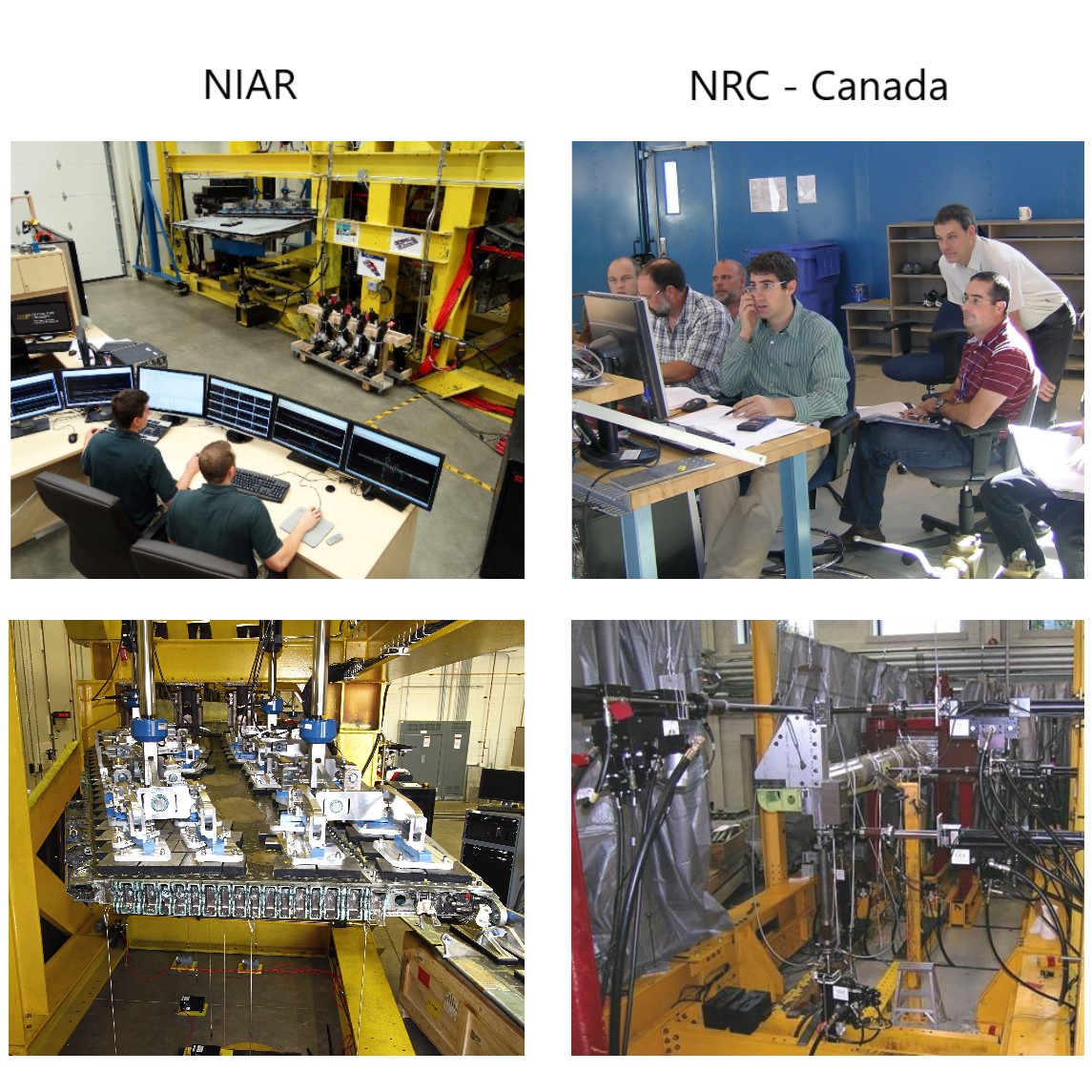
Full-scale structural test rigs that feature highly cross-coupled actuation schemes present unique challenges for aerospace test engineers. In these complex configurations, multiple actuators exert different forces on the same portion of a test article simultaneously, raising the potential for errors that can jeopardize test schedules and delay development programs.
One tool for reducing such errors - thus improving test speed and efficiency - is C3 Performance, a utility of MTS AeroPro™ Control and Data Acquisition Software. Also known as C-cubed, C3 Performance enables test teams to manage highly cross-coupled actuation schemes effectively, without having to build extra time into test schedules to resolve numerous, recurring stops and interlocks.
The C3 Performance cross-coupling compensation technique was co-developed by experts from the National Research Council of Canada (NRC) and MTS Systems Corporation. Today, it is a standard part of the testing protocol at NRC – Canada’s full-scale structural test lab, where Andre Beltempo works as a structural test engineer.
“Typically, we use C-cubed on all tests,” said Beltempo. “With full-scale fatigue tests, you see very complex actuator interaction. That’s exactly why we need it.”
Beltempo’s team recently used C3 Performance during a technology demonstration for a major helicopter manufacturer. The fatigue and static test program focused on a composite tail boom, fabricated using advanced manufacturing techniques. The tests were identical to those that would be used to certify the part for safe life tolerance FAA requirements.
“If you look at the tail rotor gear box interface fitting, the two rear actuators are both loading on the same fitting,” Beltempo said. “Cross-coupling compensation helps minimize the fighting [between actutators].”
The test involved six actuators and four million end points, running overnight for approximately 125 days, with an average frequency of 0.5 Hz. This test speed would have been impossible without C3 Performance, according to Beltempo.
“We could not have done it as quickly without cross-coupling compensation,” he said. “For an overnight test, we would have had to run the end levels at half the speed to not have to worry about unattended shutdowns. Our standard approach for any fatigue test is to tune the test, apply C-cubed, and tune it again right away. I’ve never seen a speed increase of less than a factor of two for a rigid article.”
Another aspect that Beltempo appreciates about C3 Performance is its overall ease of use. Because test operators can set it up on their own, C3 Performance helps labs gain even more time.
“The fact that it’s so hands-free gives me the ability to focus on more important tasks,” Beltempo said. “If you had to sit there and figure out all the coefficients on your own, it would be different. But you just click a button and it happens. It’s a real productivity improvement.”
While it is natural for the organization that helped develop C3 Performance to apply it to every fatigue test as a matter of protocol, other labs are also discovering the problem-solving potential of this powerful utility.
For Dr. Waruna Seneviratne, a technical director in the Composites and Advanced Materials lab at Wichita State University’s National Institute for Aviation Research (NIAR), the problem was sleep deprivation.
“We were running a fatigue test with a very distinctive combination of custom fixturing and actuation, and we had a very aggressive test schedule,” Seneviratne said. “The test ran overnight and we were experiencing a large number of nuisance error limit triggers. Our team had to come down to the lab in the middle of the night to see what was causing test shutdowns and to restart the test. We were falling behind.”
The test focused on evaluating the fatigue life of composite structures of F/A-18 Hornet aircraft, many of which are approaching retirement. Because the aircraft’s replacement will not be ready until 2019, the U.S. Navy needs to safely prolong the service life of the aircraft’s aging composite structures.
Seneviratne’s research successfully determined that the composite-to-titanium bonded joints at the wing root had a great deal of life left in them. The new test expanded the study to include the entire inner wing, which has a composite skin. The test article includes the inner wing, trailing-edge flap and center barrel as well as simulated leading-edge flap and outer wing. NIAR’s research team had to construct an elaborate high-strength steel rig with custom-designed fixturing and apply significant loads to recreate aggressive maneuvers.
“There were significant differences between stroke and loads across the actuators, which was a likely source of the errors,” he said. “We needed a way to minimize the false shutdowns, so we started looking into it.”
Research engineer Travis Cravens, a member of Seneviratne’s team, handled the setup and configuration of C3 Performance. System and application engineers from MTS completed the installation and training in less than a day, and the lab saw results almost immediately.
“We were running 20 percent faster by the end of the first day with no mechanical modifications to the test rig,” Cravens said. “C3 Performance was very easy to learn and set up; it all occurs within the software. You simply create a cross-coupling matrix by applying a unit load on each load channel, which represents just one extra step for each actuator.”
To streamline test setup, C3 Performance eliminates the time-intensive task of manually inputting cross-coupling data by employing unit load cases to generate automated cross-coupling compensation coefficients. Seneviratne characterized this process with an apt analogy.
“It’s like having a team of 20 people who don’t know each other working on the same project,” he said. “The unit loads are simply a way of introducing all those people to each other so they can collaborate and work more efficiently.”
With some extra tuning, Seneviratne and Cravens were able to increase the test rate by 24 percent and cut the number of stops significantly.
“It has greatly improved the performance of our test,” Cravens said. “With the improved load tracking, small perturbations in feedback are much less likely to trigger error limits, resulting in fewer test stoppages. The reduction in error has also allowed us to run more segments per hour.”
Before using C3 Performance, NIAR was only able to achieve a maximum of 375 segments per hour, with an average of 97 stops and 55 interlocks per test block. With C3 Performance, this has improved to 480 segments per hour with an average of 51 stops and 15 interlocks.
“The number of stops was a third of what they were, which was a huge gain for us,” Seneviratne said. “That allowed us to run the test overnight, some nights without a single interruption. That’s up to 10 hours of testing we didn’t have before, which helped tremendously with our schedule.”
C3 Performance saved weeks, enabling Seneviratne’s team to provide the test results on time. In addition, lab productivity was enhanced: the team was able to operate on a more predictable schedule and had more time to devote to other projects. In any lab with finite resources, that is an important advantage.
“Knowing that we could run the test overnight and be confident we could do inspection and repair during the day allowed us to increase the efficiency of our test path,” Seneviratne said. “We were able to plan better and coordinate our activities knowing that the test ran overnight unattended with minimal interruptions.”
One tool for reducing such errors - thus improving test speed and efficiency - is C3 Performance, a utility of MTS AeroPro™ Control and Data Acquisition Software. Also known as C-cubed, C3 Performance enables test teams to manage highly cross-coupled actuation schemes effectively, without having to build extra time into test schedules to resolve numerous, recurring stops and interlocks.
The C3 Performance cross-coupling compensation technique was co-developed by experts from the National Research Council of Canada (NRC) and MTS Systems Corporation. Today, it is a standard part of the testing protocol at NRC – Canada’s full-scale structural test lab, where Andre Beltempo works as a structural test engineer.
“Typically, we use C-cubed on all tests,” said Beltempo. “With full-scale fatigue tests, you see very complex actuator interaction. That’s exactly why we need it.”
Beltempo’s team recently used C3 Performance during a technology demonstration for a major helicopter manufacturer. The fatigue and static test program focused on a composite tail boom, fabricated using advanced manufacturing techniques. The tests were identical to those that would be used to certify the part for safe life tolerance FAA requirements.
“If you look at the tail rotor gear box interface fitting, the two rear actuators are both loading on the same fitting,” Beltempo said. “Cross-coupling compensation helps minimize the fighting [between actutators].”
The test involved six actuators and four million end points, running overnight for approximately 125 days, with an average frequency of 0.5 Hz. This test speed would have been impossible without C3 Performance, according to Beltempo.
“We could not have done it as quickly without cross-coupling compensation,” he said. “For an overnight test, we would have had to run the end levels at half the speed to not have to worry about unattended shutdowns. Our standard approach for any fatigue test is to tune the test, apply C-cubed, and tune it again right away. I’ve never seen a speed increase of less than a factor of two for a rigid article.”
Another aspect that Beltempo appreciates about C3 Performance is its overall ease of use. Because test operators can set it up on their own, C3 Performance helps labs gain even more time.
“The fact that it’s so hands-free gives me the ability to focus on more important tasks,” Beltempo said. “If you had to sit there and figure out all the coefficients on your own, it would be different. But you just click a button and it happens. It’s a real productivity improvement.”
While it is natural for the organization that helped develop C3 Performance to apply it to every fatigue test as a matter of protocol, other labs are also discovering the problem-solving potential of this powerful utility.
For Dr. Waruna Seneviratne, a technical director in the Composites and Advanced Materials lab at Wichita State University’s National Institute for Aviation Research (NIAR), the problem was sleep deprivation.
“We were running a fatigue test with a very distinctive combination of custom fixturing and actuation, and we had a very aggressive test schedule,” Seneviratne said. “The test ran overnight and we were experiencing a large number of nuisance error limit triggers. Our team had to come down to the lab in the middle of the night to see what was causing test shutdowns and to restart the test. We were falling behind.”
The test focused on evaluating the fatigue life of composite structures of F/A-18 Hornet aircraft, many of which are approaching retirement. Because the aircraft’s replacement will not be ready until 2019, the U.S. Navy needs to safely prolong the service life of the aircraft’s aging composite structures.
Seneviratne’s research successfully determined that the composite-to-titanium bonded joints at the wing root had a great deal of life left in them. The new test expanded the study to include the entire inner wing, which has a composite skin. The test article includes the inner wing, trailing-edge flap and center barrel as well as simulated leading-edge flap and outer wing. NIAR’s research team had to construct an elaborate high-strength steel rig with custom-designed fixturing and apply significant loads to recreate aggressive maneuvers.
“There were significant differences between stroke and loads across the actuators, which was a likely source of the errors,” he said. “We needed a way to minimize the false shutdowns, so we started looking into it.”
Research engineer Travis Cravens, a member of Seneviratne’s team, handled the setup and configuration of C3 Performance. System and application engineers from MTS completed the installation and training in less than a day, and the lab saw results almost immediately.
“We were running 20 percent faster by the end of the first day with no mechanical modifications to the test rig,” Cravens said. “C3 Performance was very easy to learn and set up; it all occurs within the software. You simply create a cross-coupling matrix by applying a unit load on each load channel, which represents just one extra step for each actuator.”
To streamline test setup, C3 Performance eliminates the time-intensive task of manually inputting cross-coupling data by employing unit load cases to generate automated cross-coupling compensation coefficients. Seneviratne characterized this process with an apt analogy.
“It’s like having a team of 20 people who don’t know each other working on the same project,” he said. “The unit loads are simply a way of introducing all those people to each other so they can collaborate and work more efficiently.”
With some extra tuning, Seneviratne and Cravens were able to increase the test rate by 24 percent and cut the number of stops significantly.
“It has greatly improved the performance of our test,” Cravens said. “With the improved load tracking, small perturbations in feedback are much less likely to trigger error limits, resulting in fewer test stoppages. The reduction in error has also allowed us to run more segments per hour.”
Before using C3 Performance, NIAR was only able to achieve a maximum of 375 segments per hour, with an average of 97 stops and 55 interlocks per test block. With C3 Performance, this has improved to 480 segments per hour with an average of 51 stops and 15 interlocks.
“The number of stops was a third of what they were, which was a huge gain for us,” Seneviratne said. “That allowed us to run the test overnight, some nights without a single interruption. That’s up to 10 hours of testing we didn’t have before, which helped tremendously with our schedule.”
C3 Performance saved weeks, enabling Seneviratne’s team to provide the test results on time. In addition, lab productivity was enhanced: the team was able to operate on a more predictable schedule and had more time to devote to other projects. In any lab with finite resources, that is an important advantage.
“Knowing that we could run the test overnight and be confident we could do inspection and repair during the day allowed us to increase the efficiency of our test path,” Seneviratne said. “We were able to plan better and coordinate our activities knowing that the test ran overnight unattended with minimal interruptions.”