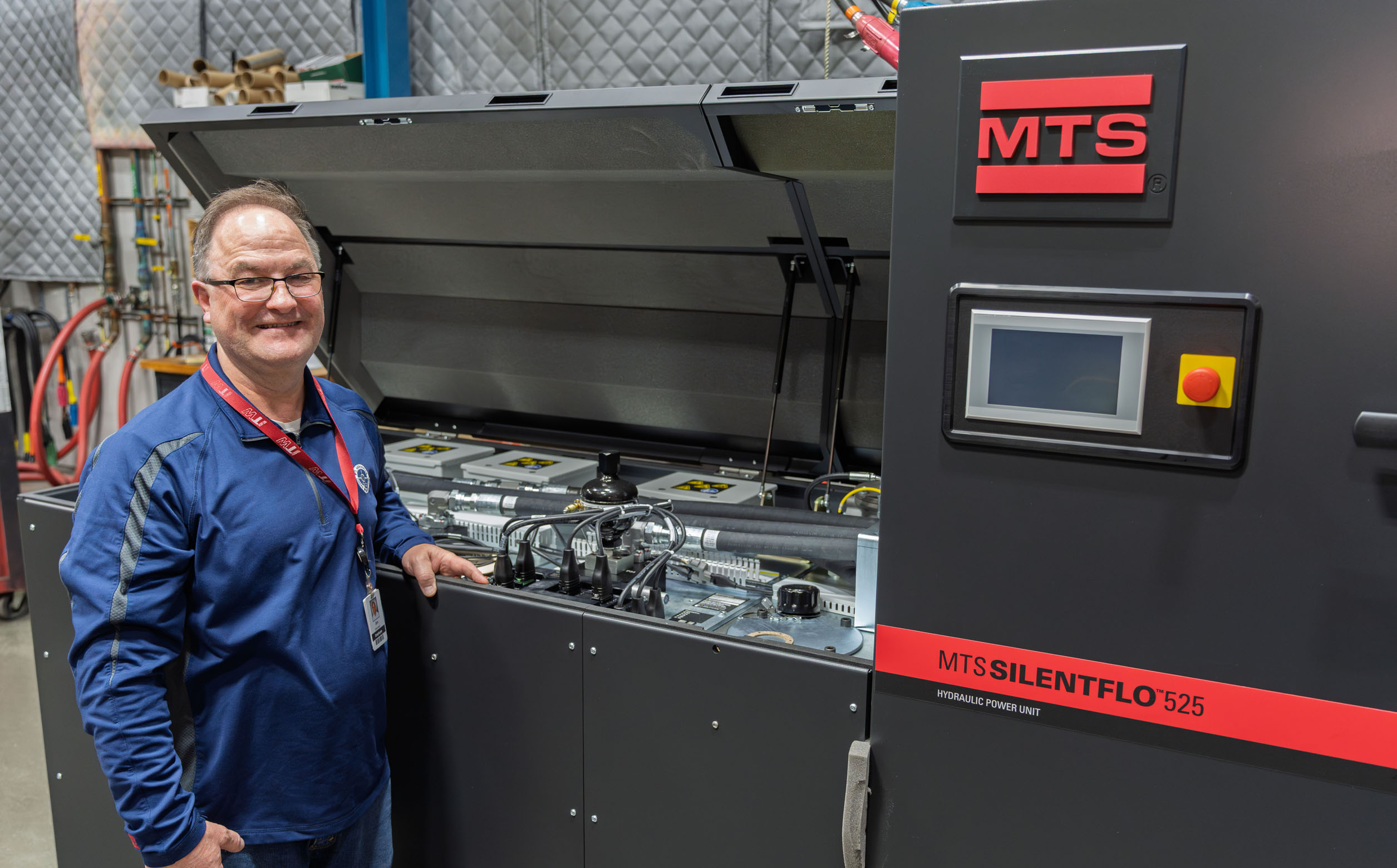
Jim Hennen, Sr. Product Development Manager, discusses hybrid HPU technology and how to maximize its benefits.
Q: Why has MTS pioneered a new, hybrid approach to hydraulic power generation?
A: With patented hybrid technology, the new MTS SilentFlo™ 525 Hydraulic Power Unit (HPU) can reduce energy use by 35% or more compared to older HPUs. This significant energy savings lowers costs and helps labs meet decarbonization goals.
Q: What is the data supporting hybrid HPU energy efficiency claims?
A: MTS conducted an exhaustive 10-year technical study of Digital Displacement® Pump (DDP) technologies. We built and commissioned several pilot hybrid HPUs within our own facility where we use the MTS SilentFlo HPU in the same manner as our customers do. We found that with proper control methods, algorithms, and design configurations, the hybrid HPU managed the on/off stages of the modules to their maximum efficiency while minimizing the inefficiencies of idle modes.
We performed an energy efficiency study using MTS Model 329 Road Simulators running a specific repeating drive file. The rig was first powered by an HPU using only swash plate pumps. The test was repeated powered by a different HPU using only DDP. The DDP HPU consistently required 37.5% less electrical energy to produce the same flow demand.
Over a calendar year of plant operations, the daily energy efficiency of each HPU was measured and plotted as a function of total flow per day per electrical KWs consumed. The data showed that the DDP HPU was more efficient by greater than 35% over the full year of highly variable and random flow demands. This analysis did not consider the additional savings in reduced cooling costs. An independent energy audit by the local utility company resulted in a substantial energy rebate.
Q: What factors should be considered to determine the mix of DDP and swash plate modules?
A: It depends on whether you want the minimum ratio (DDP to swash) to provide an idle mode benefit or the optimal ratio to maximize the benefit across system operations from idle to full power demand.
Q: What is the minimum number of DDP modules needed?
A: Having at least two DDP modules within the hydraulic power system allows it to manage idle flows up to 60GPM and to balance the wear hours across the two DDPs. For the optimal setup, we need to consider how much flow is needed to respond to Step Flow demands such that swash modules can be effectively turned on and off and not impede the demands of the test rigs consuming the flow. The rule of thumb here is to have at least two DDP per 6-bay HPU. The reason is simple. The buffer for effective Run-On-Demand module scheduling is typically 1/3 of the total flow capacity. So, 1/3 of the modules should be DDP as a starting point. Of course, the more DDP modules you can employ, the more efficient the overall system becomes.
Q: How do you maximize the efficiency of a hybrid HPU?
A: Set the swash plate pump modules to a slightly higher target pressure, and only turn them on when capacity needs exceed what the available DDP modules can deliver. This setup drives swash modules to their full displacement where they are most efficient. In this case, swash modules are either off or travelling toward full displacement when running. Total module efficiency is primarily the average of the as-running modules efficiencies, ignoring all off-state modules in the hydraulic power system.
Digital Displacement is a registered trademark of Danfoss A/S