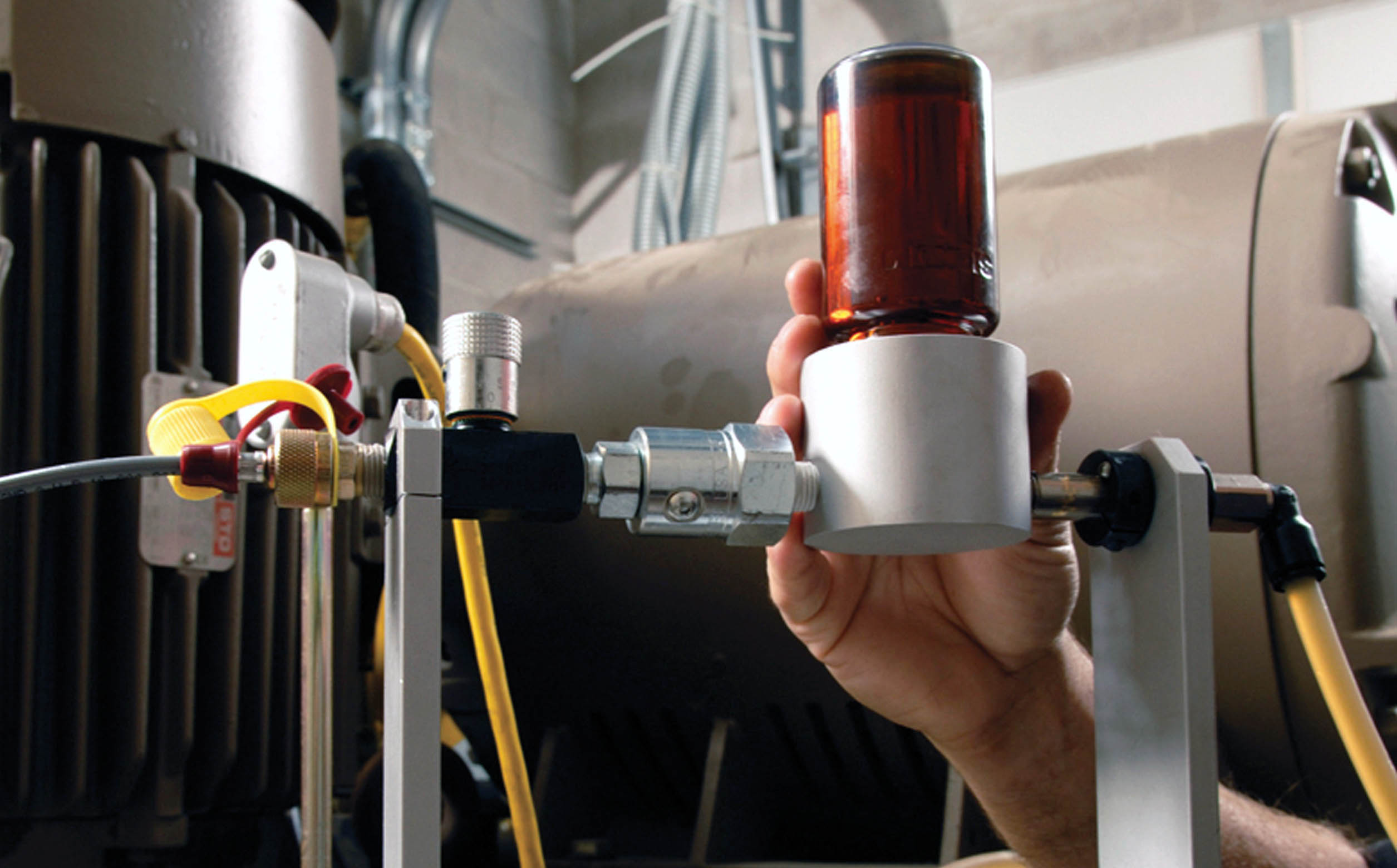
Many things can contaminate hydraulic fluid, and these items can damage your servohydraulic test systems as well as components such as servovalves, pumps and actuators. Here are some common contaminants and ways to detect them.
WATER
Oil & Water Don’t Mix
Water is highly undesirable in hydraulic systems. It can cause emulsions to form and can lead to corrosion. More than a trace of water may indicate an improper mechanical condition, poor performance of a heat exchanger or ingestion of water through the breather filter.
During system operation, a milky color of hydraulic fluid indicates likely water contamination. If the system is not in operation, contamination can usually be detected by sampling the fluid at the bottom of the reservoir, where water normally settles as it separates from the hydraulic fluid.
A simple test for water contamination is the “spat” test: Place a few drops of oil on a hot plate heated to above boiling, but less than 176° C (350° F); if the oil bubbles or sizzles, there is an unacceptable amount of water in the oil. If water contamination exists, fix the leak, and remove the water from the system immediately. Water can be removed by passing the fluid through water-absorbing filters, or by flushing or draining the entire hydraulic system.
SLUDGE, GUM & VARNISH
The Dangers of Oxidation
As hydraulic fluid deteriorates over time, it oxidizes and produces deposits that may cause servovalves to stick. The rate of oxidization increases significantly at operating temperatures higher than 66° C (150° F). Oxidation is irreversible, and the fluid must be changed when oxidization is detected.
Signs of this natural process include changes in fluid color, odor, or acidity level. Sludge, gum or varnish in the system are further evidence that oxidation has taken place. A fluid analysis with an ultra-centrifuge test can detect the level of oxidization.
HARD PARTICLES
Accelerated Abrasion Increases Contamination
Hydraulic pumps and servovalves can be damaged by fluid contaminated with hard particles larger than the clearance between lubricated surfaces. This occurrence is known as three-body abrasion, and causes scoring and heavy wear of sliding surfaces. Hard particles abrade the two surfaces that they come in contact with, and because the hard particle itself experiences wear, it is considered the third abraded surface. These hard particles create more wear contaminants by continually scraping off softer metals, like copper, to further accelerate component failures.
MTS fluid sampling and analysis services can help detect all these threats to hydraulic system health. Contact us today to learn more about fluid assessment options.