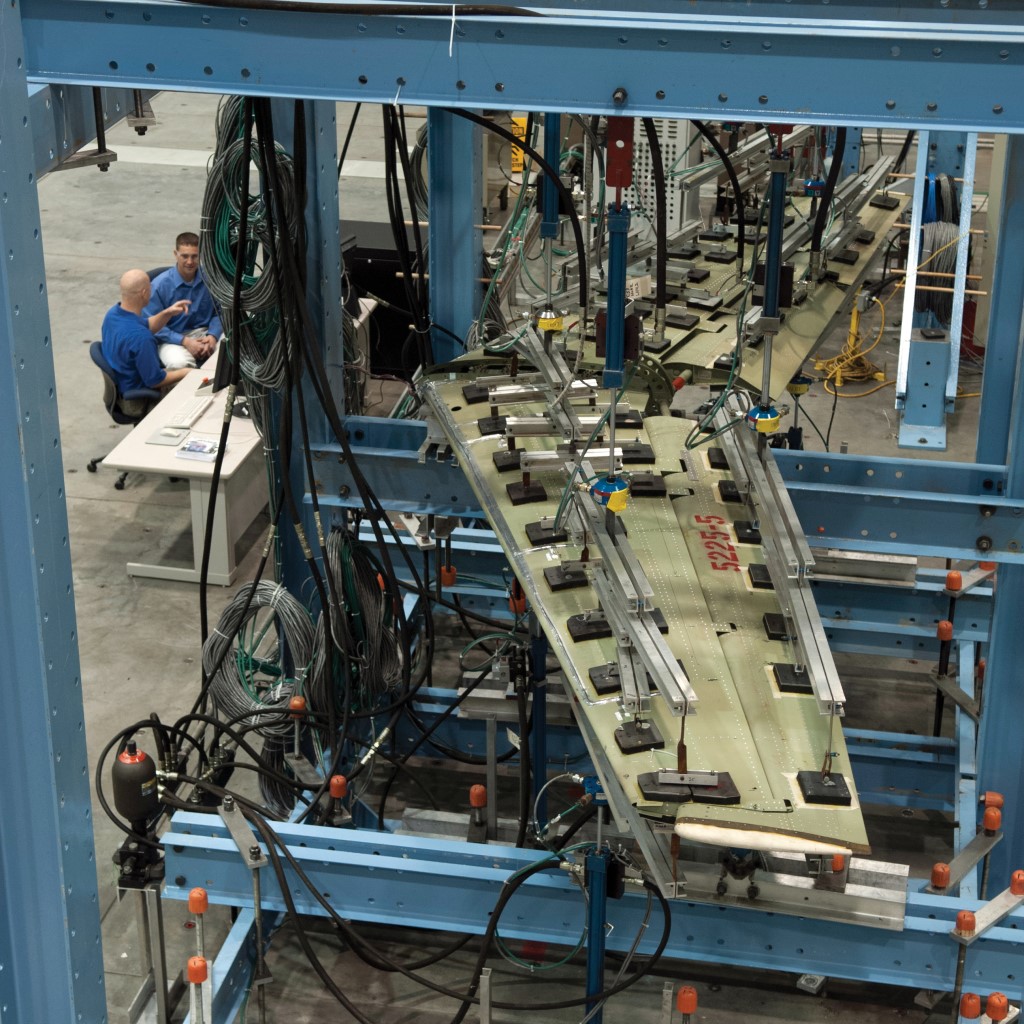
All aerospace test programs feel pressure to reduce their costs. To apply such measures, many test labs attempt to save money on setup details that appear to have little impact on overall quality of testing.
In reality, cutting costs on setup might cost you more over the long term. For example, too much time and money are at stake to cut corners on load cell configuration, calibration validation, cable quality and other essential details.
Equally important, a quality setup must be in place before you can fully leverage the most advanced test-accelerating tools available through the latest software. Such tools can help you operate as efficiently and cost-effectively as possible over the long term, equipping you to successfully compete on the global stage.
5 BEST PRACTICES FOR ENSURING A QUALITY TEST SETUP
1. USE DUAL-BRIDGE LOAD CELLS
Your control system only knows what it is told. If you have only a single-bridge load cell in place, and if that bridge or control amplifier has been incorrectly calibrated or is otherwise breaking down, the control system will not be capable of detecting the issue. Consequently, the incorrect load may be applied to the test specimen, risking damage to this multi-million-dollar structure. By using a dual-bridge load cell, you get a valuable integrity check on the applied load. The control system can verify the response it is seeing from the active feedback bridge by comparing it to the response from the second bridge.
2. PERFORM PERIODIC SHUNT VERIFICATION
Shunt verification provides a simple and precise means of ensuring proper calibration has been maintained throughout the life of a fatigue test, long after initial calibration. This procedure is performed by applying a shunt resistor to the load cell and measuring the response. A low-cost 5% tolerance resistor will perform sufficiently with the latest software packages that only need to measure and record the response of the load cell under the parameters set by the chosen calibration method. When using less precise resistors, however, be sure to use the same resistor for future verifications to ensure a valid verification check.
3. USE ONLY HIGH-QUALITY CABLES
Cables of limited quality can severely compromise the performance of your state-of-the-art servocontrols. For mV/V sensitivity calibration, it is common practice to use 8-wire cables. Such high-quality cables enable external excitation sensing at the actual sensor, along with the ability to shunt both the positive and negative sides of the bridge. This capability is critical to testing accuracy, because the excitation voltage is assumed by the control system software to be exactly the same as the requested value set by the user.
4. SIZE FOR SUCCESS
Bigger isn’t better when it comes to actuator, load cell and servovalve flow rate capacity. In fact, some customers calculate their flow rate and then double that number in an effort to operate faster. In truth, such practices do not speed testing. Rather, they threaten the stability of the control loop, which in turn compromises the efficiency and accuracy of your testing. That’s why it is critical that you select this equipment with capacities that closely match your requirements.
5. PROTECT THE SPECIMEN DURING TESTING
Today’s aircraft structural testing routinely involves dozens of actuators applying excessive loads across one-of-a-kind test articles. Without the proper measures in place for managing the release of energy, any power, mechanical or control failure can post a threat to the test article. The potential risks are simply too great not to invest in the load abort systems now available. Using a combination of hydraulic safety devices and control system and integrator limits, these systems effectively safeguard test articles from the significant amounts of energy present in the test rig.
After adhering to the best practices above, you will be equipped to test at your peak using the latest test acceleration software tools, including:
- Cross-Coupling Compensation (C3): This utility dramatically accelerates structural tests in highly coupled applications, improving accuracy without introducing additional strains on test articles.
- Profile Segment Optimization (PSO): PSO optimizes profile segment times by monitoring errors between command and feedback during transitions, and by adjusting transition times as needed to improve the next execution of the same profile.
- Calculations in the Loop Functionality: This capability allows advanced users to introduce sophisticated calculations into the control loop and run them at the system update rate, enhancing their ability to address complex structural test scenarios.
- Tightly integrated control and data acquisition: This configuration integrates the operation and analysis of hundreds of control channels and thousands of data acquisition channels into a single, unified interface.
- Best-in-class software: Only AeroPro™ software provides all the tools you need to achieve world-class aerospace structural testing. It includes automated tools for following the five best practices mentioned above, along with powerful capabilities — many of them exclusive — for accelerating your structural testing to new levels productivity and cost performance.