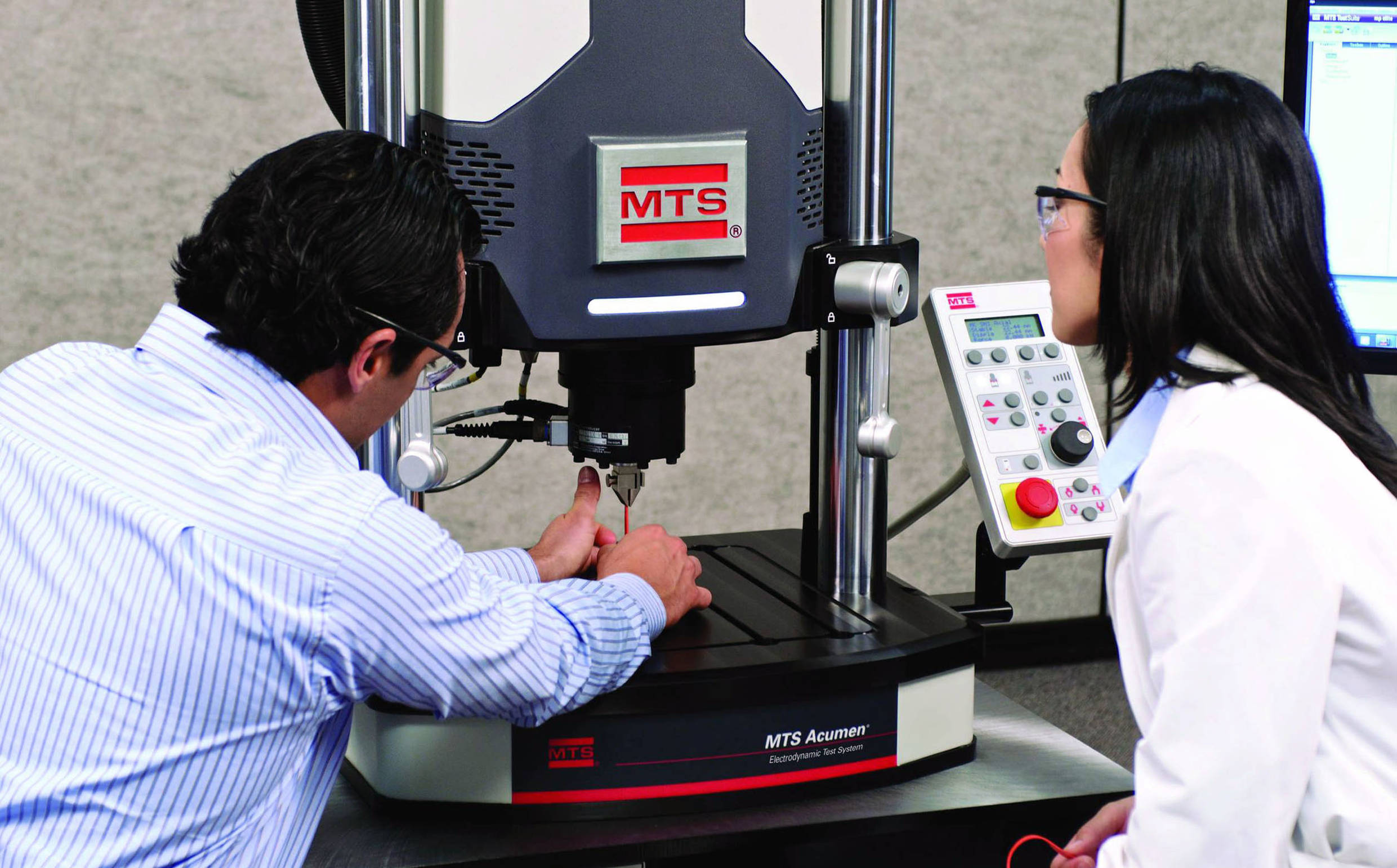
In this Q&A, one of our engineers discusses an MTS Acumen demonstration that changed a biomedical customer’s experience with electrodynamic actuation.
Q: Based on your experience demonstrating MTS Acumen test systems, what is the appeal of using electrodynamic actuation in test labs and what are some of the challenges?
A: One of the primary reasons people select electrodynamic technology is that it consumes less energy. Also, these compact systems can be installed quickly and easily in any location with a conventional electrical outlet, and they require minimal maintenance.
These benefits can be over-shadowed by some electrodynamic system's challenges with overall control, response to limits and auto-tuning. When we were approached by engineers at a biomedical materials manufacturer who had been experiencing these issues to such a degree that they had quit using their electrodynamic test system, we renewed their interest in electrodynamic actuation by demonstrating how the MTS Acumen test system could resolve these common user issues.
Q: Why is overall control challenging with electrodynamic actuation?
A: Specimen stiffness can change over the course of dynamic tests which presents a performance challenge for most systems. For stability, specimens must be tuned in the high-stiffness region but that tuning traditionally results in low performance when the specimen reaches the low-stiffness region during the test. This problem was one of the biomedical customer’s main concerns.
We demonstrated the MTS Acumen system’s ability to perform throughout the range by testing a tennis ball because its stiffness changes significantly as it is compressed. We tuned the tennis ball in the higher stiffness region, and ran a cyclic compression test passing through stiffer and softer regions. The MTS Acumen system’s advanced tuning and control techniques provided great performance and stability through the entire stiffness range.
Q: How does the test system’s response to limits affect the user-experience?
A: Electrodynamic actuation is capable of extremely high-performance and high speed, but with that performance and speed comes the possibility of unintentionally breaking specimens or fixtures. In biomedical testing, the complex specimen structure and geometry makes traditional limits inadequate for specimen protection. Unique specimens that may be in limited supply and costly can be damaged or destroyed as a result. Where the specimen and test conditions make specimen protection a challenge, the MTS Acumen system excels.
To demonstrate the MTS Acumen system’s superior response to limits and failure detection, we forced the system into an unstable state to prompt a controlled stop, which leveraged an advanced interlock method developed by MTS. The instant the instability was detected, the system locked in its current position and remained under control, with no freewheeling and essentially no additional load applied to the specimen. Both the equipment and specimen were safe from harm because the machine remained in control.
Q: Describe the auto-tuning shortcomings often associated with electrodynamic systems. How does the MTS Acumen system compare?
A: The customer commented that, in their experience, auto-tuning on other electrodynamic systems had not been flexible nor sophisticated enough to reliably tune and test anything but specimens with very limited variation.
In contrast, the MTS TestSuite™ software used with the MTS Acumen system is designed to measure multiple specimen and system characteristics for auto-tuning purposes, resulting in more appropriate tuning values. We showed the customer how the auto-tuning process incorporates specimen-specific measurements as part of the setup process, facilitating greater accuracy and customization for a specific test. With MTS auto-tuning, the software displays the accuracy of the tuning with an intuitive blue, green and red scale. Adjustments, if desired, can be made with drag and drop simplicity. For the most complex specimens, the MTS Acumen system allows full tuning and adjustment control, so the user can tune specimens that cannot be tested on some other electrodynamic systems.
Q. Why has MTS been so successful at addressing these issues?
A: I believe the exceptional performance of the MTS Acumen system is the result of our advanced product development process that is focused on meeting customer needs. During development, we carefully assessed what users were experiencing in the field with comparable systems, and our engineers dedicated the time and resources necessary to address key issues, always keeping integrated system performance as a goal.
The MTS Acumen system is also a product of MTS’ unmatched controls and technology leadership in servohydraulic and electromechanical actuation. We applied this extensive experience to successfully develop advanced control techniques which are fully integrated into the hardware and software solution. These control techniques take this electrodynamic system design to the next level of performance and accuracy.
Q. What is the takeaway for engineers at other material test labs?
A: They can now leverage all the advantages of electrodynamic actuation without the shortcomings that may have concerned them in the past. With the MTS Acumen system, issues with control, response to limits, auto-tuning and overheating have been effectively addressed and overcome.
What’s more, many of our customers have reported discovering new specimen behaviors due to the high performance of MTS Acumen systems.