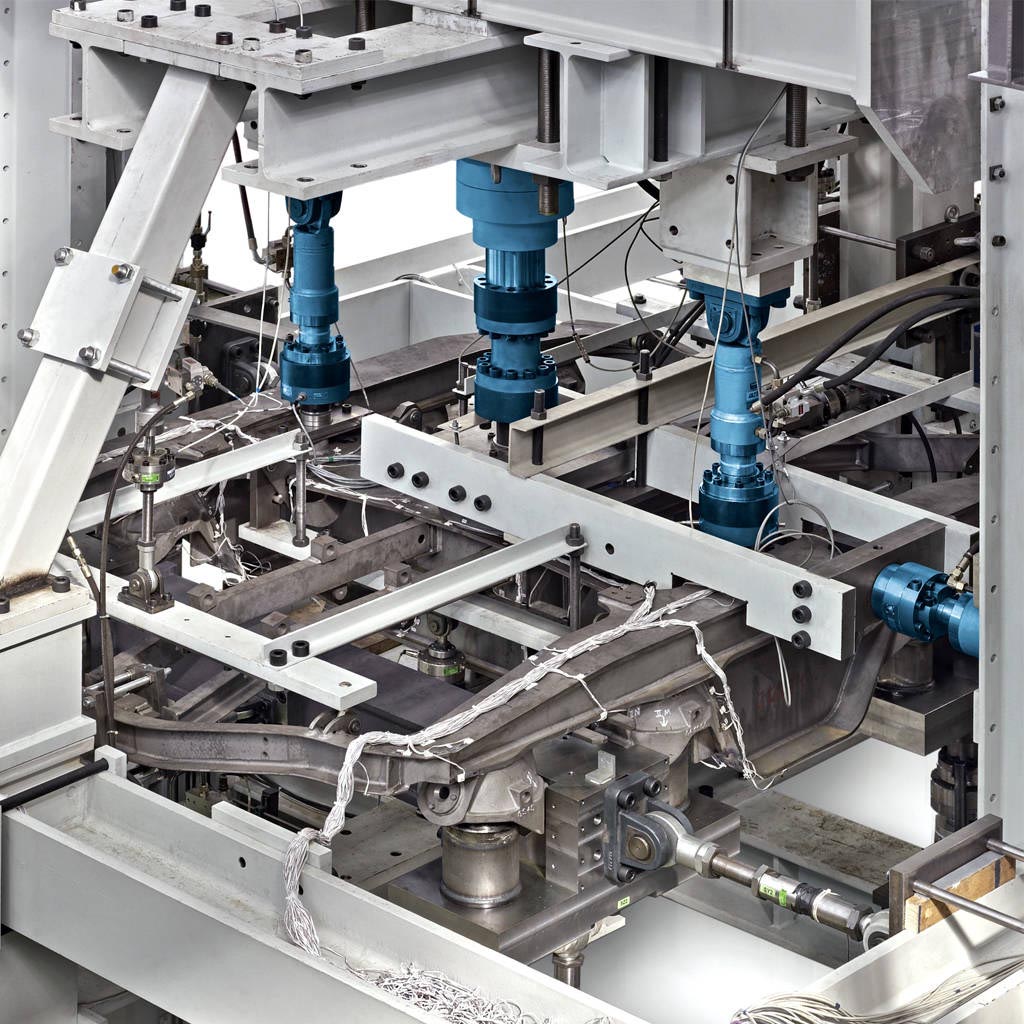
CUSTOMER CHALLENGE
IMA GmbH Dresden is a leading German contract test lab that specializes in strength and fatigue behavior analysis. The company provides a comprehensive portfolio of engineering services for its customers, including research and investigation, development and calculation, testing and certification. For its testing services, the company serves a remarkably diverse range of industries and applications — from biomedical devices such as spinal disc prosthetics to building and construction materials to components and structures used in aerospace, automotive and rail.
As a contract test lab, IMA works hard to meet an equally diverse range of customer needs as quickly and efficiently as possible. To stay competitive — and help its customers shorten time to market — IMA must frequently test new structures and materials in new ways, often with very tight turnaround times. Of course, it must achieve these goals cost-effectively. In other words, productivity is essential.
This pressure is especially intense in the rail industry, where market demands for faster trains, higher payloads and greater fuel efficiency are rising. Rail test engineers must measure, simulate and evaluate increasingly complex designs, according to more aggressive schedules, and with greater budgetary constraints.
Eckhard Hofmann, Head of Railway Test at IMA, knows this reality well. “We are a very busy lab. After we finish one rail testing project, we need to use the same control system for a different application almost immediately in order to stay as productive as possible,” Hofmann said. “The main challenge is finding testing systems that are flexible enough to handle an eight-channel test one day and a twenty-channel test the next day without too much adjustment. From this perspective, MTS is an ideal testing partner.”
MTS SOLUTION
Because flexibility is so critical to IMA’s testing schedule, it is no surprise that the solution they are now using to capitalize on opportunities in the burgeoning rail market was originally specified for a different industry.
The solution features multiple controller hardware platforms — including the legacy MTS Aero-90, the Aero ST™ (Model 493), and the FlexTest® 200 (Model 494) — which are some of the most widely installed control systems in aerospace structural testing. These systems offer ample channel counts for the full spectrum of rail testing with up to 512 closed-loop servocontrol channels. Controlling these versatile test rigs is MTS AeroPro™ Software, which efficiently manages the controller hardware and data acquisition hardware with a single interface. AeroPro software supports a large number of channels and offers an array of live data and post-test data visualization capabilities.
Overall, the MTS solution delivers the day-to-day adaptability IMA needs to configure new testing setups with speed and ease. Currently, the lab uses the solution to test rail car bogies and chassis as well as smaller components such as rods and bearings.
“When the global rail market became very active, the MTS solution made it easy for us to capture this business,” Hoffman said. “We use eight bogie test rigs, six of which incorporate the MTS hardware and software. We reconfigure them again and again, depending on what our rail customers need.”
Although other testing systems can be modified, they are often designed to serve a specific testing purpose. Figuring out how to change the hardware and software to perform a new type of test or accommodate a different size specimen quickly becomes too costly and time-consuming.
“That is the real advantage of the MTS solution — the total flexibility,” Hoffman said. “It is very easy for our test engineers to configure and reconfigure the solution. It fulfills all of our railway testing requirements.”
CUSTOMER BENEFITS
Today, IMA provides bogie, chassis and other tests for virtually all European railway manufacturers, including Bombardier, Siemens Mobility and the Stadler Rail Group, as well as a variety of other rail manufacturers worldwide. In retrospect, the MTS solution gave the lab a distinct competitive advantage.
“Recently, there has been a very strong push toward fast-paced innovation in the global railway industry,” Hoffman said. “Large urban centers need to transport larger and larger populations of passengers, as well as export higher volumes of freight, all while optimizing speed and energy efficiency. This significantly affects how rail cars are designed. The faster our customers can test new structures and components, the faster they can get these innovations to market. It has been critical for IMA to perform many different kinds of rail tests with quick, cost-effective reconfiguration.”
The familiarity of the controls is another important advantage. Test engineers at IMA can move from one test rig to the next almost effortlessly, because they already understand how to manipulate the controls, how to set up different tests and how the entire interface operates. Again, this improves productivity because it reduces the need for training.
Outside the lab, MTS also helps IMA as they follow up on new business opportunities in the rail market. Specifically, MTS can draw on a rich heritage of testing expertise to help IMA meet the needs of customers with complex testing requirements.
“The service we receive from MTS is excellent,” Hoffman said. “When we are pursuing new business, MTS provides the consultative advice we need to create proposals that align with the customer’s needs, and that are both technically sound and economically viable.”
Knowledgeable service from MTS provides an additional layer of support, ensuring that IMA can maximize the uptime of its testing solution.
“The assistance MTS provides is critical to the productivity of our lab,” Hoffman said. “With MTS, we can be confident we will get our questions answered quickly, and that any issues will be resolved responsively. We are very well supported by MTS.”