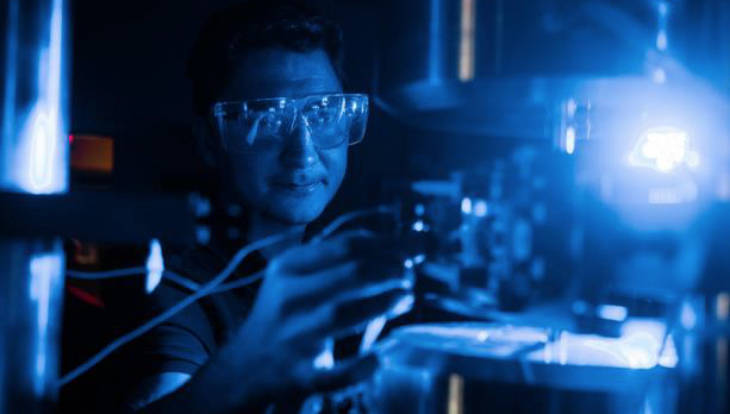
Nearly every load-bearing mechanical part is loaded more than once in a system's lifetime. In many industries, structural materials are designed to withstand repeated variable uni- or multi-axial proportional or non-proportional loading conditions. Often, designs for these kinds of metallic structures are based on elastic (yield-limited) analysis that fails to capitalize on the material's load-bearing reserve, leading to inefficiencies in structural weight and durability. In contrast, designs to shakedown, a safe cyclic elastoplastic behavior, can extend component lifetimes and/or lightweighting benefits.
Lehigh University Opening Doors For Shakedown Design
Shakedown is achieved by establishing appropriate residual stresses upon cyclic loading that lead to the arrest of plastic accumulation and the recovery of purely elastic behavior. Although developed in the 1920s, shakedown concepts and design rules are little-known outside the nuclear industry and are severely underutilized in many engineering design communities. A major obstacle to the wider application of shakedown analysis is the lack of experimental assessment over a range of demanding thermomechanical loading conditions using modern full-field measurements. Providing this experimental characterization in order to enable broader applications in shakedown design and optimization is one of the major goals of Dr. Natasha Vermaak's team at Lehigh University.
Experimental data allow the team at Lehigh to calibrate constitutive models. They combine information provided by contact extensometers and the non-contacting DIC (digital image correlation) system to better understand and model cyclic inelastic behaviors.
Data Synchronization
The test system controller has multiple digital and analog inputs and outputs that synchronize the thermomechanical testing with the DIC controller for the DIC measurements. The experimental data are stored in both systems; the DIC results (DIC fields, components, projects) are saved in the DIC system while the test system data are saved there. However, test system controller analog outputs also allow two channels to be sent to the DIC system with thermography compensation and saved in the corresponding DIC projects. This allows for a better time synchronization between the DIC fields and the applied loads. It also makes it easier to compare the full field measurements with the point-based data.
Data Analysis & Reduction
An important feature of the test system software is the ability to program experiments that change behavior based on intermediate measurements. Using conditional programming, specimen response measurements result in different criteria and launch additional measurements or adapt the loading conditions. In the case of shakedown testing, the aim is to determine whether or not plastic accumulation stabilizes during cyclic loading. The software can generate a user-defined program that automatically checks for this condition. When used to trigger the DIC controller, only the pertinent data are recorded and data reduction is accomplished. The DIC system also provides complementary features for data synchronization and acquisition.
Complementary Strain Measurement Solutions
The test lab uses both contacting and non-contacting strain measurement solutions because together they deliver a more comprehensive material characterization. DIC provides much more information than an extensometer, such as displacements and strains at all visible points on the sample. And non-contacting measurement solutions provide some additional freedom regarding sample size, experimental setup, and reusability. On the other hand, contact extensometers are well known as robust and reliable strain measurement technology. Extensometers also allow for higher data acquisition rates than a DIC system whose images can require significant data storage space and time to process.
The Vermaak Lab benefits from the engineering, application and integration support received from their test system and DIC system partners, making the data gathering, synchronization and analysis with these systems accurate and efficient.
Lehigh University Opening Doors For Shakedown Design
Shakedown is achieved by establishing appropriate residual stresses upon cyclic loading that lead to the arrest of plastic accumulation and the recovery of purely elastic behavior. Although developed in the 1920s, shakedown concepts and design rules are little-known outside the nuclear industry and are severely underutilized in many engineering design communities. A major obstacle to the wider application of shakedown analysis is the lack of experimental assessment over a range of demanding thermomechanical loading conditions using modern full-field measurements. Providing this experimental characterization in order to enable broader applications in shakedown design and optimization is one of the major goals of Dr. Natasha Vermaak's team at Lehigh University.
Experimental data allow the team at Lehigh to calibrate constitutive models. They combine information provided by contact extensometers and the non-contacting DIC (digital image correlation) system to better understand and model cyclic inelastic behaviors.
Data Synchronization
The test system controller has multiple digital and analog inputs and outputs that synchronize the thermomechanical testing with the DIC controller for the DIC measurements. The experimental data are stored in both systems; the DIC results (DIC fields, components, projects) are saved in the DIC system while the test system data are saved there. However, test system controller analog outputs also allow two channels to be sent to the DIC system with thermography compensation and saved in the corresponding DIC projects. This allows for a better time synchronization between the DIC fields and the applied loads. It also makes it easier to compare the full field measurements with the point-based data.
Data Analysis & Reduction
An important feature of the test system software is the ability to program experiments that change behavior based on intermediate measurements. Using conditional programming, specimen response measurements result in different criteria and launch additional measurements or adapt the loading conditions. In the case of shakedown testing, the aim is to determine whether or not plastic accumulation stabilizes during cyclic loading. The software can generate a user-defined program that automatically checks for this condition. When used to trigger the DIC controller, only the pertinent data are recorded and data reduction is accomplished. The DIC system also provides complementary features for data synchronization and acquisition.
Complementary Strain Measurement Solutions
The test lab uses both contacting and non-contacting strain measurement solutions because together they deliver a more comprehensive material characterization. DIC provides much more information than an extensometer, such as displacements and strains at all visible points on the sample. And non-contacting measurement solutions provide some additional freedom regarding sample size, experimental setup, and reusability. On the other hand, contact extensometers are well known as robust and reliable strain measurement technology. Extensometers also allow for higher data acquisition rates than a DIC system whose images can require significant data storage space and time to process.
The Vermaak Lab benefits from the engineering, application and integration support received from their test system and DIC system partners, making the data gathering, synchronization and analysis with these systems accurate and efficient.