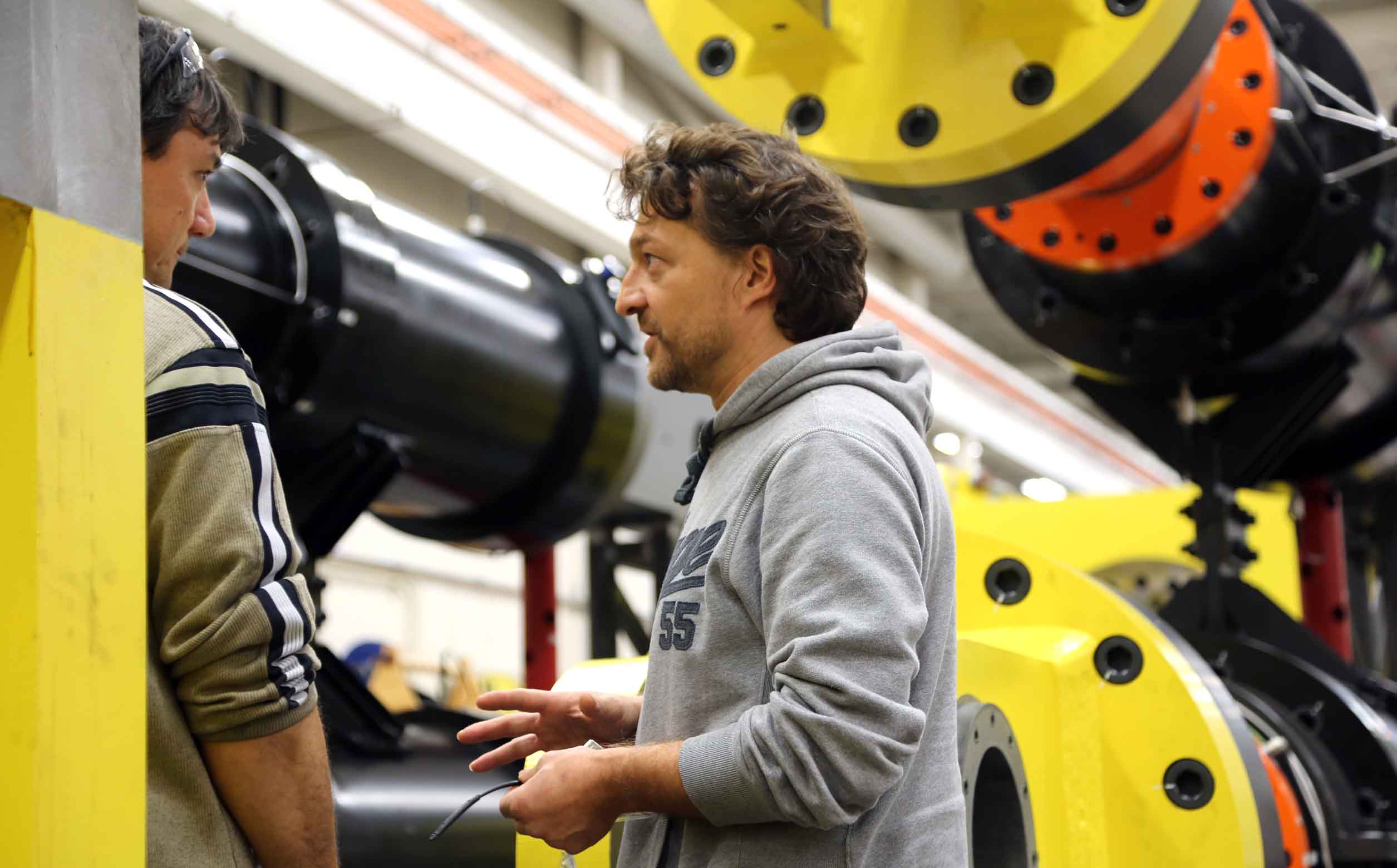
With more than 25 years of experience in materials testing, metallurgy and system engineering, MTS staff scientist Dr. Erik Schwarzkopf brings unique expertise to customer engagements. In this Q&A, he discusses fracture mechanics and fracture toughness tests.
Q: What is fracture toughness testing?
A: In simplest of terms, a fracture toughness test is a non-cyclical test that measures how much energy it takes to grow a crack catastrophically. Various types of tests define “energy” and “catastrophically” differently. Energy can encompass an energy-representative parameter such as a distance parameter like CTOD, or stress intensity parameter like KIc, or energy divided by area parameter like JIc. Catastrophic crack growth can be interpreted as very fast, very far or a little farther than the beginning state. Some common fracture toughness testing standards include ASTM E399, E561, and E1820.
R-Curve ASTM E561 test on a thin steel specimen. The noises created as the crack progresses are due to unstable crack growth, resulting in sudden changes in force or displacement commonly called “pop-ins.”
Q: Which industries care about fracture toughness measurements?
A: Any industry that relies on pressure vessels needs to know the fracture toughness properties of the materials used for those pressurized containers. When something is under pressure, it is important to know how it is going to react over time. It is highly preferable to have a container or pipe leak versus explode, so choosing the right material with the desired properties is critical. That’s why fracture toughness measurements are valuable when selecting materials for piping in power plants, or nuclear and oil & gas applications. In addition to interest from the energy sector, metals and composites manufacturers, and naval, civil engineering and aerospace industries also rely on fracture toughness measurements to assess materials.
Q: How do cracks grow and what does material plasticity have to do with it?
A: Cracks can grow and expend energy in many ways depending on the material’s properties – sometimes a crack makes the material break into two pieces (the creation of each new surface absorbs energy), sometimes the material absorbs energy by deforming, sometimes it transforms (changes from one phase to another). Because of the differing material properties, there are a couple of types of fracture mechanics. For high strength materials, Linear Elastic Fracture Mechanics (LEFM) is commonly used. For more ductile materials there is Elastic Plastic Fracture Mechanics (EPFM). Linear Elastic fracture toughness assumes that plastic deformation is small relative to all other dimensions.
Q: When would you use one fracture toughness test type over another?
A: It depends on the type of data you need and on the material. If you need a qualitative versus quantitative answer, then some of the simplest tests will be able to tell you whether the material is more or less susceptible to cracking. A simple test won’t tell you how much easier it is to crack the material, but the curve of a simple tensile test can tell you something. A Charpy impact test will tell you whether a material can withstand a force and give you pass/fail data. If you need a quantitative measurement, and you can get a valid test from a small specimen, you can try a KIc test, assuming that the material plasticity is minimal.
Q: What if the material plasticity is not minimal?
A: Sometimes conducting a valid KIc test would require a very large (and very expensive) specimen to ensure that most of the specimen is elastic. There is a solution to this problem: with a valid J Integral result, you can calculate the K value, allowing you to use a smaller specimen. Determining the J Integral requires more analysis, but because it is not dependent on the size of the plastic zone, it does not require the large specimen.
Q: What other considerations are there when choosing a fracture toughness test type?
A: As with all testing, consistency is important. Consistent notch type is important. Controlling the temperature, specimen geometry and thickness, and rate of loading are all requirements for a valid test result. Data collected from previous tests is a factor to consider as well. If you have a history of CTOD data, then it makes sense to choose that type of test.
Q: What about testing the fracture toughness of additively manufactured materials?
A: Additively manufactured materials are becoming more common, and they present several areas of concern: porosity, density and particle boundaries. Pores and boundaries in these materials act as cracks or notches, affecting the fatigue and fracture properties of the material. You must determine whether the "pseudo" notches cause cracks to grow catastrophically or not. Composites and additive manufactured materials present unique challenges in that they can have defects between the layers that we cannot see, so they must be tested.
Q: What else does the future hold for fracture toughness measurement?
A: There will continue to be new ways to make materials like 3D printing/additive manufacturing; new materials like engineered composites; new uses for materials in things like hydrogen-fueled vehicles and space travel; and new testing techniques. All this innovation means that materials will need to be evaluated for fracture toughness to determine if they are appropriate for the intended end use. By understanding the principles and methodologies of fracture toughness testing, researchers and engineers can develop safer, more reliable materials and structures to meet the evolving needs of modern technology and industry.