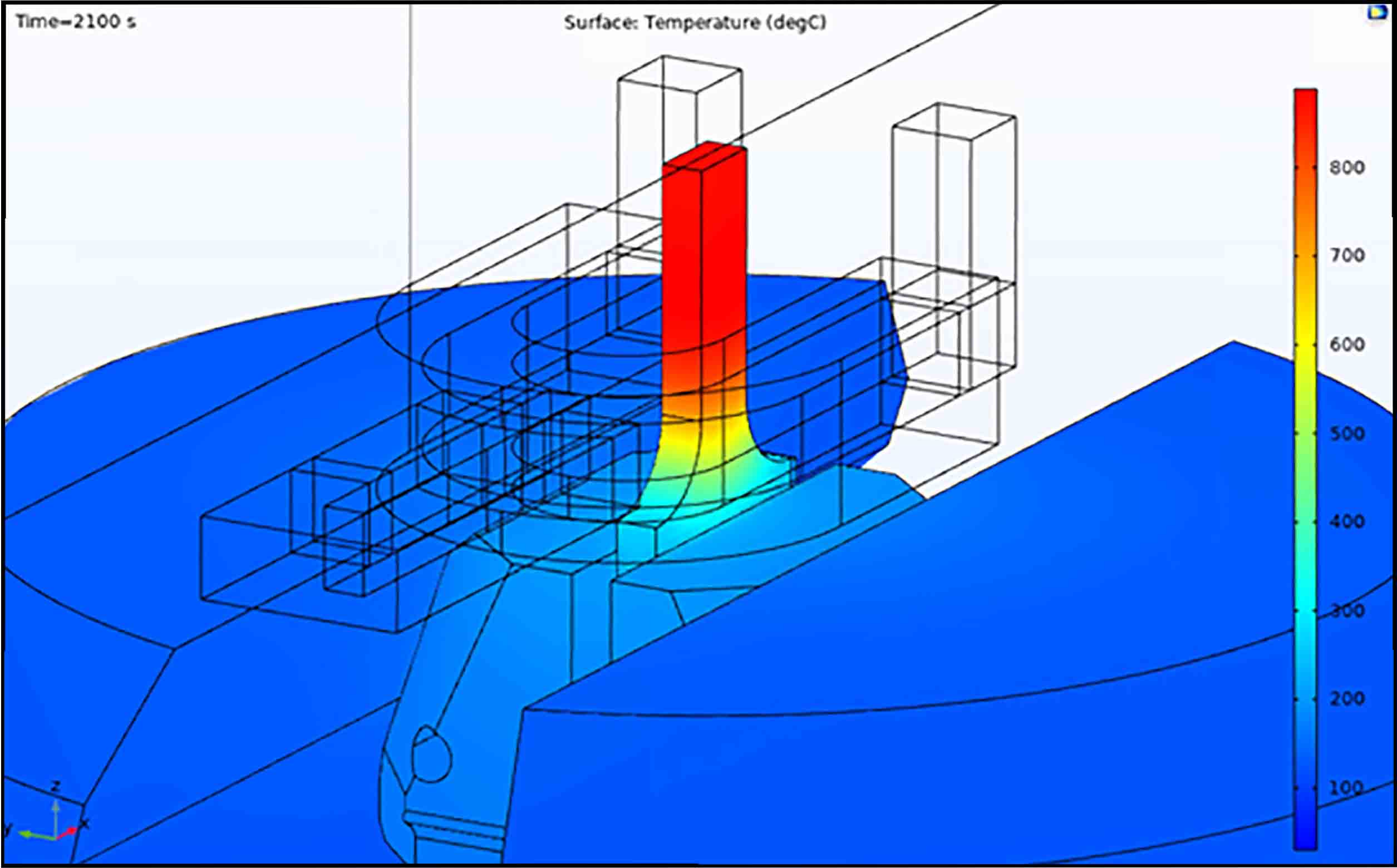
Evolving standards for additive manufactured materials are creating increased demand for small specimen testing at high temperatures. Learn how MTS and TRUMPF used multiphysics simulation to predict performance of grip and heating coil designs prior to building physical prototypes for TMF testing of additive manufactured materials.
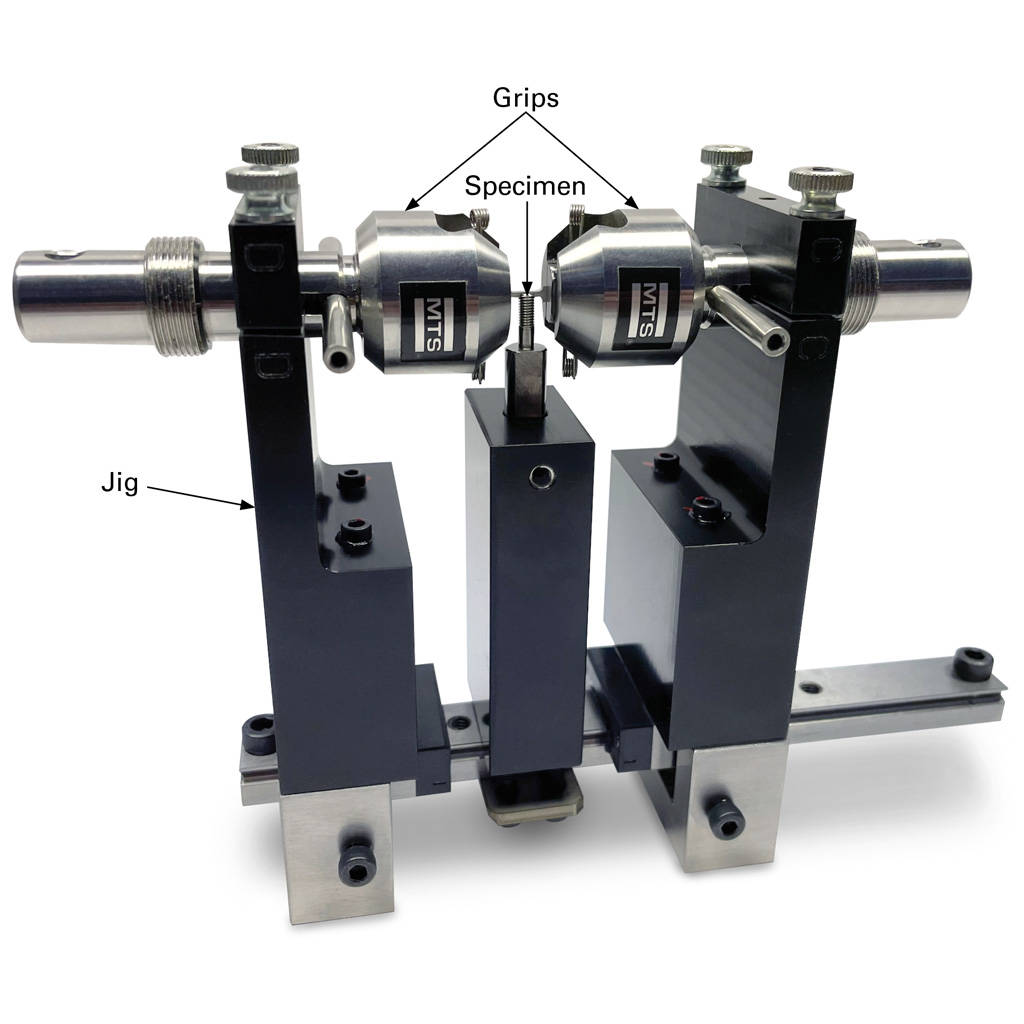
TMF Simulation Overview
Although MTS had already developed a patented grip for small specimen testing with 2.2 kN static and 1.1 kN dynamic load capacity for tensile and fully reversed fatigue applications respectively, this application required more load capacity. For this simulation, the proposed solution consisted of a mechanical grip rated at 5 kN in fully reversed fatigue loading and an open fork style induction coil.
Simulation Requirements
The multiphysics simulation characteristics included:
- Ability to deploy 2D and 3D simulations depending on the geometry of specimen and coil
- Electromagnetic field of the induction coil typically simulated as a frequency domain problem
- Thermal field inside the specimen could be simulated either as stationary or transient
- Thermal and magnetic fields could be coupled via temperature dependent material properties such as electrical conductivity, relative permeability, thermal conductivity, specific heat capacity
- Consideration of heat transfer via radiation, convection, and conduction
- Consideration of end effects due to gripping of specimen ends that attach to potentially water-cooled grips
Additional specific requirements for the heating application:
- Maximum achievable temperature: 900°C
- Ramp rates for heating and cooling: 30 K/s
- Uniform temperature distribution across the gage length: within 10 K
Simulation Results
With this simulation MTS and TRUMPF achieved the following results:
- Temperature up to 900°C
- Heating rates up to 30 K/s
- Cooling rates were strongly dependent on temperature values at grips
- Delta T across the gage length was 14.8 K, better uniformity could be achieved through additional coil design iterations
- Fork-like coil with open front met most heating and all accessibility requirements
Conclusion
Simulation is an efficient, low-cost way to evaluate proposed grip and heating coil designs before building physical prototypes. MTS and TRUMPF can use model-based design to identify areas of risk and improve component designs for TMF testing of additive manufactured materials.