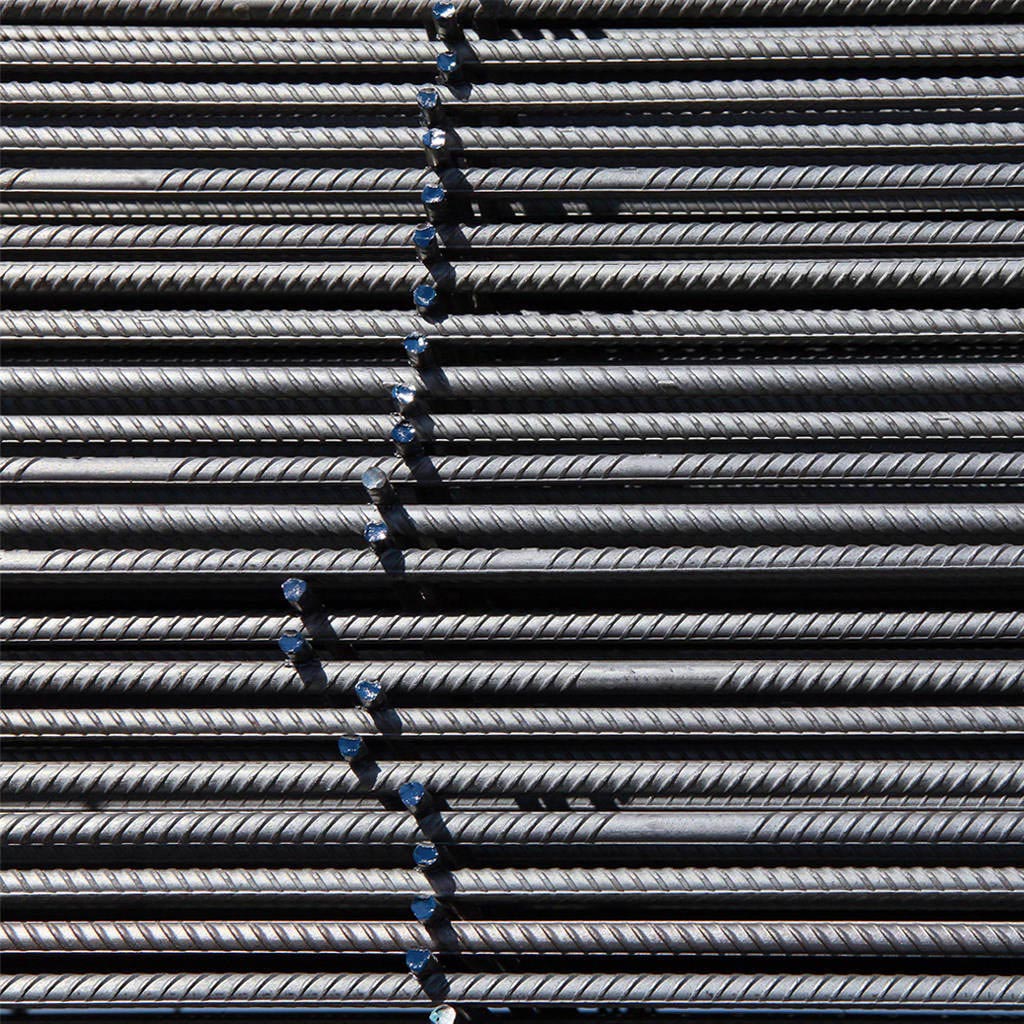
With the growing worldwide demand for new buildings and structures, there has been a corresponding drive for high-quality construction materials. Rebar, or reinforcing bar, is a high-demand material used to improve the tensile strength of concrete in structures. Because rebar and concrete have similar thermal expansion properties, it is the material of choice to reinforce structures. Rebar is often made from ridged carbon steel and comes in various sizes and grades. Today, innovations in materials and coatings are producing higher strength and more versatile rebar options, while posing new challenges for testing.
There are multiple challenges with rebar testing, and well-recognized, exacting standards to meet. One of the biggest concerns with testing rebar is the non-standard shape of the specimens. Rebar is often stored in large coils and then cut to size. So, samples need to be straightened before testing, and they may retain some curvature. The surface of the bar is ridged for better adherence to the concrete, which is good for structural stability, yet from a testing perspective, this uneven surface creates some challenges for gripping the specimen.
Another gripping challenge is created by the coatings that may be used. While coated rebar may offer better protection against corrosion, it is a slippery surface to grip properly. Additionally, some end-use applications require the rebar to be bent to create the necessary structural shapes within the concrete, so it must be tested for bend strength as well. One more concern when testing rebar is the tendency for violent failures that need to be planned for to minimize potential damage to the system and testing personnel.
Rebar is available in various sizes and grades. The grades correspond to minimum yield strength, for example, Grade 280 would have a minimum yield strength of 280 MPa; similarly, Grade 40 would have a minimum yield strength of 40,000 psi. Size is measured in diameter and offered in standard increments. The size and grade of the rebar test specimen will determine the test machine’s required force capacity. Higher grades of rebar are becoming more popular because a smaller amount of higher-strength rebar can be used to create the intended structural stability.
Rebar Grade |
280 |
420 |
520 |
|||||
Yield/Tensile Strength (MPa) |
280 |
500 |
420 |
620 |
520 |
790 |
||
Metric |
Diameter (mm) |
Area (mm2) |
Minimum Yield Force (kN) |
Minimum Tensile Force (kN) |
Minimum Yield Force (kN) |
Minimum Tensile Force (kN) |
Minimum Yield Force (kN) |
Minimum Tensile Force (kN) |
6 |
6 |
28.3 |
7.9 |
14.1 |
11.9 |
17.5 |
14.7 |
22.3 |
8 |
8 |
50.3 |
14.1 |
25.1 |
21.1 |
31.2 |
26.1 |
39.7 |
10 |
10 |
78.5 |
22.0 |
39.3 |
33.0 |
48.7 |
40.8 |
62.0 |
12 |
12 |
113.1 |
31.7 |
56.5 |
47.5 |
70.1 |
58.8 |
89.3 |
14 |
14 |
153.9 |
43.1 |
77.0 |
64.7 |
95.4 |
80.0 |
121.6 |
16 |
16 |
201.1 |
56.3 |
100.5 |
84.4 |
124.7 |
104.6 |
158.8 |
20 |
20 |
314.2 |
88.0 |
157.1 |
131.9 |
194.8 |
163.4 |
248.2 |
25 |
25 |
490.9 |
137.4 |
245.4 |
206.2 |
304.3 |
255.3 |
387.8 |
28 |
28 |
615.8 |
172.4 |
307.9 |
258.6 |
381.8 |
320.2 |
486.4 |
32 |
32 |
804.2 |
225.2 |
402.1 |
337.8 |
498.6 |
418.2 |
635.4 |
40 |
40 |
1256.6 |
351.9 |
628.3 |
527.8 |
779.1 |
653.5 |
992.7 |
50 |
50 |
1963.5 |
549.8 |
981.7 |
824.7 |
1217.4 |
1021.0 |
1551.2 |
Metric reinforcing bar calculations are approximate and intended to guide estimation of the required universal test machine (UTM) capacity.
Rebar Grade |
40 |
60 |
75 |
|||||
Yield/Tensile Strength (ksi) |
40 |
70 |
60 |
90 |
75 |
100 |
||
US/Soft Metric |
Diameter (in) |
Area (in2) |
Minimum Yield Force (kip) |
Minimum Tensile Force (kip) |
Minimum Yield Force (kip) |
Minimum Tensile Force (kip) |
Minimum Yield Force (kip) |
Minimum Tensile Force (kip) |
3 / 10 |
0.375 |
0.110 |
4.4 |
7.7 |
6.6 |
9.9 |
8.3 |
11.0 |
4 / 13 |
0.500 |
0.200 |
8.0 |
14.0 |
12.0 |
18.0 |
15.0 |
20.0 |
5 / 16 |
0.625 |
0.310 |
12.4 |
21.7 |
18.6 |
27.9 |
23.3 |
31.0 |
6 / 19 |
0.750 |
0.440 |
17.6 |
30.8 |
26.4 |
39.6 |
33.0 |
44.0 |
7 / 22 |
0.875 |
0.600 |
24.0 |
42.0 |
36.0 |
54.0 |
45.0 |
60.0 |
8 / 25 |
1.000 |
0.790 |
31.6 |
55.3 |
47.4 |
71.1 |
59.3 |
79.0 |
9 / 29 |
1.128 |
1.000 |
40.0 |
70.0 |
60.0 |
90.0 |
75.0 |
100.0 |
10 / 32 |
1.270 |
1.270 |
50.8 |
88.9 |
76.2 |
114.3 |
95.3 |
127.0 |
11 / 36 |
1.410 |
1.560 |
62.4 |
109.2 |
93.6 |
140.4 |
117.0 |
156.0 |
14 / 43 |
1.693 |
2.250 |
90.0 |
157.5 |
135.0 |
202.5 |
168.8 |
225.0 |
18 / 57 |
2.257 |
4.000 |
160.0 |
280.0 |
240.0 |
360.0 |
300.0 |
400.0 |
US Customary reinforcing bar calculations are approximate and intended to guide estimation of the required universal test machine (UTM) capacity.
MTS offers several options to meet your rebar testing needs. MTS Criterion and Exceed Series 45 Electromechanical Universal Test Systems provide an affordable choice for tensile testing up to 600 kN. For higher force rebar testing, MTS offers the Model 311 series with force capacities of 1.2 MN, 2.5 MN and higher. An MTS Landmark Test System can conduct both static and dynamic tests and can be configured to the highest safety performance levels. Each of these MTS systems can accommodate compression and bend testing as well.
MTS makes it simple to test your rebar samples with software templates for testing to the most common standards, including ASTM A370, ASTM A615, ISO 15630-1, EN 10002-1, ISO 6892-1, ASTM E8M and more. To address specimen slipping challenges, MTS offers a wide variety of grips, specimen interfaces and bend fixtures. And MTS provides both clip-on extensometry that can grip the uneven surface of the specimen without slipping, and video extensometry. MTS can also provide solutions for the testing rebar couplers.
When working with MTS, you benefit from years of testing experience, with specific civil structural expertise. We are familiar with structural testing applications, and depending on the sample size, testing standard and type of test, MTS has a solution to fit your need. With reliable load frames, standardized software templates and accessories designed for this application, MTS provides a complete solution to improve the quality and speed of your rebar testing. Contact your MTS representative today to discuss your optimal configuration.