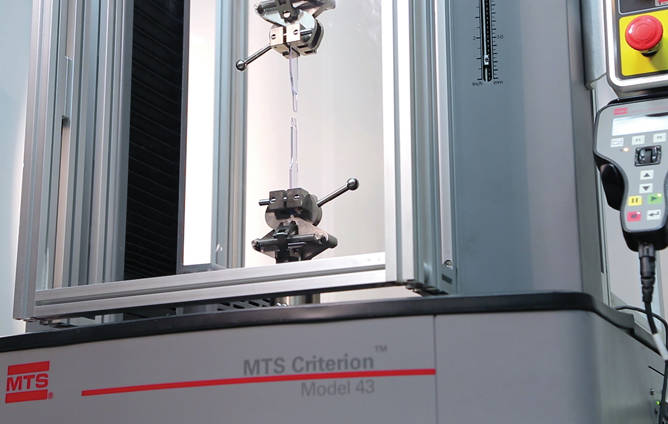
Structural plastics play a vital role across many industries as manufacturers seek to reduce the weight and cost of vehicles, consumer goods and more. MTS application engineers discuss how MTS testing solutions can help manufacturers and compounders meet ISO and ASTM standards for these materials more effectively.
Q: What are some trends shaping the plastics industry?
A: There is tremendous innovation happening right now, especially for the molded structural plastics used in a wide range of machines, vehicles and other products. High-quality lightweight plastics are not only cost-effective for manufacturers to produce, but they can provide an ideal blend of strength and durability. Compounders are constantly developing and adjusting proprietary formulas to deliver specific attributes for a particular application and each of these materials requires tensile testing.
Q: Which standards govern tensile testing for plastics?
A: Two of the more common standards are ISO 527 and ASTM D638. ISO 527 covers general principles for determining tensile properties of all kinds of plastics and has extensions that focus on extrusion plastics, films and sheets, and fiber-reinforced plastic composites. ASTM D638 offers similar guidelines for producing tensile property data for all kinds of plastics. Recently, our customers’ focus has been on standards for tensile testing of molding and extrusion plastics: ISO 527-2 and ASTM D638.
Q: What is the difference between the ISO 527-2 and ASTM D638 standards?
A: They are very similar with the exception of the analysis of the non-linear portion of a material’s stress-strain curve. For most plastics, the test results for each of these two standards will be the same. But for plastics with little or no linear region, the variation between ASTM and ISO can be significant.
Q: Why is tensile testing important?
A: Tensile testing is the most popular test for plastics because it yields so much critical data. It’s the foundation of any investigation of material properties such as stress, strain, tensile modulus and Poisson’s ratio. By measuring the force required to pull a test specimen to its breaking point, product design engineers and quality managers can accurately predict the performance of products in real-world applications. They can understand how moldable the material is, how much energy it may absorb and whether it can be used in a specific application. These tests may also need to be performed in environmental chambers to simulate conditions of use.
Q: What does tensile testing for structural plastics involve?
A: To perform these tests, flat “dogbone” style specimens are placed in the grips of a universal testing machine and subjected to controlled extension until they fail. Test speeds vary by specimen type to achieve a specific strain rate, and often an extensometer is used to measure the strain of the specimen in the area of interest. This can be complicated when tests are performed in temperature chambers where an extensometer may be damaged.
Q: What are the challenges of tensile testing for plastics?
A: The challenge is determining exactly how the material in question fails. How far the plastic stretches until it fails depends on the strain hardening coefficient and whether the material is strain-rate sensitive. As I mentioned when differentiating the standards, the focus is often the modulus, or the linear elastic portion of the test, which is a small part of the pull. Differentiating the modulus from the overall strain can be difficult where the overall elongation can vary from 100 to 1,000 percent of strain. You need a lot of data points.
Originally, mechanical extensometers were used, but they only travel 50 to 100 percent, depending on the gage length. High-elongation extensometers can travel farther but they don’t have enough resolution to capture the relatively small linear elastic region. In many cases the best solution is a non-contact extensometer, such as our MTS Advantage™ Video Extensometer (AVX). This particular tool lets you follow the entire specimen through failure without affecting it while getting enough data points for calculating the modulus.
Q: What capabilities are important to consider in a tensile test system?
A: For structural or rigid plastics, you need a test system with the capacity and resolution to perform high-elongation tests. Sometimes this can mean a force capability up to 50 kN. It is often important to test inside an environmental chamber. Testing at temperature can add a whole range of challenges. As an example, you may have to soak the specimens in the grips at a given temperature, or soak them in the chamber then stabilize them in the grips, which complicates setup and extends test time. Having an integrated package can simplify the logistics. Issues to consider include choosing a system that has enough height to accommodate the chamber and the expected specimen elongation, and a chamber with optical-grade glass for non-contact strain measurements.
Q: What does the data help compounders and manufacturers accomplish?
A: It really comes down to confidence in decisions. Compounders need to know that their material will perform as expected in the manufacturing process and deliver the specific characteristics the molder needs, whether that is durability or flexibility or strength-to-weight ratio. Manufacturers are selecting materials based on all of the nuances of the product they are designing, whether it’s part of a toy, or the headrest in a car, or part of an airplane seat. They want the right material characteristics so they can make dozens of design decisions. Accurate test data helps them do that.
Q: What else does MTS offer to help ensure accurate test results?
A: MTS has decades of experience configuring integrated system solutions for the plastics industry. The MTS Criterion® Electromechanical Test Systems are ideal for tensile testing of plastics per ISO 527-2 and ASTM D638. Available in numerous, high-stiffness configurations, these frames feature high-resolution MTS digital controls and compact AC servomotor drives to provide high-speed, low vibration testing across a very broad range of force capacities.