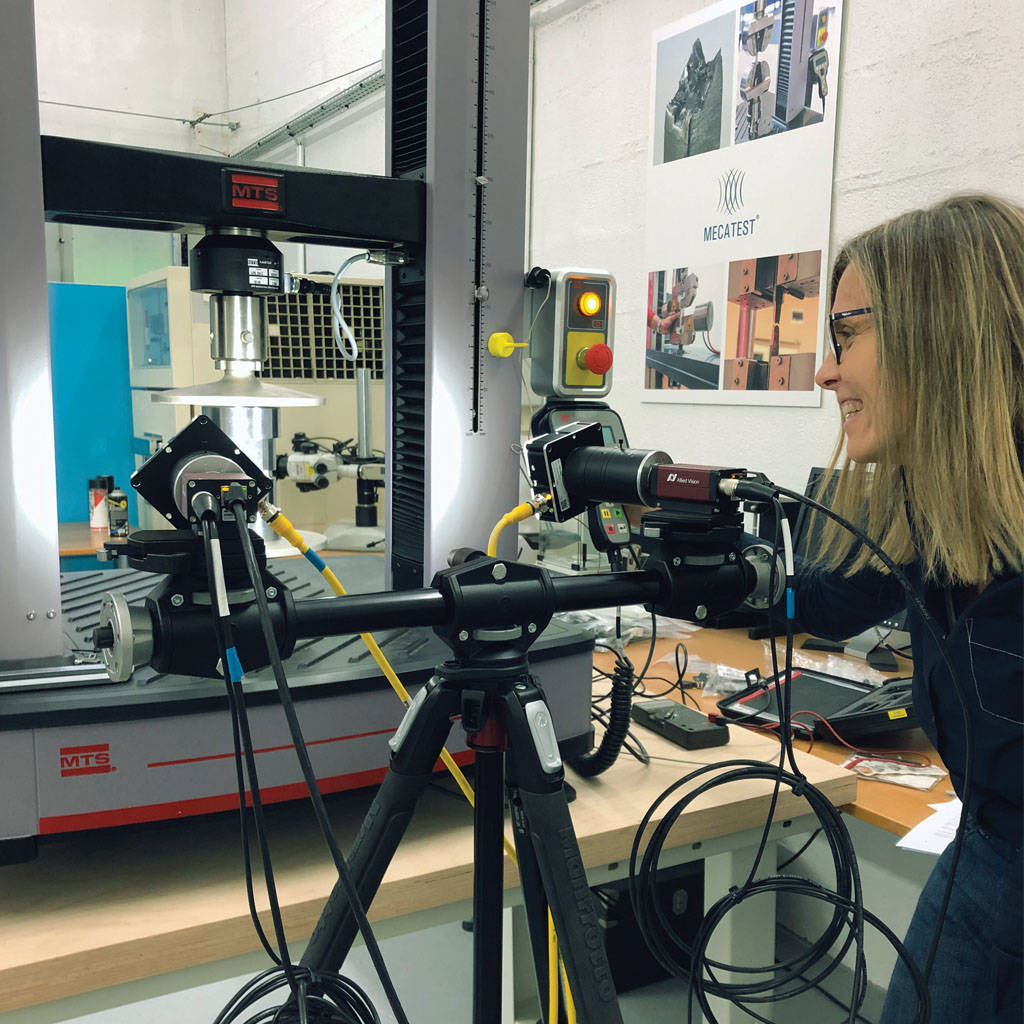
Mecatest, a provider of mechanical test services, can deliver a wide array of material characterization data to its customers. Generally working with polymers and composites, the tests are typically run in compression, flexion (bending) or tension. But regardless of the material or the type of test, the common component in most of their testing is the use of digital image correlation (commonly referred to as DIC). By synchronizing their DIC strain data with their universal test system (UTM) force and displacement data, Mecatest is easily able to produce accurate correlations between the physical test data and their customers’ modeled simulation.
Integrating communications between the test system and the DIC cameras was accomplished via TTL (standard hardware interface) signals. This closed loop communication was created so that the UTM’s system software is able to trigger, capture and store the proper images. This way all the necessary data (time, force, displacement, digital output) is maintained by the UTM. The test system data corresponding to the images (time, force, displacement) can also be filtered and sent to the DIC software for analysis.
The DIC software collects 3D images of the mechanical structure to measure displacements and strains directly on the finite element mesh that was transferred from the numerical simulation. This provides simple but essential formatting continuity between simulation and test. Such a methodology enables comparisons of measured and simulated fields to be made automatically, facilitating quick validation of the numerical simulation. Once complete, data can be exported and used by the CAE engineer to improve the previous model.
The DIC software can also be used to automate the identification of error sources and model corrections. Using this idea, simulations can be run with measured boundary conditions in order to provide a more realistic simulated result. A final option is that the DIC software can also modify the simulation according to the physical dataset (displacements, strains, forces). This method generally increases model predictability for better simulations and often reduces the need for additional testing.
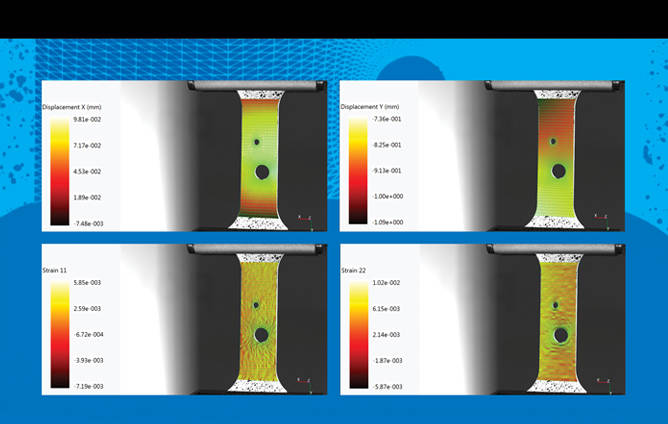
A unique specimen shape, like this one with holes, allows for characterization of the material’s application-related stress concentrations in a way that would not be possible with conventional strain measurement techniques.
Since DIC can provide full-field measurements, multiple stress scenarios can be evaluated simultaneously. Using DIC, strain level measurements become accurately predictable by improving the finite element model. This data may then be used to understand other complex geometries. Additionally, the out-of-plane measurements available with 3D DIC allow for more localized evaluations.