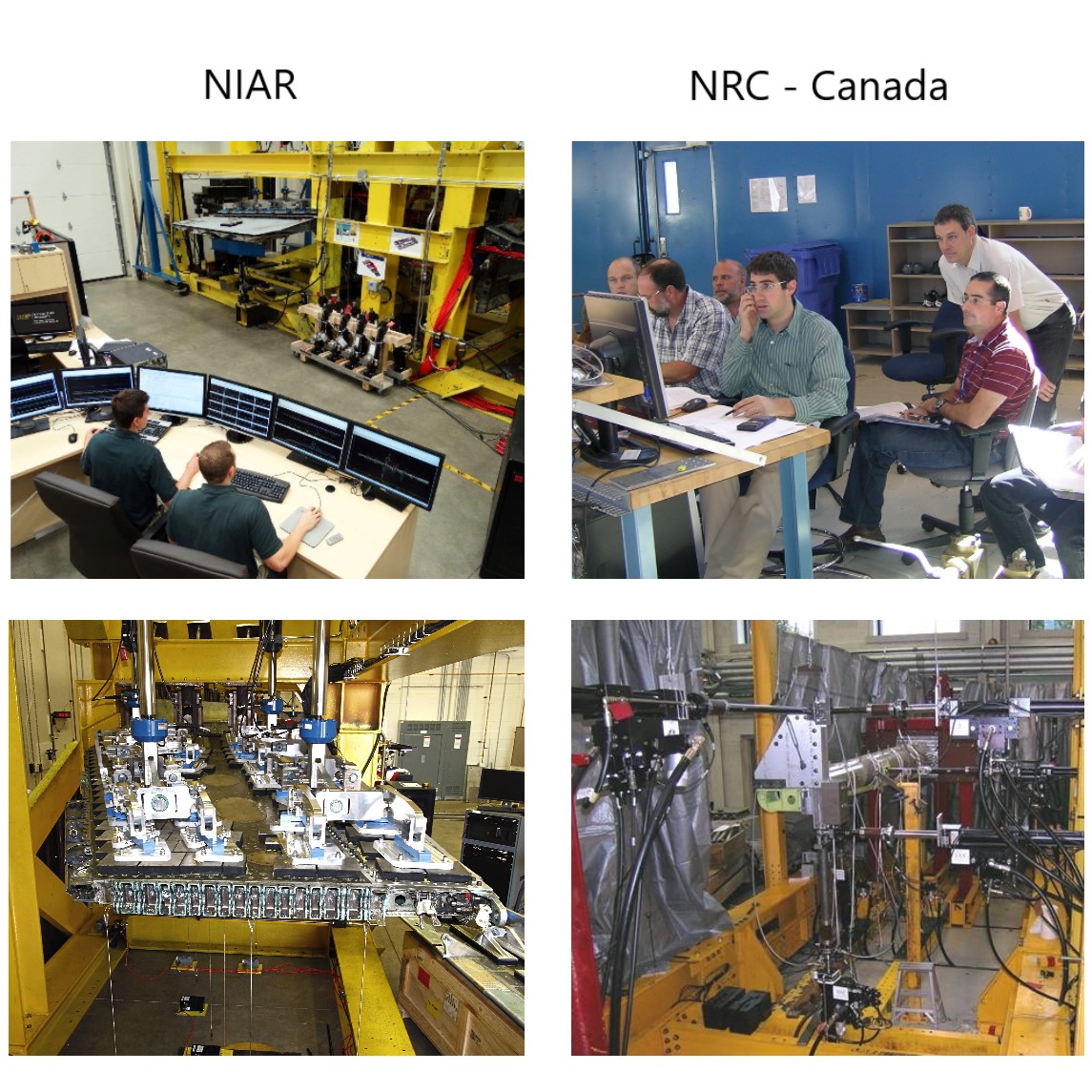
I banchi di prova strutturali su larga scala caratterizzati da schemi di attuazione altamente incrociati presentano sfide uniche per gli ingegneri di prove aerospaziali. In queste complesse configurazioni, più attuatori esercitano contemporaneamente forze diverse sulla stessa porzione di un articolo di prova, aumentando il rischio di errori che possono compromettere i programmi di prova e ritardare i programmi di sviluppo.
Uno strumento per ridurre tali errori, migliorando così la velocità e l'efficienza dei test, è C3Performance, un'utilità del software di controllo e acquisizione dati MTS AeroPro™. Conosciuto anche come C-cubed, C3Performance consente ai team di prova di gestire in modo efficace schemi di attuazione altamente incrociati, senza dover dedicare tempo extra alle pianificazioni delle prove per risolvere numerosi arresti e interblocchi ricorrenti.La tecnica di compensazione dell'accoppiamento incrociato di
C3 Performance è stata sviluppata congiuntamente da esperti del National Research Council of Canada (NRC) e di MTS Systems Corporation. Oggi è una parte standard del protocollo di prova presso l'NRC, il laboratorio di prove strutturali su vasta scala del Canada, dove Andre Beltempo lavora come ingegnere di prove strutturali.
"In genere, usiamo C-cubed per tutte le prove", ha affermato Beltempo. "Con le prove di fatica su vasta scala, si nota un'interazione dell'attuatore molto complessa. Proprio per questo ne abbiamo bisogno".
Il team di Beltempo ha recentemente utilizzato C3 Performance durante una dimostrazione tecnologica per un importante produttore di elicotteri. Il programma di prove di fatica e statiche si è concentrato su un'asse di coda in composito, fabbricata utilizzando tecniche di produzione avanzate. Le prove erano identiche a quelle che sarebbero state utilizzate per certificare la parte per i requisiti FAA di tolleranza di vita sicura.
"Se si osserva il raccordo dell'interfaccia della scatola del cambio del rotore della coda, i due attuatori posteriori caricano entrambi sullo stesso raccordo", ha affermato Beltempo. "La compensazione dell'accoppiamento incrociato aiuta a ridurre al minimo gli attriti tra gli attuatori".
La prova ha coinvolto sei attuatori e quattro milioni di end point, attivi durante la notte per circa 125 giorni, con una frequenza media di 0,5 Hz. Secondo Beltempo, questa velocità di prova sarebbe stata impossibile senza C3Performance.
"Non avremmo potuto farlo così rapidamente senza la compensazione dell'accoppiamento incrociato", ha detto. "Per un test notturno, avremmo dovuto eseguire i livelli finali a metà della velocità per non doverci preoccupare di arresti non presidiati. Il nostro approccio standard per qualsiasi prova di fatica consiste nel regolare il test, applicare C-cubed e ricalibrarlo subito. Non ho mai visto un aumento di velocità inferiore a un fattore di due per un articolo rigido”.
Un altro aspetto che Beltempo apprezza di C3Performance è la sua facilità d'uso complessiva. Poiché gli operatori di prove possono configurarlo autonomamente, C3Performance aiuta i laboratori a guadagnare ancora più tempo.
"Il fatto che sia così autonomo, mi dà la possibilità di concentrarmi su compiti più importanti", ha detto Beltempo. "Se dovessi sederti lì e calcolare tutti i coefficienti da solo, sarebbe diverso. Ma basta fare clic su un pulsante e succede. È un vero miglioramento della produttività".
Mentre è naturale per l'organizzazione che ha contribuito a sviluppare C3Performance applicarlo a ogni prova di fatica come questione di protocollo, anche altri laboratori stanno scoprendo il potenziale di risoluzione dei problemi di questa potente utilità.
Per il dott. Waruna Seneviratne, direttore tecnico del laboratorio Composites and Advanced Materials presso il National Institute for Aviation Research (NIAR) della Wichita State University, il problema era la privazione del sonno.
"Stavamo eseguendo una prova di fatica con una combinazione molto particolare di fissaggio e attuazione personalizzati e avevamo un programma di test molto aggressivo", ha affermato Seneviratne. "Il test è stato eseguito durante la notte e abbiamo riscontrato un numero elevato di trigger di limite di errore fastidiosi. Il nostro team è dovuto scendere in laboratorio nel cuore della notte per vedere cosa stava causando l'arresto dei test e per riavviare il test. Eravamo in ritardo".
Il test era concentrato sulla valutazione della resistenza alla fatica delle strutture composite del velivolo F/A-18 Hornet, molti dei quali si stanno avvicinando alla dismissione. Poiché la sostituzione del velivolo non sarà pronta fino al 2019, la Marina degli Stati Uniti deve prolungare in sicurezza la vita utile delle vecchie strutture composite del velivolo.
La ricerca di Seneviratne ha determinato con successo che le giunture legate tra composito e titanio alla radice dell'ala avevano ancora una grande quantità di vita. Il nuovo test ha ampliato lo studio per includere l'intera ala interna, che è dotata di una pelle composita. L'articolo di prova include l'ala interna, il flap del bordo d'uscita e la fusoliera centrale, nonché il flap del bordo d'attacco simulato e l'ala esterna. Il team di ricerca del NIAR ha dovuto costruire un elaborato impianto di perforazione in acciaio ad alta resistenza con attrezzature progettate su misura e applicare carichi significativi per ricreare manovre aggressive.
"C'erano differenze significative tra la corsa e i carichi attraverso gli attuatori, che rappresentavano una probabile fonte di errori", ha detto. "Avevamo bisogno di un modo per ridurre al minimo i falsi arresti, quindi abbiamo iniziato a esaminare meglio la questione".
L'ingegnere di ricerca Travis Cravens, membro del team di Seneviratne, ha gestito l'installazione e la configurazione di C3Performance. Gli ingegneri di sistema e applicativi di MTS hanno completato l'installazione e la formazione in meno di un giorno e il laboratorio ha visto i risultati quasi immediatamente.
"Alla fine del primo giorno stavamo correndo il 20% più velocemente senza modifiche meccaniche al banco di prova", ha detto Cravens. "Imparare a usare e configurare C3Performance è stato facilissimo; tutto avviene all'interno del software. È sufficiente creare una matrice di accoppiamento incrociato applicando un carico unitario su ciascun canale di carico, che rappresenta solo un passo in più per ciascun attuatore".
Per semplificare la configurazione delle prove, C3Performance elimina il compito dispendioso in termini di tempo di immettere manualmente i dati di accoppiamento incrociato utilizzando casi di carico unitari per generare coefficienti di compensazione dell'accoppiamento incrociato automatizzati. Seneviratne ha caratterizzato questo processo con un'analogia appropriata.
"È come avere un team di 20 persone che non si conoscono e che lavorano allo stesso progetto", ha detto. "I carichi unitari sono semplicemente un modo per presentare tutte queste persone l'una all'altra in modo che possano collaborare e lavorare in modo più efficiente".
Con qualche messa a punto in più, Seneviratne e Cravens sono stati in grado di aumentare il tasso di prova del 24 percento e ridurre significativamente il numero di arresti.
"Ha notevolmente migliorato le prestazioni del nostro test", ha affermato Cravens. "Con il monitoraggio del carico migliorato, è molto meno probabile che piccole perturbazioni nel feedback attivino limiti di errore, con conseguente minor numero di interruzioni del test. La riduzione dell'errore ci ha anche permesso di eseguire più segmenti all'ora”.
Prima di utilizzare C3Performance, il NIAR era in grado di raggiungere solo un massimo di 375 segmenti all'ora, con una media di 97 arresti e 55 interblocchi per blocco di prova. Con C3 Performance, questo è migliorato a 480 segmenti all'ora con una media di 51 arresti e 15 interblocchi.
"Il numero di arresti era un terzo di quello precedente, il che è stato un enorme guadagno per noi", ha detto Seneviratne. "Ciò ci ha permesso di eseguire il test durante la notte, alcune notti senza una sola interruzione. Sono fino a 10 ore di test che non avevamo prima, il che ci ha aiutato moltissimo con il nostro programma".
C3Performance ci ha permesso di risparmiare settimane di lavoro, consentendo al team di Seneviratne di fornire i risultati del test in tempo. Inoltre, la produttività del laboratorio è stata migliorata: il team è riuscito a operare con un programma più prevedibile e ha avuto più tempo da dedicare ad altri progetti. In qualsiasi laboratorio con risorse limitate, questo è un vantaggio importante.
"Sapere che avremmo potuto eseguire il test durante la notte ed essere sicuri di poter eseguire ispezioni e riparazioni durante il giorno ci ha permesso di aumentare l'efficienza del nostro percorso di prova", ha affermato Seneviratne. "Siamo stati in grado di pianificare e coordinare meglio le nostre attività sapendo che il test veniva eseguito durante la notte incustodito con interruzioni minime".
Uno strumento per ridurre tali errori, migliorando così la velocità e l'efficienza dei test, è C3Performance, un'utilità del software di controllo e acquisizione dati MTS AeroPro™. Conosciuto anche come C-cubed, C3Performance consente ai team di prova di gestire in modo efficace schemi di attuazione altamente incrociati, senza dover dedicare tempo extra alle pianificazioni delle prove per risolvere numerosi arresti e interblocchi ricorrenti.La tecnica di compensazione dell'accoppiamento incrociato di
C3 Performance è stata sviluppata congiuntamente da esperti del National Research Council of Canada (NRC) e di MTS Systems Corporation. Oggi è una parte standard del protocollo di prova presso l'NRC, il laboratorio di prove strutturali su vasta scala del Canada, dove Andre Beltempo lavora come ingegnere di prove strutturali.
"In genere, usiamo C-cubed per tutte le prove", ha affermato Beltempo. "Con le prove di fatica su vasta scala, si nota un'interazione dell'attuatore molto complessa. Proprio per questo ne abbiamo bisogno".
Il team di Beltempo ha recentemente utilizzato C3 Performance durante una dimostrazione tecnologica per un importante produttore di elicotteri. Il programma di prove di fatica e statiche si è concentrato su un'asse di coda in composito, fabbricata utilizzando tecniche di produzione avanzate. Le prove erano identiche a quelle che sarebbero state utilizzate per certificare la parte per i requisiti FAA di tolleranza di vita sicura.
"Se si osserva il raccordo dell'interfaccia della scatola del cambio del rotore della coda, i due attuatori posteriori caricano entrambi sullo stesso raccordo", ha affermato Beltempo. "La compensazione dell'accoppiamento incrociato aiuta a ridurre al minimo gli attriti tra gli attuatori".
La prova ha coinvolto sei attuatori e quattro milioni di end point, attivi durante la notte per circa 125 giorni, con una frequenza media di 0,5 Hz. Secondo Beltempo, questa velocità di prova sarebbe stata impossibile senza C3Performance.
"Non avremmo potuto farlo così rapidamente senza la compensazione dell'accoppiamento incrociato", ha detto. "Per un test notturno, avremmo dovuto eseguire i livelli finali a metà della velocità per non doverci preoccupare di arresti non presidiati. Il nostro approccio standard per qualsiasi prova di fatica consiste nel regolare il test, applicare C-cubed e ricalibrarlo subito. Non ho mai visto un aumento di velocità inferiore a un fattore di due per un articolo rigido”.
Un altro aspetto che Beltempo apprezza di C3Performance è la sua facilità d'uso complessiva. Poiché gli operatori di prove possono configurarlo autonomamente, C3Performance aiuta i laboratori a guadagnare ancora più tempo.
"Il fatto che sia così autonomo, mi dà la possibilità di concentrarmi su compiti più importanti", ha detto Beltempo. "Se dovessi sederti lì e calcolare tutti i coefficienti da solo, sarebbe diverso. Ma basta fare clic su un pulsante e succede. È un vero miglioramento della produttività".
Mentre è naturale per l'organizzazione che ha contribuito a sviluppare C3Performance applicarlo a ogni prova di fatica come questione di protocollo, anche altri laboratori stanno scoprendo il potenziale di risoluzione dei problemi di questa potente utilità.
Per il dott. Waruna Seneviratne, direttore tecnico del laboratorio Composites and Advanced Materials presso il National Institute for Aviation Research (NIAR) della Wichita State University, il problema era la privazione del sonno.
"Stavamo eseguendo una prova di fatica con una combinazione molto particolare di fissaggio e attuazione personalizzati e avevamo un programma di test molto aggressivo", ha affermato Seneviratne. "Il test è stato eseguito durante la notte e abbiamo riscontrato un numero elevato di trigger di limite di errore fastidiosi. Il nostro team è dovuto scendere in laboratorio nel cuore della notte per vedere cosa stava causando l'arresto dei test e per riavviare il test. Eravamo in ritardo".
Il test era concentrato sulla valutazione della resistenza alla fatica delle strutture composite del velivolo F/A-18 Hornet, molti dei quali si stanno avvicinando alla dismissione. Poiché la sostituzione del velivolo non sarà pronta fino al 2019, la Marina degli Stati Uniti deve prolungare in sicurezza la vita utile delle vecchie strutture composite del velivolo.
La ricerca di Seneviratne ha determinato con successo che le giunture legate tra composito e titanio alla radice dell'ala avevano ancora una grande quantità di vita. Il nuovo test ha ampliato lo studio per includere l'intera ala interna, che è dotata di una pelle composita. L'articolo di prova include l'ala interna, il flap del bordo d'uscita e la fusoliera centrale, nonché il flap del bordo d'attacco simulato e l'ala esterna. Il team di ricerca del NIAR ha dovuto costruire un elaborato impianto di perforazione in acciaio ad alta resistenza con attrezzature progettate su misura e applicare carichi significativi per ricreare manovre aggressive.
"C'erano differenze significative tra la corsa e i carichi attraverso gli attuatori, che rappresentavano una probabile fonte di errori", ha detto. "Avevamo bisogno di un modo per ridurre al minimo i falsi arresti, quindi abbiamo iniziato a esaminare meglio la questione".
L'ingegnere di ricerca Travis Cravens, membro del team di Seneviratne, ha gestito l'installazione e la configurazione di C3Performance. Gli ingegneri di sistema e applicativi di MTS hanno completato l'installazione e la formazione in meno di un giorno e il laboratorio ha visto i risultati quasi immediatamente.
"Alla fine del primo giorno stavamo correndo il 20% più velocemente senza modifiche meccaniche al banco di prova", ha detto Cravens. "Imparare a usare e configurare C3Performance è stato facilissimo; tutto avviene all'interno del software. È sufficiente creare una matrice di accoppiamento incrociato applicando un carico unitario su ciascun canale di carico, che rappresenta solo un passo in più per ciascun attuatore".
Per semplificare la configurazione delle prove, C3Performance elimina il compito dispendioso in termini di tempo di immettere manualmente i dati di accoppiamento incrociato utilizzando casi di carico unitari per generare coefficienti di compensazione dell'accoppiamento incrociato automatizzati. Seneviratne ha caratterizzato questo processo con un'analogia appropriata.
"È come avere un team di 20 persone che non si conoscono e che lavorano allo stesso progetto", ha detto. "I carichi unitari sono semplicemente un modo per presentare tutte queste persone l'una all'altra in modo che possano collaborare e lavorare in modo più efficiente".
Con qualche messa a punto in più, Seneviratne e Cravens sono stati in grado di aumentare il tasso di prova del 24 percento e ridurre significativamente il numero di arresti.
"Ha notevolmente migliorato le prestazioni del nostro test", ha affermato Cravens. "Con il monitoraggio del carico migliorato, è molto meno probabile che piccole perturbazioni nel feedback attivino limiti di errore, con conseguente minor numero di interruzioni del test. La riduzione dell'errore ci ha anche permesso di eseguire più segmenti all'ora”.
Prima di utilizzare C3Performance, il NIAR era in grado di raggiungere solo un massimo di 375 segmenti all'ora, con una media di 97 arresti e 55 interblocchi per blocco di prova. Con C3 Performance, questo è migliorato a 480 segmenti all'ora con una media di 51 arresti e 15 interblocchi.
"Il numero di arresti era un terzo di quello precedente, il che è stato un enorme guadagno per noi", ha detto Seneviratne. "Ciò ci ha permesso di eseguire il test durante la notte, alcune notti senza una sola interruzione. Sono fino a 10 ore di test che non avevamo prima, il che ci ha aiutato moltissimo con il nostro programma".
C3Performance ci ha permesso di risparmiare settimane di lavoro, consentendo al team di Seneviratne di fornire i risultati del test in tempo. Inoltre, la produttività del laboratorio è stata migliorata: il team è riuscito a operare con un programma più prevedibile e ha avuto più tempo da dedicare ad altri progetti. In qualsiasi laboratorio con risorse limitate, questo è un vantaggio importante.
"Sapere che avremmo potuto eseguire il test durante la notte ed essere sicuri di poter eseguire ispezioni e riparazioni durante il giorno ci ha permesso di aumentare l'efficienza del nostro percorso di prova", ha affermato Seneviratne. "Siamo stati in grado di pianificare e coordinare meglio le nostre attività sapendo che il test veniva eseguito durante la notte incustodito con interruzioni minime".