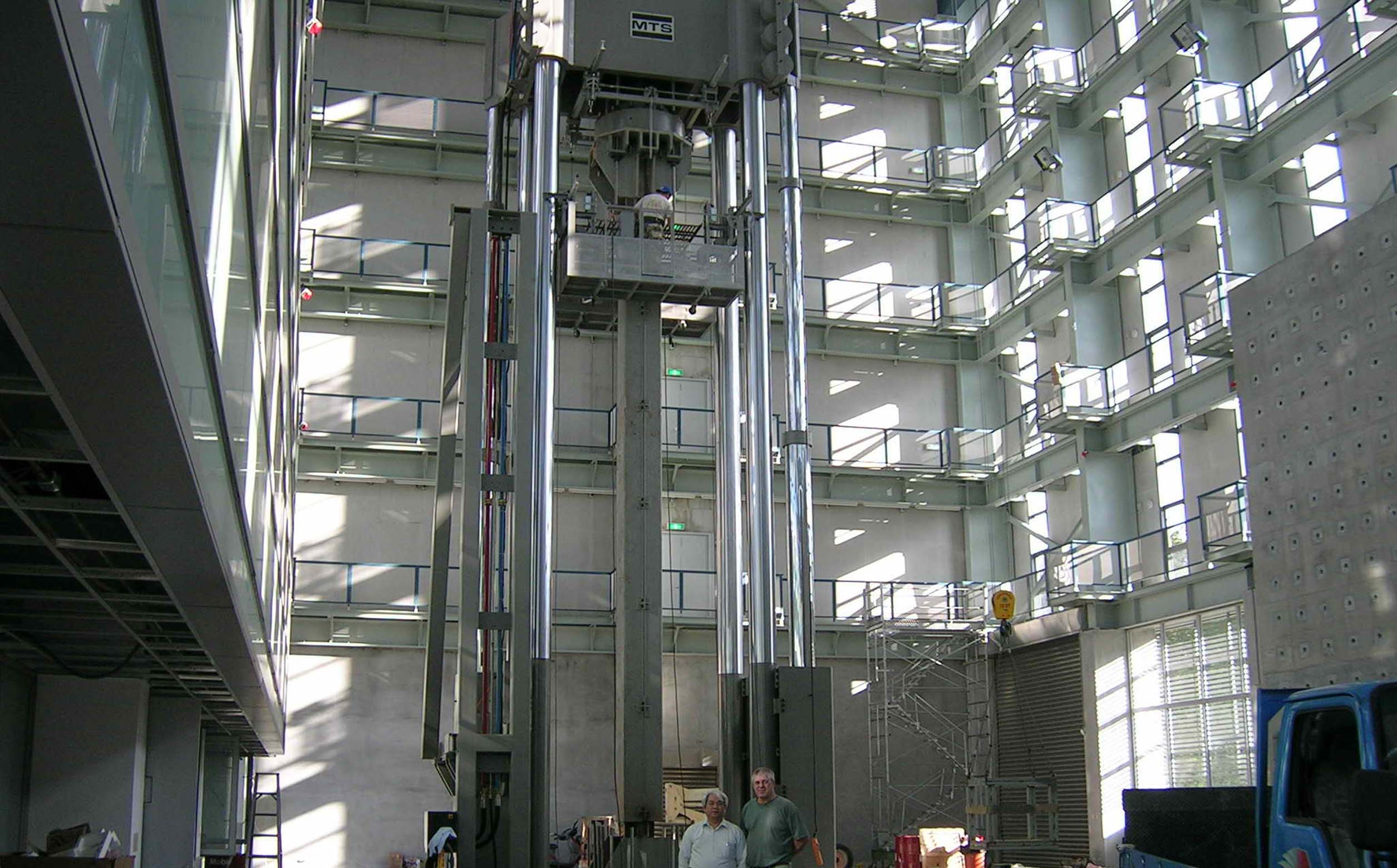
In this Q&A, MTS application engineers discuss the challenges and nuances of high-force materials and components testing.
Q: What is a high-force test? What kinds of specimens require high-force testing?
A: In general, any test that requires more than 1 Meganewton (MN), or 220 kip, qualifies as a high-force test. High-force mechanical testing is critical for determining the performance and durability properties of materials, components and sub-assemblies in many industries, including construction materials like concrete and steel; civil structures, such as beams, columns and rebar; and large components for aerospace, oil and gas, rail and wind turbines. Essentially, if you make a specimen large enough it will require a high-force test.
Q: What applications are most common in high-force testing?
A: High-force applications can range from static strength characterization to complex, dynamic life studies. Many product developers and manufacturers prefer to test full-scale components due to volumetric effects—as a material sample or specimen gets larger, its behavior may change. This variability is especially true for some materials, such as aluminum or polymer composites.
Q: How do engineers use data from high-force tests?
A: High-force tests provide essential data for developing reliable structures, components and products that perform as expected. High-force tests investigate and determine maximum stresses for materials, which can be difficult to predict due to the volumetric effects mentioned in the previous answer. Specimen size can greatly influence a material’s fatigue curve, which is used in product design.
Engineers use high-force testing to determine whether a material’s failure mechanisms vary according to specimen sizes, and then create models that accommodate for these variances. For some materials, such as polymer composites, high-force dynamic testing helps engineers understand how the weave and angle of the reinforcing fibers affect the ultimate strength and life of the material.
Q: How long has MTS provided high-force solutions? Where have they been deployed?
A: MTS has been solving high-force testing challenges for more than 50 years. We were the first to use hydraulics for cyclic materials testing and the first to use them for high-force testing. What that means for customers is that our team understands the implications of all the decisions that must be made to get a solution that delivers the data you need. We have seen what works and what doesn’t and can help you avoid problems before they begin.
MTS has deployed these systems globally for applications ranging from basic research to identifying specific material properties, and today we have systems at universities, government research centers, and commercial manufacturing facilities in a wide range of industries including aerospace, automotive, energy and civil engineering.
Q: What kind of systems does MTS offer for high-force testing applications?
A: MTS offers a complete portfolio of standard high-force test systems for testing up to 5 MN (1100 kip) and can provide custom-engineered solutions for higher force capacity requirements as well. In these instances, MTS works closely with customers to design and build their system, such as a 10 MN (2200 kip) system for conducting bend tests of structural steel beams, or a 30 MN (6600 kip) system for running compression tests of reinforced concrete columns. Test systems can come in a traditional vertical or horizontal orientation.
Q: What are the advantages of a horizontal or vertical orientation?
A: That depends on the specimen being tested. A customer testing long length cables or oil pipelines for instance may have an easier time loading the specimen into a horizontal frame using an overhead crane. Conversely, a compression test using platens is much easier to do in a vertical frame where the user can properly set and align the specimen on the bottom platen—something that would be nearly impossible to do in a horizontal frame.
Horizontal High-Force Load Frame
Q: Does high-force testing require special grips?
A: Yes. Our grips are sized and engineered to reduce mass for high-force dynamic testing. They are designed to be light to improve performance and give customers the widest possible range of frequency and maximum force. Light grips help avoid wasting a great deal of energy to get the same results.
Reduced-mass high-force grips offer wide range of frequency and maximum force
Q: How do you measure the force applied to the specimens?
A: Accurately measuring force at these high loads is a unique challenge, and we have a couple of different solutions. MTS can manufacture custom load cells for high-force testing requirements up to 30 MN. These high capacity force transducers can feature either a multi-column design or tube design that resists extraneous forces and moments for greater accuracy and high lateral stiffness. We also have a lower cost solution that uses a pressure sensor to calculate the applied force based on the actuator's piston area. This "Delta P" sensor is easy to install and calibrate and has similar accuracies to a load cell at high forces.
MTS 30 MN (6500 kip) Load Cell
Q: How do you maintain proper alignment in high-force test solutions?
A: Alignment is critical because any bending in the specimen will compromise data quality. Our load frames exhibit superior system alignment, which minimizes bending strain to enhance test accuracy and reduce data scatter. In addition, we offer alignment fixtures for our standard solutions (up to 1 MN) that make it easy to detect whether any part of the load train for a fully instrumented specimen is out of alignment.
Q: How do MTS high-force load frames compare to other high-force solutions on the market?
A: Numerous design refinements derived from decades of meeting real-world needs put MTS high-force systems in a category of their own. For example, the welded crosshead has a “bathtub” design that contains the system actuator, minimizing the distance between the bearing and the test base to provide more accurate results. The hydraulic service manifolds (HSMs) are mounted directly on the frame and we use local close-coupled accumulation as required. The system’s smooth columns with clamps integral to the crosshead allow for fast adjustment of crosshead height. All of these design elements manifest in the unmatched utility and ruggedness of the system, and its ability to run fatigue tests to the full force rating of the frame for very long periods of time.
Q: Do high-force load frame systems present unique facilities challenges?
A: Yes, it can be very challenging. We’ve had to remove roofs from buildings and move systems in on a crane. Installing these high-force testing solutions usually requires extensive systems integration expertise. For example, we delivered a 30 MN system to a facility in Taiwan where we integrated components designed in Minneapolis and manufactured by suppliers from across the globe. Even for smaller high-force systems, facility design plays an important role. The base plate of the system often must be integrated with the floor of the building. We have the experience to guide customers through the process, so they understand how to prepare the facility for a successful installation and test operations.
Contact MTS today and learn how you can benefit from decades of MTS high-force testing expertise.