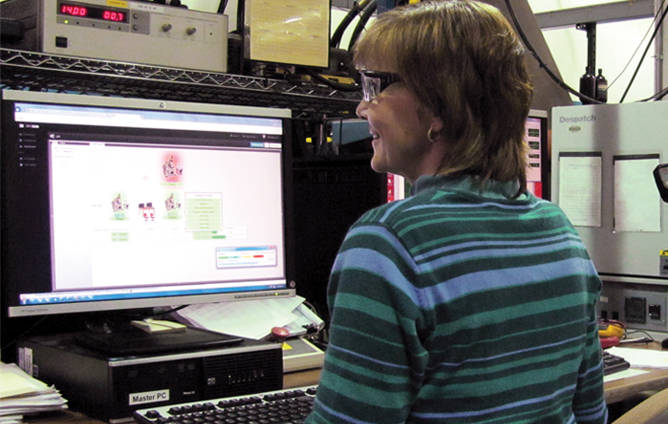
CUSTOMER CHALLENGE
BWI Group is a leading global manufacturer of vehicle brake and suspension systems. Every new component in development must complete a series of mechanical tests during validation, including fatigue or “life” testing. A life test subjects a prototype to the simulated real-world loads and moments under which it must ultimately perform over its functional life – for example, over a period of 100,000 miles when used in a passenger car.
The BWI Validation and Test Development group often develops new test fixtures, methods and equipment to meet customers’ requirements and specifications. Due to this innovation in test development, close monitoring is necessary to conduct meaningful life tests. “Monitoring and maintaining specimen temperature and test inputs are vital to ensuring a repeatable test that produces dependable results,” said Michael Rutkowski, Validation and Test Engineer for Suspensions at BWI Group. “Monitoring specimen attributes throughout the test is also very important for determining reliability of the product.”
Since speed-to-market is also vital to the success of every new vehicle component, test labs face immense pressure to uphold the highest levels of uptime. This reality prompted the BWI Group test team to pursue a way of knowing instantly and remotely if a life test required attention at any time and for any reason.
“For our high-profile tests, we developed a remote monitoring method that was basically an answering machine in reverse,” said Rutkowski. “A phone dialer converted a digital control signal to a preprogrammed audio message that was sent to a technician on call. It said, ‘Something needs attention with your test,’ but supplied no further detail. The severity of the issue wasn’t clear, so a trip into the lab was required.”
MTS SOLUTION
Rutkowski and his team have used MTS technology, products and personnel to enhance lab operations for several years. They were among the first to learn about the MTS Echo® Intelligent Lab, an innovation that leverages digital communications technology to help test labs function in a more integrated, automated and unified fashion.
BWI Group was clearly intrigued by the idea of remote monitoring already, so Rutkowski and his team began to use MTS Echo Intelligent Lab Equipment Monitoring for their powertrain mounts life testing. The equipment monitoring module allows lab personnel to view detailed, real-time test system status messages from any web-enabled device, at any time. Alerts can also be set up to notify any individual with security access the instant a test requires attention or reaches a defined state.
As a result of their positive experiences with this module, they are now keenly interested in expanding their monitoring capability through other Intelligent Lab modules such as proactive system health monitoring, customer test status tracking and software version management.
In addition to taking advantage of the MTS Echo technology, Rutkowski and his team have been satisfied with MTS products, saying “Their systems are scalable, reliable and meet our high performance requirements.” The BWI Validation and Test Development group has been particularly pleased with the performance of the MTS controller. “The FlexTest™ line of MTS controllers has simplified and synergized our testing methods. All aspects of the damper life test can now be controlled through the FlexTest; from ECU control, to specimen temperature control, to off-axis loading control, and beyond,” said Rutkowski.
CUSTOMER BENEFITS
Today, with MTS Echo Equipment Monitoring, BWI Group can easily tell which systems are running, idle or scheduled for downtime, helping them maximize equipment productivity. In addition to monitoring powertrain mount testing, they now also remotely monitor suspension damper life testing, and plan to expand this capability to all life testing across the test lab.
“The ability to check on a test from your smartphone may sound trivial at first, but we’ve found the peace of mind and ability to reduce downtime to be beyond measure,” Rutkowski said. “We’ve grown to appreciate having on-demand access to test progress without having to be in the lab or even the building. It is hard to imagine doing things the old way.”
Rutkowski and his team appreciate the ways MTS has worked with them to achieve their business goals. “There are many people who have been working here with MTS for at least 20 years, and there is a feeling of family between people from our two companies; a feeling of common, vested interest,” Rutkowski said. “From its field service techs to sales and support, we know that MTS has our back. That kind of relationship is special, particularly in business.”