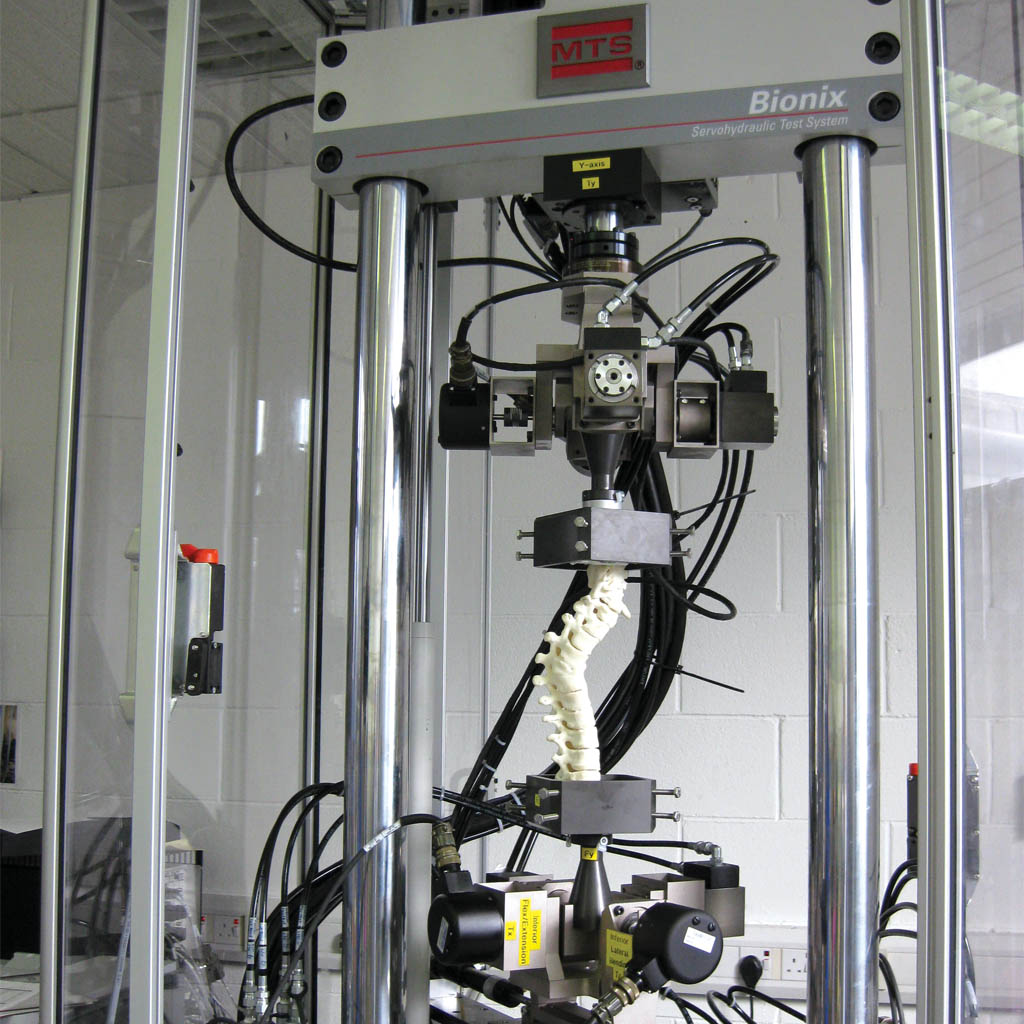
MTS helps biomechanical researchers equip surgeons with better information prior to scoliosis surgery.
CUSTOMER CHALLENGE
Approximately four in every 1,000 children will develop an unnatural curvature of the spine that requires medical supervision. One of these four will eventually need major corrective scoliosis surgery. This surgery involves physically correcting the spinal curvature and stabilizing it via vertebral fusion and/or the permanent insertion of metal instrumentation.
The Institute of Technology, Tallaght (ITT Dublin) is a university-level institution located in South Dublin, Ireland. The Bioengineering Technology Centre (BTC) is an established research center within the School of Engineering, providing intensive instruction to a handful of students pursuing advanced degrees in biomechanical engineering. One student is Nor Amalina Binti Muhayudin. She began her Master’s studies at the BTC in January 2009, in the pursuit of new methods for scoliosis diagnosis.
Historically, diagnosing scoliosis has involved a two-dimensional (2D) measurement technique known as the Cobb angle. This technique requires using a 2D spine image to identify the most tilted vertebra above and below the apex of the curvature in the frontal plane, and drawing lines along the top- and bottom-most tilted vertebrae. When two lines are drawn perpendicular to these lines, the angle created where the lines intersect is the Cobb angle.
Cobb angle measurements cannot quantify the spine’s vertebral rotation angle, however, which is an essential measurement for scoliosis diagnosis and treatment. Muhayudin’s challenge was to develop a detailed spinal bio-prototype for each patient. This prototype could provide a complete, three-dimensional (3D) diagnosis prior to major corrective surgery, including data on vertebral rotation angle.
“To date, surgeons have entered the operating room with limited information about the degree of a patient’s spinal curvature, meaning they had to spend time making these assessments during surgery,” Muhayudin said. “My research aims to provide a precise calculation of how much force will be necessary to straighten a spine before going in, reducing surgery time. This data could also lead to better long-term patient outcomes, because it can help us to better predict possible relapses under natural spinal loads and motions over time.”
MTS SOLUTION
In March 2009, the BTC upgraded its spine-related mechanical testing capabilities by purchasing an MTS Bionix® Test System with MTS FlexTest® controls and MTS MultiPurpose TestWare® (MPT) software.
Since a cadaveric spine could not be used for ethical reasons, Muhayudin began her research by developing a true-to-life artificial spine for use with the new Bionix test system. She took a 3D CAT scan of the mid-thoracic region of a pediatric spine and fabricated a prototype using a Select Laser Sintering (SLS) machine. The prototype was enlarged to twice its size to suit the Bionix test fixture. An artificial spine was built from a mould of the prototype, manufactured from polyurethane and silicone materials.
The Bionix test system can be used to simulate a full range of motions to the artificial spine and other specimens in six degrees of freedom, including axial displacements, flexion, extension, lateral bending and torsion. Load cells capture test data as the forces and moments are applied.
“With the new MTS test system, Nor can now apply a preload to a spine specimen to precisely identify the forces required to move the spine back into a natural alignment during surgery,” said Dr. Fiona McEvoy, founder of the BTC. “This process holds tremendous potential for knowing more about what will be required during a spinal fusion procedure, based on the unique curvature of each patient’s spine.”
Muhayudin’s characterization method is the reverse of conventional spine testing. Rather than applying forces and moments to the artificial spine, she uses displacement as the control mode. The resulting forces and moments acting on the spine specimen determine the degree of displacement with each scoliosis case, allowing surgeons to quantify how much force and torque will be required to optimally correct the curvature.
CUSTOMER BENEFITS
Muhayudin says that if her new diagnosis technique ultimately gets validated and used in the field, the end result will be faster, smoother spinal fusion procedures and better long-term patient prognoses. “We anticipate this new technique will reduce time in the operating room by 25 percent, which is significant considering these surgeries can take up to 12 hours,” she said.
“This time savings will help to significantly reduce the risk of infection and speed recovery time, not to mention the positive potential impact on surgeon productivity.”
Muhayudin will soon begin using live animal spines to validate her research findings. This will require adding an environmental chamber with saline bath to the Bionix test system, as a means of preserving biological specimens and enhancing the simulation accuracy of in-vivo spine conditions.
“It is very exciting that an artificial prototype can be manufactured for each patient undergoing spinal fusion surgery,” she said. “We are breaking new ground here, and it’s brilliant that such a complex test system is so user-friendly. This allows me to spend more time on my research and less time trying to master the test equipment.”