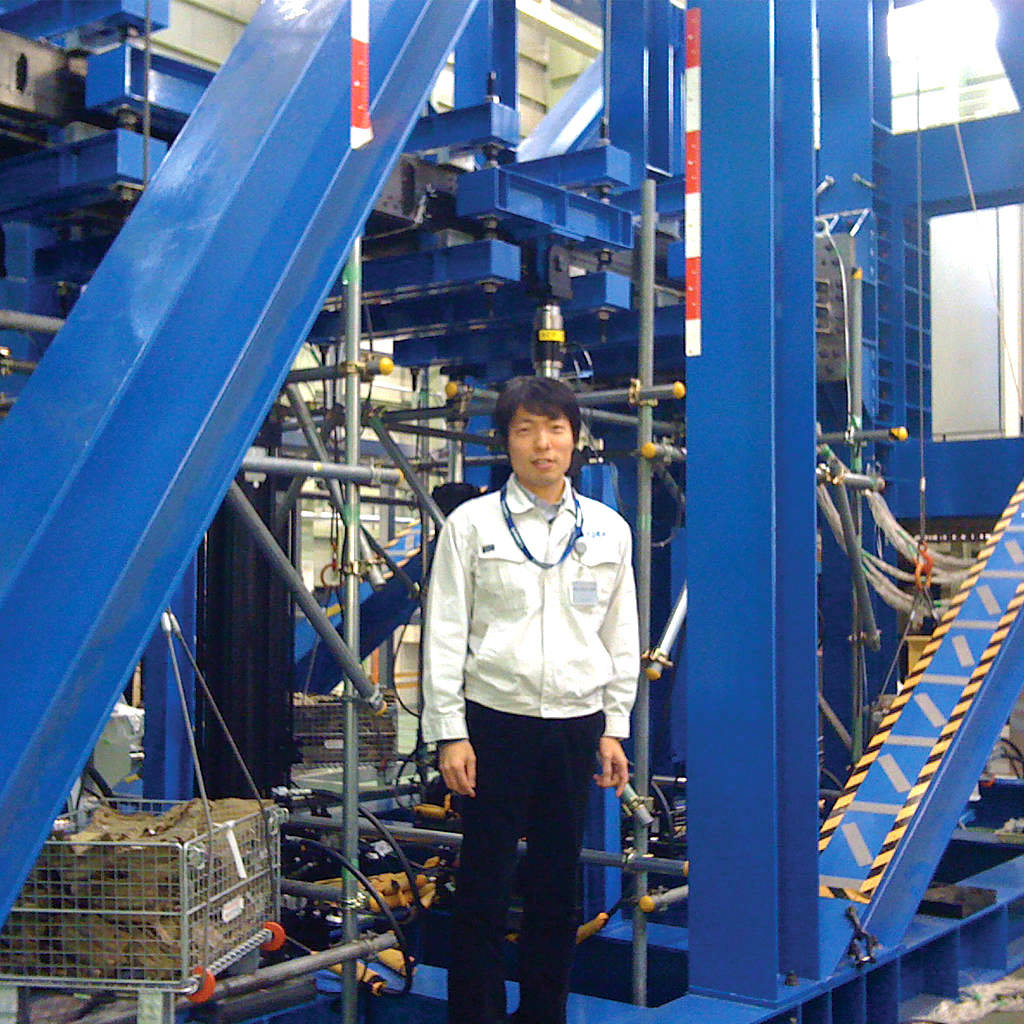
CUSTOMER CHALLENGE
As part of its mission to advance aerospace research, the Japan Aerospace Exploration Agency (JAXA) is developing innovative technologies and evaluation methods for improving the quality and reducing the cost of aircraft materials, components and structures. For passenger aircraft, quality means safety. Consequently, the JAXA Civil Transport Team, Aviation Program Group must be absolutely certain that any production methods it introduces not only reduce cost, but also yield products that perform to the highest standards of durability, strength and reliability.
Rising fuel costs and a global focus on energy conservation have generated strong demand for more lightweight airplanes that consume less fuel. However, the composite components and structures employed to achieve this objective generally cost more to produce than their conventional aluminum counterparts. Dr. Yuichiri Aioki and his Advanced Composite Group set out to resolve this dilemma. Specifically, the team focused on the new fabrication technology of Vacuum-assisted Resin Transfer Molding (VaRTM) to explore its potential for low-cost composite component and structure production. What they discovered was that the innovative resin-infusion process could produce composite parts that not only weighed 20% less, but also cost 20% less than products made using conventional methods. VaRTM reduced part cost and weight compared to the typical autoclaved prepreg processes by employing a more streamlined single-sided molding, without an autoclave, to form larger, more complex composite structures with fewer parts.
Having proven the effectiveness of VaRTM as a low-cost production process, Dr. Aioki and his team next had to prove that parts yielded by the VaRTM process could withstand the complex loading experienced by aircraft in flight. A key component of this task included mechanical testing. The mechanical testing solutions JAXA selected would need to be flexible enough to manage the demands of the testing required, and capable of delivering the high levels of control needed to fulfill the multi-axial demands of real-world simulation.
JAXA ultimately chose to work with MTS, and according to Dr. Aioki, the choice was easy. “MTS is a technology leader with a proven track record in aircraft component testing solutions,” he said. “The company also possesses the expertise necessary to help us precisely and confidently meet our unique needs.”
MTS SOLUTION
The objective of JAXA’s mechanical testing program was to subject VaRTM-generated composite parts to the demanding conditions of actual flight, including steep changes in altitude. The program included fatigue tests of subcomponents, as well as static testing of a full-scale wing. MTS helped JAXA meet this objective with its offering of precision digital controls, robust load frames and actuators, advanced application software, and expert service and support.
For the subcomponent fatigue tests, MTS supplied a Model 311.41 servohydraulic load frame (2500 kN) outfitted with high-force Model 647.200 hydraulic grips for wide panel specimens. The system employs a versatile FlexTest® 40 digital controller and a PC running Multi-Purpose TestWare® software.
Equipment for the static testing of the full-scale wing included four, compact MTS servohydraulic actuators driven by a high-capacity FlexTest 200 digital controller and client PC running AeroPro™ Control & Data Acquisition software.
In addition to high-performance hardware and software, Dr. Aioki also credited MTS calibration services and onsite training as vital to his team’s success. “The calibration service of MTS was important in enabling us to trace the data from the experiment. In aircraft testing, the traceability of the test data is strictly regulated - data that is not traceable will not be approved.” With regards to MTS support, he added, “When questions arose, the experts from MTS promptly delivered the answers and guidance we needed to keep our testing on schedule.”
CUSTOMER BENEFITS
MTS solutions helped JAXA quickly and confidently confirm that composite parts produced using the new process could withstand the real-world forces experienced by aircraft in flight. “We can now prove that composite materials fabricated by VaRTM have been subjected to rigorous performance evaluations and have demonstrated their suitability for use in aircraft wings,” said Aioki. “MTS’ deep experience with full-scale structural component testing was obvious, they clearly had the knowledge required to formulate the exact testing solutions we required.”
In addition to MTS’ in-house expertise, Aioki expressed appreciation for MTS-sponsored user forums and seminars. “Being able to widely exchange ideas and best practices with fellow users of MTS devices is instrumental to the continued success of our research.”
“Thanks to MTS, we will soon start certification tests of passenger aircraft developed by Japanese companies,” Aioki concluded. “The world will soon have a safe and cost-effective new means of manufacturing more lightweight and fuel-efficient commercial aircraft without compromising passenger safety. The reliability of the testing equipment and the guidance of MTS experts were indispensable to this achievement.”