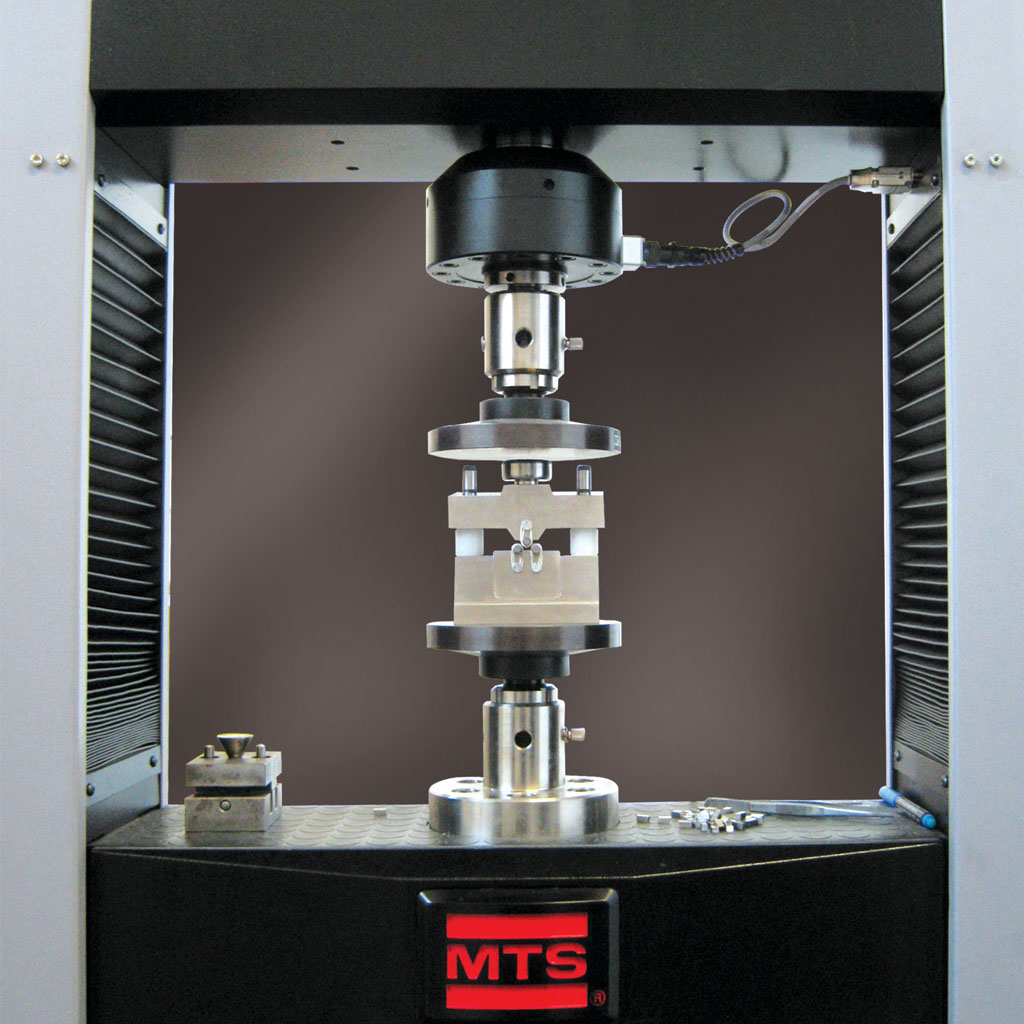
SFIDA DEL CLIENTE
Gli sviluppatori di dispositivi ortopedici devono affrontare una forte concorrenza, il che significa che la velocità di immissione sul mercato è fondamentale. Gli sviluppatori sono costantemente alla ricerca di nuovi modi per accelerare il processo di sviluppo del prodotto e ottenere informazioni su nuovi materiali e design prima e con maggiore sicurezza.
K4Sint è una piccola azienda che ha un grande impatto in questo campo di studi. La società privata di ricerca e sviluppo, che si trova appena fuori Trento, in Italia, è specializzata nell'applicazione di tecniche di metallurgia delle polveri per produrre nuovi materiali per dispositivi ortopedici impiantabili che altrimenti sarebbero impossibili da ottenere.
"I nostri clienti sono produttori di dispositivi ortopedici ad alte prestazioni", afferma il dottor Mario Zadra, uno dei fondatori di K4Sint ed esperto sia di scienza dei materiali che di metallurgia delle polveri. "In genere hanno bisogno di migliorare le prestazioni dei dispositivi, ma vogliono anche mantenere i costi il più bassi possibile. Produciamo nuove componenti utilizzando diverse combinazioni di materiali per trovare la soluzione migliore".
Proprio come gli sviluppatori al servizio di K4Sint, il team del dottor Zadra è costantemente sotto pressione per creare nuove parti molto rapidamente. Per fare ciò, K4Sint utilizza una sequenza brevettata di alligazione meccanica e sinterizzazione al plasma a scintilla. La sinterizzazione, un metodo per creare oggetti da materiali in polvere, aiuta i ricercatori di K4Sint a formare nuove composizioni molto più velocemente rispetto alla lega diretta. Quando ogni nuova lega è pronta, il passaggio successivo consiste nell'eseguire prove meccanici con uguale efficienza.
SOLUZIONE MTS
Dalle teste femorali e le coppe acetabolari ai condili e alle spugne metalliche, tutte le parti dei dispositivi ortopedici impiantabili devono offrire le prestazioni che gli sviluppatori si aspettano. I produttori di dispositivi di fascia alta sono particolarmente interessati a nuove leghe che possono fornire resistenza e affidabilità ideali ma offrono nuovi modi per ridurre i costi di materiale e produzione.
"In termini di leghe, ci sono solo pochi elementi che possono essere utilizzati, tra cui titanio e zirconio", afferma il dottor Zadra. "Li mescoliamo per ottenere una composizione che mostri le giuste proprietà meccaniche, la più importante delle quali è la durezza. Produciamo dischi da 20 millimetri, che tagliamo per ottenere campioni più piccoli che testiamo con un dispositivo di piegatura a tre punti nel nostro sistema di prova MTS. Possiamo ottenere rapidamente i dati delle prove, mettere a punto il materiale, ripetere la prova di piegatura a tre punti e sapere quando la composizione è corretta".
Nel laboratorio K4Sint, il team del dottor Zadra si affida a un sistema di prova universale elettromeccanico MTS Criterion ®di serie 40, utilizzato insieme al software MTS TestSuite™TW, morsetti a cuneo e piastre di compressione MTS e uno strumento di piegatura a tre punti unico nel suo genere, progettato su misura dal team K4Sint. Il sistema MTS Criterion offre al laboratorio la capacità di caratterizzare la durezza di nuove leghe e di valutarne la tensione di snervamento, la resistenza finale alla trazione e la duttilità.
VANTAGGI PER IL CLIENTE
Con il sistema MTS Criterion nel suo laboratorio, K4Sint può mantenere un programma di prova rigorosamente efficiente, eseguendo da 10 a 15 prove di flessione a tre punti ogni settimana, oltre a prove di trazione settimanali di materiali che hanno dimostrato di meritare ulteriori valutazioni.
"Prima di acquisire il sistema di prova MTS, abbiamo dovuto eseguire tutti le nostre prove presso l'Università di Trento", afferma il dottor Zadra. "Ora le nostre prove sono molto più veloci e convenienti, e la velocità delle prove è direttamente correlata al successo della nostra attività".
Il dottor Zadra apprezza anche le prestazioni del sistema MTS Criterion, che è in funzione nel laboratorio K4Sint da poco più di un anno. Il sistema è costruito per funzionare in modo affidabile ed è progettato specificamente per una facile manutenzione.
"Il motivo per cui inizialmente abbiamo scelto MTS è che avevamo bisogno di un sistema che potesse tenere il passo con i nostri obiettivi di prova sfruttando la versatilità delle prove e massimizzando i tempi di attività", afferma il dottor Zadra. "Con il marchio MTS abbiamo ottenuto entrambi. Abbiamo un ottimo rapporto con MTS".