Model 320 Tire-coupled Road Simulators
Apply vertical forces through vehicle tires to replicate the effects of real-world road loads on a wide range of vehicles. The original laboratory-based road simulator, today’s Model 320 combines linear electric or servohydrualic actuation, FlexTest controls and RPC or First Road Interact software to support applications ranging from end-of-line production quality to vibration transmissibility to durability.
Applications
- Durability
- Noise and Vibration Transmissibility
- NVH
- BSR
- Ride / Comfort Assessment
- Road Holding
- Production End-of-Line - Quality Control
Test Specimens
- Passenger Cars and SUVs
- Light Trucks
- Heavy Trucks
- Motorcycles
- All-Terrain Vehicles
- Off-highway Vehicles
- Motorsport Vehicles
Key Product Features
Durable / Reliable
Model 320 systems can perform in high duty cycle and high capacity testing for decades without a breakdown, requiring only limited routine maintenance and service.
Accurate / Repeatable Results
High-performance MTS servohydraulic or electric actuation delivers precise, high fidelity road load reproductions.
Efficient Operation
Versatile 793 controller software, renowned RPC software and easy-to-use First Road Interact software enhance the operational efficiency of both novice and expert lab personnel.
Versatile
The Model 320 product line can test all types of ground vehicles, including motorcycles, scooters and ATVs; passenger cars, light and heavy trucks; as well as train cars and off highway vehicles.
Model Comparison
First Road Systems
- Servohydraulic 4 post system
- 25 kN actuators with 6” displacement
- First Road Interact application software with tablet control
- Automatic Vehicle positioning system (X/Y)
- Applications: End-of-line Production Quality, BSR, Ride Comfort
Passenger Car & Light Truck Systems
- Electric or Servohydraulic 4-post actuators
- 25 kN – 50 kN actuators with 10” - 12” (254 mm – 305 mm) displacement
- Vehicle positioning systems (X/Y) available
- Optional actuators with a low flow mode for human-rated operation
- Environmental Chamber integration available
- Applications: Durability, Ride Comfort, NVH
Medium - Heavy Truck Systems
- Servohydraulic 4 – 8+ actuator system
- 100 kN – 250 kN+ Force capacity, with 12” actuator stroke (typical)
- Adjustable Static Support for high unsprung mass vehicles
- Multi- Pump Control Manager for multi HPU systems
- Vehicle stability fixtures available
- Applications: Durability
High-performance Vehicle Systems
- Servohydraulic 7-8 actuator systems
- 38 kN Vertical actuators with 10” (254mm) displacement
- Includes 3-4 down force actuators, used to simulate aerodynamic forces on test specimen
- Test Applications: Advanced Durability, Road holding (chassis setup)
Motorcycle Systems
- Servohydraulic 2/4 post systems
- 25 kN – 50 kN actuators with 6”- 16”+ (152 mm -406 mm+) displacement
- Vehicle stability control fixtures included
- Optional sliding wheel pans available to follow arcing suspension travel
- Applications: Durability, BSR, NVH
Technical Overview
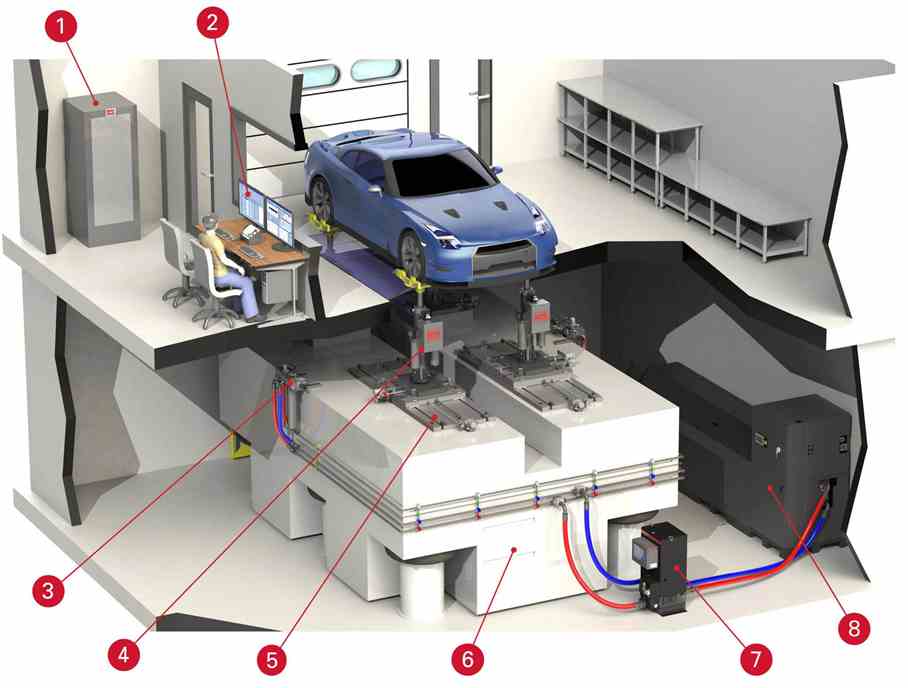
- FlexTest Controller with Uninterruptible Power Supply (UPS)
- PC workstation with FlexTest controller software (793) and RPC Pro application software
- Hydraulic distribution manifold with accumulators
- Model 248 Actuator with closed-coupled accumulators
- Vehicle Trackwidth & Wheelbase (X/Y) Positioning System
- Seismic Reaction Mass
- Hydraulic Service Manifold (HSM)
- SilentFlo Hydraulic Power Unit (HPU)
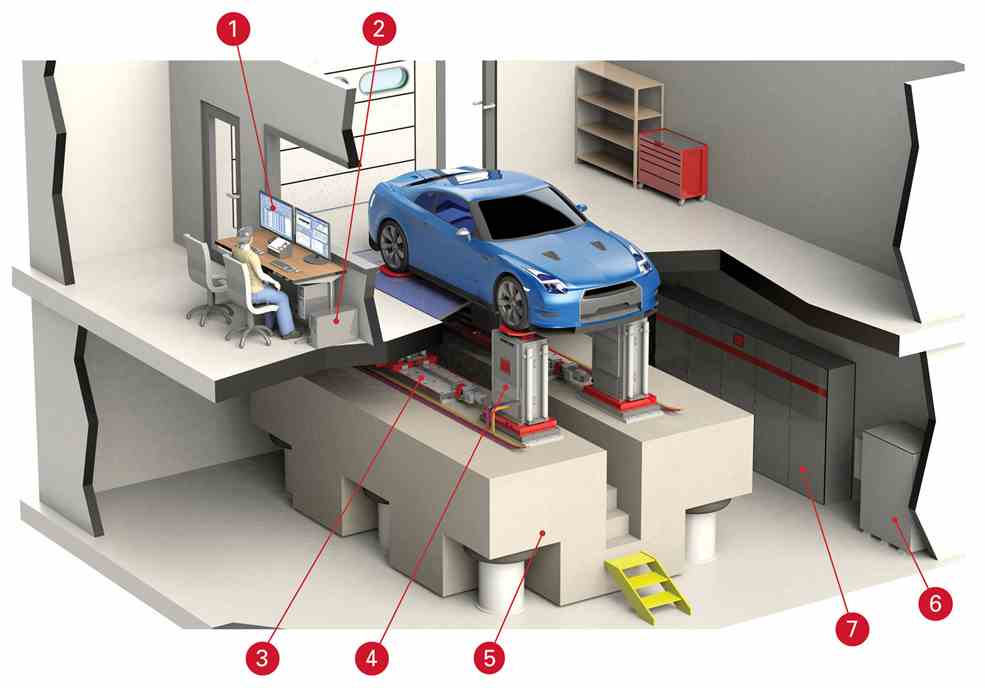
- PC workstation with FlexTest controller software (793) and RPC Pro application software
- FlexTest Controller with Uninterruptible Power Supply (UPS)
- Vehicle Trackwidth & Wheelbase (X/Y) Positioning System
- ePOST linear electric actuator with pneumatic static support
- Seismic Reaction Mass
- Drive Cabinet Chiller
- Electric Drive Cabinet
|
Units |
320.025 FR First Road System |
320.025 Small Car System |
320.035 Large Car System |
320.050 Light Truck System |
Typical GVW |
kg |
2500 |
2500 |
3500 |
5000 |
lbm |
5500 |
5500 |
7700 |
11000 |
|
Actuator Rated Force1 |
kN |
28 |
28 |
38.6 |
50 |
kip |
6.3 |
(6.3 |
8.7 |
11.2 |
|
Dynamic Double Amplitude Displacement |
mm |
152 |
254 |
254 |
254 |
in |
6 |
10 |
10 |
10 |
|
Servovalve |
lpm |
2 x 57 |
2 x 57 |
340 |
340 (optional 680) |
gpm |
2 x 15 |
2 x 15 |
90 |
90 (optional 180) |
|
Performance (@ Wheel Pan) 2 |
|
|
|
|
|
Maximum Velocity |
m/s |
1.5 |
1.5 |
3.6 |
2.7 (optional 5.4) |
in/s |
59 |
59 |
142 |
106 (optional 213) |
|
Maximum Acceleration (Sinusoidal) |
g |
19.5 |
20 g |
24.5 |
21 |
@ assumed unsprung (dynamic) mass |
kg |
40 |
40 kg |
60 |
100 |
lbm |
88 |
88 |
132 |
220 |
|
@ assumed sprung (static) mass 4 |
kg |
750 |
750 kg |
1050 |
1500 |
lbm |
1653 |
1653 |
2315 |
3307 |
|
Recommended Hydraulic Supply 5 |
|
505.30 |
505.30 |
505.90 |
505.150 (optional 2x 505.150) |
Operating System Pressure |
bar |
210 |
210 |
210 |
210 |
psi |
3000 |
3000 |
3000 |
3000 |
|
Wheel Pan Diameter (round) 6 |
mm |
635 |
432 |
432 |
432 |
in |
25 |
17 |
17 |
17 |
Note: Mass assumptions shown are per corner.
Note: Performance specifications are based on assumptions for sprung and unsprung masses.
Note: Specifications are subject to change without notice.
- Rated force is determined at 2800 psi differential across the piston.
- Performance is measured at the wheel pan. Performance is not representative of spindle motion. For performance estimations at the spindle see below tire magnification factors (valid near wheelhop frequency):
- Passenger car: 2.0 to 2.5
- Truck: 1.25 to 1.5
- Static Support is used to zero out the mean load resulting from the sprung and unsprung masses so that actuator force is available solely for acceleration forces.
- Vehicle weight distribution for the 320.025 through 320.050 systems is taken as 60/40 Front/Rear. The 320.100 and 320.200 systems are distributed 40/60 Front/Rear. Worst case for all systems is for an actuator supporting 30% of total vehicle weight.
- HPS sizing assumes average flow requirement is 25% of peak flow and HPU is operating at 50 Hz. This is only an estimate. More exact requirements can be determined by analyzing customer’s drive files, if available.
- Custom wheelpan solutions are available upon request.
|
Units |
320.100 Medium Truck System |
320.200 Heavy Truck System |
320.250 Heavy Truck System |
Typical GVW |
kg |
10000 |
20000 |
25000 |
lbm |
22000 |
44000 |
55000 |
|
Actuator Rated Force 1 |
kN |
100 |
100 (front) |
160 (front) |
kip |
22 |
22 (front) |
35 (front) |
|
kN |
|
160 (rear) |
213 (rear) |
|
kip |
|
35 (rear) |
48 (rear) |
|
Dynamic Double Amplitude Displacement |
mm |
254 |
254 |
254 |
in |
10 |
10 |
10 |
|
Servovalve |
lpm |
680 |
680 (front) |
950 (front) |
gpm |
180 |
180 (front) |
250 (front) |
|
lpm |
|
950 (rear) |
1515 (rear) |
|
gpm |
|
250 (rear) |
400 (rear) |
|
Performance (@ Wheel Pan) 2 |
|
|
|
|
Maximum Velocity |
m/s |
3.4 |
3.4 (front) |
3.0 (front) |
in/s |
134 |
134 (front) |
118 (front) |
|
m/s |
|
3.0 (rear) |
3.6 (rear) |
|
in/s |
|
118 (rear) |
142 (rear) |
|
Maximum Acceleration (Sinusoidal) |
g |
29 |
21 (front) |
28.5 (front) |
g |
|
20 (rear) |
18 (rear) |
|
@ assumed unsprung (dynamic) mass |
kg |
120 |
180 (front) 3 |
250 (front) 3 |
lbm |
265 3 |
397 (front) 3 |
551 (front) 3 |
|
kg |
|
350 (rear) 3 |
450 (rear) 3 |
|
lbm |
|
772 (rear) 3 |
992 (rear) 3 |
|
@ assumed sprung (static) mass 4 |
kg |
3000 3 |
6000 3 |
7500 3 |
lbm |
6614 3 |
13228 3 |
16535 3 |
|
Recommended Hydraulic Supply 5 |
|
2 x 505.150 (2 axle) |
2 x 505.180 (2 axle) |
3 x 505.180 (2 axle) |
|
|
3 x 505.150 (3 axle) |
3 x 505.180 (3 axle) |
|
Operating System Pressure |
bar |
210 |
210 |
210 |
psi |
3000 |
3000 |
3000 |
|
Wheel Pan Diameter (round) 6 |
mm |
635 |
635 (front) 7 |
635 (front) 7 |
in |
25 |
25 (front) 7 |
25 (front) 7 |
|
mm |
|
1016 (rear) 7 |
1016 (rear) 7 |
|
in |
|
40 (rear) 7 |
40 (rear) 7 |
Note: Mass assumptions shown are per corner.
Note: Performance specifications are based on assumptions for sprung and unsprung masses.
Note: Specifications are subject to change without notice.
- Rated force is determined at 2800 psi differential across the piston.
- Performance is measured at the wheel pan. Performance is not representative of spindle motion. For performance estimations at the spindle see below tire magnification factors (valid near wheelhop frequency):
- Passenger car: 2.0 to 2.5
- Truck: 1.25 to 1.5
- Static Support is used to zero out the mean load resulting from the sprung and unsprung masses so that actuator force is available solely for acceleration forces.
- Vehicle weight distribution for the 320.025 through 320.050 systems is taken as 60/40 Front/Rear. The 320.100 and 320.200 systems are distributed 40/60 Front/Rear. Worst case for all systems is for an actuator supporting 30% of total vehicle weight.
- HPS sizing assumes average flow requirement is 25% of peak flow and HPU is operating at 50 Hz. This is only an estimate. More exact requirements can be determined by analyzing customer’s drive files, if available.
- Custom wheelpan solutions are available upon request.
- External vehicle restraints are required.
|
Units |
320e.050 |
Peak Dynamic Force (peak dynamic force electric only with cooling) |
kN |
42 |
lbf |
9400 |
|
Continuous Dynamic Force (electric motor only with cooling) |
kN |
16 |
lbf |
3600 |
|
Continuous Static Force (pneumatic only) |
kN |
10 |
lbf |
2250 |
|
Peak Combined Force (peak dynamic force and continuous pneumatic force) |
kN |
52 |
lbf |
11700 |
|
Continuous Combined Force (continuous dynamic force and continuous static force) |
kN |
26 |
lbf |
5875 |
|
Velocity |
m/sec |
4 |
in/sec |
157 |
|
Stroke |
mm |
250 |
in |
10 |
|
Actuator Height with Standard Wheelpan |
cm |
120.65 |
in |
47.5 |
|
Maximum Acceleration 1 |
g |
30 |
Digital Encoder Accuracy |
µ |
0.005 |
Noise Level – Typical |
dbA |
<55 |
Emergency Stop Method |
MTS SoftStop or HardStop Shutdown |
|
Wheelbase Adjust |
Electromagnetic Clamping (60 TONS) Electromechanical Positioning |
|
Bearing Material |
Air Bearings - Maintenance Free |
|
Facility Requirements 2 |
V |
480 |
A |
400 @ 460V |
|
Air Supply 3 |
PSI |
100 |
BAR |
7 |
|
CFM |
60 |
|
Recommended Reaction Mass |
t |
200 |
Note: Higher pneumatic and combined force available on request
Note: Specifications subject to change
- 40 kg unsprung mass used for specifications
- MTS can supply transformers for voltages other than 220V III-Phase
- Air supply system must be adequately sized for continuous operation providing above specified flow at a pressure consistently above 5.2 bar (75 psi)
|
Units |
320 Racing Vehicle System |
Actuator Rated Force 1 |
kN |
38.6 |
kip |
8.7 |
|
Adjustable Downforce |
kN |
15 – 20 |
kip |
3.5 – 4.5 |
|
Adjustable Upforce |
kN |
10.2 – 15.1 |
kip |
2.3 – 3.4 |
|
Dynamic Double Amplitude Displacement |
|
|
Actuator |
mm |
254 |
in |
10 |
|
Adjustable Downforce |
mm |
300 – 198 |
in |
12 – 7.8 |
|
Servovalve |
lpm |
950 (front) |
gpm |
250 (front) |
|
lpm |
1515 (rear) |
|
gpm |
400 (rear) |
|
Performance (@ Wheel Pan) 2 |
|
|
Actuator Maximum Velocity |
m/s |
3.6 |
in/s |
142 |
|
Actuator Maximum Acceleration (Sinusoidal) |
g |
24 |
@ assumed unsprung (dynamic) mass |
kg |
60 |
lbm |
132 |
|
@ assumed sprung (static) mass 4 |
kg |
1050 |
lbm |
2315 |
|
Recommended Hydraulic Supply 5 |
|
505.150 |
|
5 x 505.180 (3 axle) |
|
Operating System Pressure |
bar |
210 |
psi |
3000 |
|
Wheel Pan Diameter (square) 6 |
mm |
457 |
in |
18 |
Note: Mass assumptions shown are per corner.
Note: Performance specifications are based on assumptions for sprung and unsprung masses.
Note: Specifications are subject to change without notice.
- Rated force is determined at 2800 psi differential across the piston.
- Performance is measured at the wheel pan. Performance is not representative of spindle motion. For performance estimations at the spindle see below tire magnification factors (valid near wheelhop frequency):
- Passenger car: 2.0 to 2.5
- Truck: 1.25 to 1.5
- Static Support is used to zero out the mean load resulting from the sprung and unsprung masses so that actuator force is available solely for acceleration forces.
- Vehicle weight distribution for the 320.025 through 320.050 systems is taken as 60/40 Front/Rear. The 320.100 and 320.200 systems are distributed 40/60 Front/Rear. Worst case for all systems is for an actuator supporting 30% of total vehicle weight.
- HPS sizing assumes average flow requirement is 25% of peak flow and HPU is operating at 50 Hz. This is only an estimate. More exact requirements can be determined by analyzing customer’s drive files, if available.
- Custom wheelpan solutions are available upon request.
Service and Support
Our experts are here to help keep you up and running.
Related Products, Parts or Accessories
RPC® Connect Software
First Road Interact Software
FlexTest® Controllers
SilentFlo™ 515 & 525 Hydraulic Power Units (HPU)
Multi-Pump Control Manager
TestSuite Software
Looking for more products?
Go to Solution FinderContact An MTS Rep Today
Ready for a quote or need more information? We're here to help. Request A QuoteResources
Next-generation RPC Connect Software Now Available!
Josh Hernandez marks the beginning of the RPC Connect era in…
Introducing FlexTest Elite Performance Controllers
Increase channel count, system rate and computational cap…
Factors to Weigh When Considering Electric or Hydraulic Test Systems
Guidance on damper test systems and road simulators
The Origins of RPC with Dr. Glen Grenier
Q&A with the durability testing pioneer on the rise of R…
The Case for Calibration
MTS calibration can help increase data validity and lab effi…