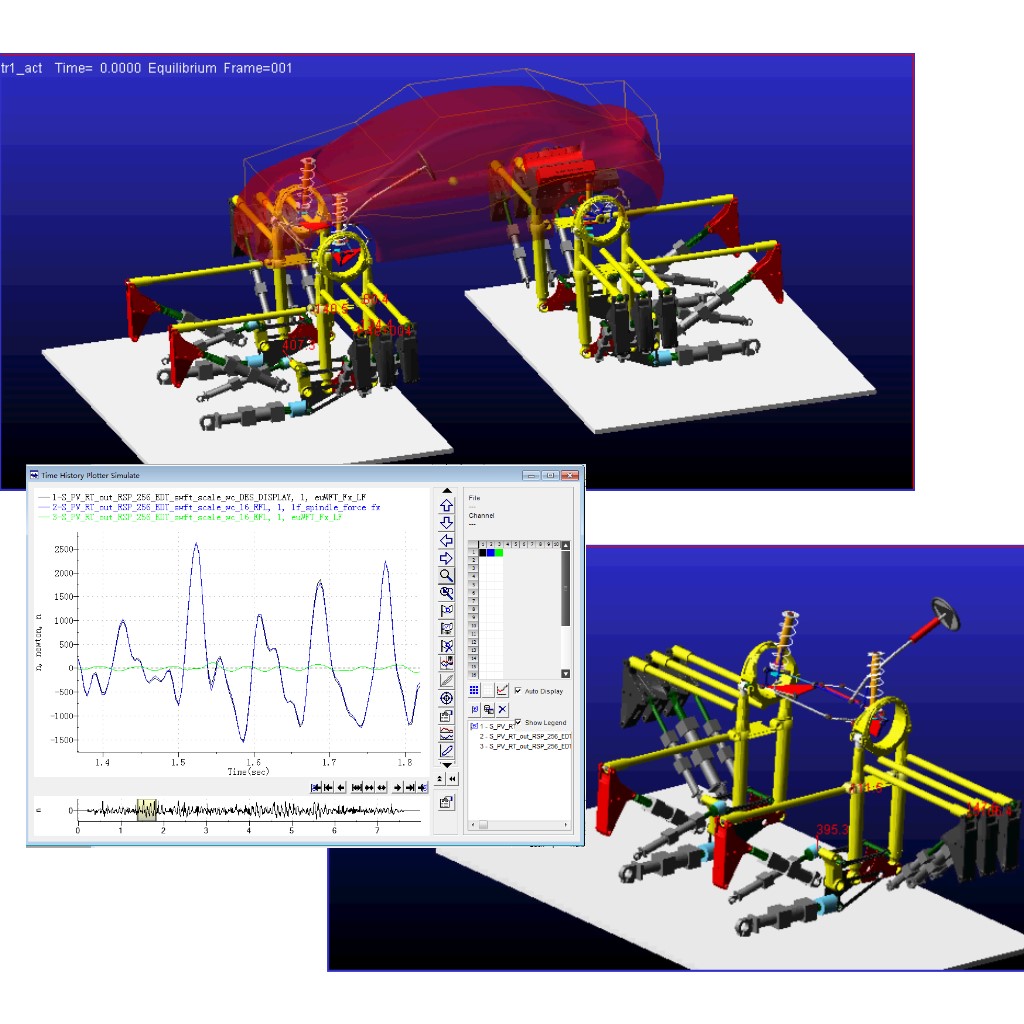
Sotto l'incessante pressione per accelerare i cicli di sviluppo e ridurre i costi, i produttori di automobili stanno esplorando sempre più modi per utilizzare strumenti di analisi per eseguire valutazioni virtuali significative dei progetti di veicoli in anticipo, molto prima della disponibilità di prototipi fisici. La capacità di ottenere carichi accurati previsti - o calcolati - in questo modo aumenta l'efficacia dei test fisici dei componenti, consente l' identificazione precoce e l'eliminazione dei difetti di progettazione, riduce la necessità di rilavorazione e la dipendenza dai prototipi e semplifica la convalida del progetto.
È stata ideata una varietà di approcci di simulazione per ottenere carichi calcolati accurati nelle prime fasi del processo di sviluppo del veicolo. Un metodo, il Virtual Proving Ground, prevede la "guida" di un modello di veicolo su una strada digitalizzata. Pur avendo il vantaggio di affidarsi interamente a modelli virtuali, questo approccio genera carichi imprecisi che sono difficili da convalidare tramite test fisici. Un metodo semi-analitico, invece, utilizza i carichi del mandrino acquisiti da un veicolo esistente per eccitare il modello del veicolo. Anche se ciò fornisce risultati migliori rispetto al banco di prova virtuale, stabilisce condizioni limite non del tutto appropriate per il modello del veicolo, quindi i carichi calcolati continuano a essere errati e difficili da convalidare. Un terzo metodo, il Virtual Testing, risolve questi problemi integrando un modello di un sistema di test fisico effettivo nella simulazione per eccitare il modello del veicolo.
Il test virtuale è la simulazione di un test fisico, che sfrutta strumenti di analisi ad elementi finiti, strumenti di analisi dinamica multi-corpo e tecniche di iterazione RPC per derivare carichi precisi, informazioni sul movimento e sui danni di un sistema di veicoli nelle prime fasi del processo di sviluppo. I vantaggi di questo approccio sono numerosi. In primo luogo, poiché è più facile modellare i vincoli di un sistema di test fisico piuttosto che provare le superfici del terreno o gli pneumatici, il test virtuale stabilisce condizioni limite molto più efficaci rispetto agli altri metodi. In secondo luogo, i test virtuali ricorrono a un arsenale di strumenti e tecniche di test fisici comprovati e consolidati, che hanno dimostrato la loro utilità nel campo dell'analisi. E in terzo luogo, l'incorporazione di un sistema di test fisico modellato semplifica notevolmente la convalida dei risultati attraverso i successivi test fisici e offre l'opportunità di migliorare le configurazioni dei test fisici e la progettazione dei dispositivi. Applicando le discipline dei test analitici e fisici, i test virtuali richiedono una conoscenza avanzata sia degli strumenti CAE che dei test fisici, lo sviluppo di un processo per collegare il software RPC Pro e i modelli di analisi e, preferibilmente, un certo grado di esposizione ed esperienza nei test virtuali.
Per anni, MTS si è concentrata sul perfezionamento dell'approccio dei test virtuali, conducendo una serie di progetti dimostrativi con clienti chiave come Hyundai Motor Company (HMC) e Thermo King al fine di valutare varie metodologie. Questi progetti includevano test virtuali di veicoli e sottosistemi completi, tutti con una correlazione soddisfacente con i dati di carico stradale misurati (RLD) o con test fisici effettivi. La metodologia di base ricavata da queste esperienze comprende i seguenti passaggi: 1) Collegare i modelli del banco di prova con i modelli del campione; 2) Accoppiare i modelli con RPC Pro; 3) Riprodurre i dati del carico stradale sul banco di prova virtuale; 4) Estrarre i carichi calcolati; 5) Creare il test del componente fisico/sottosistema.
Un recente progetto dimostrativo con lo State Automotive Institute of China (SAIC) fornisce un eccellente esempio di questa metodologia nella pratica:
- Collegare i modelli del banco di prova con i modelli del campione
All'inizio del progetto, MTS ha creato una raccolta di modelli di banchi di prova nei formati di co-simulazione ADAMS, Simulink e ADAMS-Simulink. I banchi di prova MTS che sono stati modellati includevano una varietà di simulatori stradali accoppiati a mandrino modello 329, un sistema MAST (Multi-axial Simulation Table) modello 353.20 e un sistema di test dei componenti TestLine. Sono stati inoltre modellati componenti selezionati del banco di prova, tra cui un controller digitale FlexTest, attuatori e servovalvole MTS e una trasformazione dell'attuatore che converte lo spostamento, l'accelerazione e la forza dell'attuatore in spostamento, accelerazione e forza DOF. A causa dei vincoli temporali del progetto e delle velocità di simulazione relativamente basse dei modelli di co-simulazione più complessi, il modello ADAMS/Car 329 è stato accoppiato con il veicolo completo SAIC, i modelli con sospensione anteriore e sospensione posteriore e infine utilizzato per la maggior parte dei test virtuali.
- Accoppiare i modelli con RPC Pro
È stato sviluppato un server di test virtuale per collegare il software RPC Pro e il modello ADAMS/Car 329. Durante il test, RPC Pro utilizza questo server virtuale per inviare drive file al modello ADAMS, avviare la simulazione ADAMS e copiare il file di risposta dalla cartella ADAMS nella directory di lavoro di RPC Pro. Inoltre, è stato utilizzato uno strumento di interfaccia Matlab già esistente in RPC Pro per accoppiare RPC Pro con i modelli di co-simulazione.
- Riprodurre i dati del carico stradale sul banco di prova virtuale
La tecnica di iterazione RPC è stata quindi utilizzata per riprodurre i dati relativi al carico su strada (forza del mandrino) raccolti dal banco di prova per una serie di eventi e manovre selezionati. È interessante notare che le iterazioni RPC iniziali sui rig 329 virtuali non hanno mostrato alcuna convergenza, suggerendo difetti nel modello di veicolo SAIC. L'analisi successiva del modello ha effettivamente rivelato carenze, che sono state corrette in breve tempo. Con il modello migliorato, le iterazioni RPC sono finalmente convergenti, mostrando un'eccellente correlazione tra segnali desiderati e raggiunti e bassi errori RMS su tutti i canali per le simulazioni virtuali del veicolo sia complete che parziali.
- Estrarre i carichi calcolati
Dopo la convergenza dell'iterazione RPC, i carichi calcolati per qualsiasi componente meccanico o sottosistema potrebbero essere facilmente ottenuti dal modello del veicolo come funzioni temporali.
- Creazione di test fisici
Le cronologie dei tempi di caricamento estratte dal modello del veicolo sono state quindi utilizzate per definire i successivi test dei componenti fisici. Una volta stabilito se una parte è soggetta a carico su asse singolo o multiasse, l'arsenale di metodi e strumenti di prova RPC Pro può essere utilizzato per definire test dei componenti notevolmente accelerati. Per i componenti sottoposti a carico su asse singolo, è possibile utilizzare i metodi Block Cycle o Power Spectrum Density (PSD). Per i componenti soggetti a carico multiasse, è possibile utilizzare il metodo Peak Valley Slicing. Per le situazioni in cui è necessario preservare la frequenza di caricamento di un componente, il metodo di riproduzione cronologia temporale è il più appropriato; per questi tipi di test, RPC Pro dispone della funzione di Fatigue Sensitive Editing che ha il potenziale di accelerare i test di durata di un fattore da 2 a 10. Una volta determinati i segnali di carico per ciascun componente, è possibile utilizzare lo stesso sistema di test fisico su cui si basavano i banchi di prova virtuali per condurre il test del componente. Inoltre, è possibile utilizzare una varietà di tecniche di compensazione in RPC Pro, come la compensazione dei valori di picco, la compensazione inversa adattiva e l'iterazione RPC, per assicurarsi che le condizioni di carico desiderate vengano raggiunte con precisione durante i test fisici.
La continua esplorazione da parte di MTS dei test virtuali dimostra che si tratta di un mezzo efficace per prevedere con precisione i carichi dei componenti prima di sviluppare parti fisiche o prototipi. Una volta ottenuti questi carichi calcolati, gli stessi strumenti e le stesse tecniche RPC Pro utilizzati per ottenerli possono essere utilizzati per creare e condurre i test fisici necessari per convalidare la loro accuratezza e l'accuratezza del modello del veicolo. I potenziali impatti di test virtuali efficaci sullo sviluppo del veicolo sono considerevoli. La disponibilità di carichi previsti accurati e i successivi test fisici anticipati ridurranno al minimo la rilavorazione di componenti e sottosistemi, nonché la necessità di creare più prototipi e accelererà la convalida del progetto. Inoltre, il ruolo dei test fisici si evolverà: mentre i test continueranno a essere necessari per ottenere la convalida finale del progetto di un veicolo, saranno sempre più personalizzati per convalidare l'accuratezza del modello del veicolo. Infine, i test virtuali favoriranno l'integrazione di discipline e culture di analisi e test fisici, stimolando l'avvento di nuove efficienze attraverso la condivisione di strumenti, processi ed esperienze.
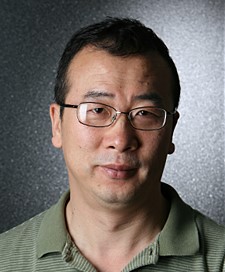