MTS FlexDAC 20 Data Acquisition Systems
Acquire high-fidelity test data from bridge-based devices such as strain gages and load cells, and high-level devices such as accelerometers and thermocouples. Fast acquisition speeds, high-channel-count capabilities and synchronization with FlexTest controllers make MTS FlexDAC data acquisition units ideal for evaluating the behavior of full-scale and component structures under load.
Key Product Features
Integrated / Synchronized
Employs hardware-based clock synchronization with FlexTest controllers to yield extremely high data accuracy
Versatile
Can distribute data acquisition channels in any proportion across multiple test stations simultaneously
Accelerated Testing
Eliminates the need to synthesize data manually after testing, improving productivity
Accurate / Repeatable
Automated calibration quickly verifies and documents measurement accuracy
Model Comparison
48-channel Units
- 48 input channels
- 15360 max channels per system
- Remote excitation sensing for ½ and full bridge sensors
- 70 mA, over current protected
- 1/2 bridge completion: 6-wire configuration
- Full bridge completion: 7-wire configuration
64-channel Units
- 64 input channels
- 20480 max channels per system
- 50 mA, over current protected
- 1/2 bridge completion: 4-wire configuration
- Full bridge completion: 5-wire configuration
Technical Overview
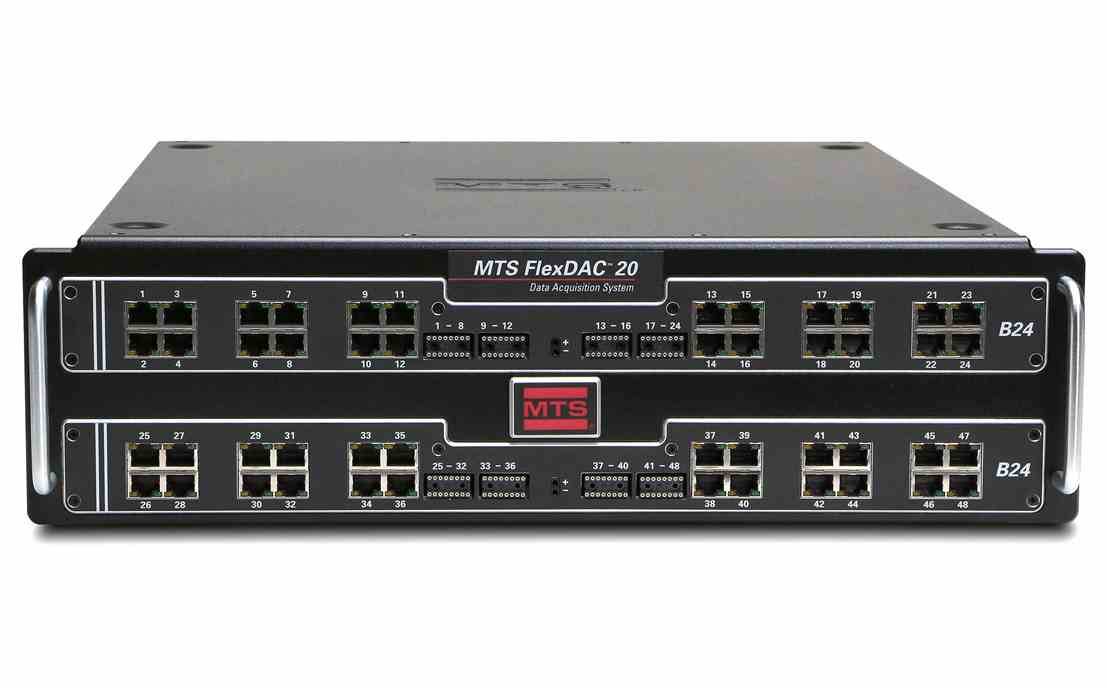
|
48-channel Unit |
General Functionality |
|
Total inputs per chassis |
48 |
Maximum number of channels per system |
15360 |
Input connector |
RJ-45 |
Synchronization with control system |
Hardware synchronized A/D conversion between all channels in all chassis and FlexTest 40/60/100/200 controllers or timestamp |
A/D converters |
24-bits per channel |
Independent stations |
Up to 4, any channel in any chassis |
Independent acquisition rate groups |
2 per station (up to 8 total) |
Supported sensors |
1/4 bridge, 1/2 bridge and full bridge strain gages, load cells, analog temposonics, string potentiometers and voltage input +/- 11mV, +/-110mV, +/-1.1V, +/- 11V |
Integration with other vendors |
Yes |
Network connection |
10/100 Base-T Ethernet |
Size |
48.26 cm W x 13.21 cm H x 55.5 cm L (19” x 5.2” x 21.85”) |
Weight |
7.76 kg (17.1 lb) |
Power and Environmental Specifications |
|
Power |
100 - 240 V AC, 50/60 Hz @ 250 VA max |
Ambient temperature |
0° - 55° C (32 - 131° F) |
Relative humidity |
0 - 85%, non-condensing |
Altitude |
Up to 3,048 m (10,000 ft) |
Certifications |
CE, EN 61326, EN 61010 |
Electrical Specifications |
|
Excitation |
0.5 V, 1 V, 2 V, 5 V, 7.5 V, 10 V |
Maximum current |
70 mA, over current protected |
Gains |
x1, x10, x100, x1000, set on a per-channel basis |
Temperature shift |
± 0.1% over temperature range |
Sampling rate |
1 Hz to 6 kHz, user selectable on a per channel basis in up to 8 acquisition groups |
Shunt resistors |
One per channel, externally installed on front of chassis, value specified at time of order |
Resistor connection |
Software activated per channel, shunts across local bridge completion resistor for 1/4 bridge or remote for 1/2, full bridge |
Back half resistor network |
1k/1k (0.05% ratio matching, 2 ppm/°C) |
Synchronization cable maximum lengths |
300 m between MTS FlexDAC chassis and FlexTest controller, 100 m between MTS FlexDAC chassis |
Synchronization chain restrictions |
160 FlexDAC chassis (7,680 channels) per chain, 2 chains per FlexTest controller |
Synchronization chain media |
Cat5e Ethernet cable |
Synchronization limitations |
Hot plugging allowed, auto master/slave detect, no cabling restrictions for acquisition groups |
Performance |
|
FIFO data buffering |
75 MB |
Tare |
Available for all channels |
Event/action |
Through AeroPro software |
Limit detection |
Through AeroPro software |
Conditioning |
|
1/4 bridge completion |
Standard 3-wire |
1/4 bridge completion resistance |
120 Ω, 350 Ω, optional user-specified (0.05%), set on a per-channel basis |
1/2 bridge completion |
6-wire configuration |
Full bridge completion |
7-wire configuration |
Bridge type and completion restrictions |
No restrictions, each channel individually configurable |
Excitation restrictions |
No restrictions, the excitation voltage is uniquely programmed for each channel |
Filters |
Bessel, Butterworth, Elliptical, Adjustable pass band (1 kHz max), no filter |
Filtering |
Analog anti-aliasing filter with digital low-pass filter set on a per-channel basis |
Filter frequencies |
Customer definable through AeroPro software to 1 kHz |
Filtering restrictions |
No restrictions |
Lead wire resistance |
Lead wire compensation is available for 3 wire ¼ bridge sensors. Remote excitation sensing for ½ and full bridge sensors. |
High strain nonlinearity |
Yes |
Features |
|
Modularity |
All units can stand alone or be combined with other units, from the same or different manufacturers |
LEDs |
Green LED for software controlled connection identification, yellow LED for excitation over current indication |
Transducer Electronic Data Sheets (TEDS) |
Supports IEEE 1451 class 2 interface |
Digital I/O |
“SMART DIO” enables any analog channel to be configured as a digital IO channel |
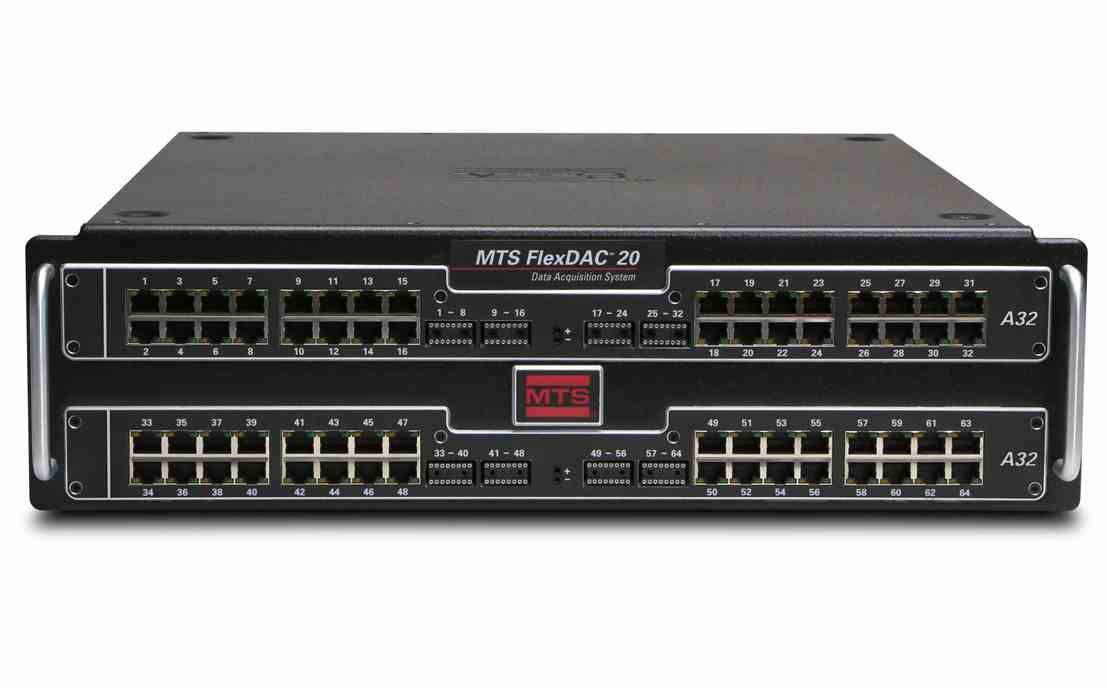
|
64-channel Unit |
General Functionality |
|
Total inputs per chassis |
64 |
Maximum number of channels per system |
20480 |
Input connector |
RJ-45 |
Synchronization with control system |
Hardware synchronized A/D conversion between all channels in all chassis and FlexTest 40/60/100/200 controllers or timestamp |
A/D converters |
24-bits per channel |
Independent stations |
Up to 4, any channel in any chassis |
Independent acquisition rate groups |
2 per station (up to 8 total) |
Supported sensors |
1/4 bridge, 1/2 bridge and full bridge strain gages, load cells, analog temposonics, string potentiometers and voltage input +/- 11mV, +/-110mV, +/-1.1V, +/- 11V |
Integration with other vendors |
Yes |
Network connection |
10/100 Base-T Ethernet |
Size |
48.26 cm W x 13.21 cm H x 55.5 cm L (19” x 5.2” x 21.85”) |
Weight |
7.76 kg (17.1 lb) |
Power and Environmental Specifications |
|
Power |
100 - 240 V AC, 50/60 Hz @ 250 VA max |
Ambient temperature |
0° - 55° C (32 - 131° F) |
Relative humidity |
0 - 85%, non-condensing |
Altitude |
Up to 3,048 m (10,000 ft) |
Certifications |
CE, EN 61326, EN 61010 |
Electrical Specifications |
|
Excitation |
0.5 V, 1 V, 2 V, 5 V, 7.5 V, 10 V |
Maximum current |
50 mA, over current protected |
Gains |
x1, x10, x100, x1000, set on a per-channel basis |
Temperature shift |
± 0.1% over temperature range |
Sampling rate |
1 Hz to 6 kHz, user selectable on a per channel basis in up to 8 acquisition groups |
Shunt resistors |
One per channel, externally installed on front of chassis, value specified at time of order |
Resistor connection |
Software activated per channel, shunts across local bridge completion resistor for 1/4 bridge or remote for 1/2, full bridge |
Back half resistor network |
1k/1k (0.05% ratio matching, 2 ppm/°C) |
Synchronization cable maximum lengths |
300 m between MTS FlexDAC chassis and FlexTest controller, 100 m between MTS FlexDAC chassis |
Synchronization chain restrictions |
160 FlexDAC chassis (10,240 channels) per chain, 2 chains per FlexTest controller |
Synchronization chain media |
Cat5e Ethernet cable |
Synchronization limitations |
Hot plugging allowed, auto master/slave detect, no cabling restrictions for acquisition groups |
Performance |
|
FIFO data buffering |
75 MB |
Tare |
Available for all channels |
Event/action |
Through AeroPro software |
Limit detection |
Through AeroPro software |
Conditioning |
|
1/4 bridge completion |
Standard 3-wire |
1/4 bridge completion resistance |
120 Ω, 350 Ω, optional user-specified (0.05%), set on a per-channel basis |
1/2 bridge completion |
4-wire configuration |
Full bridge completion |
5-wire configuration |
Bridge type and completion restrictions |
No restrictions, each channel individually configurable |
Excitation restrictions |
No restrictions, the excitation voltage is uniquely programmed for each channel |
Filters |
Bessel, Butterworth, Elliptical, Adjustable pass band (1 kHz max), no filter |
Filtering |
Analog anti-aliasing filter with digital low-pass filter set on a per-channel basis |
Filter frequencies |
Customer definable through AeroPro software to 1 kHz |
Filtering restrictions |
No restrictions |
Lead wire resistance |
Lead wire compensation is available for 3 wire ¼ bridge sensors. |
High strain nonlinearity |
Yes |
Features |
|
Modularity |
All units can stand alone or be combined with other units, from the same or different manufacturers |
LEDs |
Green LED for software controlled connection identification, yellow LED for excitation over current indication |
Transducer Electronic Data Sheets (TEDS) |
Supports IEEE 1451 class 2 interface |
Digital I/O |
“SMART DIO” enables any analog channel to be configured as a digital IO channel |
Service and Support
Our experts are here to help keep you up and running.
Related Products, Parts or Accessories
FlexTest® Controllers
AeroPro Software
MTS Wind Turbine Blade Fatigue Test Solutions
MTS Wind Turbine Blade Static Test Solutions
Looking for more products?
Go to Solution Finder