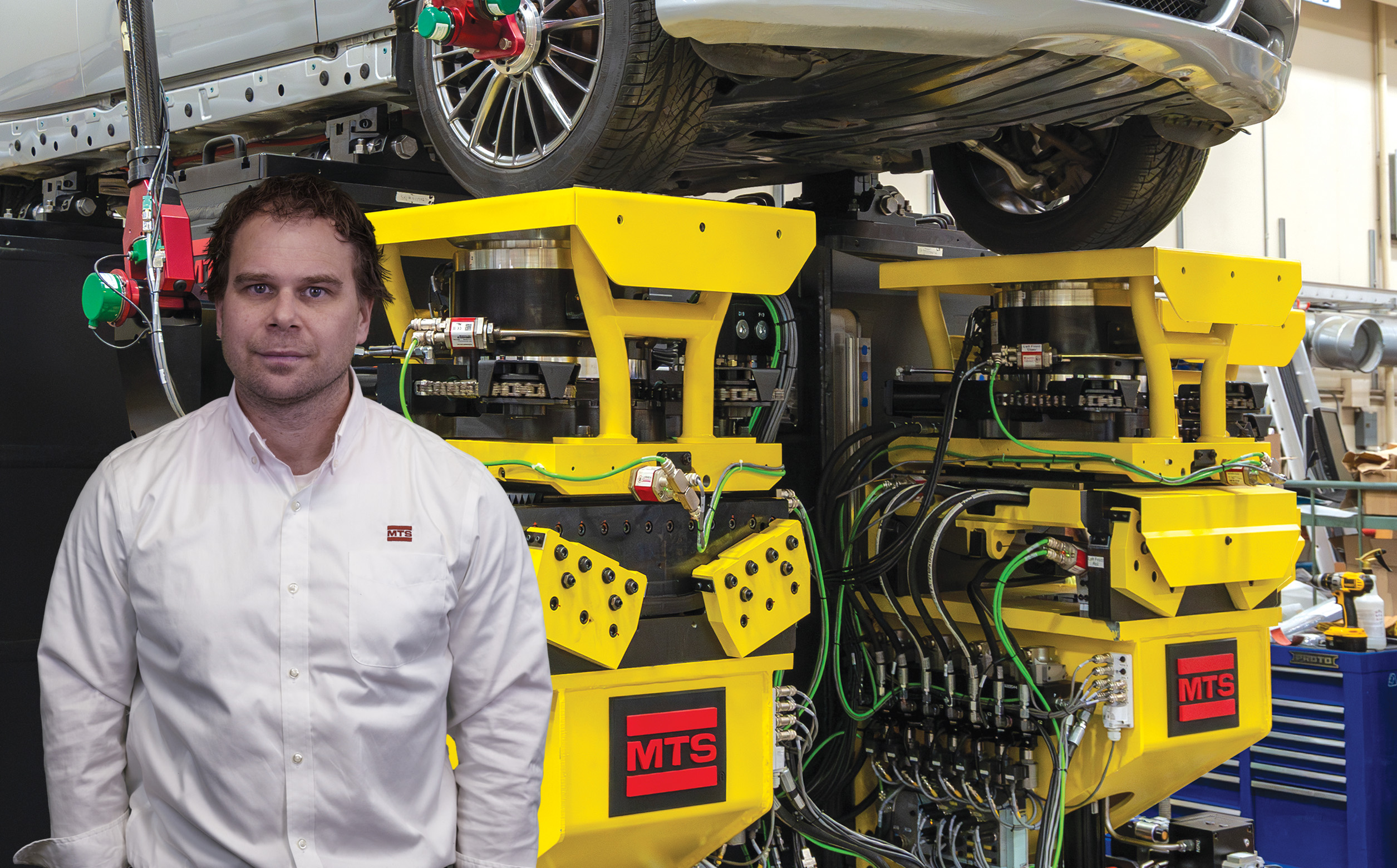
A: One key adaptation is the recent launch of our next-generation Passenger Car Kinematic & Compliance (K&C) Deflection Measurement System. The redesign of our K&C platform was born of an initiative to increase performance capabilities using a more cost-competitive system design while matching the data accuracy and operational efficiency of our legacy systems. Embarking on the third-generation redesign also allowed us to address three decades of customer feedback and enhance performance in many areas. The resulting Gen 3 K&C machine leverages the same superior independent platform motion concept as our legacy models to deliver optimum test flexibility and features an array of mechanical improvements that make it ideal for characterizing fast evolving electric vehicle suspensions and chassis.

Q: What is the most significant mechanical difference between the legacy and Gen 3 K&C design?
A: The biggest improvements to our Gen 3 K&C machine stem from a new tower-based design. Requiring far less steel than the legacy, lateral beam concept, the tower structure is smaller, lighter, easier to install and more cost-competitive to manufacture. It allows vertical forces to be input and reacted from the vehicle directly into ground, improving stiffness and effectively increasing resonance free motion and measurement frequency capabilities to 10Hz. As with the legacy design, the new tower is available in four corners to test complete vehicles, two corners to test a single axle, and a single corner for quarter-car testing early in development.
The new tower structure also provides a fixed mounting location for the wheel motion sensors (WMS) with respect to the platform, so operators no longer need to worry about re-positioning them after trackwidth or wheelbase changes. This change prevents accidental breakage that sometimes occurred in previous designs when a WMS was not re-positioned correctly.
The new tower design also prompted the redesign of vehicle clamping solutions. Engineered to interface with the top surface of the tower structure and the test vehicle, these simplified mechanical clamps are an improvement over the previous magnetic design, which were bulky and sensitive to dirt and debris.
Q: What features of the Gen 3 K&C system were engineered to enhance the development of electric vehicles?
A: The Gen 3 K&C system features an array of mechanical innovations to accommodate the new geometries and kinematics of electric vehicles:
Re-engineered steer input assemblies with a new linear-to-rotary design provide backlash-free operation and increased steer angle, and steer torque needed for characterizing electric vehicles.
New carbon wheel motion sensors (WMS) provide higher data accuracy at high frequencies in both absolute and relative modes and enable travel and measurement across a larger range of wheel motion.
Redesigned trackwidth and wheelbase components and VIM (Vehicle Inertial Measurement) fixtures provide the flexibility needed to accommodate a wider array of vehicles, including micro-cars, passenger cars, and large SUVs. Additionally, we have incorporated the ability to measure static vehicle alignment data and quickly measure vehicle inertia without a fixture with only a small reduction in accuracy.
And finally, the new highly adjustable body clamping provides varying degrees of adjustability to more readily engage evolving electric vehicle chassis designs.
Q: How did the redesign affect K&C system application software?
A: Our K&C system users really appreciate the built-in flexibility provided by our scripting-based software solution. For our next generation redesign, we improved this software by fixing several bugs with data acquisition and stability, simplified the use of multiple monitors, and added features such as multi-degree of freedom acceleration compensation to improve load measurement accuracy at high frequencies.
Q: What types of tests can be conducted on the new G3 K&C machine?
A: The new Passenger Car K&C system performs the full spectrum of standard kinematics and compliance deflection measurement applications, including suspension and steering characterization, benchmarking and target setting, model verification, evaluating design changes, and diagnosing problems. It can also be used for performing highly accurate mass and inertia measurements, RPC file playout, and maneuver decomposition (cornering study). With 10Hz motion capabilities, the new Gen 3 can also be integrated into a real-time Mechanical Hardware-in-the-Loop (mHIL) simulation for performing high-fidelity suspension subsystem tuning.
Q: Will data from the redesigned next-generation K&C correlate with data gained from legacy machines?
A: Yes, we performed comparative testing of the two generations of machines and found equivalency variation of less than machine-to-machine of the prior generation. This is because both generations employ the same strain-based load cell design, which offers superior measurement capability for both static DC measurements and at frequency. Additionally, all MTS K&C systems – first, second and third generation – are subject to system-level calibration in the factory to ensure optimal measurement accuracy. This involves 6DOF calibration at each corner (Fx, Fy, Fz, Mx, My, Mz), followed by a four-corner system alignment.
Q: How has MTS improved the safety of the new Gen 3 K&C machine while simultaneously improving efficiency?
A: MTS has incorporated a safety rated control system with defined modes for both standard operation and setup. These modes are adjustable via a removable key switch located near the control PC. The setup mode restricts the maximum speed of the system to reduce the likelihood of injury and enables safe position monitoring the platforms. During setup, a new hand-held control pendant enables operators to work safely near a K&C machine under live hydraulic power, allowing jogging of individual axes for installation of vehicles and components such as spindle adaptors.
Q: How difficult is it to service and maintain a system as complex and sensitive as the K&C?
A: First, MTS K&C machines are robust and last a long time: our first installation was in 1998, and this machine is still in operation today! Second, the K&C does not require a significant amount of maintenance. And third, over the years, we have built a large K&C customer base around the world with a highly trained service team who work frequently on the K&C. In addition to this global service team, we maintain a core design team focused on the K&C product at our Eden Prairie, Minnesota headquarters. Together, this combined team ensures strong K&C customer support worldwide.
Q: In summary, what should we take away from this discussion about the new Gen 3 K&C, when will the new models be available, and how can we learn more?
A: By applying an array of mechanical and electrical innovations to enhance efficiency and expand K&C system utility, we took an excellent product and made it better. Data from the new Gen 3 K&C systems correlates exceedingly well with legacy machines, offering best-in-market data accuracy with increased performance specifications. The new machine continues to offer the highest flexibility and capability with a superior independent platform motion concept. Since a similar footprint system has been maintained, the new systems will fit in existing laboratories, allowing existing machines a straightforward upgrade path.
The Gen 3 Passenger Car K&C machine is available now. I welcome anyone interested in learning more to contact their local MTS sales representative or visit the MTS website and submit an online request for more information.