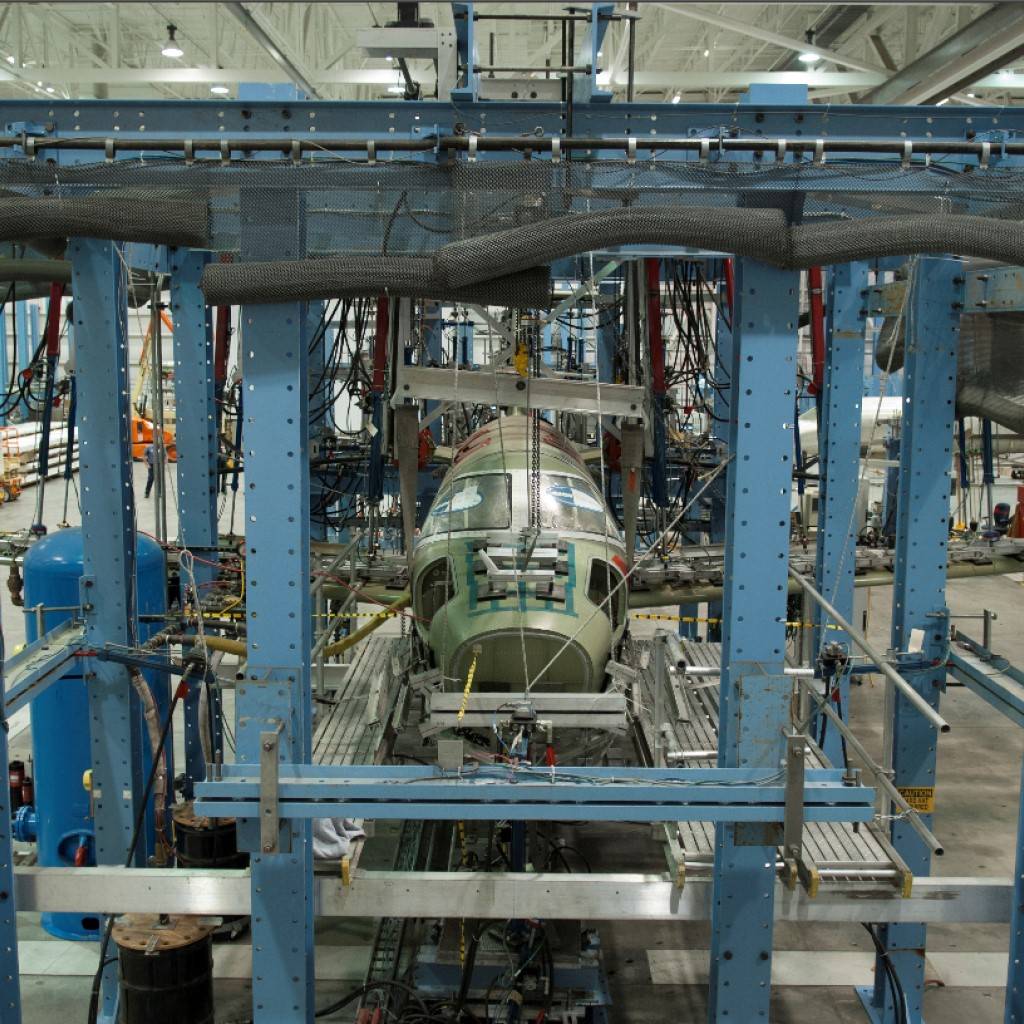
Setting up a full-frame aircraft tests is an increasingly complex, time-consuming exercise. One reason for this is a dramatic rise in data acquisition channels. Test teams are replicating real-world environments more accurately with more complex loading schemes. They are also trying to capture meaningful data from more of the test article to understand unanticipated failures more precisely, characterize load paths more accurately, and correlate these paths with models. These trends boost channel count.
Given the potential complexity of setup, it is vital for teams to work efficiently. The realities of the development schedule are also a factor. Upstream delays in the preparation of the test rig are common, and structural test teams are expected to make up the deficit during runtime. Often, the minute aerospace test teams commence actual testing they are already behind schedule.
To help teams overcome this growing challenge, MTS offers an unmatched portfolio of capabilities for accelerating complex structural test setup.
Leverage the power of integrated Control and DAC
The MTS portfolio comprises a tightly integrated structural testing solution, featuring MTS AeroPro software, MTS FlexTest® controllers and the MTS FlexDAC™ 20 data acquisition system.
The benefits of integration are significant. Teams can expect components that are engineered for compatibility. In addition, MTS offers the only truly synchronized solution in the industry, which eliminates data skew and removes a major source of uncertainty post-test. If potential issues arise as setup proceeds, system-level support enables faster resolution without the need to contact multiple vendors or coordinate a meeting among all of them to diagnose the problem. Integration also simplifies training because test engineers and operators only have one platform to learn for testing, data acquisition, and control.
Most important, AeroPro software creates a unified experience that makes setup much more efficient. Instead of using separate tools for each component, engineers can manage everything through one interface. This makes it quick and easy to perform automated setup, calibration and many other operations that affect thousands of control and DAC channels simultaneously.
Efficiently manage thousands of DAC channels
For data acquisition, setup for a full-frame aircraft may involve 10,000 or more strain gages, with all of the associated connection points and large bundles of cables.
MTS AeroPro software helps manage this complexity. Its user-friendly interface features a file-tree structure and drag-and-drop functionality, making it easy for test engineers to find everything they need. Setup wizards speed processes along, including the ability to import test parameters and hardware assignments, so engineers spend less time on setup and more time on the test.
AeroPro also supports Transducer Electronic Data Sheet (TEDS) sensors, which feature built-in memory chips for storing critical information such as the manufacturer, model, number, serial number and calibration data of virtually any transducer or strain gage. Full TEDS sensor support streamlines and improves the efficiency of sensor calibration, setup and verification. In large-scale structural tests, for example, these sensors are particularly helpful for automatic verification during troubleshooting. The alternative is spending time physically following cables from the DAC console to the specimen, one by one, until the error is located.
To maximize setup flexibility, MTS FlexDAC 20 systems are designed to distribute channels in any proportion across as many as eight test stations simultaneously. This exclusive capability helps test teams that need to run more tests with fewer channels without managing a separate box for every test — or letting unused channel capacity from one box sit idle because it can’t be dedicated to a different test.
While integration is important, many labs need the ability to incorporate DAC boxes from more than one manufacturer. MTS FlexDAC 20 systems can work alongside DAC units from other providers on the same test and the lab can manage all of them with AeroPro software. In other words, test teams can increase the channel count with MTS DAC systems while protecting investments in current systems. For even more flexibility, labs can mix and match the two types of FlexDAC chassis, the A32 and B24, in any combination, depending on the individual lab’s needs. Within AeroPro, it’s very easy to distinguish these platforms from one another.
Quickly and Easily Set up advanced, test-accelerating features
On the control side, mistakes in setup could cause specimen damage. To this end, AeroPro makes it relatively simple to set up advanced control features designed to accelerate testing while protecting the specimen from harm. These capabilities include:
- Cross-Coupling Compensation (C3 Performance) In highly coupled applications, where multiple actuators exert different forces on the same portion of a test article simultaneously, C3 Performance improves test efficiency by fully compensating for the influences of all actuators present. During setup, AeroPro eliminates the time-intensive task of manually inputting volumes of cross-coupling data by employing unit load survey to generate automated cross-coupling compensation coefficients.
- Forward Loop Optimization (FLO) This allows test engineers to improve and accelerate system performance during load control tests. It reduces test times through proprietary algorithms that improve channel stability and allow more aggressive tuning parameters. Essentially, FLO allows test teams to transition the test article between end levels more quickly without sacrificing accuracy. It can be activated within AeroPro with a single click.
- Profile Segment Optimization (PSO) PSO accelerates large, complex tests. It reduces the time required to optimize the segment transition times by monitoring errors between command and feedback during transitions, adjusting transition times as needed to improve the next execution of the same profile. Like FLO, PSO can be implemented very easily within AeroPro software.
One final way the MTS portfolio makes setup faster and easier is through automated calibration. Available for both FlexTest controllers and MTS FlexDAC 20 data acquisition units, this service helps test engineers perform traceable calibrations of large, complex aerospace structural test systems. Automated calibration methods are designed to quickly verify and document that controllers and data acquisition units are operating within stated performance specifications. They ensure the accuracy and traceability of test results while eliminating the introduction of manual errors.