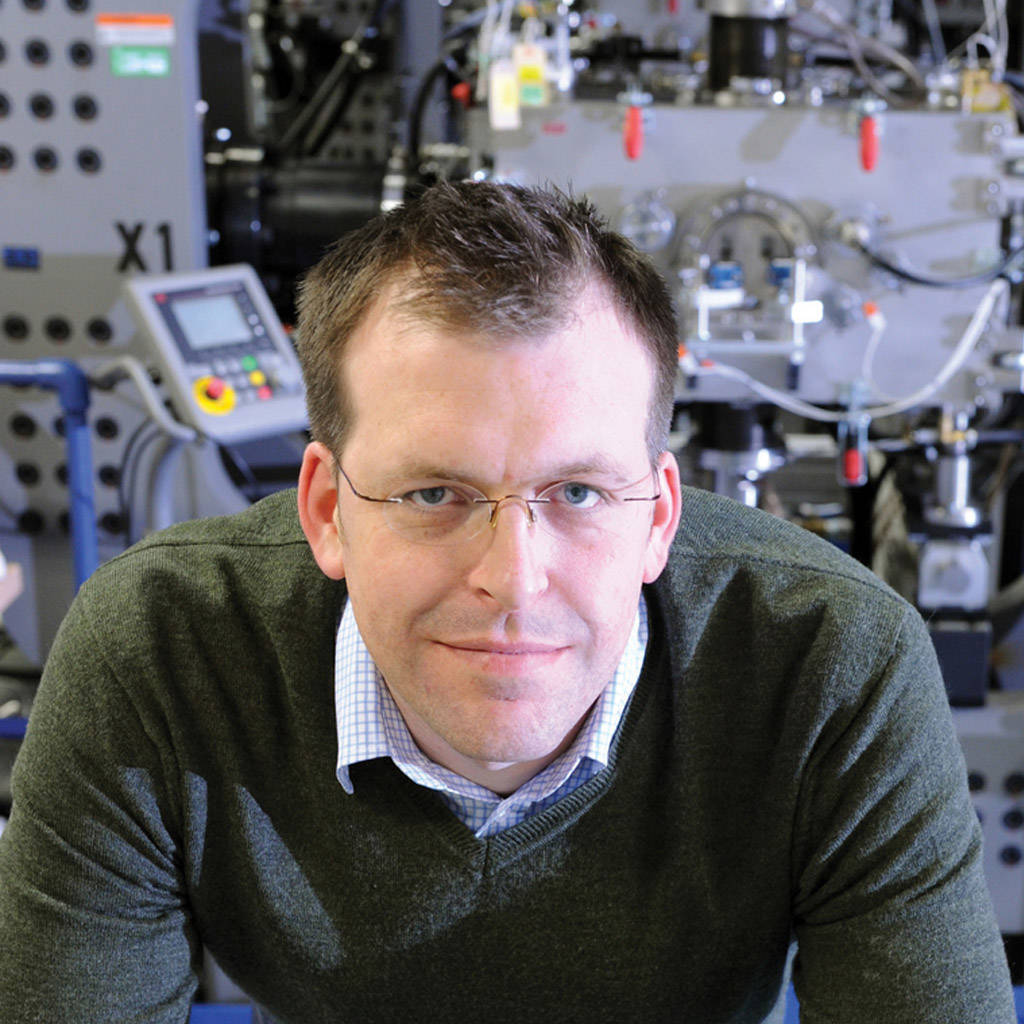
CUSTOMER CHALLENGE
Aerospace manufacturers constantly strive to find new ways to improve efficiency and longevity of their aircraft designs. Even modest improvements in engine fuel-efficiency and reliability can save millions over time.
Rolls-Royce continues to lead the development of cleaner, more fuel-efficient and more durable jet engines. To reach such exceptional performance, each material and component incorporated into an engine design has to operate reliably at higher temperatures over a longer service life.
From a product development perspective, validating this performance requires subjecting jet engine materials and components to the complex loads present during takeoff, flight and landing, while also simulating the extreme temperatures required for engines to run at higher temperatures and consequently improve fuel and emissions performance.
“We knew that raising the standard for gas turbine engine performance would require equivalent advances in our testing technology,” said Barry Ward, Materials Testing Team Leader for Rolls-Royce. “Specifically, we would have to accurately simulate extreme real-world jet engine operating environments in our test lab, accompanied by advanced data correlation capabilities to gain meaningful insight.
“We needed especially robust solutions for high-temperature testing and simulation,” Ward said. “Since we were intending to build a new testing facility, we also needed suppliers who had good facilities planning expertise.”
MTS believes it was chosen to help enhance the gas turbine material and component test capabilities of Rolls-Royce, based on technology leadership, system integration expertise and superior reputation for service and support.
MTS SOLUTION
In September 2009, MTS helped Rolls-Royce specify a variety of advanced hardware, software and accessories optimized for high-temperature material and component testing. Technology chosen included MTS Landmark™ servohydraulic test systems for uniaxial thermomechanical fatigue (TMF), high-temperature low-cycle fatigue (LCF), fracture mechanics and tensile testing. The systems included grips, high-temperature extensometers and environmental simulation systems.
Rolls-Royce also ordered the MTS Planar Biaxial Test System, which provides precise multiaxial force and torque control of test specimens in high-stress, elevated-temperature vacuum environments that closely resemble actual jet engine operating conditions.
The MTS tests systems are powered by versatile FlexTest® digital controls and clean, quiet SilentFlo™ hydraulic power units. MTS TestSuite™ application software was selected for its ability to simplify and standardize test development, execution and reporting, helping to facilitate the efficient sharing and analysis of test results across Rolls-Royce mechanical testing operations.
The MTS test solutions were deployed in the new, state-of-the-art Rolls-Royce Mechanical Test Operations Centre (MTOC) in Dahlewitz, Germany, which opened in May 2010. “The unique thing about the MTOC facility is that it is designed from the ground up for testing, whereas the majority of the world’s other test facilities have evolved from an earlier generation of facilities,” said Ward.
Prior to and during the MTOC facility’s construction, MTS engineers worked closely with building architects, the Rolls-Royce information technology department and third-party vendors to plan for hydraulic power distribution, computer networking, test system integration and other crucial details. “We needed suppliers who could work to understand our needs beforehand and help determine what possibilities there were for making this a smart working environment,” said Ward.
MTS also assisted in the move of six MTS material test systems and four planar biaxial systems from the old testing facility to MTOC. “This was an extremely complex installation, and we relied heavily on MTS expertise to help us get everything running smoothly,” Ward said. “Our suppliers need to help us find the best technical solution.”
CUSTOMER BENEFITS
Ward says that with its advanced testing capabilities and state-of-the-art MTOC facility, Rolls-Royce is well equipped to support the improvement of the fuel performance and service life of gas turbine materials and components — ultimately resulting in the introduction of cleaner, more energy-efficient and more durable jet engines.
“We have not only achieved great strides in testing capability, but in productivity as well,” Ward said. “All our technicians have found software easy to learn and use, which has helped us to work more efficiently. Our in-house thermomechanical fatigue test experts are especially impressed with the simplicity of the software’s TMF module.” MTS and Rolls-Royce have worked cooperatively to develop software solutions for Rolls-Royce’s TMF testing applications.
Rolls-Royce test engineers have found the new hardware to be equally versatile, which is helping MTOC to make the best use of its resources. “In our old facility, we had specific machines for specific types of tests. We can now configure a machine for a certain type of test one month, and then easily reconfigure it to support a different test the next. You will never see one system constantly running at capacity here while the one next to it stands idle.”
The versatility of MTS testing solutions also allows Rolls-Royce to easily respond to the many unknowns that are common to advanced materials and component research. “We do a lot of research that requires nonstandard tests, and versatility and reconfigurability are needed to support all of it.
“Rolls-Royce is well prepared to address both the near- and long-term needs of the aerospace industry,” Ward said. “While we currently have the ideal setup for developing the next generation of gas turbine materials and components, we are also agile enough to satisfy any new test requirements that arise well into the future.”