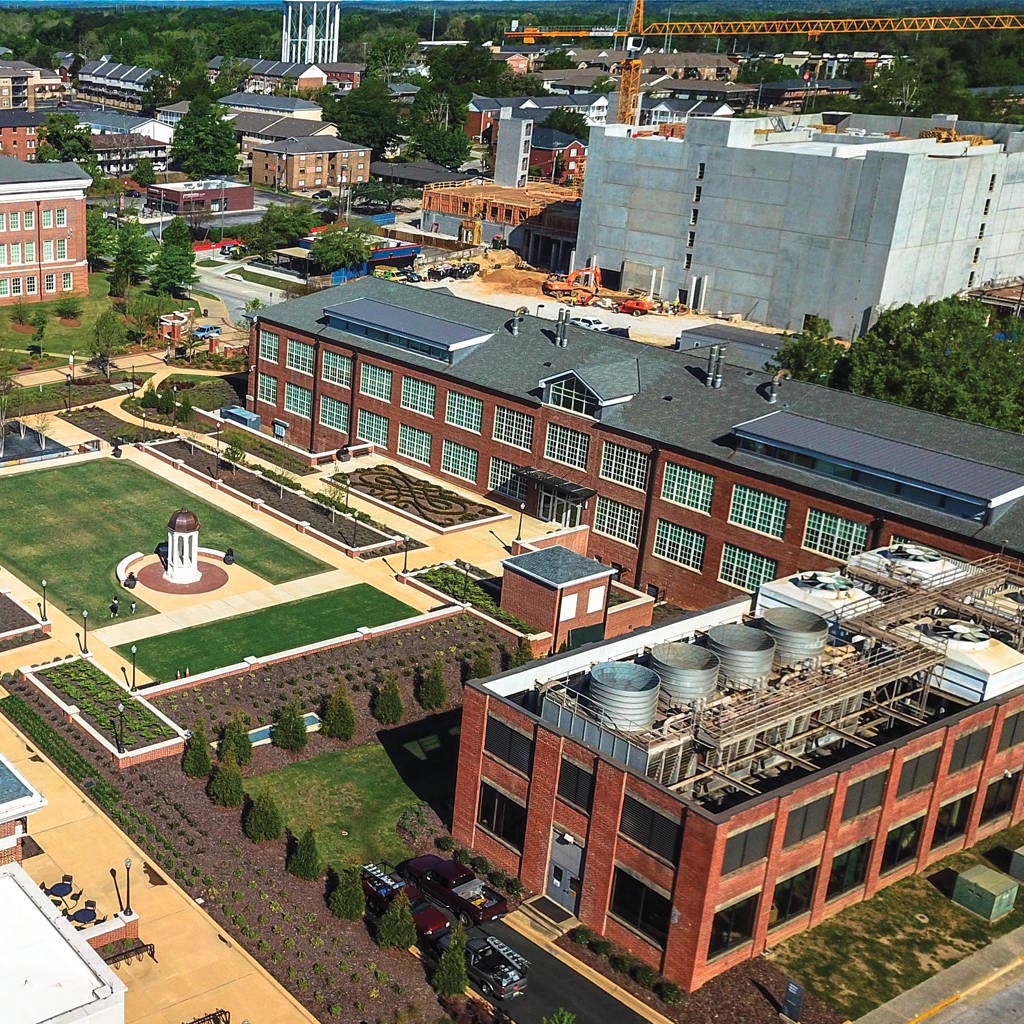
La fatica è ancora la causa della maggior parte dei cedimenti meccanici in molte applicazioni strutturali. Un tipico cedimento per fatica ha almeno 3 fasi: inizio della cricca, propagazione della cricca e frattura finale. È ben noto che i difetti superficiali (ad esempio, una rugosità superficiale), i difetti volumetrici (ad esempio, pori o mancanza di fusione) e la microstruttura sono fattori influenti sulle prestazioni a fatica dei materiali metallici. Occorre anche notare che spesso le cricche si concentrano a partire dalla superficie o nei pressi della superficie stessa per diversi motivi, quali una più facile deformazione anelastica, maggiori stress o deformazioni dati da carichi esterni ed effetti della concentrazione degli stress.
Il crescente interesse per i processi di produzione a strati, anche denominati produzione additiva (AM, additive manifacturing), ha spinto molti settori a prendere in considerazione l'adozione di queste tecnologie. Sebbene i processi di produzione additiva sembrino semplici (produzione strato per strato), ci sono molte complessità fisiche e metallurgiche associate ai ripetuti e rapidi processi di scioglimento e solidificazione durante la fabbricazione. L'intricata storia termica (ad esempio, il gradiente termico, la velocità di raffreddamento, ecc.) sperimentata dal componente durante la fabbricazione influenza la microstruttura, la struttura cristallografica, gli stress residui, la rugosità superficiale e la formazione di difetti volumetrici (ad esempio, pori intrappolati da gas e mancanza di fusioni), che di conseguenza influiscono sulle proprietà meccaniche, in particolare sotto carico ciclico [1, 2]. A questo proposito, ci sono diversi studi che hanno studiato l'effetto di difetti volumetrici, rugosità superficiale e microstruttura sul comportamento a fatica di materiali metallici prodotti in modo additivo (AM). [3].
La maggior parte degli studi ha riportato una resistenza alla fatica inferiore per i materiali metallici AM, anche nella loro condizione superficiale lavorata, rispetto alle loro controparti lavorate, a causa degli effetti dannosi dei difetti volumetrici inerenti ai processi AM [4]. A questo proposito, sono stati fatti molti sforzi per ridurre le dimensioni e il numero di questi difetti regolando i parametri di processo. Tuttavia, anche utilizzando i parametri del processo di produzione più ottimizzati, ci saranno ancora alcuni difetti indotti dal processo, come i pori intrappolati da gas nei componenti AM, che possono esacerbare le loro prestazioni a fatica. I processi superficiali e termici post-produzione sono spesso essenziali per migliorare le prestazioni a fatica dei materiali AM. Ad esempio, nella Figura 1 si può vedere che la rimozione della rugosità superficiale mediante lavorazione meccanica può migliorare significativamente le prestazioni a fatica della fusione a letto di polvere con raggio laser (LB-PBF) 17-4 PH SS [1]. Effetti della rugosità superficiale simili sul comportamento a fatica sono stati riportati anche per altri sistemi di materiali [5].
Figura 1
Confronto stress/vita e fatica di LB-PBF17-4 PH SS sottoposto a trattamento termico CA-H900con condizioni di superficie lavorata e costruita[1].
I processi termici post-produzione (ad esempio, la pressatura isostatica a caldo (HIP, hot isostatic pressing) o il trattamento termico) possono influenzare le prestazioni a fatica dei materiali metallici AM associati a cambiamenti nella microstruttura (ad esempio, dimensione e distribuzione dei pori, dimensione e morfologia dei grani, comportamento delle precipitazioni, eccetera) [2,4]. Ad esempio, i processi di trattamento termico post-produzione, compreso il processo di trattamento termico in soluzione (noto come condizione A (CA) per 17-4 PH SS) migliorano la resistenza alla fatica di LB-PBF 17-4 PH SS (Figura 2). Ciò è attribuito alla microstruttura più omogeneizzata e più fine ottenuta dopo la fase CA rispetto alla microstruttura prodotta dopo procedure di trattamento termico senza questa fase [1].
Figura 2
Dati di resistenza alla fatica di LB-PBF 17-4 PHSS, in condizioni di superficie as-built, sottoposti a varieprocedure di trattamento termico [1]. Si noti che i marcatori vuoti mostrano le procedure di trattamento termico senza passaggio CA, mentre i marcatori pieni presentano condizioni di trattamento termico compreso il passaggio CA.
È interessante notare che i materiali metallici prodotti in modo additivo mostrano per lo più un comportamento di crescita delle cricche per fatica (FCG, fatigue crack growth behavior) simile a quello della controparte lavorata nel regime di Parigi (cioè la regione di crescita stabile della cricca). La Figura 3 è un esempio che mostra che LB-PBF 17-4 PH SS ha un comportamento FCG identico rispetto al materiale lavorato [6]. Tuttavia, l'LB-PBF 17-4 PH SS mostra un tasso FCG più elevato (cioè una resistenza FCG inferiore) nella regione FCG instabile (cioè regione ÄK alta) rispetto al materiale lavorato. Ciò può essere dovuto alle differenze nella microstruttura, nonché alla presenza di difetti volumetrici in LB-PBF 17-4 PH SS con conseguente minore tenacità alla frattura ciclica rispetto a quella del materiale lavorato. Tali difetti possono anche aumentare il tasso di FCG di LB-PBF 17-4 PH SS nella regione vicina alla soglia.
Figura 3
Comportamento della crescita di cricche da fatica (FCG) di LBPBF17-4 PH SS sottoposto a trattamento termico CA-H900rispetto a quello della controparte lavorata con la stessa condizione di trattamento termico [6].
Riferimenti
1. Nezhadfar PD, Shrestha R, Phan N, Shamsaei N. Int J Fatica. 2019;124:188-204.
2. Pegues JW, Shao S., Shamsaei N., Sanaei N., Fatemi A., Warner DH, Li P., Phan N., Int J Fatigue, 2020: 132, p.105358.
3. Fatemi A, Molaei R, Simsiriwong J, Sanaei N, Pegues J, Torries B, Phan N, Shamsaei N., Fatigue & Fracture of Eng. Mater. & Struc. 2019: 991-1009.
4. Pegues JW, Shao S., Shamsaei N., Sanaei N., Fatemi A., Warner DH, Li P., Phan N., Int J Fatigue, 2020: 132, p.105363.
5. Pegues J., Roach M., Williamson RS, Shamsaei N. Int J Fatigue, 116, 2018: 543-552.
6. Nezhadfar PD, Burford E, Anderson-wedge K, Zhang B, Daniewicz SR, Shamsaei N., Int J Fatigue. 2019.
Il National Center for Additive Manufacturing Excellence (NCAME) presso la Auburn Universityè stato formato nel 2017 grazie a una collaborazione con il Marshall Space Flight Center della NASA.