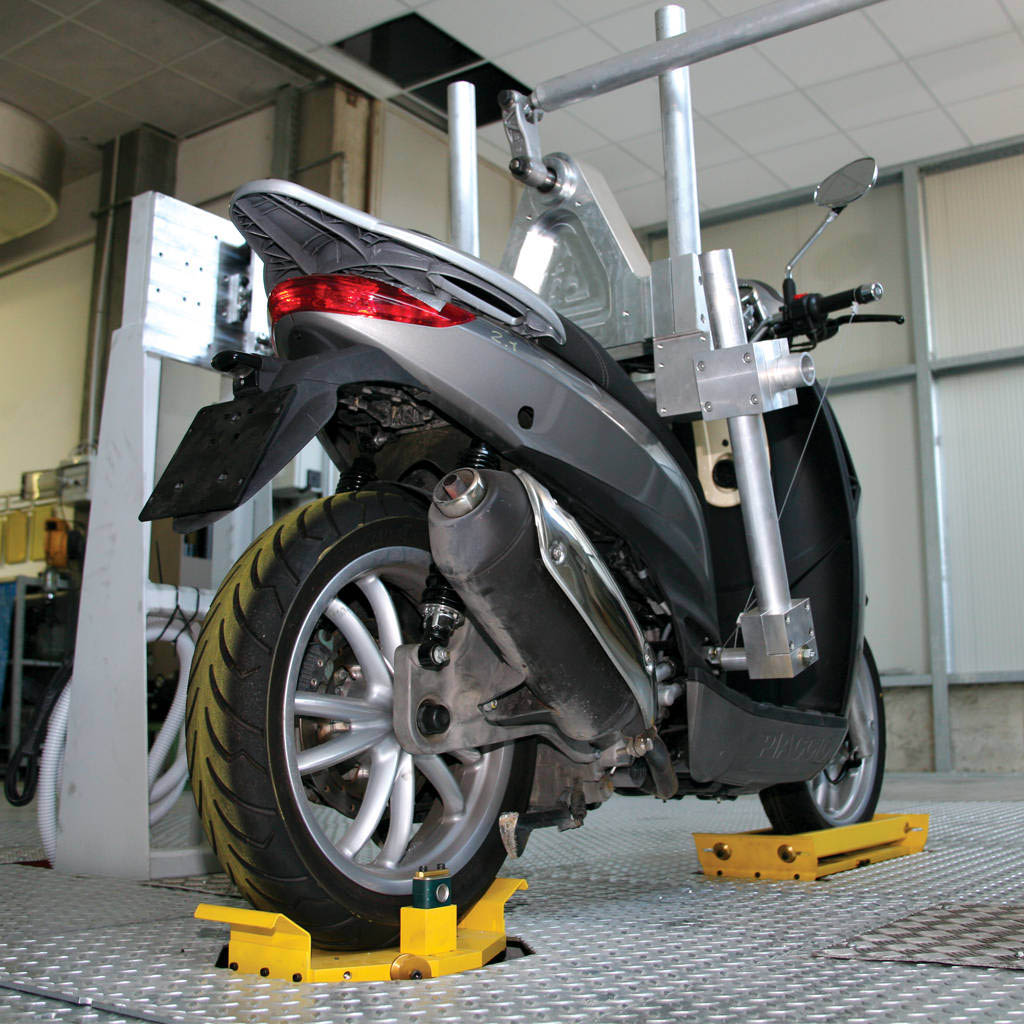
SFIDA DEL CLIENTE
I veicoli a due ruote sono diventati il mezzo di trasporto preferito in molte parti del mondo, ma soprattutto nelle affollate città di Europa, Asia e America Latina che non sono state progettate per le automobili e in cui il traffico è un problema molto serio.
Come uno dei principali produttori mondiali di scooter, ciclomotori e motociclette - incluso il famoso marchio Vespa ® - il Gruppo Piaggio con sede a Pontedera, Italia, produce più di 600.000 veicoli all'anno. I suoi sette marchi sono supportati da cinque centri di ricerca e sviluppo e 6.700 dipendenti in 50 Paesi.
Nonostante la sua forte brand equity e la sua leadership di prodotto nei mercati in cui opera, Piaggio deve affrontare la forte concorrenza di altri produttori che cercano di soddisfare la crescente domanda di questi veicoli agili e a basso consumo di carburante. Di conseguenza, l'azienda deve trovare nuovi modi per accrescere l'innovazione riducendo i costi di sviluppo, al fine di immettere sul mercato nuovi prodotti ricchi di funzionalità con maggiore frequenza e a prezzi interessanti.
"Il primo, e più ovvio, luogo in cui abbiamo cercato di migliorare l'efficienza è stato il banco di prova”, ha affermato Stefano Borghesi, che dirige il Laboratorio Meccanico di Pontedera per Piaggio. "Oltre a essere costoso ed essenzialmente non ripetibile, il test in pista fornisce quantità limitate di informazioni effettivamente applicabili ai progetti di prototipi.
"Tuttavia, il più grande svantaggio dei test in pista è il tempo necessario dall'inizio alla fine", ha aggiunto Borghesi. "Il tipico test in pista richiede ai conducenti di registrare migliaia di miglia in una varietà di condizioni operative, il che richiede mesi per essere completato. Nel panorama competitivo odierno, non possiamo più permetterci il lusso di dedicare così tanto tempo alla convalida di un progetto”.
SOLUZIONE MTS
Nel novembre 2008, Piaggio ha lavorato a stretto contatto con MTS per integrare il sistema di prova a 2 posti MTS modello 320 nel proprio laboratorio meccanico di Pontedera. Il sistema è fissato a un dispositivo isolante proprietario di "massa sismica" installato sotto il livello del pavimento, progettato per impedire che le forze di attuazione idraulica si disperdano verso l'esterno attraverso il laboratorio e lontano dal provino.
Il sistema ha eseguito il suo primo test ufficiale nell'aprile 2009. Piaggio è stato uno dei primi produttori di scooter al mondo a integrare tale tecnologia di simulazione avanzata nel proprio processo di sviluppo del prodotto.
Questo simulatore accoppiato a pneumatici a due assi sfrutta il software MTS RPC® per replicare in modo preciso e ripetibile le forze indotte dalla strada sull'intero prototipo del veicolo, producendo carichi e momenti che assomigliano molto a quelli sul terreno di prova, inclusi i test su fondi stradali irregolari. Poiché queste sono anche le condizioni che il pilota tipico incontrerà durante l'uso quotidiano, i professionisti dei test hanno un'idea più chiara di come si comporterà il veicolo dopo anni di utilizzo nel mondo reale.
In precedenza, Piaggio utilizzava sistemi di simulazione solo per i test sui componenti, il che richiedeva all'azienda di fare molto affidamento sui test in pista per valutare la durata e le prestazioni dell'intero veicolo.
"Ora stiamo valutando l'intera gamma di tipi e dimensioni di veicoli sia nel laboratorio di prova che sul circuito di prova, il che ci fornisce nuovi livelli di conoscenza nelle prime fasi di sviluppo", ha affermato Borghesi. "Inoltre, questo test può essere completato in una frazione del tempo che sarebbe richiesto su una pista di prova, con conseguente risparmio sui costi di sviluppo per Piaggio”.
VANTAGGI PER IL CLIENTE
Secondo Borghesi, il sistema di prova a 2 montanti MTS modello 320 ha aiutato Piaggio a ottenere un nuovo vantaggio competitivo, consentendo alla sua azienda di portare sul mercato progetti di prodotto migliori in meno tempo e a un costo inferiore.
"Con la nostra nuova capacità di simulazione di laboratorio, abbiamo migliorato le prestazioni dei nostri veicoli soddisfacendo al contempo la domanda dei clienti di minori emissioni e maggiore efficienza nei consumi", ha affermato Borghesi. "Abbiamo anche migliorato la durata del veicolo sottoponendo i nostri prototipi alle condizioni operative più impegnative in questo ambiente di laboratorio controllato e abbiamo fatto progressi significativi in termini di guida e comfort".
Inoltre, i collaudatori Piaggio utilizzano regolarmente il sistema di prova per verificare i risultati del modello, fornendo al team maggiore fiducia relativamente alla validità dei calcoli e all'integrità dei dati di prova.
"MTS ci ha dimostrato di offrire il miglior valore totale di qualsiasi fornitore di soluzioni di test", ha affermato Borghesi. "Da prodotti di alta qualità a un team esperto di tecnici dell'assistenza sul campo, MTS è stato determinante nell'aiutarci a simulare con successo gli eventi stradali più critici e rivelatori nel nostro laboratorio. Siamo impazienti di lavorare con MTS anche in futuro".