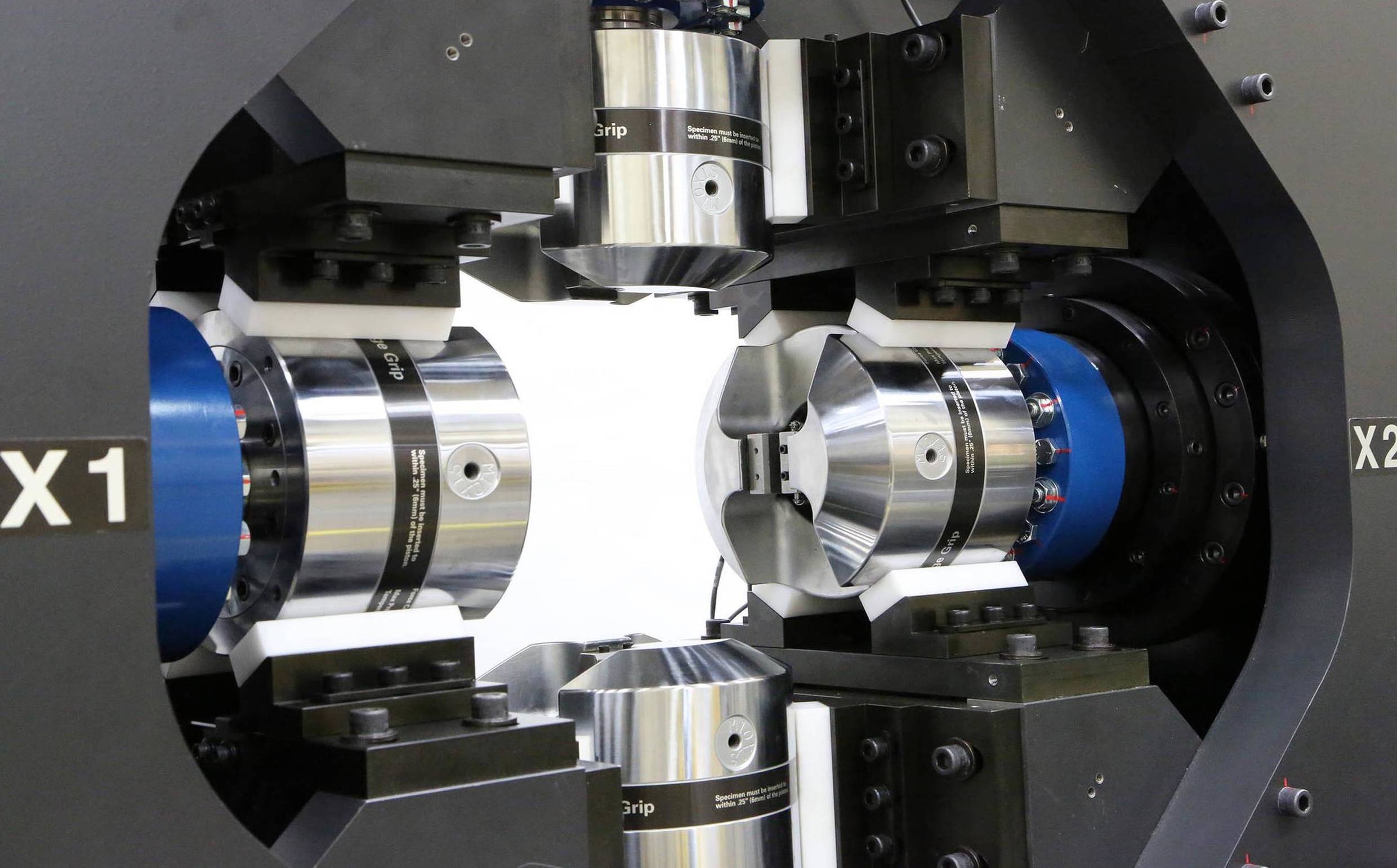
With more than 25 years of experience in materials testing, metallurgy and system engineering, MTS staff scientist Dr. Erik Schwarzkopf brings unique expertise to customer engagements. Steve Lemmer, MTS Senior Design Engineer, has been developing innovative test solutions for more than 23 years and played an instrumental role in designing the fifteen planar biaxial test systems MTS has installed worldwide. In this Q&A, they discuss the origins, challenges and advantages of planar biaxial testing.
Q: What is planar biaxial testing? How does it differ from conventional uniaxial testing?
Schwarzkopf: The idea of planar biaxial testing is that in the real world, most structures and components are subject to loading in more than one direction. To simulate real-world conditions, test engineers need the ability to pull the specimen in multiple directions while exerting a great deal of control over the process. In this case, “control” means keeping the center of the specimen precisely in the center and removing the risk of additional bending stress. Our planar biaxial system uses four actuators in one plane to accomplish this. Test specimens for planar biaxial tests are unique in that they are often a cruciform shape with four points of attachment; and the arms are typically equal in length. This is important because everything around the center of the specimen needs to stretch evenly. If not, the test will not achieve the right results.
Q: How did planar biaxial testing come about? What are its origins?
Schwarzkopf: The need for planar biaxial testing emerged in the 1960s with the advent of jet engines. There was a lot of interest among aerospace manufacturers about stress states on aircraft structures. Another early application was analyzing the grain structure of sheet metal in automobile manufacturing. Prior to planar biaxial testing, engineers would perform multiple, separate uniaxial tests and predict real-world, multi-axial behavior using extrapolation.
Q: What role did MTS play in the refinement of planar biaxial testing technology?
Schwarzkopf: MTS got involved in the 1980s. We were pioneers in developing the first biaxial test systems that could twist and pull at the same time, using a single loading unit. Then we added side loads, for which you need four actuators. The ability of our solutions to control multiple axes simultaneously was vital for making this type of testing both feasible and accurate. MTS was very familiar with controlling the phase relationship among multiple actuators through our experience in the automotive industry. Then we added a load frame to ensure a specific geometric relationship. Then in the 1990s we developed the software, digital controllers and control schemes that made it easier for the customer to achieve proper centroid control. It was possible prior to this, but it was very difficult and not efficient for many labs.
Q: What critical needs do planar biaxial tests address?
Schwarzkopf: Engineers rely on planar biaxial test data to make important design decisions about material strength and thickness. There are applications in many industries, primarily for testing metals. The focus tends to be on dynamic testing, meaning fracture mechanics and fatigue crack growth. Our customers need to know how quickly a crack will grow and how soon it will reach a critical size under various loading conditions. Other planar biaxial simulations are used to test actual, real-world components. These tests can be truly biaxial as well as axial and torsional, and these forces can be in synch or opposing. Some customers might want to run damage tolerance tests to measure crack growth from a large hole in the material, then repair the damage and see how the repair holds up, or test how many times the same hole can be repaired. This is the beauty of planar biaxial testing: it can be tailored to control the forces in whatever way produces the data you need.
Q: How do customers use the data from planar biaxial tests?
Schwarzkopf: The data helps our customers develop new manufacturing techniques, understand the behavior of new materials like composites and develop better models. There are numerous practical applications, typically performed in large research and development facilities. Aerospace manufacturers are examining structures and components of aircraft. Gas turbine manufacturers are testing components used in aircraft jet engines and power generation units. Big national labs tend to be very interested in planar biaxial testing. It provides a degree of realism that is significantly closer to the actual operating environment than can be achieved with uniaxial testing. But in cases where structural or component failure can have disastrous results, which is certainly the case with aerospace and power generation, planar biaxial testing is very popular.
Q: What are some of the key technical challenges of planar biaxial testing?
Lemmer: The most challenging aspects of planar biaxial testing include: achieving precise centroid control; ensuring proper system alignment; and realizing test repeatability.
Q: What is centroid control?
Lemmer: Centroid control refers to the ability to keep the center of the specimen precisely where the researcher wants – usually, but not always, in the center of the test space. MTS planar biaxial systems can control the centroid’s location within microns. In most applications, the customer wants to move the edges out or in, squeezing and pulling, in a cyclical test. But the center has to remain stationary. These tests last for days. Our planar biaxial systems are optimized for low-cycle fatigue testing, which is typically ten thousand cycles. A typical frequency for these tests is 1 Hz.
Q: Why is ensuring system alignment important?
Lemmer: If the test pushes and pulls the specimen in two directions, the application of those forces must occur in the same plane. Otherwise, it introduces an unintentional bending force or shear stress that can’t be properly controlled and is unaccounted for in the analysis. That compromises the data because unintentional stress can lead to early specimen failure. If you’re counting cycles to failure, that number will not be accurate. Unintentional stress also puts the specimen at risk of buckling. In many industries, aerospace especially, the specimen can be very expensive to replace. MTS ensures proper alignment with an alignment fixture that provides grip-to-grip alignment adjustment to ensure everything is coplanar, concentric and angularly adjusted. MTS precisely machines the actuators and their mounting locations to minimize bending strains, but even small misalignments can affect the test; minor adjustments must be made and the alignment fixture makes it easy to perform those adjustments.
Q: Does the alignment fixture guarantee test repeatability?
Lemmer: After you get the frame alignment perfect, you have to put the actual specimen in place and then ensure that the alignment is still correct. We use standard hydraulic wedge grips that clamp onto the specimen in the same way every time. They apply the same force to every leg of the specimen. In other words, they are very repeatable. And they are designed to accommodate many different specimen sizes. The other option is to use a bolt-together mechanical fixture that is not nearly as flexible and does not provide the same kind of grip-induced alignment repeatability. With MTS, you can make sure the specimen is aligned within minutes. Other systems might take half a day.
Q: How have these challenges shaped the MTS planar biaxial offering?
Lemmer: To ensure the integrity of test data our systems are designed for the utmost control and alignment. They provide exceptional lateral stiffness. The actuators include hydrostatic bearings, and they are nested together to minimize the distance from the actuator to the test space. An over-moment protection device helps support each actuator in the event of an out-of-plane event. These will catch the fixturing in the load train and take the forces back to ground instead of damaging the load cells or actuators. Because no matter how careful you are, specimen legs can break unexpectedly. Our system design prevents the frame from being damaged. It is a very robust design with hardly any friction in the actuators, which is also important for wave shape fidelity and the control software.
Q: What is the range of MTS offerings for planar biaxial testing?
Lemmer: We have force capacities ranging from 25 to 500 kN. We also have a system that can deliver 250 kN in one direction and 500 kN in another. Many of these systems also have torsional capabilities. Each solution includes the necessary accessories, software, digital control technology and user interface to meet each customer’s specific test application requirements. It’s a complete solution, so the customer enjoys a “one-stop” experience and can be confident that all of the components are engineered to interact seamlessly. We have installed fifteen of these systems around the world since 1990 and we understand both the test equipment and the tests very deeply.
Q: What are some examples of enhancements MTS can build into planar biaxial systems?
Lemmer: The design of MTS planar biaxial systems can be readily modified to meet customers’ exact testing requirements. Many customers want to keep the loads equal in both directions. But some do not. For example, a planar biaxial customer was more interested in controlling the ratio of the loads, and changing the ratio to see how it affected crack propagation and orientation. This is also known as the output of Mohr’s circle. The principal stresses create shear stress at an angle. The stress states and crack growth rates can be completely different in these cases, which of course has design implications. As mentioned, we can also add rotation to a planar biaxial test system configuration, which allows researchers to investigate a far larger portion of the stress tensor. Over the years we have integrated a variety of environmental simulation systems into planar biaxial solutions to apply extreme temperatures, vacuum and humidity to specimens under test. Most recently, we designed a compact, low-mass 25 kN system that allows researchers to integrate and articulated within a stationary particle beam line.
Contact MTS today to learn more about solutions for planar biaxial testing.
Q: What is planar biaxial testing? How does it differ from conventional uniaxial testing?
Schwarzkopf: The idea of planar biaxial testing is that in the real world, most structures and components are subject to loading in more than one direction. To simulate real-world conditions, test engineers need the ability to pull the specimen in multiple directions while exerting a great deal of control over the process. In this case, “control” means keeping the center of the specimen precisely in the center and removing the risk of additional bending stress. Our planar biaxial system uses four actuators in one plane to accomplish this. Test specimens for planar biaxial tests are unique in that they are often a cruciform shape with four points of attachment; and the arms are typically equal in length. This is important because everything around the center of the specimen needs to stretch evenly. If not, the test will not achieve the right results.
Q: How did planar biaxial testing come about? What are its origins?
Schwarzkopf: The need for planar biaxial testing emerged in the 1960s with the advent of jet engines. There was a lot of interest among aerospace manufacturers about stress states on aircraft structures. Another early application was analyzing the grain structure of sheet metal in automobile manufacturing. Prior to planar biaxial testing, engineers would perform multiple, separate uniaxial tests and predict real-world, multi-axial behavior using extrapolation.
Q: What role did MTS play in the refinement of planar biaxial testing technology?
Schwarzkopf: MTS got involved in the 1980s. We were pioneers in developing the first biaxial test systems that could twist and pull at the same time, using a single loading unit. Then we added side loads, for which you need four actuators. The ability of our solutions to control multiple axes simultaneously was vital for making this type of testing both feasible and accurate. MTS was very familiar with controlling the phase relationship among multiple actuators through our experience in the automotive industry. Then we added a load frame to ensure a specific geometric relationship. Then in the 1990s we developed the software, digital controllers and control schemes that made it easier for the customer to achieve proper centroid control. It was possible prior to this, but it was very difficult and not efficient for many labs.
Q: What critical needs do planar biaxial tests address?
Schwarzkopf: Engineers rely on planar biaxial test data to make important design decisions about material strength and thickness. There are applications in many industries, primarily for testing metals. The focus tends to be on dynamic testing, meaning fracture mechanics and fatigue crack growth. Our customers need to know how quickly a crack will grow and how soon it will reach a critical size under various loading conditions. Other planar biaxial simulations are used to test actual, real-world components. These tests can be truly biaxial as well as axial and torsional, and these forces can be in synch or opposing. Some customers might want to run damage tolerance tests to measure crack growth from a large hole in the material, then repair the damage and see how the repair holds up, or test how many times the same hole can be repaired. This is the beauty of planar biaxial testing: it can be tailored to control the forces in whatever way produces the data you need.
Q: How do customers use the data from planar biaxial tests?
Schwarzkopf: The data helps our customers develop new manufacturing techniques, understand the behavior of new materials like composites and develop better models. There are numerous practical applications, typically performed in large research and development facilities. Aerospace manufacturers are examining structures and components of aircraft. Gas turbine manufacturers are testing components used in aircraft jet engines and power generation units. Big national labs tend to be very interested in planar biaxial testing. It provides a degree of realism that is significantly closer to the actual operating environment than can be achieved with uniaxial testing. But in cases where structural or component failure can have disastrous results, which is certainly the case with aerospace and power generation, planar biaxial testing is very popular.
Q: What are some of the key technical challenges of planar biaxial testing?
Lemmer: The most challenging aspects of planar biaxial testing include: achieving precise centroid control; ensuring proper system alignment; and realizing test repeatability.
Q: What is centroid control?
Lemmer: Centroid control refers to the ability to keep the center of the specimen precisely where the researcher wants – usually, but not always, in the center of the test space. MTS planar biaxial systems can control the centroid’s location within microns. In most applications, the customer wants to move the edges out or in, squeezing and pulling, in a cyclical test. But the center has to remain stationary. These tests last for days. Our planar biaxial systems are optimized for low-cycle fatigue testing, which is typically ten thousand cycles. A typical frequency for these tests is 1 Hz.
Q: Why is ensuring system alignment important?
Lemmer: If the test pushes and pulls the specimen in two directions, the application of those forces must occur in the same plane. Otherwise, it introduces an unintentional bending force or shear stress that can’t be properly controlled and is unaccounted for in the analysis. That compromises the data because unintentional stress can lead to early specimen failure. If you’re counting cycles to failure, that number will not be accurate. Unintentional stress also puts the specimen at risk of buckling. In many industries, aerospace especially, the specimen can be very expensive to replace. MTS ensures proper alignment with an alignment fixture that provides grip-to-grip alignment adjustment to ensure everything is coplanar, concentric and angularly adjusted. MTS precisely machines the actuators and their mounting locations to minimize bending strains, but even small misalignments can affect the test; minor adjustments must be made and the alignment fixture makes it easy to perform those adjustments.
Q: Does the alignment fixture guarantee test repeatability?
Lemmer: After you get the frame alignment perfect, you have to put the actual specimen in place and then ensure that the alignment is still correct. We use standard hydraulic wedge grips that clamp onto the specimen in the same way every time. They apply the same force to every leg of the specimen. In other words, they are very repeatable. And they are designed to accommodate many different specimen sizes. The other option is to use a bolt-together mechanical fixture that is not nearly as flexible and does not provide the same kind of grip-induced alignment repeatability. With MTS, you can make sure the specimen is aligned within minutes. Other systems might take half a day.
Q: How have these challenges shaped the MTS planar biaxial offering?
Lemmer: To ensure the integrity of test data our systems are designed for the utmost control and alignment. They provide exceptional lateral stiffness. The actuators include hydrostatic bearings, and they are nested together to minimize the distance from the actuator to the test space. An over-moment protection device helps support each actuator in the event of an out-of-plane event. These will catch the fixturing in the load train and take the forces back to ground instead of damaging the load cells or actuators. Because no matter how careful you are, specimen legs can break unexpectedly. Our system design prevents the frame from being damaged. It is a very robust design with hardly any friction in the actuators, which is also important for wave shape fidelity and the control software.
Q: What is the range of MTS offerings for planar biaxial testing?
Lemmer: We have force capacities ranging from 25 to 500 kN. We also have a system that can deliver 250 kN in one direction and 500 kN in another. Many of these systems also have torsional capabilities. Each solution includes the necessary accessories, software, digital control technology and user interface to meet each customer’s specific test application requirements. It’s a complete solution, so the customer enjoys a “one-stop” experience and can be confident that all of the components are engineered to interact seamlessly. We have installed fifteen of these systems around the world since 1990 and we understand both the test equipment and the tests very deeply.
Q: What are some examples of enhancements MTS can build into planar biaxial systems?
Lemmer: The design of MTS planar biaxial systems can be readily modified to meet customers’ exact testing requirements. Many customers want to keep the loads equal in both directions. But some do not. For example, a planar biaxial customer was more interested in controlling the ratio of the loads, and changing the ratio to see how it affected crack propagation and orientation. This is also known as the output of Mohr’s circle. The principal stresses create shear stress at an angle. The stress states and crack growth rates can be completely different in these cases, which of course has design implications. As mentioned, we can also add rotation to a planar biaxial test system configuration, which allows researchers to investigate a far larger portion of the stress tensor. Over the years we have integrated a variety of environmental simulation systems into planar biaxial solutions to apply extreme temperatures, vacuum and humidity to specimens under test. Most recently, we designed a compact, low-mass 25 kN system that allows researchers to integrate and articulated within a stationary particle beam line.
Contact MTS today to learn more about solutions for planar biaxial testing.