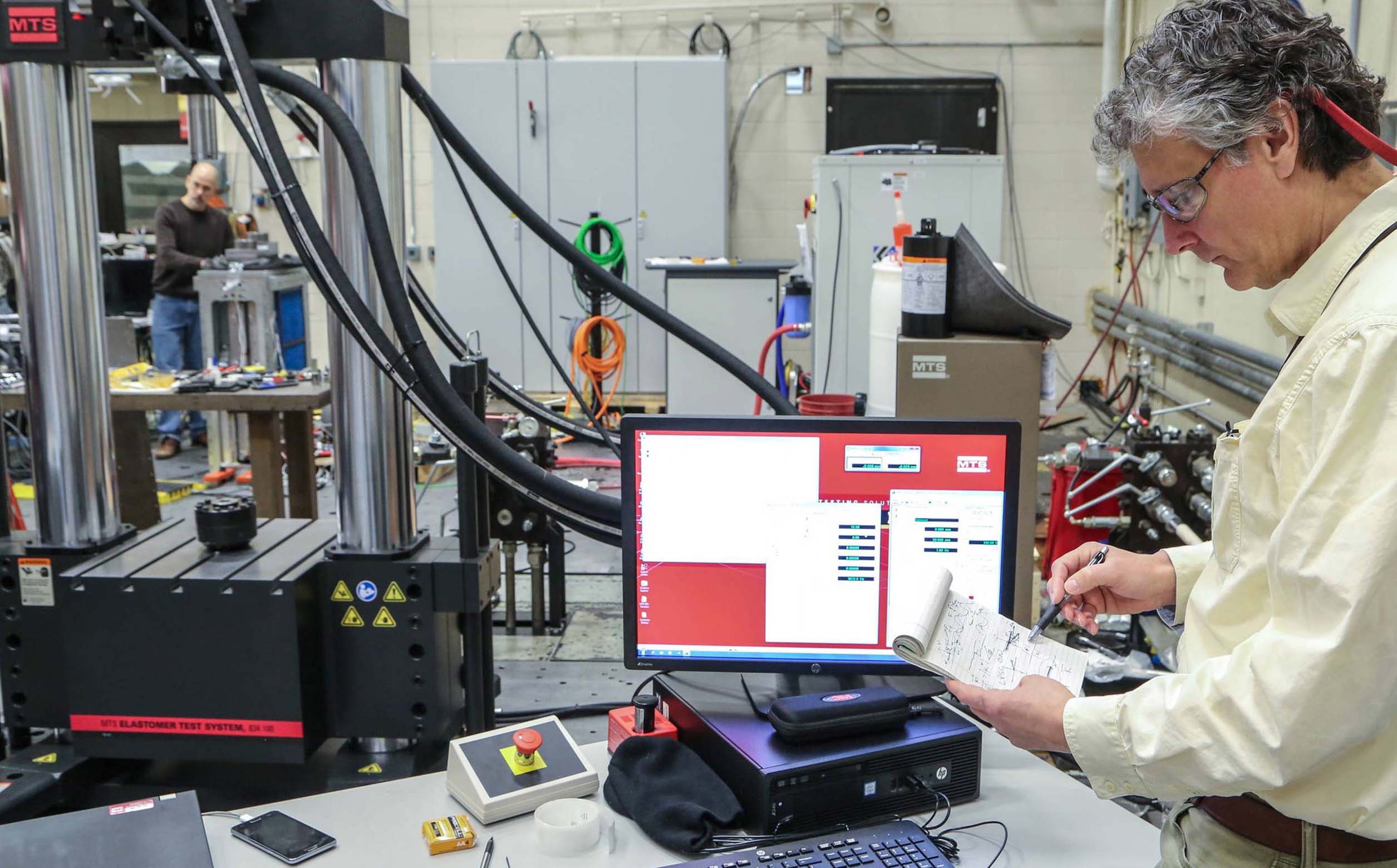
MTS R&D Engineer Byron Saari, P.E. is an expert in materials characterization, holding several patents in the field. In this interview, Saari talks about dynamic mechanical analysis, or DMA, which is a vital capability for any research team focused on elastomers, polymers and shape memory alloys.
Q: What is Dynamic Mechanical Analysis?
A: Dynamic Mechanical Analysis (DMA) is a dynamic characterization technique that measures stress as a function of strain, or force as a function of displacement. It involves applying a sinusoidal strain to the material and measuring the resulting stress. Typically, DMA also involves varying the frequency of the strain and/or the temperature of the specimen, also known as Dynamic Mechanical Thermal Analysis (DMTA).
Q: What is the role that DMA plays in the development of elastomeric materials?
A: DMA is very useful for characterizing the properties and behaviors of elastomers, polymers and shape memory alloys. These materials all exhibit damping and can be used in applications where operation at higher frequencies is critical. DMA gives researchers the tools to study damping effects in great detail. DMA allows researchers to calculate the complex modulus, storage modulus, loss modulus and tan delta of a material. One area where DMA is used is in the development of new materials for components that are lighter but still maintain high performance, which is important in a number of industries.
Q: Please describe some of the challenges involved with DMA.
A: It is very difficult to measure motion and force accurately at high frequencies. The ability to accurately measure the phase lag between the applied displacement and resulting force at these frequencies is a critical aspect of DMA. Phase lag is critical as it differentiates purely elastic materials from purely viscous materials. Elastomers, polymers and shape memory alloys all exhibit viscoelastic properties, so they fall somewhere in between the two.
Q: How does MTS help researchers address this challenge?
A: The MTS DMA software package helps ensure accurate phase measurement through specialized dynamic correction techniques. It involves measuring the phase characteristics of the force and motion transducers, and conditioning electronics, and applying proprietary calculations to correct for these effects. This package can correct for amplitude as well as phase dynamic response characteristics. It represents more than 30 years of in-house expertise in materials testing and dynamic characterization across many different applications and industries.
Q: Which systems offer this DMA capability?
A: MTS offers an extensive portfolio of dynamic test systems suitable for DMA, ranging from 250 kN to 1.25 kN force capacity at resolution down to 0.01 N. For higher-force and higher-frequency applications, the DMA package is available with many of our servohydraulic test systems, including those specifically designed for elastomer testing. MTS Acumen® Test Systems, which are electrodynamic test systems that perform a wide range of high-fidelity dynamic and static tests, are also well-suited to DMA testing. Optional chambers are available when required for Dynamic Mechanical Thermal Analysis (DMTA).
Q: Isn’t it more common to use a dedicated DMA test system?
A: It has been in the past, yes. But many researchers, especially those at universities, are now under a great deal of pressure to do more with less. They do not always have the budget to acquire one test system for every type of testing. With the MTS Acumen test system, researchers have the versatility to perform DMA testing and many other tests, all with one system. In addition, the MTS Acumen test system is designed to measure lower forces and very small displacements with its precision force transducers, high-stiffness configuration and high-resolution digital encoder.
Q: Why is the dynamic range of the system important?
A: One of the significant characteristics researchers often need to determine is the material’s glass transition temperature, when it shifts from having a hard, “glassy” quality to having a softer, “rubbery” quality. The test usually involves measuring the material in its glassy state, increasing the temperature in a controlled manner and taking frequent measurements as the material transitions through its rubbery state. When the transition occurs, the stress/strain modulus can change by a factor of a thousand. To measure it accurately, you need high dynamic displacement and force transducers and a robust control system.
Q: What other DMA capabilities does the software deliver?
A: MTS DMA software can perform time-temperature superposition, or TTS, according to the Williams-Landel-Ferry (WLF) model. This model allows materials researchers to generate master curves which are used to extrapolate the material behavior at higher frequencies through testing at lower temperatures.
Q: What industries will find the DMA software most useful?
A: There is really no limit to its application, because it is vital for characterizing any material that exhibits damping. There will be obvious applications in automotive components, biomaterials and civil engineering. But the exciting thing about materials research is its diversity. With the range of systems we offer, MTS is uniquely able to help materials researchers develop a complete DMA solution for virtually any need.